Меры предосторожности при литье водяного стекла в песчаные формы
Какие факторы влияют на «старение» жидкого стекла? Как устранить «старение» жидкого стекла?
Свежеприготовленный стакан для воды - верное решение. Однако во время процесса хранения кремниевая кислота в жидком стекле будет подвергаться конденсационной полимеризации, которая будет постепенно поликонденсироваться из истинного раствора в раствор высокомолекулярной кремниевой кислоты и, наконец, превратиться в гель кремниевой кислоты. Следовательно, жидкое стекло на самом деле представляет собой гетерогенную смесь, состоящую из поликремниевой кислоты с разной степенью полимеризации, на которую легко влияют ее модуль, концентрация, температура, содержание электролита и время хранения.
Во время хранения молекулы жидкого стекла подвергаются конденсационной полимеризации с образованием геля, и его прочность связи постепенно снижается с увеличением времени хранения. Это явление называется «старением» жидкого стекла.
Явление «старения» можно объяснить следующими двумя наборами данных испытаний: жидкое стекло с высоким модулем упругости (M = 2.89, ρ = 1.44 г / см3) после 20, 60, 120, 180, 240 дней хранения, отверждение CO2 жидкое стекло выдувается. Прочность на разрыв в сухом состоянии песка падает соответственно на 9.9%, 14%, 23.5%, 36.8% и 40%; низкомодульный силикат натрия (M = 2.44, ρ = 1.41 г / см3) хранится в течение 7, 30, 60 и 90 дней после высыхания. Прочность на разрыв снизилась на 4.5%, 5%, 7.3% и 11% соответственно.
Время хранения жидкого стекла мало влияет на начальную прочность самоотверждающегося песка из жидкого стекла, отвержденного сложным эфиром, но существенно влияет на последующую прочность. Согласно измерениям, она уменьшается примерно на 60% для высокомодульного жидкого стекла и на 15-20% для низкомодульного жидкого стекла. . Остаточная прочность также уменьшается с увеличением срока хранения.
Во время хранения жидкого стекла поликонденсация и деполимеризация поликремниевой кислоты протекают одновременно, молекулярная масса диспропорционируется, и, наконец, образуется многодисперсная система, в которой сосуществуют моноортосиликатная кислота и коллоидные частицы. То есть во время процесса старения жидкого стекла степень полимеризации кремниевой кислоты непропорциональна, и содержание моноортосиликатной кислоты и поликремниевой кислоты с высоким содержанием увеличивается с увеличением времени хранения. В результате конденсационной полимеризации и реакции деполимеризации жидкого стекла при хранении прочность сцепления снижается, то есть возникает явление «старения».
Основными факторами, влияющими на «старение» жидкого стекла, являются: время хранения, модуль и концентрация жидкого стекла. Чем дольше время хранения, чем выше модуль упругости и чем выше концентрация, тем серьезнее «старение».
Давно существующее жидкое стекло можно модифицировать различными способами, чтобы исключить "старение" и восстановить жидкое стекло до характеристик свежего жидкого стекла:
1. Физическая модификация
Старение жидкого стекла - это спонтанный процесс, который медленно высвобождает энергию. Физическая модификация «состаренного» жидкого стекла заключается в использовании магнитного поля, ультразвука, высокой частоты или нагрева для обеспечения энергией системы жидкого стекла и содействия высокой полимеризации полисиликатного клея. Частицы повторно деполимеризуются и способствуют гомогенизации молекулярной массы поликремниевой кислоты, тем самым устраняя явление старения, которое является механизмом физической модификации. Например, после обработки магнитным полем прочность силикатного песка натрия увеличивается на 20-30%, количество добавляемого силиката натрия снижается на 30-40%, сохраняется CO2, улучшается разрушаемость, и есть хорошие экономическая выгода.
Недостатком физической модификации является то, что она недолговечна, а прочность сцепления будет снижаться при хранении после обработки, поэтому ее можно использовать как можно скорее после обработки в литейном производстве. Особенно для жидкого стекла с M> 2.6 концентрация молекул кремниевой кислоты велика, и после физической модификации и деполимеризации оно будет поликонденсироваться относительно быстро. Лучше всего использовать сразу после лечения.
