Различные факторы, влияющие на стабильность размеров отливок по выплавляемым моделям
Постоянное повышение точности размеров отливок по выплавляемым моделям и сокращение количества отходов, вызываемых слишком большими размерами, всегда было одной из основных целей, преследуемых рабочими по литью по выплавляемым моделям в стране и за рубежом.
1. Стабильность размеров отливок по выплавляемым моделям.
1. Стабильность размеров восковой модели и влияющие на нее факторы.
В большинстве случаев размер восковой формы сильно колеблется, когда колеблется размер отливки, и есть несколько исключений. В целом колебания размеров восковой формы составляют от 10% до 70% колебаний размеров отливки.
Параметры процесса формования имеют решающее влияние на стабильность размеров восковой формы. Основные факторы следующие:
(1) Температура прессования воска
Различные формовочные материалы имеют разные характеристики из-за влияния температуры прессования воска. Когда используются формовочные материалы на основе воска, температура прессования воска очень чувствительна к влиянию стабильности размеров восковой формы, в то время как формовочные материалы на основе смолы имеют меньшее влияние.
(2) Давление впрыска
Когда давление невелико, степень усадки восковой формы значительно уменьшается при увеличении давления. Однако после некоторого повышения давления (≥1.6 МПа) давление почти не влияет на размер восковой формы. Неудивительно, что по результатам зарубежных испытаний часто делается вывод о том, что «давление не имеет ничего общего с размером восковой формы», но впечатление многих отечественных компаний не совсем такое.
(3) Скорость потока
Скорость потока материала формы можно изменить двумя способами, но влияние на размер восковой формы неодинаково:
· Изменяя настройку скорости потока воскового пресса, этот метод мало влияет на усадку восковой формы. Однако он оказывает важное влияние на заполнение и качество поверхности тонкостенных деталей сложной формы или восковых форм с стержнями.
· Этот метод имеет большое влияние за счет изменения площади поперечного сечения порта для впрыска парафина, поскольку увеличение площади поперечного сечения порта для впрыска парафина может не только снизить температуру прессования парафина, но и продлить затвердевание. время нахождения материала формы в отверстии для впрыска парафина, тем самым увеличивая уплотнение формы для парафина. Степень усадки и поверхностной усадки снижается.
(4) Время впрыска
Так называемое время впрыска здесь включает три периода наполнения, уплотнения и выдержки. Время заполнения относится к времени, в течение которого формовочный материал заполняет формовочную полость; уплотнение относится к времени от заполнения формованного изделия до закрытия сопла для впрыскивания парафина; и выдержка относится ко времени от закрытия сопла для впрыска парафина до выталкивания формы.
Время впрыска существенно влияет на степень усадки восковой формы. Это связано с тем, что большее количество материала формы может быть выдавлено в полость за счет увеличения времени впрыска, и восковая форма будет более уплотнена, тем самым уменьшая степень усадки. Вес восковой модели увеличивается с увеличением времени уплотнения. Время уплотнения должно быть подходящим. Если время уплотнения слишком велико, материал формы в отверстии для впрыска парафина полностью затвердеет, и уплотнение не будет работать. Из рисунка 4 также видно, что при коротком времени впрыска (15-25 с) температура прессования парафина повышается, а степень усадки увеличивается; но когда время впрыска увеличивается до 25-35 с (при условии, что время наполнения остается постоянным, фактическое значение выше должно продлить время уплотнения), влияние температуры прессования парафина становится меньше; когда время впрыска увеличивается до более чем 35 секунд, возникает противоположная ситуация, то есть при повышении температуры прессования парафина вместо этого уменьшается степень усадки восковой формы. Это явление можно объяснить тем, что повышение температуры материала формы и увеличение времени уплотнения имеют тот же эффект, что и увеличение степени уплотнения восковой формы.
(5) Температура формования и оборудование для прессования воска.
Температура формования высока, восковая форма охлаждается медленно, а степень усадки увеличивается. Это связано с тем, что восковая форма все еще находится в компрессионном формовании перед выталкиванием формы, и усадка ограничена, но после выталкивания формы она становится свободной для усадки. Следовательно, если температура формы для воска высока, когда форма освобождена, конечная степень усадки будет большой, и, наоборот, степень усадки будет небольшой.
