Тенденции развития автомобильных отливок и технологий их производства
Литье - один из старейших методов обработки металлов давлением. Примерно от 15% до 20% автозапчастей - это отливки, произведенные различными методами литья. Эти отливки в основном являются ключевыми компонентами энергосистемы и важными конструктивными элементами. В настоящее время технология производства автомобильных отливок в развитых странах в европейской и американской автомобильной промышленности является передовой, с хорошим качеством продукции, высокой производственной эффективностью и низким уровнем загрязнения окружающей среды. Сырье для литья и вспомогательные материалы были сериализированы и стандартизированы, а весь производственный процесс механизирован, автоматизирован и интеллектуален. Эти страны обычно используют цифровые технологии для улучшения проектирования процесса литья. Уровень отказа от кастинга составляет от 2% до 5%, была создана транснациональная система обслуживания и реализована сетевая техническая поддержка. Напротив, хотя производство автомобильного литья в моей стране относительно велико, большинство из них представляют собой черные отливки с относительно низкой добавленной стоимостью и техническим содержанием, а также относительно простой структурой, что далеко от зарубежного уровня. В этой статье в основном обсуждается направление развития автомобильного литья и автомобильной техники из потребностей развития автомобильной энергосбережения и защиты окружающей среды.
Комплексное проектирование автомобильных отливок
С повышением требований к энергосбережению и защите окружающей среды автомобилей и снижению производственных затрат мы будем в полной мере использовать преимущества литья для реализации литья интегрированных деталей за счет разумной конструкции и оптимизации конструкции нескольких деталей, сформированных штамповкой, сваркой, ковка и литье. Формовка может эффективно снизить вес деталей и сократить ненужные процессы обработки, тем самым получая легкие и высокопроизводительные детали.
Основная форма обычного литого монолитного картера оси заключается в том, что бесшовные стальные трубы вдавливаются в два конца картера оси как втулки полуоси и фиксируются штифтами, образуя узел картера оси. Чтобы еще больше повысить прочность и жесткость картера моста и упростить процесс, FAW Group разработала интегрированный картер моста, в котором осевые втулки (детали с обеих сторон картера моста на рис.1) отлиты непосредственно на картер моста. Обработка затруднена, снижение затрат больше, конструкция корпуса оси имеет тенденцию быть простой, а жесткость корпуса оси лучше, может быть сделана сложной и идеальной формы, толщина стенки может быть изменена, может быть получено идеальное распределение напряжений, а его прочность и жесткость оба большие, работают надежно. Благодаря интеграции осевой втулки, размер отливки значительно увеличен. Длина отливки составляет 2 258 мм, а масса единичной детали превышает 200 кг. Принимая во внимание характеристики этого интегрированного литья, компания создала специальную производственную линию для обеспечения производства.
Тенденция развития интеграции автомобильных отливок более очевидна при разработке отливок из цветных сплавов. Для того, чтобы в полной мере использовать характеристики процесса литья, позволяющие производить отливки сложной конструкции, необходимо интегрированное проектирование отливок под высоким давлением, таких как внутренние панели дверей, рамы сидений, рамы приборных панелей, передние рамы и противопожарные перегородки. появился. Размеры значительно больше, чем производимые в настоящее время. Для производства отливок требуется машина для литья под давлением грузоподъемностью от 4 000 до 5 000 тонн или даже больше.
Легкие автомобильные отливки
В целях обеспечения прочности и безопасности автомобиля максимально уменьшите снаряженную массу автомобиля для достижения легкого веса, тем самым повышая мощность автомобиля, снижая расход топлива и уменьшая загрязнение выхлопных газов. На каждые 100 кг снижения снаряженной массы автомобиля расход топлива на 100 км может быть снижен на 0.3–0.6 л. При уменьшении массы автомобиля на 10% топливная эффективность может быть увеличена на 6–8%. Учитывая необходимость защиты окружающей среды и энергосбережения, легкость автомобилей стала тенденцией мирового развития автомобилей, а легкость автомобильных отливок также стала одним из важных направлений развития автомобильного литья.
