Как обеспечить стабильность системы зеленого песка?
I. Введение
Из-за изменений производственных условий и окружающей среды неизбежно изменятся другие параметры отливки. Если процесс формовочного песка невозможно отрегулировать вовремя, песчаная система будет нестабильной, что в конечном итоге приведет к более сложной очистке отливки или даже к лому;
Таким образом, необходимо скорректировать исходный процесс формовочной смеси для стабилизации песчаной системы; Материальный состав формовочного песка в основном состоит из старого песка, сырого песка, бентонита и добавок. Поскольку более 95% формовочного песка составляет старый песок, и на старый песок влияют такие факторы, как различное соотношение песка и железа в отливке и различное количество смеси для стержневого песка, что приводит к очень большим колебаниям материальный состав. Следовательно, чтобы контролировать состав формовочного песка, необходимо проверить эффективное содержание бентонита, эффективное содержание добавок и содержание грязи в формовочном песке, чтобы определить добавленное количество бентонита, добавок и сырого песка во время перемешивания песка.
В этой статье мы кратко расскажем, как литейный цех компании автора укореняется в реальном производственном процессе.
В соответствии с изменением параметров процесс формовочной смеси регулируется для обеспечения устойчивости песчаной системы.
2. Определение основных параметров формовочной смеси:
1. Эффективное содержание бентонита: эффективное содержание бентонита (активного) определяется на основе характеристик минерала монтмориллонита, содержащегося в бентоните, который может поглощать метиленовый синий и другие красители; это относится к титрованию 5.00 г формовочного песка с 0.20% -ным раствором реагента чистого метиленового синего [мл]; преобразовано по формуле стандартной кривой бентонита (%)
2. Эффективная дозировка добавки: сравнивается с выделением газа добавками для формовочного песка и рассчитывается по формуле; то есть выделение газа 1.00 г формовочного песка при 900 ° C [мл] минус газовыделение активированного бентонита в формовочном песке (среднее количество, измеренное перед расчетом). Затем сравните с 1 г дополнительного объема газа (%).
3. Содержание грязи. В соответствии с национальным стандартом GB / T9442-1998 мелкие частицы порошка диаметром менее 20 мкм считаются грязью. Шлам обычно удаляют методом промывки [2].
4. Размер частиц формовочного песка: выражается в тонкости AFS, то есть средний размер частиц песка отображается в соответствии с воображаемой меткой сита [3];
5. Метод расчета тонкости помола AFS: Процедуры измерения тонкости помола AFS и методы расчета, определенные Американским институтом литейного производства, следующие:
①. Сначала взвесьте около 50 г измеряемого образца песка, смойте грязь, просушите и просейте.
②. Взвесьте и запишите качество частиц песка, оставшихся на каждом сите;
③. Рассчитайте процентное соотношение количества частиц песка, оставшихся на каждом сите, к общему количеству образцов песка;
④. Умножьте процент количества частиц песка, оставшихся на каждом сите, на «множитель тонкости помола AFS», соответствующий каждому сите;
⑤. Чтобы найти сумму, сложите указанные выше продукты для каждого номера сита:
⑥. Разделите сумму, полученную в пункте 5, на сумму процентов задержанного песка на каждом сите в пункте 3, чтобы получить тонкость помола AFS.
3. План корректировки:
Оборудование для перемешивания песка, используемое на заводе, - это песочная мельница DISA и формовочное оборудование KW, линия статического прессования под давлением; Используя статистические данные за полгода, были сформулированы следующие планы для его системы формовочной смеси:
1. Статистика:
① Определите количество формовочного песка, добавляемого в каждую коробку, в соответствии со значением настройки формовочной основы, и рассчитайте соотношение песка и железа для каждой коробки отливок в соответствии с весом каждой коробки с отливками и весом заливки. система и количество стержневого песка, используемого при отливке;
②Статистика количества сброшенного отработанного песка и использования основного песка и вспомогательных материалов
③ Статистика пылеудаления формовочной системы
2. Регулировка песка:
① В зависимости от производственной ситуации, когда отливка производится непрерывно в течение двух или более дней, добавляемое количество вспомогательных материалов для формовочной смеси (бентонит, добавки) должно быть зафиксировано, и изменения в эффективном количестве формовочной смеси должны быть подсчитаны, и затем постепенно проверяется во время непрерывного производства других отливок. Связь между соотношением песка и железа и добавленным количеством;
② Регулировка размера частиц формовочного песка: отрегулируйте в соответствии со средним значением сита 50/100 (кварцевый песок сита 50/100, среднее значение средней крупности составляет 50 [4]), когда AFS формовочного песка составляет меньше или равно 50, добавляя мелкий песок 70/140 или более мелкий, новый песок 140/70 корректируется, добавляется 30-60 кг на мельницу, и анализируется изменение размера частиц.
