Три ключевых фактора деформации пресс-формы
В настоящее время в производстве пресс-форм применяются новые технологии, такие как электроэрозионная обработка, формование, проволочная резка и т. Д., Чтобы лучше решить проблемы сложной обработки пресс-форм и деформации термообработки. Однако эти новые процессы еще не получили широкого распространения из-за различных ограничений. Поэтому вопрос о том, как уменьшить деформацию формы при термообработке, по-прежнему остается очень важным.
Как правило, формы требуют высокой точности. После термической обработки его неудобно или даже невозможно обработать и исправить. Следовательно, после термообработки, даже если структура и характеристики достигли требований, если деформация выходит за пределы допуска, она все равно будет списана, потому что ее нельзя сохранить. Не только влияет на производство, но и приводит к экономическим потерям.
Общий закон деформации термообработки здесь не обсуждается. Ниже приводится краткий анализ некоторых факторов, влияющих на деформацию пресс-формы.
Влияние материала пресс-формы на деформацию термообработки
Влияние материалов на деформацию термообработки включает влияние химического состава стали и исходной структуры.
С точки зрения самого материала на деформацию при термообработке в основном влияет влияние состава на прокаливаемость и точку Ms.
Когда углеродистая инструментальная сталь закаливается водой и маслом при нормальной температуре закалки, возникает большое термическое напряжение выше точки Ms; когда он охлаждается ниже точки Ms, аустенит превращается в мартенсит, что приводит к структурному напряжению, но из-за плохой прокаливаемости углеродистой инструментальной стали величина структурного напряжения невелика. Кроме того, балл Ms невысокий. Когда происходит мартенситное превращение, пластичность стали уже очень низкая, и пластическая деформация возникнет нелегко. Следовательно, характеристики деформации, вызванные термическим напряжением, сохраняются, и полость формы имеет тенденцию к усадке. Однако, если температура закалки увеличивается (> 850 ° C), структурное напряжение также может играть ведущую роль, и полость имеет тенденцию расширяться.
При изготовлении литейных форм из низколегированных инструментальных сталей, таких как сталь 9Mn2V, 9SiCr, CrWMn, GCr15, закон закалочной деформации аналогичен закону деформации углеродистой инструментальной стали, но степень деформации меньше, чем у углеродистой инструментальной стали.
Для некоторых высоколегированных сталей, таких как сталь Cr12MoV, из-за высокого содержания углерода и легирующих элементов и низкой точки Ms после закалки остается больше остаточного аустенита, что оказывает значительное влияние на объемное расширение из-за мартенсита. Поэтому деформация после закалки довольно мала. Как правило, при закалке с воздушным охлаждением, воздушным охлаждением и ванной с нитратной солью полость формы имеет тенденцию незначительно расширяться; если температура закалки слишком высока, количество остаточного аустенита увеличится. Полость также может дать усадку.
Если форма изготовлена из углеродистой конструкционной стали (например, стали 45) или некоторой легированной конструкционной стали (например, 40Cr), из-за ее высокой точки Ms, когда поверхность начинает превращаться в мартенсит, температура сердцевины все еще выше, и Предел текучести Он невысок и обладает определенной степенью пластичности. Мгновенное растягивающее напряжение ткани поверхности к сердцевине легко превышает предел текучести сердцевины, и полость имеет тенденцию к разбуханию.
Исходная структура стали также оказывает определенное влияние на закалочную деформацию. Упоминаемая здесь «первичная структура стали» включает уровень включений в стали, уровень полосчатой структуры, степень сегрегации компонентов, направленность распределения свободных карбидов и т. Д., А также различные структуры. полученные в результате различных предварительных термообработок (например, перлит, отпущенный сорбит, отпущенный троостит и т. д.). Для штамповой стали главное внимание уделяется сегрегации карбидов, форме и распределению карбидов.