Легкая конструкция автомобильных отливок
Из-за необходимости обеспечения общего запаса прочности отливок расчет равной толщины является одним из основных методов проектирования автомобильных отливок. Однако основным недостатком конструкции равной толщины является то, что конструктивные характеристики не могут быть полностью использованы, и вес отливки увеличивается. Используйте CAE-анализ, оптимизацию топологии и другие методы для оптимизации конструкции деталей, чтобы значения напряжений частей деталей были близки, то есть толщина стенок каждой детали была непостоянной, а детали с малыми силы истончаются или не нужны для уменьшения деталей. вес. Учитывая, что формовка отливок может реализовывать формовку отливок сложной конструкции, могут быть реализованы различные поперечные сечения неправильной формы. При проектировании используйте CAE или оптимизацию топологии для выполнения анализа нагрузки на компоненты. В соответствии с распределением силы определите форму детали и толщину материала конкретной детали. За счет армирования, выкапывания ям и утолщения отливок можно значительно снизить вес деталей.
Отливки легкосплавные автомобильные
Использование легких сплавов, таких как алюминий и магний, в настоящее время является основной мерой по снижению веса, принятой производителями автомобилей в различных странах. Плотность алюминия составляет всего 1/3 плотности стали, он обладает отличной коррозионной стойкостью и пластичностью. Магний имеет более низкую плотность, всего на 2/3 плотности алюминия, и обладает отличной текучестью в условиях литья под высоким давлением. Удельная прочность (отношение прочности к массе) алюминия и магния довольно высока, что играет решающую роль в снижении собственного веса и повышении эффективности использования топлива. Повышение конкурентоспособности автомобильной промышленности США за последние два года тесно связано с широкомасштабным внедрением алюминиево-магниевых конструкционных отливок и интегрированных отливок.
Новая 5-я серия, выпущенная немецкой компанией BMW, оснащена рядным шестицилиндровым двигателем из магниево-алюминиевого композитного композита последнего поколения, вес которого уменьшен на 10 кг по сравнению с предыдущим поколением, что значительно улучшает характеристики и расход топлива. экономия. Однако следует отметить, что цена на сырье для легких сплавов, таких как алюминий и магний, намного выше, чем на стальные материалы, что ограничивает его более широкое применение в автомобильной промышленности. Однако, несмотря на относительно высокую стоимость сырья, текущее потребление магниевых и алюминиевых отливок для велосипедов из года в год увеличивается. С одной стороны, технический прогресс компенсировал рост затрат. С другой стороны, рыночная конкуренция вынудила автопроизводителей снизить прибыль и использовать больше легких сплавов. Однако для значительного увеличения количества легких сплавов и снижения закупочной цены слитков магния и алюминия разработка передовых технологий формования является одним из ключевых факторов.
Высокая производительность автомобильных литейных материалов
Улучшение характеристик материала, чтобы единичный вес детали мог выдерживать более высокие нагрузки, является одним из методов эффективного снижения веса отливки. Конструкционные отливки кронштейнов составляют большую часть автомобильных отливок, поэтому разработка их отливок стала одним из основных направлений внимания. Благодаря термообработке и другим мерам микроструктура материала изменяется, тем самым улучшая прочность, жесткость или ударную вязкость деталей, что может эффективно снизить вес деталей.
Ковкий чугун после закалки не только имеет более высокую прочность, чем обычные стальные литые материалы, но также имеет более низкую плотность, чем сталь. Его плотность составляет 7.1 г / см3, а плотность литой стали - 7.8 г / см3, которая в последние годы широко рекомендуется в качестве материала. . В нем используется закаленный высокопрочный чугун, который на 10% легче стальных отливок при тех же размерах отливок. Корпорация Dongfeng Motor Corporation провела работы по проверке облегченных грузовых автомобилей определенного типа с использованием закаленного высокопрочного чугуна вместо стальных отливок. В связи с высокими прочностными характеристиками деталей из закаленного высокопрочного чугуна на экспертном форуме было переработано 14 деталей подвески. Вообще говоря, замена материала автомобильных отливок часто сопровождается облегчением конструкции деталей.
В отливках из алюминиевых и магниевых сплавов вместо них используются высокопрочные и высокопрочные материалы. На основе оригинального снижения веса легкого сплава используются высокоэффективные материалы для дальнейшего снижения веса. General Motors в США вместо этого использует высокопроизводительный сплав AE44. В оригинальном алюминиевом сплаве для изготовления подрамника используется литье под высоким давлением, что дополнительно снижает вес алюминиевого сплава на 6 кг.
