Резка и механическая обработка деталей из порошковой металлургии (P / M)
Использование процесса порошковой металлургии (P / M) для производства деталей для автомобильных энергосистем продолжает расти. Детали, изготовленные по технологии P / M, обладают многими важными и уникальными преимуществами. Остаточная пористая структура, намеренно оставленная в этих частях, хороша для самосмазки и звукоизоляции. Сложные сплавы, которые трудно или невозможно изготовить традиционным способом литья, можно производить с использованием технологии P / M. Детали, изготовленные по этой технологии, обычно имеют небольшую перерабатывающую способность или вообще не имеют ее, что делает их дешевле и снижает количество отходов в материалах. К сожалению, из-за привлекательности этих характеристик детали P / M трудно обрабатывать.
Хотя одним из первоначальных намерений индустрии P / M является устранение всей обработки, эта цель еще не достигнута. Большинство деталей могут быть только «близки к окончательной форме» и все еще нуждаются в доработке.
Однако по сравнению с отливками и поковками небольшое количество материала, которое необходимо удалить с деталей из P / M, является типичным износостойким материалом.
Пористая структура - одна из характеристик, благодаря которым детали из p / M имеют широкий спектр применения, но срок службы инструмента также будет снижаться из-за пористой структуры. Пористая структура может накапливать масло и звук, но это также приводит к прерывистой микроперемежающейся резке. При движении назад и вперед от отверстия к твердым частицам режущая кромка инструмента постоянно ударяется, что может привести к очень небольшой деформации усталостного разрушения и мелкому разрушению кромок вдоль режущей кромки. Что еще хуже, частицы обычно очень твердые. Даже если макротвердость измеряемого материала составляет от 20 до 35 градусов, размер частиц компонента достигает 60 градусов. Эти твердые частицы вызывают сильный и быстрый износ кромок. Многие детали из п / м поддаются термообработке, а твердость и прочность материала после термообработки выше. Наконец, из-за технологии спекания и термообработки и используемых газов поверхность материала будет содержать твердые и износостойкие оксиды и / или карбиды.
Производительность деталей P / M
Большинство свойств деталей из P / M, включая обрабатываемость, связаны не только с химическим составом сплава, но и с уровнем пористости пористой структуры. Пористость многих деталей конструкции составляет до 15% ~ 20%. Пористость деталей, используемых в качестве фильтрующих устройств, может достигать 50%. На другом конце серии пористость кованых или шатровых деталей составляет всего 1% или меньше. Эти материалы становятся особенно важными в автомобильной и авиационной промышленности, поскольку они могут обеспечить более высокий уровень прочности.
Прочность на растяжение, ударная вязкость и пластичность сплава П / М увеличиваются с увеличением плотности, а обрабатываемость также может быть улучшена, поскольку пористость вредна для режущей кромки инструмента.
Повышение уровня пористости может улучшить звукоизоляционные характеристики деталей. Демпфирующие колебания в стандартных деталях значительно уменьшаются в деталях P / M, что очень важно для станков, нагнетательных труб для кондиционирования воздуха и пневматических инструментов. Самосмазывающимся зубчатым колесам также необходима высокая пористость.
Трудности при обработке
Хотя одной из целей непрерывного развития индустрии P / M является отказ от механической обработки, а одним из главных преимуществ процесса P / M является то, что требуется лишь небольшой объем обработки, многие детали все еще нуждаются в дополнительной обработке для получения более высокая точность или лучшее качество поверхности. К сожалению, обработка этих деталей крайне затруднительна. Большинство проблем вызвано пористостью. Пористость приводит к микроусталости режущей кромки. Режущая кромка постоянно врезается и опускается. Он проходит между частицами и дырами. Повторяющиеся небольшие удары приводят к появлению небольших трещин на режущей кромке.
Эти усталостные трещины растут до тех пор, пока режущая кромка не разрушится. Кромка с микротрещинами обычно очень мала и обычно имеет нормальный абразивный износ.
Пористость также снижает теплопроводность деталей из P / M, что приводит к высокой температуре режущей кромки и вызывает кратерный износ и деформацию. Пористая структура с внутренним соединением обеспечивает путь для выпуска смазочно-охлаждающей жидкости из зоны резания. Это может вызвать горячие трещины или деформацию, особенно при сверлении.
Увеличение площади поверхности, вызванное внутренней пористой структурой, также приводит к окислению и / или карбонизации во время термообработки. Как упоминалось ранее, эти оксиды и карбиды твердые и износостойкие.
Пористая структура также не позволяет считывать твердость детали, что очень важно. Когда макротвердость детали из P / M измеряется намеренно, она включает коэффициент твердости отверстия. Пористая структура приводит к разрушению конструкции и создает неправильное впечатление об относительно мягких частях. Частицы намного тверже. Как описано выше, разница огромна.