2. Химическая модификация
Химическая модификация заключается в добавлении небольшого количества соединений в жидкое стекло, все эти соединения содержат карбоксил, амид, карбонил, гидроксил, эфир, амино и другие полярные группы, которые адсорбируются на молекулах кремниевой кислоты или коллоидных частицах посредством водородных связей или статического электричества. электричество. Поверхность, изменяет ее потенциальную энергию поверхности и сольватирующую способность, улучшает стабильность поликремниевой кислоты, тем самым предотвращая «старение».
Например, добавление в жидкое стекло полиакриламида, модифицированного крахмала, полифосфата и т. Д. Может привести к лучшим результатам.
Включение органического вещества в обычное жидкое стекло или даже в модифицированное жидкое стекло может выполнять множество функций, таких как: изменение вязкостной текучести жидкого стекла; улучшение характеристик моделирования жидких стеклянных смесей; увеличение прочности склеивания, чтобы жидкое стекло было абсолютно добавленным. Количество уменьшено; повышается пластичность геля кремниевой кислоты; остаточная прочность снижается, поэтому жидкий стеклянный песок больше подходит для чугуна и цветных сплавов.
3. Физико-химическая модификация
Физическая модификация подходит для «состаренного» жидкого стекла, и его можно использовать сразу после модификации. Химическая модификация подходит для обработки пресного жидкого стекла, а модифицированное жидкое стекло может храниться долгое время. Комбинация физической модификации и химической модификации может сделать жидкое стекло длительным модифицирующим эффектом. Например, добавление полиакриламида в автоклав для модификации «стареющего» жидкого стекла дает хороший эффект. Среди них используются давление и давление автоклава. Перемешивание - это физическая модификация, а добавление полиакриламида - это химическая модификация.
Как предотвратить меление поверхности затвердевшей силикатно-натриевой песчаной формы (стержня) вдуванием CO2?
После выдувания силикатно-натриево-натриевого песка CO2 затвердевает и оставляется на некоторое время, иногда на поверхности нижней формы (стержня) появляется такое вещество, как иней, что серьезно снижает поверхностную прочность места и легко образует песок. дефекты промывки при заливке. Согласно анализу, основным компонентом этого белого вещества является NaHCO3, что может быть вызвано чрезмерной влажностью или CO2 в силикатном песке натрия. Реакция следующая:
- Na2CO3 + H2O → NaHCO3 + NaOH
- Na2O+2CO2+H2O→2NaHCO3
- NaHCO3 легко мигрирует наружу с влагой, вызывая порошкообразный иней на поверхности формы и стержня.
Решение заключается в следующем:
- Следите за тем, чтобы содержание влаги в силикатном песке не было слишком высоким (особенно в сезон дождей и зимой).
- Время продувки CO2 не должно быть слишком большим.
- Затвердевшую форму и стержень нельзя ставить надолго, их нужно вовремя формовать и заливать.
- Добавление около 1% (массовая доля) сиропа с плотностью 1.3 г / см3 к силикатному песку натрия может эффективно предотвратить измельчение поверхности.
Как улучшить влагопоглощение песчаной формы (стержня) из жидкого стекла?
Сердцевина из песочного стекла с содовой водой, закаленная методами CO2 или нагрева, собирается в форме для влажной глины. Если вовремя не залить, прочность песчаного керна резко снизится, может не только сползти, но и обрушиться; он хранится во влажной среде. Прочность песчаного ядра также значительно снижается. В таблице 1 показаны значения прочности сердцевин из песка из натриевого жидкого стекла, отвержденного CO2, при помещении в среду с относительной влажностью 97% на 24 часа. Причина потери прочности при хранении во влажной среде связана с регидратацией натриевого жидкого стекла. Na + и OH- в матрице связующего из силиката натрия поглощают влагу и разрушают матрицу, в конечном итоге разрывая связь кремний-кислород Si-O-Si, что приводит к значительному снижению прочности сцепления силикатного песка натрия.
Меры по решению этой проблемы:
- 1. Литиевое жидкое стекло добавляют в натриевое жидкое стекло или Li2CO3, CaCO3, ZnCO3 и другие неорганические добавки добавляют в натриевое жидкое стекло, поскольку могут образовываться относительно нерастворимые карбонаты и силикаты, а свободные ионы натрия могут уменьшаться. сопротивление абсорбции связующего для жидкого натриевого стекла может быть улучшено.