Цифровизация развития автомобильного литья
Комплексное сочетание развития автомобильного литья и цифровых технологий может значительно улучшить уровень технологии литья и сократить цикл разработки продукта и пробного производства. В настоящее время цифровые технологии производства широко используются при разработке автомобильных отливок. На этапе проектирования отливок и процесса отливки широко использовалось программное обеспечение для трехмерного проектирования, такое как Pro / E, CATIA и UG, а некоторые передовые литейные компании реализовали безбумажное проектирование. Программное обеспечение, такое как MAGMA, ProCAST и Huazhu CAE, широко используется для моделирования процесса затвердевания, микроструктуры, разделения состава и свойств материалов автомобильных отливок. Он также может анализировать поле скорости, поле концентрации, поле температуры и фазу в процессе литья. Моделирование полей, полей напряжений и т. Д. Может гарантировать оптимизацию технологического плана перед массовым производством.
Для удовлетворения потребностей быстрого развития автомобильных отливок, основанных на проектировании и разработке CAD / CAE, RP (технология быстрого прототипирования) широко использовалась для быстрого пробного производства автомобильных отливок. После получения исходных данных CAD / CAE применяется послойный метод для получения прототипа отливки или прототипа формы, необходимой для формирования отливки путем соединения, спекания или спекания. Первые могут представлять собой опытные образцы отливок с помощью литья по выплавляемым моделям, гипсового литья и других методов, в то время как последние могут быть непосредственно использованы в качестве формы для изготовления песчаных стержней, а отливки могут быть отлиты посредством моделирования сборки стержней. Кроме того, метод порошкового лазерного спекания (SLS) можно использовать для непосредственного завершения производства песчаных стержней и песчаных форм, чтобы получить песчаные формы, необходимые для пробного производства отливок. Для наружных форм с относительно простой конструкцией станки с ЧПУ могут также использоваться для обработки CAM с обрабатываемыми пластиками для получения стержневого ящика и шаблона, необходимого для пробного производства отливок, или непосредственно обрабатывать песчаный блок для получения песчаной формы для внешней формы. напрямую.
Вообще говоря, цифровые технологии проникли во все аспекты проектирования, разработки и пробного производства отливок, эффективно повысив скорость и эффективность разработки отливок. Основная проблема в настоящее время заключается в том, что цифровые технологии проектирования, анализа и быстрого производства независимы друг от друга. Когда процесс разработки переводится с одного этапа на другой, также требуется довольно утомительная работа по преобразованию данных. Есть надежда, что в будущем можно будет разработать унифицированную платформу интерфейса данных для цифровых технологий, применяемых во всех аспектах разработки отливок, и можно будет установить стандартизированные стандарты преобразования данных для обеспечения беспрепятственного преобразования данных между различным программным обеспечением с целью дальнейшего увеличения скорость развития отливок.
Технология производства тонкостенных отливок сложной конструкции.
С развитием автомобильной промышленности и потребностями в энергосбережении и сокращении выбросов автомобильные детали становятся все легче и легче. Снижение веса за счет тонкостенной конструкции является важным направлением развития блоков цилиндров. В качестве примера возьмем компанию FAW Casting Co., Ltd., которая занимается производством блоков цилиндров из чугуна FAW-Volkswagen. Блок цилиндров 06A раннего выпуска имеет толщину стенок 4.5 мм ± 1.5 мм, а блок цилиндров EA111 имеет толщину стенки 4 мм ± 1 мм. Текущий серийно выпускаемый блок цилиндров EA888Evo2 имеет толщину стенок 4 мм ± 1 мм. 3.5 мм ± 0.8 мм, структура продукта блока цилиндров следующего поколения EA888Gen.3 более сложна, его толщина стенки составляет всего 3 мм ± 0.5 мм, в настоящее время это самый тонкий блок цилиндров из серого чугуна. Несмотря на то, что при массовом производстве возникают проблемы с сломанными стержнями, плавающими стержнями и большими колебаниями толщины стенок, благодаря контролю качества песчаных стержней и формовочного песка широко используемый процесс горизонтальной разливки по-прежнему может соответствовать производственным требованиям цилиндров EA888Evo2. Но он не может соответствовать производственным требованиям блока цилиндров EA888Gen.3, поэтому необходимо принять весь процесс вертикального литья сердечника в сборе.