Наличие включений в деталях из ПМ также является недостатком. Во время обработки эти частицы будут подниматься с поверхности, и при трении перед инструментом на поверхности детали будут образовываться царапины или царапины. Эти включения обычно имеют большие размеры, оставляя видимые дыры на поверхности детали.
Разница в содержании углерода приводит к несогласованности обрабатываемости. Например, содержание углерода в сплаве fc0208 составляет от 0.6% до 0.9%. Партия материалов с содержанием углерода 0.9% относительно тверда, что снижает стойкость инструмента. Другая партия материалов с содержанием углерода 0.6% имеет превосходный срок службы. Оба сплава находятся в допустимом диапазоне.
Проблема окончательной обработки связана с типом резания детали P / M. Поскольку деталь близка к окончательной форме, глубина резания обычно очень мала. Для этого нужна свободная режущая кромка. Накопление стружки на режущей кромке часто приводит к образованию микротрещин.
Технология обработки
Для преодоления этих проблем применяется несколько технологий (уникальных для отрасли). Поверхностная пористая структура часто герметизируется инфильтрацией. Обычно требуется дополнительная свободная резка. В последнее время используются улучшенные технологии производства порошка, предназначенные для повышения чистоты порошка и уменьшения содержания оксидов и карбидов во время термообработки.
Пористая структура с закрытой поверхностью достигается за счет инфильтрации металла (обычно меди) или полимера. Было высказано предположение, что инфильтрация действует как смазка. Большинство экспериментальных данных показывают, что реальное преимущество заключается в закрытии пористой структуры поверхности и, таким образом, предотвращении микроусталости режущей кромки. Уменьшение вибрации увеличивает стойкость инструмента и качество поверхности. Наиболее эффективное использование инфильтрации показывает увеличение срока службы инструмента на 200% при закрытой пористой структуре.
Такие добавки, как MNS, s, MoS2, MgSiO3 и BN, как известно, увеличивают стойкость инструмента. Эти добавки улучшают обрабатываемость, облегчая отделение стружки от заготовки, ломая стружку, предотвращая нарастание стружки и смазывая режущую кромку. Увеличение количества добавок может улучшить обрабатываемость, но снизить прочность и ударную вязкость.
Технология распыления порошка для управления печным газом для спекания и термообработки позволяет производить чистый порошок и детали, что сводит к минимуму появление включений и поверхностных оксидных карбидов.
Инструментальный материал
Наиболее широко используемые инструменты в промышленности P / M - это те материалы, которые являются износостойкими, стойкими к краевым трещинам и не содержат сколов при условии хорошей отделки поверхности. Эти характеристики полезны для любых операций обработки, особенно для деталей P / M. Инструментальные материалы, включенные в эту категорию, включают инструменты из кубического нитрида бора (CBN), керметы без покрытия и с покрытием, а также улучшенные спеченные твердые сплавы с покрытием.
Инструменты CBN привлекательны своей высокой твердостью и износостойкостью. Этот инструмент уже много лет используется при обработке стали и чугуна с твердостью по Роквеллу 45 и выше. Однако из-за уникальных свойств сплава P / M и значительной разницы между микротвердостью и макротвердостью инструменты CBN могут использоваться для деталей из P / M с твердостью 25 по Роквеллу. Ключевым параметром является твердость частиц. Когда твердость частиц превышает 50 градусов по Роквеллу, инструменты CBN доступны независимо от значения макротвердости. Очевидным ограничением этих инструментов является их недостаточная прочность. В случае прерывистого резания или высокой пористости необходимо усиление кромок, включая снятие фаски и тяжелое хонингование. Простая легкая резка может выполняться с помощью заточенной режущей кромки.
Есть несколько эффективных материалов CBN. Материал с наилучшей прочностью в основном состоит из цельного CBN. У них отличная вязкость, поэтому их можно использовать для черновой обработки. Их ограничения обычно связаны с отделкой поверхности. Это во многом определяется отдельными частицами CBN, из которых состоит инструмент. Когда частицы падают с режущей кромки, они воздействуют на поверхность обрабатываемого материала. Однако не все так серьезно, чтобы инструмент с мелкими частицами упал с одной частицы.
Обычно используемый материал CBN имеет высокое содержание CBN и средний размер частиц. Чистовое полотно из CBN имеет мелкое зерно и низкое содержание CBN. Они наиболее эффективны, когда требуется легкая резка и обработка поверхности или когда обрабатываемый сплав особенно твердый.
Во многих случаях резания стойкость инструмента не зависит от типа материала. Другими словами, любой материал CBN может обеспечить аналогичную стойкость инструмента. В этих случаях выбор материала в основном основан на наименьшей стоимости каждой режущей кромки. Одно круглое лезвие имеет всю верхнюю поверхность из CBN и может иметь четыре или более режущих кромок, что дешевле, чем четыре инкрустированных лезвия из CBN.