- 2. Добавьте небольшое количество органического материала или органического вещества с поверхностно-активным действием в натриевое жидкое стекло. Когда связующее затвердевает, гидрофильные ионы Na + и OH- в геле натриевого жидкого стекла могут быть замещены органическими гидрофобными группами или в сочетании друг с другом открытая органическая гидрофобная основа улучшает поглощение влаги.
- 3. Улучшите модуль жидкого стекла, потому что влагостойкость высокомодульного жидкого стекла выше, чем у низкомодульного жидкого стекла.
- 4. Добавьте гидролизат крахмала в силикатный песок натрия. Лучшим методом является использование гидролизата крахмала для модификации натриевого жидкого стекла.
4 Каковы характеристики процесса композита из затвердевшего жидкого стекла и песка на основе фенольной смолы с выдуванием CO2?
В последние годы, чтобы улучшить качество стальных отливок, некоторым малым и средним предприятиям срочно необходимо внедрить процесс производства смоляного песка. Однако из-за ограниченных экономических возможностей они не могут приобрести оборудование для регенерации смоляного песка, а старый песок не может быть переработан и повторно использован, что приводит к высоким производственным затратам. Чтобы найти эффективный способ улучшить качество отливок без чрезмерного увеличения стоимости, можно объединить технологические характеристики вдувания углекислого газа отвержденного силикатно-натриевого песка и углекислотного вдувания затвердевшего песка из щелочно-фенольной смолы, и вдувания углекислого газа отвержденного силиката натрия - щелочного можно использовать фенольную смолу. В процессе компаундирования смоляного песка используется песок на основе щелочной фенольной смолы в качестве поверхностного песка и песок из жидкого стекла в качестве обратного песка с продувкой CO2 для отверждения.
Фенольная смола, используемая в песке на основе CO2-щелочной фенольной смолы, получается путем поликонденсации фенола и формальдегида под действием сильного щелочного катализатора и добавления связующего агента. Его значение pH ≥13, а вязкость ≤500 мПа • с. Количество фенольной смолы, добавляемой в песок, составляет от 3% до 4% (массовая доля). Когда расход CO2 составляет 0.8 ~ 1.0 м3 / ч, оптимальное время продувки составляет 30 ~ 60 с; если время продувки слишком короткое, прочность песчаного стержня будет низкой; если время продувки слишком велико, прочность песчаного ядра не увеличится, и это будет пустой тратой газа.
CO2 - песок из щелочной фенольной смолы не содержит вредных элементов, таких как N, P, S и т. Д., Поэтому дефекты литья, такие как поры, микротрещины на поверхности и т. Д., Вызванные этими элементами, устраняются; во время заливки не выделяются вредные газы, такие как H2S и SO2, что благоприятно сказывается на защите окружающей среды; Хорошая складываемость, легко чистится; высокая точность размеров; высокая эффективность производства.
Процесс производства композита из закаленного жидкого стекла и щелочной фенольной смолы с продувкой углекислым газом может широко использоваться в стальных отливках, чугунных отливках, медных сплавах и отливках из легких сплавов.
Составной процесс - простой и удобный процесс. Процесс выглядит следующим образом: сначала отдельно смешайте песок со смолой и песок силиката натрия, а затем поместите их в два ведра с песком; затем добавьте смешанный смолистый песок в качестве поверхностного песка в песочницу. Толщина поверхностного слоя песка обычно составляет 30-50 мм; затем добавляется жидкий стеклянный песок, чтобы песок на обратной стороне заполнялся и уплотнялся; наконец, в форму для отверждения вдувается газообразный углекислый газ.
Диаметр выдувной трубы обычно составляет 25 мм, а диапазон закалки примерно в 6 раз превышает диаметр выдувной трубы.
Время продувки зависит от размера, формы, расхода газа и площади выпускной пробки песчаной формы (стержня). Как правило, время продувки регулируется в пределах 15 ~ 40 с.
После выдувания твердой песчаной формы (стержня) форму можно снимать. Прочность песчаной формы (стержня) быстро возрастает. Краску смажьте кистью в течение получаса после взятия формы, а через 4 часа закройте ящик для заливки.