Технология изготовления крупногабаритных конструкционных деталей из алюминиево-магниевого сплава.
В связи с повышением требований к энергосбережению, защите окружающей среды и снижению стоимости компонентов крупногабаритные конструкционные отливки из алюминиево-магниевого сплава стали важной тенденцией развития, а технология их производства также стала основным направлением развития. В настоящее время основными технологиями производства крупногабаритных конструкционных деталей из алюминиево-магниевого сплава являются литье под высоким давлением, литье под давлением и литье под низким давлением. Благодаря высокой эффективности производства литья под высоким давлением и хорошему качеству продукции, в настоящее время он стал основным производственным процессом. Разработка технологии производства в основном направлена на облегчение улавливания газа в процессе литья под высоким давлением и образование пор внутри отливок, что не может решить проблему термической обработки.
Немецкая компания Fulai разработала процесс литья под вакуумом и отрицательным давлением, весь процесс литья под давлением осуществляется под высоким вакуумом (менее 30 мбар). Расплавленный металл проходит через форму, камеру давления и всасывающую трубу в вакууме и всасывается из печи всасывающей трубой без окисления, а пары разделительного агента также выводятся вакуумной системой. Основными особенностями вышеупомянутого процесса разливки с отсасыванием под вакуумом являются: когда начинается количественная разливка, вся система находится в состоянии высокого вакуума; в процессе количественной разливки газ из полости и расплавленный металл могут эффективно отводиться; в процессе разливки не происходит окисления металлического расплава; нет потерь тепла во время процесса разливки, и для разливки можно использовать более низкую температуру разливки, а заполнение непрерывным ламинарным потоком может выполняться под контролем в реальном времени. Вышеупомянутый процесс был успешно применен к массовому производству автомобильных конструкционных отливок Auto Expert Forum, обеспечивая передовые методы и процессы формования для применения высококачественных отливок из легких сплавов.
Швейцарская компания Buhler разработала двухконтурную вакуумную систему для производства конструкционных отливок. Эта технология производства называется структурной технологией производства. Использование структурной технологии производства позволяет увеличить скорость вакуумирования, тем самым получить стабильные производственные условия и значительно улучшить качество деталей при литье под давлением. Как показано на рис. 5, отверстие для вытяжки воздуха одного контура в двухконтурной вакуумной системе расположено в верхнем конце напорной камеры и в основном используется для удаления воздуха из напорной камеры. Он начинается, когда впрыскивающий поршень движется вперед, чтобы закрыть разливочное отверстие, и закрывается, когда поршень собирается закрыть всасывающий порт. Настройка другого контура такая же, как и для традиционного процесса вакуумирования, и в основном используется для удаления воздуха из полости. В настоящее время технология успешно применяется при изготовлении интегрированных амортизирующих опор из алюминиевого сплава, внутренних панелей дверей и направляющих кузова легковых автомобилей.
Технология прецизионного литья под давлением для отливок
Обычно называемое прецизионным литьем автомобильных отливок в основном относится к технологии литья по выплавляемым моделям и литья по выплавляемым моделям. С развитием технологии формовки автомобильных отливок прецизионное формование отливок относится к типу методов формовки отливок. Отливки, изготовленные с помощью этого метода формования, можно использовать напрямую, без резки или меньшей резки. С повышением требований к точности размеров отливок в последние годы быстро развивалась технология точного литья, и появился ряд новых методов литья, таких как прецизионное литье в песчаные формы, литье по потерянной пене, литье под давлением и литье под давлением. Метод литья Cosworth - это метод, разработанный в Соединенном Королевстве, который использует узел сердечника из циркониевого песка и электромагнитный насос для управления разливкой. Он успешно используется в массовом производстве блоков цилиндров из алюминиевого сплава, и появилось множество вариантов процесса, таких как использование заливки под низким давлением вместо электромагнитных процессов, таких как заливка насосом. С помощью этого метода литья можно производить цилиндры из алюминиевого сплава с толщиной стенки от 3.5 до 4.0 мм, что в настоящее время является типичным представителем прецизионного литья в песчаные формы.