Когда твердость деталей из P / M ниже, чем 35 градусов по Роквеллу, а твердость частиц находится в заданном диапазоне, обычно одним из вариантов является металлокерамика. Керметы очень твердые, могут эффективно предотвращать накопление стружки и выдерживать высокие скорости. Кроме того, поскольку металлокерамика всегда использовалась для высокоскоростной и чистовой обработки стали и нержавеющей стали, они обычно имеют идеальные геометрические канавки, подходящие для деталей, близких к формованным.
Современные металлокерамические материалы сложны в металлургии и содержат до 11 легирующих элементов. Обычно они спекаются из частиц TiCN и никель-молибденового клея. TiCN обеспечивает твердость, стойкость к образованию стружки и химическую стабильность, которые важны для успешного использования металлокерамики. Кроме того, эти инструменты обычно имеют высокое содержание клея, что означает, что они обладают хорошей вязкостью. Одним словом, они обладают всеми характеристиками эффективной обработки сплава П / М. Эффективны несколько видов металлокерамики, например, спеченный цементированный карбид вольфрама: чем выше содержание связующего, тем выше ударная вязкость.
Известная относительно новая разработка заключается в том, что химическое осаждение из паровой фазы при средней температуре (mtcvd) также обеспечивает преимущество для промышленности P / M. Mtcvd сохраняет всю износостойкость и стойкость к кратерному износу традиционного химического осаждения из паровой фазы (CVD), но также объективно улучшает ударную вязкость. Повышение ударной вязкости происходит в основном за счет уменьшения трещин. Покрытие наносится при высокой температуре, а затем охлаждается в печи. Покрытие содержит трещины, когда инструмент достигает комнатной температуры из-за непостоянного теплового расширения. Подобно царапинам на плоском стекле, эти трещины снижают прочность режущей кромки. Более низкая температура осаждения mtcvd приводит к меньшей частоте трещин и лучшей ударной вязкости режущей кромки.
Когда подложка покрытия CVD и покрытия mtcvd имеют одинаковые характеристики и правку кромок, можно продемонстрировать разницу в их прочности. При использовании в областях, где требуется прочность кромок, характеристики покрытия mtcvd лучше, чем у покрытия CVD. В результате анализа при обработке деталей из P / M с пористой структурой важна прочность кромки. Покрытие MTCVD лучше, чем покрытие CVD.
Покрытие физического осаждения из паровой фазы (PVD) более тонкое и менее износостойкое, чем покрытие mtcvd или CVD. Однако покрытие PVD может выдерживать значительные удары при нанесении. Покрытие PVD эффективно при резке с абразивным износом, CBN и металлокерамика слишком хрупкие и требуют отличной обработки поверхности.
Например, режущая кромка твердого сплава C-2 может быть обработана fc0205 при линейной скорости 180 м / мин и скорости подачи 0.15 мм / оборот. После обработки 20 деталей наросты стружки могут вызвать микроудаление. Использование PVD-покрытия из нитрида титана (TIN) сдерживает нарастание стружки и продлевает срок службы инструмента. При использовании оловянного покрытия для этого испытания ожидается, что характеристики абразивного износа деталей из P / M будут более эффективными с покрытием TiCN. TiCN имеет почти такую же стойкость к образованию стружки, как олово, но он тверже и износостойче, чем олово.
Пористая структура важна, и она влияет на обрабатываемость сплава fc0208. При изменении пористой структуры и характеристик различные инструментальные материалы обеспечивают соответствующие преимущества. При низкой плотности (6.4 г / см3) макротвердость низкая. В этом случае цементированный карбид с покрытием из MTCVD обеспечивает лучшую стойкость инструмента. Микроусталость режущей кромки очень важна, а прочность кромки очень важна. В этом случае лезвие из металлокерамики с хорошей прочностью обеспечивает максимальную стойкость инструмента.
При производстве того же сплава плотностью 6.8 г / см3 абразивный износ становится более важным, чем краевые трещины. В этом случае покрытие mtcvd обеспечивает лучшую стойкость инструмента. Твердый сплав с покрытием PVD используется для испытания двух типов чрезвычайно твердых деталей, и он ломается при соприкосновении с режущей кромкой.
Когда скорость увеличивается (линейная скорость превышает 300 метров в минуту), металлокерамика и даже металлокерамика с покрытием будут вызывать кратерный износ. Твердый сплав с покрытием более подходит, особенно когда ударная вязкость режущей кромки твердого сплава с покрытием является хорошей. Покрытие MTCVD особенно эффективно для цементированного карбида с высоким содержанием кобальта.
Керметы чаще всего используются при точении и растачивании. Твердые сплавы с покрытием PVD идеально подходят для обработки резьбы, поскольку можно ожидать более низких скоростей и большего внимания к наросту.