Особенно очевидно влияние сегрегации карбидов в высокоуглеродистой и высоколегированной стали (такой как сталь Cr12) на деформацию закалки. Поскольку сегрегация карбида вызывает неоднородность состава стали после нагрева до аустенитного состояния, точки Ms в различных областях будут высокими или низкими. При тех же условиях охлаждения сначала происходит превращение аустенита в мартенсит, и удельный объем преобразованного мартенсита изменяется в зависимости от содержания углерода, и даже в некоторых низкоуглеродистых и низколегированных областях может не быть мартенсита (но бейнита, троостит и др.), все это вызовет неравномерную деформацию деталей после закалки.
Различные формы распределения карбидов (распределенные в гранулированной или волокнистой форме) по-разному влияют на расширение и сжатие матрицы, что также влияет на деформацию после термообработки. Обычно полость расширяется в направлении волокон карбида, и это более очевидно, хотя направление, перпендикулярное волокну, уменьшается, но не существенно. На некоторых заводах для этого есть специальные правила. Поверхность полости должна быть перпендикулярна направлению карбидного волокна, чтобы уменьшить деформацию полости. Когда карбид гранулированный. Когда он равномерно распределен, полость демонстрирует равномерное расширение и сжатие.
Кроме того, определенное влияние на деформацию оказывает состояние конструкции перед окончательной термообработкой. Например, исходная структура сферического перлита имеет меньшую тенденцию к деформации после закалки, чем чешуйчатый перлит. Поэтому формы с жесткими требованиями к деформации часто подвергаются закалке и отпуску после черновой обработки, а затем чистовой и окончательной термообработке.
Влияние геометрии пресс-формы на деформацию
Влияние геометрии пресс-формы на деформацию термообработки фактически проявляется в виде термического напряжения и организационного напряжения. Поскольку форма формы разнообразна, по ней все же сложно сформулировать точный закон деформации.
Для симметричных форм тенденцию к деформации полости можно учитывать в соответствии с размером полости, размером формы и высотой. Когда стенка формы тонкая, а высота небольшая, ее легче закалить. В это время, возможно, главную роль играет стресс тканей. Поэтому полость часто имеет тенденцию к набуханию. Напротив, при большой толщине и высоте стенки затвердеть непросто. В это время тепловая нагрузка может играть ведущую роль. Поэтому полость часто имеет тенденцию к усадке. Здесь упоминается общая тенденция. В производственной практике необходимо учитывать конкретную форму детали, марку стали, процесс термообработки и т. Д. И постоянно обобщать опыт на практике. В реальном производстве внешние размеры пресс-формы часто не являются основными рабочими размерами, и деформация может быть исправлена шлифованием и т. Д., Поэтому основной анализ, приведенный выше, - это тенденция деформации полости.
Деформация асимметричных форм также является результатом комбинированного воздействия термического напряжения и напряжения тканей. Например, для тонкостенной и тонкостенной формы, поскольку стенка формы тонкая, разница температур между внутренней и внешней стороной во время закалки мала, поэтому термическое напряжение невелико; но его легко закалить, а структурное напряжение велико, поэтому деформация имеет тенденцию расширять полость.
Чтобы уменьшить деформацию пресс-формы, отдел термической обработки должен работать с отделом проектирования пресс-форм для улучшения конструкции пресс-формы, например, избегать структур пресс-формы с большими различиями в размерах поперечного сечения, симметричной формы пресс-формы и раздельных конструкций для сложных формы.
Когда форма формы не может быть изменена, для уменьшения деформации могут быть приняты другие меры. Общее рассмотрение этих мер состоит в том, чтобы улучшить условия охлаждения, чтобы каждая часть могла охлаждаться равномерно; Кроме того, могут применяться различные принудительные меры для ограничения деформации деталей при закалке. Например, добавление технологических отверстий является мерой для равномерного охлаждения каждой детали, то есть открытия отверстий в некоторых частях формы, так что каждая часть формы может быть равномерно охлаждена для уменьшения деформации. Его также можно обернуть асбестом по периферии формы, который легко расширяется после закалки, чтобы увеличить разницу в охлаждении между внутренним отверстием и внешним слоем и уменьшить полость. Еще одной обязательной мерой для уменьшения деформации является удержание ребер или ребер жесткости на пресс-форме. Он особенно подходит для штампов с расширяющейся полостью и штампов с выемкой, которые легко расширяются или сжимаются.