Процесс литья по выплавляемой пене был изобретен в 1965 году, и основные производимые автомобильные отливки - это блоки цилиндров, головки цилиндров, впускные и выпускные трубы и другие изделия, которые стали массовым производством. С момента внедрения технологии литья по выплавляемым моделям в 1990-х годах в 20-м веке моя страна начала формироваться, и государство продвигало ее как наиболее широко используемую передовую и новую технологию для преобразования традиционной литейной промышленности. В настоящее время в моей стране существует три процесса прецизионного литья по выплавляемым моделям: оболочка из силиката натрия, композитная оболочка и оболочка из золя кремния. Среди них качество поверхности отливки, используемой при производстве оболочки из золя кремниевой кислоты для автомобильных изделий, может достигать Ra 1.6 мкм, а точность размеров может достигать CT4. Марка, минимальная толщина стенки может составлять 0.5 ~ 1.5 мм. Компания Dongfeng Motor Precision Casting Co., Ltd. применяет процесс изготовления композитной оболочки золь кремния + жидкое стекло для производства интегрированных отливок сложной конструкции, что значительно снижает производственные затраты. Тенденция развития процесса литья по выплавляемым моделям заключается в том, что отливки становятся все ближе и ближе к конечному продукту, а сложность и качество продуктов становятся все выше и выше. Применение CAD, CAM и CAE стало основной технологией разработки продуктов, и начало проявляться профессиональное сотрудничество.
Вакуумное литье, литье под давлением с кислородным наполнением, реологическое или тиксотропное литье полутвердого металла и другие технологические методы, разработанные на основе процесса литья под высоким давлением, предназначены для устранения дефектов литья, улучшения внутреннего качества и расширения области применения литья под давлением. . Во время процесса литья под давлением расплав заполняется и затвердевает под давлением, что имеет такие преимущества, как гладкость, отсутствие брызг металла, меньшие потери жидкого металла при окислении, экономия энергии, безопасная работа и уменьшение отверстий для литья и других дефектов. Он используется в подрамниках из алюминиевого сплава и т. Д. Широкое распространение получили разработка и применение отливок из алюминиевого сплава с высокими эксплуатационными характеристиками.
Непрерывный рост производства автомобилей настоятельно требует развития литейного производства в направлении высокого качества, отличных характеристик, почти чистой формы, разнообразия разновидностей, низкого потребления и низкой стоимости. Потому что от 15% до 20% деталей автомобиля - отливки. Это требует от литейной промышленности постоянного применения различных новых технологий и новых материалов для улучшения общего уровня литья. Технология прецизионного литья под давлением отливок может удовлетворить вышеупомянутые требования к автомобильным отливкам, и ее применение также будет охватывать различные процессы производства отливок автомобильных отливок.
Заключение
Чтобы соответствовать все более строгим требованиям экологических норм, автомобили развиваются в направлении уменьшения веса. На каждые 10% снижения веса транспортного средства расход топлива может быть снижен на 5.5%, экономия топлива может быть увеличена на 3–5%, а выбросы могут быть сокращены примерно на 10%. Применение отливок из алюминиево-магниевых и других цветных сплавов, разработка крупномасштабных комплексных отливок со сложной структурой и широкое применение технологии прецизионного литья под давлением являются основными способами получения легких автомобильных отливок. Следовательно, для удовлетворения потребностей современной автомобильной промышленности необходимо осуществлять исследования, разработки и производство автомобильных отливок с использованием высококачественных литейных материалов и широкого применения средств автоматизации на основе широкого использования цифровых технологий.
Сохраните источник и адрес этой статьи для перепечатки.: Тенденции развития автомобильных отливок и технологий их производства
Минхэ Компания по литью под давлением специализируются на производстве и предоставлении качественных и высокопроизводительных литых деталей (ассортимент металлических деталей для литья под давлением в основном включает Тонкостенное литье под давлением,Литье под давлением,Литье под давлением в холодной камере), Round Service (Служба литья под давлением,Обработка с ЧПУ,Изготовление пресс-форм, Обработка поверхности) .Любое индивидуальное литье под давлением из алюминия, магния или замака / цинка, а также другие требования к отливкам, пожалуйста, свяжитесь с нами.