Сохраните источник и адрес этой статьи для перепечатки.:Резка и механическая обработка деталей из порошковой металлургии (P / M)
Minghe Casting Company специализируется на производстве и предоставлении качественных и высокопроизводительных литых деталей (ассортимент металлических деталей для литья под давлением в основном включает Тонкостенное литье под давлением,Литье под давлением,Литье под давлением в холодной камере), Round Service (Служба литья под давлением,Обработка с ЧПУ,Изготовление пресс-форм, Обработка поверхности) .Любое индивидуальное литье под давлением из алюминия, магния или замака / цинка, а также другие требования к отливкам, пожалуйста, свяжитесь с нами.
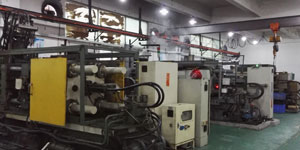
Под контролем ISO9001 и TS 16949, все процессы выполняются на сотнях передовых машин для литья под давлением, 5-осевых станках и других объектах, от струйных до стиральных машин Ultra Sonic. Minghe не только имеет современное оборудование, но и имеет профессиональное оборудование. команда опытных инженеров, операторов и инспекторов для воплощения в жизнь проекта заказчика.
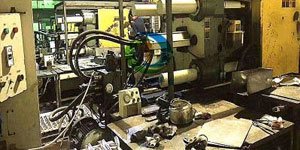
Контрактный производитель отливок под давлением. Возможности включают в себя детали для литья под давлением алюминия с холодной камерой весом от 0.15 фунта. до 6 фунтов, быстрая установка и обработка. Дополнительные услуги включают полировку, вибрацию, удаление заусенцев, дробеструйную очистку, окраску, гальванику, нанесение покрытий, сборку и оснастку. Обрабатываемые материалы включают такие сплавы, как 360, 380, 383 и 413.
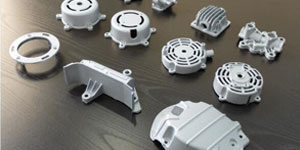
Помощь в проектировании литья цинка под давлением / сопутствующие инженерные услуги. Изготовление на заказ прецизионных отливок из цинка под давлением. Могут изготавливаться миниатюрные отливки, отливки под высоким давлением, отливки в формы с несколькими суппортами, отливки в обычные формы, единичные отливки под давлением и независимые отливки под давлением, а также отливки с герметизацией полости. Отливки могут изготавливаться длиной и шириной до 24 дюймов с допуском +/- 0.0005 дюйма.
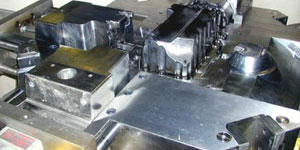
Производитель литья под давлением из магния, сертифицированный по стандарту ISO 9001: 2015. Возможности включают литье под давлением магния под высоким давлением с горячей камерой до 200 тонн и холодной камерой на 3000 тонн, проектирование инструментов, полировку, формование, механическую обработку, порошковую и жидкостную окраску, полный контроль качества с возможностями CMM , сборка, упаковка и доставка.
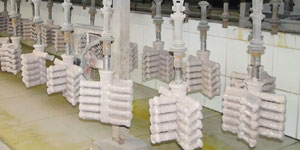
Сертифицирован ITAF16949. Дополнительные услуги трансляции включают инвестиционное литье,литье в песчаные формы,Гравитационное литье, Литье по выплавляемым моделям,Центробежное литье,Вакуумное литье,Постоянное литье формыВозможности включают EDI, техническую поддержку, твердотельное моделирование и вторичную обработку.
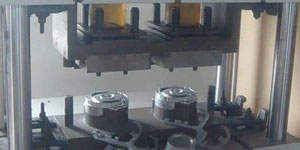
Литейная промышленность Примеры использования запчастей для: автомобилей, велосипедов, самолетов, музыкальных инструментов, судов, оптических устройств, датчиков, моделей, электронных устройств, корпусов, часов, машинного оборудования, двигателей, мебели, ювелирных изделий, приспособлений, телекоммуникаций, освещения, медицинских устройств, фотографических устройств, Роботы, скульптуры, звуковое оборудование, спортивное оборудование, инструменты, игрушки и многое другое.
Что мы можем вам сделать дальше?
∇ Перейти на главную страницу для Литье под давлением Китай
→Литье деталей-Узнай, что мы сделали.
→ Общие советы о Услуги литья под давлением
By Производитель литья под давлением Minghe | Категории: Полезные статьи |Материалы Теги: Литье алюминия, Цинковое литье, Литье магния, Титановое литье, Литье из нержавеющей стали, Латунное литье,Бронзовое литье,Кастинг видео,История компании,Литье алюминия под давлением | Комментарии отключены