Композитный процесс особенно подходит для сталеплавильных заводов, которые не имеют оборудования для регенерации смоляного песка и нуждаются в производстве высококачественных отливок. Процесс прост и легок в управлении, а качество производимых отливок эквивалентно качеству отливок из других смол в песчаные формы.
Затвердевший песок силиката натрия с продувкой CO2 также может быть смешан с песком из твердой полиакрилатной смолы натрия с продувкой CO2 для производства различных высококачественных отливок.
Каковы плюсы и минусы процесса отверждения силикатно-натриево-натриевого композита из композита СО2-органический эфир?
В последние годы процесс отверждения силикатно-натриевого песка из композита СО2-органический сложный эфир имеет тенденцию к расширению применения. Процесс заключается в следующем: добавляют определенное количество органического эфира во время перемешивания песка (обычно половина от нормального необходимого количества или 4 ~ 6% от веса жидкого стекла); после того, как моделирование завершено, продуйте CO2 для отверждения до прочности смазки формы (обычно требуется сопротивление сжатию). Прочность составляет около 0.5 МПа); после извлечения из формы сложный органический эфир продолжает затвердевать, и прочность формовочного песка возрастает более быстрыми темпами; после выдувания CO2 и помещения на 3-6 часов песчаную форму можно объединить и залить.
Механизм закаливания:
Когда жидкий стеклянный песок выдувает CO2, под действием разницы давлений газа и разницы концентраций газ CO2 будет пытаться течь во всех направлениях формовочного песка. После того, как газ CO2 контактирует с жидким стеклом, он немедленно вступает в реакцию с ним, образуя гель. Из-за эффекта диффузии реакция всегда происходит снаружи вовнутрь, и внешний слой сначала образует гелевую пленку, которая предотвращает продолжение реакции газа CO2 и жидкого стекла. Следовательно, за короткое время, независимо от того, какой метод используется для контроля газа CO2, невозможно заставить его реагировать со всем жидким стеклом. Согласно анализу, когда формовочный песок достигает наилучшей прочности на выдувание, жидкое стекло, реагирующее с газом CO2, составляет около 65%. Это означает, что жидкое стекло не полностью проявляет свой скрепляющий эффект, и по крайней мере 35% жидкого стекла не вступают в реакцию. Отвердитель на основе сложного органического эфира может образовывать однородную смесь со связующим и может дать полную игру связующему эффекту связующего. Все части стержневого песка набирают прочность с одинаковой скоростью.
Увеличение количества добавленного жидкого стекла увеличит конечную прочность песчаной формы, но ее остаточная прочность также увеличится, что затруднит очистку песка. Когда добавленное количество жидкого стекла слишком мало, конечная прочность слишком мала и не может соответствовать требованиям для использования. В реальном производстве количество добавляемого жидкого стекла обычно контролируется на уровне около 4%.
При использовании одного органического эфира для отверждения общее количество добавляемого органического эфира составляет 8-15% от количества жидкого стекла. При использовании упрочнения композита, по оценкам, примерно половина жидкого стекла затвердела при выдувании CO2, а примерно половина жидкого стекла еще не затвердела. Поэтому более целесообразно, чтобы количество органических сложных эфиров составляло от 4 до 6% от количества жидкого стекла.
Метод отверждения композита может полностью раскрыть двойные преимущества отверждения CO2 и отверждения на основе органических сложных эфиров, а также может полностью проявить связующий эффект жидкого стекла для достижения высокой скорости отверждения, раннего высвобождения из формы, высокой прочности, хорошей разрушаемости и низкой стоимости. Комплексный эффект.
Однако в процессе отверждения композита СО2-органический эфир необходимо добавить на 0.5-1% больше жидкого стекла, чем при использовании простого метода отверждения на основе сложного органического эфира, что усложняет регенерацию использованного жидкого стеклянного песка.
Почему легко производить липкий песок, если процесс изготовления чугунных отливок используется с применением силикатно-натриевого песка? Как это предотвратить?
Когда песчаная форма (стержень) из силикатно-натриевого песка используется для разливки чугунных отливок, часто образуется серьезный липкий песок, что ограничивает его применение в производстве чугуна.