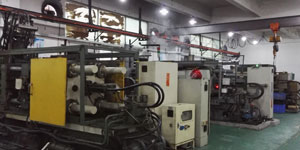
Под контролем ISO9001 и TS 16949, все процессы выполняются на сотнях передовых машин для литья под давлением, 5-осевых станках и других объектах, от струйных до стиральных машин Ultra Sonic. Minghe не только имеет современное оборудование, но и имеет профессиональное оборудование. команда опытных инженеров, операторов и инспекторов для воплощения в жизнь проекта заказчика.
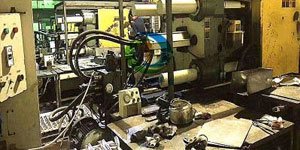
Контрактный производитель отливок под давлением. Возможности включают в себя детали для литья под давлением алюминия с холодной камерой весом от 0.15 фунта. до 6 фунтов, быстрая установка и обработка. Дополнительные услуги включают полировку, вибрацию, удаление заусенцев, дробеструйную очистку, окраску, гальванику, нанесение покрытий, сборку и оснастку. Обрабатываемые материалы включают такие сплавы, как 360, 380, 383 и 413.
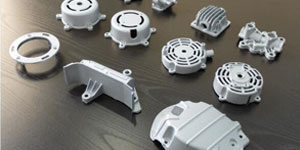
Помощь в проектировании литья цинка под давлением / сопутствующие инженерные услуги. Изготовление на заказ прецизионных отливок из цинка под давлением. Могут изготавливаться миниатюрные отливки, отливки под высоким давлением, отливки в формы с несколькими суппортами, отливки в обычные формы, единичные отливки под давлением и независимые отливки под давлением, а также отливки с герметизацией полости. Отливки могут изготавливаться длиной и шириной до 24 дюймов с допуском +/- 0.0005 дюйма.
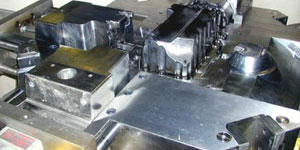
Производитель литья под давлением из магния, сертифицированный по стандарту ISO 9001: 2015. Возможности включают литье под давлением магния под высоким давлением с горячей камерой до 200 тонн и холодной камерой на 3000 тонн, проектирование инструментов, полировку, формование, механическую обработку, порошковую и жидкостную окраску, полный контроль качества с возможностями CMM , сборка, упаковка и доставка.
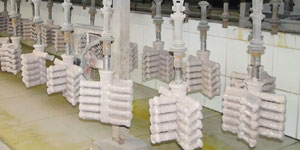
Сертифицирован ITAF16949. Дополнительные услуги трансляции включают инвестиционное литье,литье в песчаные формы,Гравитационное литье, Литье по выплавляемым моделям,Центробежное литье,Вакуумное литье,Постоянное литье формыВозможности включают EDI, техническую поддержку, твердотельное моделирование и вторичную обработку.
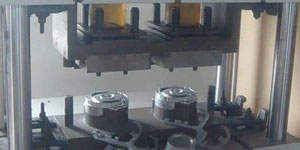
Литейная промышленность Примеры использования запчастей для: автомобилей, велосипедов, самолетов, музыкальных инструментов, судов, оптических устройств, датчиков, моделей, электронных устройств, корпусов, часов, машинного оборудования, двигателей, мебели, ювелирных изделий, приспособлений, телекоммуникаций, освещения, медицинских устройств, фотографических устройств, Роботы, скульптуры, звуковое оборудование, спортивное оборудование, инструменты, игрушки и многое другое.
Что мы можем вам сделать дальше?
∇ Перейти на главную страницу для Литье под давлением Китай
→Литье деталей-Узнай, что мы сделали.
→ Общие советы о Услуги литья под давлением
By Производитель литья под давлением Minghe | Категории: Полезные статьи |Материалы Теги: Литье алюминия, Цинковое литье, Литье магния, Титановое литье, Литье из нержавеющей стали, Латунное литье,Бронзовое литье,Кастинг видео,История компании,Литье алюминия под давлением | Комментарии отключены