Влияние процесса термообработки на деформацию пресс-формы
1. Влияние скорости нагрева
Вообще говоря, во время закалочного нагрева, чем выше скорость нагрева, тем больше термическое напряжение, создаваемое в форме, которое может вызвать деформацию и растрескивание формы. Особое внимание следует уделять предварительному нагреву, особенно для легированной и высоколегированной стали, из-за их плохой теплопроводности. Для некоторых высоколегированных форм сложной формы необходимо выполнять несколько этапов предварительного нагрева. Однако в отдельных случаях быстрое нагревание иногда может уменьшить деформацию. В это время нагревается только поверхность формы, в то время как центр остается «холодным», поэтому напряжение ткани и термическое напряжение соответственно снижаются, а сопротивление деформации сердечника увеличивается. Таким образом, уменьшение закалочной деформации, согласно некоторому опыту завода, используемого для решения проблемы деформации шага отверстия, имеет определенный эффект.
2. Влияние температуры нагрева
Температура закалочного нагрева влияет на прокаливаемость материала и в то же время влияет на состав и размер зерна аустенита.
- (1) С точки зрения прокаливаемости, высокая температура нагрева увеличивает термическое напряжение, но в то же время увеличивает прокаливаемость, поэтому структурное напряжение также увеличивается и постепенно преобладает. Например, для углеродистых инструментальных сталей T8, T10, T12 и т. Д. ., при закалке при общей температуре закалки внутренний диаметр имеет тенденцию к усадке, но если температура закалки увеличивается до ≥850 ° C, способность к закалке возрастает, и структурное напряжение постепенно становится преобладающим, поэтому внутренний диаметр может проявлять тенденцию вспухать.
- (2) С точки зрения состава аустенита повышение температуры закалки увеличивает содержание углерода в аустените и прямоугольность мартенсита после закалки (увеличенный удельный объем), что увеличивает объем после закалки.
- (3) При более внимательном рассмотрении влияния на точку Ms, чем выше температура закалки, тем крупнее зерна аустенита, что увеличивает склонность деталей к деформации и растрескиванию.
Таким образом, для всех марок сталей, особенно для некоторых высокоуглеродистых средне- и высоколегированных сталей, температура закалки, очевидно, будет влиять на деформацию закалки литейной формы. Поэтому очень важен правильный выбор температуры закалочного нагрева.
Вообще говоря, слишком высокая температура закалочного нагрева не способствует деформации. При условии, что это не влияет на производительность, всегда используется более низкая температура нагрева. Однако для некоторых марок стали с большим количеством остаточного аустенита после закалки (например, Cr12MoV и т. Д.) Количество остаточного аустенита также можно регулировать, регулируя температуру нагрева, чтобы отрегулировать деформацию формы.
3. Влияние скорости закалки при охлаждении.
Как правило, увеличение скорости охлаждения выше точки Ms значительно увеличивает термическое напряжение, и в результате деформация, вызванная термическим напряжением, имеет тенденцию к увеличению; увеличение скорости охлаждения ниже точки Ms в основном вызывает тенденцию к увеличению деформации, вызванной напряжением ткани.
Для разных марок стали из-за разной высоты точек Ms при использовании одной и той же закалочной среды наблюдаются разные тенденции к деформации. Для одной и той же марки стали, если используются разные закалочные среды, они также имеют разные тенденции к деформации из-за разной охлаждающей способности.
Например, точка Ms углеродистой инструментальной стали относительно низка, поэтому при использовании водяного охлаждения влияние термического напряжения имеет тенденцию преобладать; при охлаждении может преобладать структурное напряжение.