Таким же образом система охлаждения воскового пресса может влиять примерно на 0.3% на размер восковой формы.
Наконец, стоит подчеркнуть, что при использовании материалов для форм на основе воска восковая паста представляет собой трехфазную систему сосуществования твердого вещества, жидкости и газа. Соотношение объемов между тремя фазами имеет большое влияние на размер восковой формы. Пропорциональное соотношение между этими тремя невозможно контролировать в реальном производстве, что также является важной причиной плохой стабильности размеров восковых форм с использованием формовочных материалов на основе воска.
2. Влияние материала оболочки и процесса изготовления оболочки на стабильность размеров отливок.
Влияние оболочки формы на размер отливки в основном вызвано тепловым расширением и термической деформацией (высокотемпературной ползучестью) оболочки формы во время обжига, а также ограничением (препятствием) оболочки формы на усадку при охлаждении Кастинг.
(1) Тепловое расширение оболочки
В основном зависит от материала корпуса. Различные огнеупорные материалы имеют разную степень расширения. Среди обычно используемых огнеупоров плавленый кварц имеет наименьшую скорость расширения, за ним следует силикат алюминия, а кремнезем является самым большим и неравномерным. После испытаний установлено, что оболочка из силиката алюминия может быть нагрета от комнатной температуры до 1000 ℃, оболочка может расширяться примерно на 0.25%, что составляет небольшую долю от общей усадки размера отливки. Следовательно, если используются такие огнеупорные материалы, оболочка будет иметь лучшую стабильность размеров, например плавленый кварц, несомненно, будет лучше. Однако при использовании кремнезема размер оболочки сильно колеблется.
(2) Термическая деформация (ползучесть при высоких температурах)
Например, оболочка, в которой в качестве связующего используется жидкое стекло, имеет значительно большую степень ползучести при высоких температурах выше 1000 ° C, чем оболочка из золя кремниевой кислоты и этилсиликатной оболочки. Хотя сам плавленый корунд имеет высокую огнеупорность, из-за присутствия примесей, таких как оксид натрия, температура обжига оболочки выше 1000 ℃ может также вызвать ползучесть, что приведет к плохой стабильности размеров.
(3) Сдерживание оболочки формы при усадке отливки - отступление и сжимаемость оболочки формы. Это также в основном зависит от материала оболочки формы.
Таким образом, огнеупорные материалы играют важную роль во влиянии оболочки на колебания размеров отливки, но нельзя игнорировать роль связующего. Напротив, влияние процесса изготовления скорлупы невелико.
3. Влияние напряжения, вызванного неравномерным охлаждением отливок, на стабильность размеров.
Скорость охлаждения каждой части отливки (включая литниковую систему) различна, что создает термическое напряжение и деформирует отливку, тем самым влияя на стабильность размеров. Это часто встречается в реальном производстве. Эффективными профилактическими мерами являются снижение скорости охлаждения отливок и улучшение комбинации бегунов.
2. Правильно назначен ключ к повышению точности - коэффициент усадки пресс-формы.
Вышеупомянутая «стабильность размеров» отличается от «точности размеров» и «прецизионности (прецизионности)». Стабильность размеров (т.е. точность) является синонимом размерной согласованности, отражающей степень размерных колебаний или дисперсии, и обычно измеряется стандартным отклонением σ. Основная причина нестабильности размеров - слабый контроль процесса, который является случайной ошибкой. Точность - это степень отклонения среднего арифметического многих измеренных значений от номинального размера для определенного размера отливки, то есть величина среднего отклонения. Для литья по выплавляемым моделям основной причиной плохой точности размеров является неправильное задание степени усадки при проектировании профилирования, что является систематической ошибкой, которая обычно корректируется путем многократного ремонта формы. Точность размеров (прецизионность) - это комбинация двух вышеперечисленных. Следовательно, для повышения точности размеров отливок и решения проблемы допусков на размеры изделий необходимо не только строго контролировать процесс, чтобы уменьшить размерные колебания, но также необходимо правильно задавать степень усадки каждого размера отливки при проектировании профиля. .