③ Регулировка содержания грязи в формовочной смеси: анализ изменения содержания грязи в формовочной смеси посредством статистики ежедневного удаления пыли;
В-четвертых, конкретный процесс настройки:
1. Статистика соотношения литейного песка и железа:
(Примечание: поскольку корпус цилиндра X2B1 отлит со встроенным песчаным сердечником, он не сжигает формовочный песок, поэтому вес внешнего формовочного песка отливки рассчитывается как "0")
2. Отрегулируйте эффективное количество в соответствии с соотношением песка и железа в отливке. Соотношение песка и железа в блоке цилиндров 56D составляет 6.57. Среди вышеуказанных отливок соотношение песка и железа является самым высоким среди отливок блока цилиндров. Поэтому сначала испытывается блок цилиндров 56D:
Когда 56D производили в течение трех последовательных дней, количество добавки составляло 22 кг / мельница, а количество добавки глины составляло 33 кг / мельница; эффективное количество добавок увеличилось с 4.55% до 5.03%; эффективное количество глины увеличилось с 6.56% до 7%; увеличение примерно на 0.5%; Это означает, что при изготовлении цилиндра 56D добавляемое количество должно быть отрегулировано так, чтобы оно превышало балансовое значение песчаной системы;
В результате анализа данных, приведенного выше, количество добавленных вспомогательных материалов корректируется следующим образом:
1) При воспроизведении цилиндра количество добавки устанавливается на 19 кг / мельница, а когда количество добавки глины составляет 26 кг / мельница, статистические данные за три последовательных дня показывают, что эффективное количество добавок изменилось с 4.36% до 4.29%. ; эффективное количество глины изменилось с 4.36% до 4.29%. 7.22% становится 7.11%; эффективное количество колеблется на 0.1%; следовательно, план регулировки процесса является разумным и может обеспечить баланс системы формовочной смеси;
2) Аналогичным образом соотношение между количеством вспомогательных материалов, добавленных к другим отливкам, и эффективным количеством рассчитывается с помощью анализа экспериментальных данных и теории; при воспроизведении различных отливок отрегулируйте необходимое количество добавленных вспомогательных материалов.
3. Используйте новый песок 70/140 меш и новый песок 140/70, чтобы отрегулировать размер песка (содержание грязи в песке-прототипе составляет 11.42%):
① С 16 января по 21 января всего 4257 раз шлифовки песка за пять дней, примерно 4257 * 3/900 = 14 раз; размер частиц в каждом цикле изменяется примерно на 0.26 (за измельчение); следовательно, формовочный песок 16 января. Значение AFS составляет 49.15; с 16 января, пять дней непрерывного добавления 70/140 нового песка для корректировки размера частиц, 60 кг на мельницу, значение AFS формовочного песка 21 января составляет 52.84;
② С 25 по 27 января в общей сложности 2165 раз шлифовки песка за три дня, примерно 2165 * 3/900 = 7 циклов; размер зерна в каждом цикле изменяется примерно на 0.22 (за измельчение); поэтому 24 января песок AFS = 52.44, когда размер частиц формовочного песка достигает 52-53, непрерывное добавление нового песка 70/140 мало влияет на песчаную систему AFS; начиная с 26 января, 140/70 нового песка добавляется в течение трех дней подряд для корректировки, и добавляется 60 кг для каждого измельчения1. 28-го числа AFS песка составляет 54.
(Примечание: ①Стандарт предприятия FAW предусматривает, что скорость просеивания 70/140 кварцевого песка 70,100,140 ≥80%, из которых 70,100 просеивания ≥60%; 140/70 кварцевого песка 70,100,140 скорость рассева ≥80%, из которых 100,140 степень рассева ≥60 % ②Каждый объем измельчения составляет 3 тонны, а объем песка в системе оценивается в 900 тонн)
4. Сравнение содержания грязи и удаления пыли за три месяца подряд:
Из-за холодного климата на севере с февраля по март пыль в трубопроводе холодного удаления пыли будет конденсироваться и затвердевать после удаления горячей пыли. Если вовремя не очистить трубопровод, засорения будут происходить часто, а суточный сброс будет колебаться от 4 до 8 тонн. Содержание грязи в песчаной системе сильно колеблется. В течение этого периода единственный способ повысить производительность по удалению пыли и уменьшить содержание грязи - это увеличить объем воздуха в пылеулавливающем оборудовании и провести дноуглубительные работы на трубопроводах;
После вступления в апрель температура постепенно повышалась, явления конденсации и затвердевания пыли больше не возникали, количество удаляемой пыли постепенно стабилизировалось, достигнув среднего расхода 7-8 тонн в сутки, а диапазон колебаний содержания грязи уменьшился;
Содержание грязи в системе формовочного песка также можно уменьшить, добавив новый песок или уменьшив добавление вспомогательных материалов. Недостатки этих двух методов будут объяснены в заключении теста.