Na2O, SiO2 в силикатном песке натрия и оксид железа, образованный жидким металлом во время разливки, образуют легкоплавкий силикат. Как упоминалось ранее, если этот состав содержит более плавкое аморфное стекло, сила связи между этим слоем стекла и поверхностью отливки очень мала, а коэффициент усадки отличается от коэффициента усадки металла. Большие напряжения легко снимаются с поверхности отливки без налипания песка. Если состав, образующийся на поверхности отливки, имеет высокое содержание SiO2 и низкое содержание FeO, MnO и т. Д., Его затвердевшая структура в основном имеет кристаллическую структуру, которая будет прочно соединяться с отливкой, в результате чего образуется липкий песок. .
Когда силикатный песок натрия используется для производства чугунных отливок, из-за низкой температуры разливки и высокого содержания углерода в чугунных отливках железо и марганец нелегко окисляются, и образующийся липкий слой песка имеет кристаллическую структуру, и это затруднительно. для создания подходящего слоя между чугунным отливом и слоем липкого песка. Толщина слоя оксида железа отличается от толщины смоляного песка между отливкой и липким песчаным слоем, который может образовывать яркую углеродную пленку в результате пиролиза смолы при производстве чугунных отливок, поэтому липкий песчаный слой удалить нелегко.
Чтобы предотвратить образование содового жидкого стеклянного песка при производстве отливок из чугуна, можно использовать подходящие покрытия. Например, краску на водной основе, поверхность после покраски необходимо высушить, поэтому лучше всего подойдет быстросохнущая краска на спиртовой основе.
Как правило, в чугунные отливки можно также добавить соответствующее количество угольного порошка (например, от 3% до 6%) (массовая доля) в песок силиката натрия, так что пиролиз угольного порошка между отливкой и слоем песка может привести к яркая углеродная пленка. Он не смачивается металлами и их оксидами, поэтому липкий слой песка легко снимается с отливки.
Ожидается ли, что силикатно-натриевый песок станет экологически чистым формовочным песком без сброса отработанного песка?
Жидкое стекло не имеет цвета, запаха и нетоксично. Это не вызовет серьезных проблем, если оно коснется кожи и одежды и будет смыто водой, но следует избегать попадания брызг в глаза. Жидкое стекло не имеет раздражающих или вредных газов, выделяемых во время перемешивания, моделирования, затвердевания и заливки песка, а также нет черных и кислотных загрязнений. Однако, если процесс неправильный и добавлено слишком много силиката натрия, усадочная способность силикатного песка натрия не будет хорошей, и пыль будет разлетаться во время очистки песка, что также вызовет загрязнение. В то же время старый песок трудно регенерировать, а сброс отработанного песка вызывает щелочное загрязнение окружающей среды.
Если эти две проблемы удастся преодолеть, силикатно-натриевый песок может стать экологически чистым формовочным песком практически без сброса отработанного песка.
Основная мера для решения этих двух проблем - уменьшить количество добавляемого жидкого стекла до менее 2%, которое может стряхнуть песок. Когда количество добавляемого жидкого стекла уменьшается, остаточный Na2O в старом песке также уменьшается. Используя относительно простой метод сухой регенерации, можно поддерживать остаточный Na2O в циркулирующем песке ниже 0.25%. Этот регенерированный песок может удовлетворить требования к применению одинарного формовочного песка для малых и средних стальных отливок. В настоящее время, даже если в старом песке из силиката натрия не используется дорогостоящий и сложный мокрый метод регенерации, а используется относительно простой и дешевый сухой метод, он может быть полностью переработан, отработанный песок практически не выгружается, а соотношение из песка в железо Оно может быть уменьшено до менее чем 1: 1.
Как эффективно регенерировать силикатно-натриевый песок?
Если остаточное количество Na2O в старом силикатном песке натрия слишком велико, после добавления силиката натрия в песок формовочный песок не будет иметь достаточно времени, и накопление слишком большого количества Na2O ухудшит огнеупорность кварцевого песка. Поэтому при регенерации использованного силикатно-натриевого песка следует как можно больше удалить остаточный Na2O.
Сохраните источник и адрес этой статьи для перепечатки.: Меры предосторожности при литье водяного стекла в песчаные формы
Минхэ Компания по литью под давлением специализируются на производстве и предоставлении качественных и высокопроизводительных литых деталей (ассортимент металлических деталей для литья под давлением в основном включает Тонкостенное литье под давлением,Литье под давлением,Литье под давлением в холодной камере), Round Service (Служба литья под давлением,Обработка с ЧПУ,Изготовление пресс-форм, Обработка поверхности) .Любое индивидуальное литье под давлением из алюминия, магния или замака / цинка, а также другие требования к отливкам, пожалуйста, свяжитесь с нами.