Хорошо известно, что окончательная полная усадка прецизионных отливок представляет собой комбинацию восковой формы, усадки сплава и небольшого расширения корпуса. Оболочка разбухает примерно на 0.25%, и ее действие ограничено. Хотя скорость линейной усадки сплава часто выше, чем у восковой формы, колебания размеров, вызванные процессом прессования воска, имеют большее влияние. Чтобы снизить стоимость ремонта формы и уменьшить колебания размера отливки, очень важно контролировать степень усадки восковой формы.
1. Усадка восковой формы
Усадку восковой формы следует измерять после того, как размер восковой формы полностью стабилизируется. Это связано с тем, что усадка восковой формы не прекращается полностью после извлечения формы. Размер восковой формы иногда стабилизируется всего через несколько дней после извлечения формы. Однако большая часть усадки материала формы в основном завершается в пределах от одного до нескольких часов после выталкивания формы. На степень усадки восковой формы в основном влияют следующие факторы:
(1) Тип материала пресс-формы;
(2) Размер восковой модели в разрезе;
Стоит подчеркнуть, что размер поперечного сечения восковой формы существенно влияет на степень усадки. Например, степень усадки типичного материала формы без наполнителя при прессовании восковых форм разной толщины. Толщина секции восковой формы, как правило, не должна превышать 13 мм. Когда толщина превышает 13 мм, толщину стенки можно уменьшить, используя блоки из холодного воска или металлические стержни для достижения цели уменьшения усадки, что особенно важно для материалов форм без наполнителя.
Примечание: 1. Степень усадки водорастворимого материала формы составляет около 0.25%;
2. При использовании растворимых стержней, керамических стержней или трубок из кварцевого стекла линейная усадка восковой формы при контакте с стержнем отсутствует;
(3) Основные типы
Размер полости восковой формы, несомненно, соответствует форме сердечника. Таким образом, использование стержней стало способом повысить точность размеров полости восковой формы.
2. Усадка сплава.
Усадка сплава в основном зависит от следующих факторов:
· Тип и химический состав литейного сплава;
· Геометрия отливки (включая состояние ограничений и размер сечения);
· Параметры отливки, такие как температура заливки, температура корпуса, скорость охлаждения отливки и т.д .;
· Использование керамических стержней, трубок из кварцевого стекла и т. Д.
Поскольку температура разливки, температура корпуса, скорость охлаждения отливки и другие параметры процесса, как правило, строго контролируются стандартными технологическими картами во время производственного процесса, вызванные этим колебания размеров невелики между различными производственными партиями. Даже если температура разливки превышает диапазон, требуемый спецификацией процесса, колебание размера отливки обычно невелико. Как и в восковой форме, размер сечения отливки и ограничения корпуса формы являются основными факторами, влияющими на усадку сплава. Опыт показывает, что степень усадки полностью ограниченного размера составляет от 85% до 89% от степени свободной усадки; полуограниченный размер составляет от 94% до 95%.
3. Минимальное количество первой партии образцов для измерения.
Указанная выше степень усадки является эмпирическими данными, основанными на прошлом опыте, а не реальной степенью усадки. При проектировании и изготовлении пресс-форм по этим данным ремонт неизбежен. Для повышения точности и успешности ремонта и уменьшения количества ремонтов ключевым звеном является тщательная проверка размера достаточного количества пробных отливок. Поскольку размер отливок, которые мы производим, не может быть точно таким же, поэтому, только когда количество измеренных образцов достаточно велико, полученное среднее значение может быть близко к истинному среднему арифметическому. Из этого нетрудно понять, что минимальное количество образцов для измерений напрямую связано с технологической способностью производственного процесса контролировать согласованность размеров продукта (возможности процесса). Если отливки полностью одинаковы по размеру, то требуется испытание только одного образца; И наоборот, если размер отливки сильно колеблется,
Для получения более точных данных об усадке необходимо отмерить большое количество образцов. Как упоминалось ранее, способность производственного процесса контролировать размер может быть представлена 6σ размера отливки, полученной с помощью этого процесса. Исходя из текущего технологического уровня большинства инвестиционных литейных производств, Hp в большинстве случаев превышает 0.5, поэтому для первой партии образцов для измерений обычно требуется не менее 11 образцов.