5. Заключение теста
1. Отрегулируйте эффективное количество насадки для песка.
Кристаллы бентонита в определенной степени повреждаются при нагревании, и прочность сцепления во влажном состоянии, очевидно, снизится после добавления воды и перемешивания. После нагревания при более высокой температуре и в течение более длительного времени кристаллическая структура бентонита полностью разрушается, и он становится «мертвой глиной» без силы сцепления. Увеличенная толщина отливки, низкое соотношение песка и железа, высокая температура разливки и длительное время охлаждения - все это увеличивает потери бентонита при горении.
Самый простой способ определить, достаточно ли эффективного угольного порошка в формовочном песке, - это посмотреть на гладкость поверхности отливки и на наличие прилипания песка. Часть угля в старом песке сгорает из-за тепла разлитого расплавленного металла и нуждается в пополнении. С другой стороны, новые добавленные материалы, такие как свежий песок, смешанный керновой песок и бентонит, также должны быть добавлены для достижения уровня эффективного измельченного угля. Общее количество пылевидного угля, добавленного во время перемешивания песка, представляет собой сумму потерь от горения и дополнительного дополнительного количества. (Эффективный угольный порошок эквивалентен эффективной добавке в тексте)
2. Регулировка размера песка:
Размер частиц формовочного песка под высоким давлением обычно составляет 50/140, в то время как размер частиц сердцевины смоляного песка обычно составляет 50/100 или более крупный. Чрезмерное перемешивание стержневого песка повлияет на укрупнение всего старого влажного песка, что увеличит проницаемость песка и шероховатость поверхности отливки.
Чтобы частицы формовочного песка не становились крупными, частицы из системы пылеудаления могут быть переработаны в старый песок. Или добавьте новый мелкий песок для корректировки; как упоминалось в литейном производстве, когда AFS формовочного песка достигает примерно 48, отрегулируйте, непрерывно добавляя 70/140 или 140/70 нового песка; однако из-за того, что отливки разбиваются о сердцевину песчаной системы, количество песка уже велико. Если размер частиц формовочного песка не увеличился до невыносимой степени, не рекомендуется добавлять такое большое количество нового песка непрерывно, иначе это повлияет на другие рабочие показатели системы формовочного песка (содержание грязи, эффективное количество и прочность из-за чрезмерного количества нового песка). ) иметь влияние на;
3. Регулировка содержания бурового раствора.
Увеличение содержания бурового раствора вызовет снижение проницаемости формовочного песка, и в процессе заливки произойдет явление «взрыва газа», и отливка будет утилизирована из-за взрыва и липкого песка. Содержание грязи в системе формовочного песка не должно быть слишком высоким; содержание бурового раствора в песчаной системе может быть уменьшено за счет уменьшения количества вспомогательных материалов, но уменьшение эффективного содержания бентонита приведет к снижению прочности формовочного песка и уменьшит способность поднимать и противостоять песку; эффективная дозировка Decrease приведет к снижению способности формовочного песка к предотвращению прилипания.
Если вы увеличиваете количество нового песка, добавляемого для корректировки содержания бурового раствора, сначала подсчитайте, сколько грязи производят различные вновь добавленные материалы в литом песке, а затем вы можете рассчитать, сколько необработанного песка необходимо добавить, чтобы сделать содержание грязи равным формовочная смесь соответствует технологическим регламентам.
Как упоминалось в статье, содержание бурового раствора можно снизить на 0.1% на каждые 30 кг нового песка, добавляемого в литейный цех; однако чрезмерное добавление нового песка не только приведет к потере затрат, но также снизит долю использованного песка в системе формовочной смеси, что снизит производительность формовочной смеси. , Формовочный песок расходится, что влияет на способность формовочного песка к формованию, и в процессе литья возникает явление промывки песка;
Поэтому автор считает, что это лучший выбор, если содержание грязи в песчаной системе можно регулировать путем регулировки оборудования для удаления пыли.
В целом, система стабилизированного песка позволяет производить отливки высокого качества. Используя эту концепцию, мы должны постоянно корректировать процесс формования формовочной смеси в соответствии с изменяющимися условиями производства для удовлетворения производственных потребностей.
Сохраните источник и адрес этой статьи для перепечатки.: Как обеспечить стабильность системы зеленого песка?