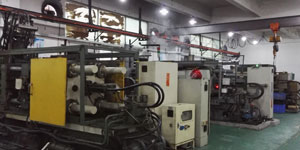
Под контролем ISO9001 и TS 16949, все процессы выполняются на сотнях передовых машин для литья под давлением, 5-осевых станках и других объектах, от струйных до стиральных машин Ultra Sonic. Minghe не только имеет современное оборудование, но и имеет профессиональное оборудование. команда опытных инженеров, операторов и инспекторов для воплощения в жизнь проекта заказчика.
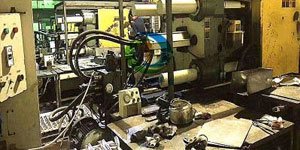
Контрактный производитель отливок под давлением. Возможности включают в себя детали для литья под давлением алюминия с холодной камерой весом от 0.15 фунта. до 6 фунтов, быстрая установка и обработка. Дополнительные услуги включают полировку, вибрацию, удаление заусенцев, дробеструйную очистку, окраску, гальванику, нанесение покрытий, сборку и оснастку. Обрабатываемые материалы включают такие сплавы, как 360, 380, 383 и 413.
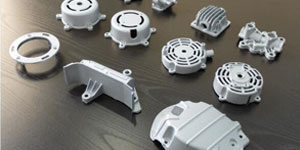
Помощь в проектировании литья цинка под давлением / сопутствующие инженерные услуги. Изготовление на заказ прецизионных отливок из цинка под давлением. Могут изготавливаться миниатюрные отливки, отливки под высоким давлением, отливки в формы с несколькими суппортами, отливки в обычные формы, единичные отливки под давлением и независимые отливки под давлением, а также отливки с герметизацией полости. Отливки могут изготавливаться длиной и шириной до 24 дюймов с допуском +/- 0.0005 дюйма.
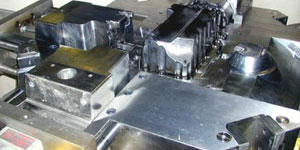
Производитель литья под давлением из магния, сертифицированный по стандарту ISO 9001: 2015. Возможности включают литье под давлением магния под высоким давлением с горячей камерой до 200 тонн и холодной камерой на 3000 тонн, проектирование инструментов, полировку, формование, механическую обработку, порошковую и жидкостную окраску, полный контроль качества с возможностями CMM , сборка, упаковка и доставка.
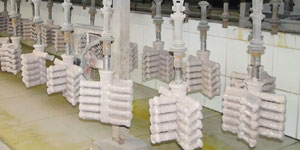
Сертифицирован ITAF16949. Дополнительные услуги трансляции включают инвестиционное литье,литье в песчаные формы,Гравитационное литье, Литье по выплавляемым моделям,Центробежное литье,Вакуумное литье,Постоянное литье формыВозможности включают EDI, техническую поддержку, твердотельное моделирование и вторичную обработку.
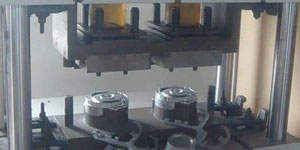
Литейная промышленность Примеры использования запчастей для: автомобилей, велосипедов, самолетов, музыкальных инструментов, судов, оптических устройств, датчиков, моделей, электронных устройств, корпусов, часов, машинного оборудования, двигателей, мебели, ювелирных изделий, приспособлений, телекоммуникаций, освещения, медицинских устройств, фотографических устройств, Роботы, скульптуры, звуковое оборудование, спортивное оборудование, инструменты, игрушки и многое другое.
Что мы можем вам сделать дальше?
∇ Перейти на главную страницу для Литье под давлением Китай
→Литье деталей-Узнай, что мы сделали.
→ Общие советы о Услуги литья под давлением
By Производитель литья под давлением Minghe | Категории: Полезные статьи |Материалы Теги: Литье алюминия, Цинковое литье, Литье магния, Титановое литье, Литье из нержавеющей стали, Латунное литье,Бронзовое литье,Кастинг видео,История компании,Литье алюминия под давлением | Комментарии отключены