три. Анализ системы измерений
При анализе и решении проблем, связанных с размером продукта, мы должны обращать внимание на точность и надежность используемой системы измерения. Помимо частой калибровки самих средств измерений и оборудования, также важно минимизировать ошибки измерения. Если система измерения (включая оператора и метод работы) имеет большую ошибку, не только бракованные продукты могут быть оценены как квалифицированные продукты, но также и многие квалифицированные продукты могут быть ошибочно приняты за бракованные, что может вызвать серьезные аварии или ненужные экономические последствия. убытки. Самый простой способ определить, подходит ли измерительная система для конкретной измерительной задачи, - это выполнить квалификационные испытания воспроизводимости и повторяемости. Так называемая повторяемость означает, что один и тот же инспектор использует один и тот же инструмент (или оборудование) и метод для проверки одной и той же детали и получения согласованности результатов. Воспроизводимость означает согласованность результатов, полученных разными операторами, использующими разные инструменты для проверки одной и той же детали. Группа действий американской автомобильной промышленности (Automotive Industry Action Group) устанавливает, что процент интегрированного стандартного отклонения повторяемости и воспроизводимости R&R в стандартном отклонении измеренных колебаний размера отливки составляет ≤30% в качестве стандарта для системы измерения, отвечающей требованиям требования [5]. При измерении некоторых крупногабаритных отливок и отливок сложной формы не все измерительные системы могут удовлетворить это требование. Допустимая погрешность измерения при измерении форм должна быть меньше, обычно 1/3.
четыре. Структура пресс-формы и уровень обработки
Хорошо известно, что структура формы и качество обработки имеют важное влияние на размер и геометрию восковой формы. Например, является ли механизм позиционирования и зажима точным и надежным, соответствует ли соответствующий зазор подвижных частей (таких как подвижные блоки, болты и т. Д.), Полезен ли метод вытяжки для обеспечения точности размеров отливок. и т. д. Излишне говорить, что для значительного числа отечественных заводов по литью по выплавляемым моделям уровень проектирования и производства форм все еще нуждается в срочном улучшении.
Пятерки. в заключении
Из приведенного выше анализа нетрудно увидеть, что повышение точности размеров отливок по выплавляемым моделям - это систематический проект, включающий все аспекты процесса производства отливок по выплавляемым моделям. Основные моменты можно резюмировать следующим образом:
1) Строго контролируйте параметры процесса формования, особенно параметры, которые существенно влияют на размер отливки.
2) Выберите подходящий материал оболочки.
3) Собирать, подсчитывать и анализировать данные, относящиеся к усадке, правильным методом, который соответствует статистическим принципам, для повышения точности определения усадки.
4) Часто контролируйте систему измерения (включая оборудование, проверяющий персонал и технологии), чтобы убедиться, что повторяемость и воспроизводимость ошибок соответствуют установленным требованиям.
5) Постоянно улучшайте уровень проектирования и производства пресс-форм.
6) Такие меры, как корректировка отливки и стабилизационная термообработка, по-прежнему необходимы во многих случаях.
Сохраните источник и адрес этой статьи для перепечатки.: Различные факторы, влияющие на стабильность размеров отливок по выплавляемым моделям
Минхэ Компания по литью под давлением специализируются на производстве и предоставлении качественных и высокопроизводительных литых деталей (ассортимент металлических деталей для литья под давлением в основном включает Тонкостенное литье под давлением,Литье под давлением,Литье под давлением в холодной камере), Round Service (Служба литья под давлением,Обработка с ЧПУ,Изготовление пресс-форм, Обработка поверхности) .Любое индивидуальное литье под давлением из алюминия, магния или замака / цинка, а также другие требования к отливкам, пожалуйста, свяжитесь с нами.