Минхэ Компания по литью под давлением специализируются на производстве и предоставлении качественных и высокопроизводительных литых деталей (ассортимент металлических деталей для литья под давлением в основном включает Тонкостенное литье под давлением,Литье под давлением,Литье под давлением в холодной камере), Round Service (Служба литья под давлением,Обработка с ЧПУ,Изготовление пресс-форм, Обработка поверхности) .Любое индивидуальное литье под давлением из алюминия, магния или замака / цинка, а также другие требования к отливкам, пожалуйста, свяжитесь с нами.
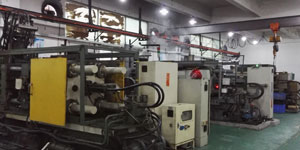
Под контролем ISO9001 и TS 16949, все процессы выполняются на сотнях передовых машин для литья под давлением, 5-осевых станках и других объектах, от струйных до стиральных машин Ultra Sonic. Minghe не только имеет современное оборудование, но и имеет профессиональное оборудование. команда опытных инженеров, операторов и инспекторов для воплощения в жизнь проекта заказчика.
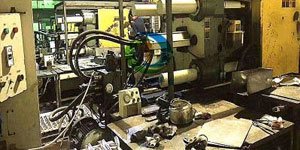
Контрактный производитель отливок под давлением. Возможности включают в себя детали для литья под давлением алюминия с холодной камерой весом от 0.15 фунта. до 6 фунтов, быстрая установка и обработка. Дополнительные услуги включают полировку, вибрацию, удаление заусенцев, дробеструйную очистку, окраску, гальванику, нанесение покрытий, сборку и оснастку. Обрабатываемые материалы включают такие сплавы, как 360, 380, 383 и 413.
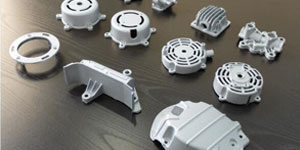
Помощь в проектировании литья цинка под давлением / сопутствующие инженерные услуги. Изготовление на заказ прецизионных отливок из цинка под давлением. Могут изготавливаться миниатюрные отливки, отливки под высоким давлением, отливки в формы с несколькими суппортами, отливки в обычные формы, единичные отливки под давлением и независимые отливки под давлением, а также отливки с герметизацией полости. Отливки могут изготавливаться длиной и шириной до 24 дюймов с допуском +/- 0.0005 дюйма.
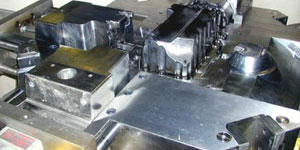
Производитель литья под давлением из магния, сертифицированный по стандарту ISO 9001: 2015. Возможности включают литье под давлением магния под высоким давлением с горячей камерой до 200 тонн и холодной камерой на 3000 тонн, проектирование инструментов, полировку, формование, механическую обработку, порошковую и жидкостную окраску, полный контроль качества с возможностями CMM , сборка, упаковка и доставка.
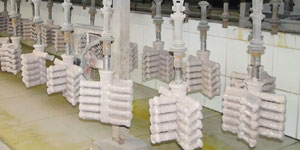
Сертифицирован ITAF16949. Дополнительные услуги трансляции включают инвестиционное литье,литье в песчаные формы,Гравитационное литье, Литье по выплавляемым моделям,Центробежное литье,Вакуумное литье,Постоянное литье формыВозможности включают EDI, техническую поддержку, твердотельное моделирование и вторичную обработку.
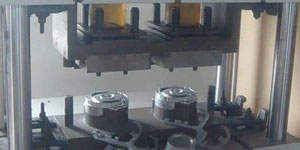
Литейная промышленность Примеры использования запчастей для: автомобилей, велосипедов, самолетов, музыкальных инструментов, судов, оптических устройств, датчиков, моделей, электронных устройств, корпусов, часов, машинного оборудования, двигателей, мебели, ювелирных изделий, приспособлений, телекоммуникаций, освещения, медицинских устройств, фотографических устройств, Роботы, скульптуры, звуковое оборудование, спортивное оборудование, инструменты, игрушки и многое другое.
Что мы можем вам сделать дальше?
∇ Перейти на главную страницу для Литье под давлением Китай
→Литье деталей-Узнай, что мы сделали.
→ Общие советы о Услуги литья под давлением
By Производитель литья под давлением Minghe | Категории: Полезные статьи |Материалы Теги: Литье алюминия, Цинковое литье, Литье магния, Титановое литье, Литье из нержавеющей стали, Латунное литье,Бронзовое литье,Кастинг видео,История компании,Литье алюминия под давлением | Комментарии отключены