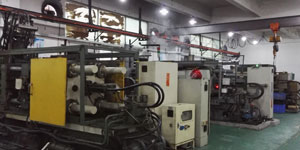
Под контролем ISO9001 и TS 16949, все процессы выполняются на сотнях передовых машин для литья под давлением, 5-осевых станках и других объектах, от струйных до стиральных машин Ultra Sonic. Minghe не только имеет современное оборудование, но и имеет профессиональное оборудование. команда опытных инженеров, операторов и инспекторов для воплощения в жизнь проекта заказчика.
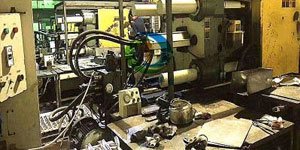
Контрактный производитель отливок под давлением. Возможности включают в себя детали для литья под давлением алюминия с холодной камерой весом от 0.15 фунта. до 6 фунтов, быстрая установка и обработка. Дополнительные услуги включают полировку, вибрацию, удаление заусенцев, дробеструйную очистку, окраску, гальванику, нанесение покрытий, сборку и оснастку. Обрабатываемые материалы включают такие сплавы, как 360, 380, 383 и 413.
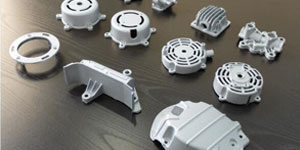
Помощь в проектировании литья цинка под давлением / сопутствующие инженерные услуги. Изготовление на заказ прецизионных отливок из цинка под давлением. Могут изготавливаться миниатюрные отливки, отливки под высоким давлением, отливки в формы с несколькими суппортами, отливки в обычные формы, единичные отливки под давлением и независимые отливки под давлением, а также отливки с герметизацией полости. Отливки могут изготавливаться длиной и шириной до 24 дюймов с допуском +/- 0.0005 дюйма.
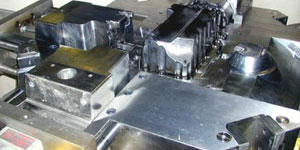
Производитель литья под давлением из магния, сертифицированный по стандарту ISO 9001: 2015. Возможности включают литье под давлением магния под высоким давлением с горячей камерой до 200 тонн и холодной камерой на 3000 тонн, проектирование инструментов, полировку, формование, механическую обработку, порошковую и жидкостную окраску, полный контроль качества с возможностями CMM , сборка, упаковка и доставка.
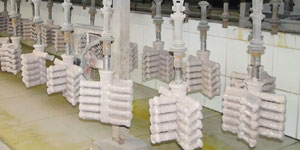
Сертифицирован ITAF16949. Дополнительные услуги трансляции включают инвестиционное литье,литье в песчаные формы,Гравитационное литье, Литье по выплавляемым моделям,Центробежное литье,Вакуумное литье,Постоянное литье формыВозможности включают EDI, техническую поддержку, твердотельное моделирование и вторичную обработку.
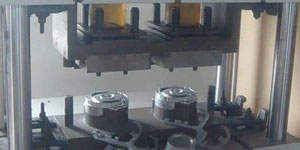
Литейная промышленность Примеры использования запчастей для: автомобилей, велосипедов, самолетов, музыкальных инструментов, судов, оптических устройств, датчиков, моделей, электронных устройств, корпусов, часов, машинного оборудования, двигателей, мебели, ювелирных изделий, приспособлений, телекоммуникаций, освещения, медицинских устройств, фотографических устройств, Роботы, скульптуры, звуковое оборудование, спортивное оборудование, инструменты, игрушки и многое другое.
Что мы можем вам сделать дальше?
∇ Перейти на главную страницу для Литье под давлением Китай
→Литье деталей-Узнай, что мы сделали.
→ Общие советы о Услуги литья под давлением
By Производитель литья под давлением Minghe | Категории: Полезные статьи |Материалы Теги: Литье алюминия, Цинковое литье, Литье магния, Титановое литье, Литье из нержавеющей стали, Латунное литье,Бронзовое литье,Кастинг видео,История компании,Литье алюминия под давлением | Комментарии отключены