В реальном производстве формы обычно не закаливаются полностью, когда они сортируются или подвергаются постепенному отпуску, поэтому термическое напряжение часто является основным эффектом, который имеет тенденцию к усадке полости. Однако, поскольку термическое напряжение в это время не очень велико, общая деформация относительно мала. Если используется двухжидкостная закалка в воде и масле, или закалка в масле, вызываемое термическое напряжение будет больше, и усадка полости будет увеличиваться.
4. Влияние температуры отпуска
Влияние температуры отпуска на деформацию в основном вызвано преобразованием структуры в процессе отпуска. Если в процессе отпуска происходит явление «вторичной закалки», остаточный аустенит превращается в мартенсит, и удельный объем образовавшегося мартенсита больше, чем у остаточного аустенита, что приведет к расширению полости формы; Для некоторых высоколегированных инструментальных сталей, таких как Cr12MoV, используется высокотемпературная закалка, для которой в качестве основного требования требуется красная твердость. При многократном отпуске объем увеличивается один раз при каждом отпуске.
При отпуске в других температурных областях удельный объем уменьшается из-за превращения закаленного мартенсита в отпущенный мартенсит (или отпущенный сорбит, отпущенный троостит и т. Д.), И, следовательно, полость имеет тенденцию к усадке.
Кроме того, во время отпуска релаксация остаточного напряжения в форме также влияет на деформацию. После закалки формы, если поверхность находится в состоянии растягивающего напряжения, размер после отпуска увеличится; напротив, если поверхность находится в состоянии сжимающего напряжения, она будет давать усадку. Но из двух эффектов организационной трансформации и снятия стресса первый является основным.
Сохраните источник и адрес этой статьи для перепечатки.: Три ключевых фактора деформации пресс-формы
Минхэ Компания по литью под давлением специализируются на производстве и предоставлении качественных и высокопроизводительных литых деталей (ассортимент металлических деталей для литья под давлением в основном включает Тонкостенное литье под давлением,Литье под давлением,Литье под давлением в холодной камере), Round Service (Служба литья под давлением,Обработка с ЧПУ,Изготовление пресс-форм, Обработка поверхности) .Любое индивидуальное литье под давлением из алюминия, магния или замака / цинка, а также другие требования к отливкам, пожалуйста, свяжитесь с нами.
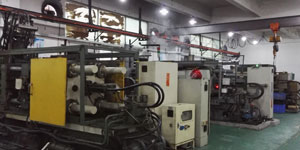
Под контролем ISO9001 и TS 16949, все процессы выполняются на сотнях передовых машин для литья под давлением, 5-осевых станках и других объектах, от струйных до стиральных машин Ultra Sonic. Minghe не только имеет современное оборудование, но и имеет профессиональное оборудование. команда опытных инженеров, операторов и инспекторов для воплощения в жизнь проекта заказчика.
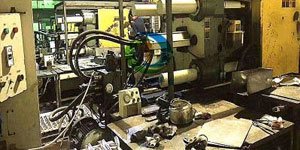
Контрактный производитель отливок под давлением. Возможности включают в себя детали для литья под давлением алюминия с холодной камерой весом от 0.15 фунта. до 6 фунтов, быстрая установка и обработка. Дополнительные услуги включают полировку, вибрацию, удаление заусенцев, дробеструйную очистку, окраску, гальванику, нанесение покрытий, сборку и оснастку. Обрабатываемые материалы включают такие сплавы, как 360, 380, 383 и 413.
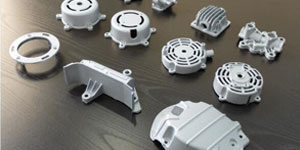
Помощь в проектировании литья цинка под давлением / сопутствующие инженерные услуги. Изготовление на заказ прецизионных отливок из цинка под давлением. Могут изготавливаться миниатюрные отливки, отливки под высоким давлением, отливки в формы с несколькими суппортами, отливки в обычные формы, единичные отливки под давлением и независимые отливки под давлением, а также отливки с герметизацией полости. Отливки могут изготавливаться длиной и шириной до 24 дюймов с допуском +/- 0.0005 дюйма.
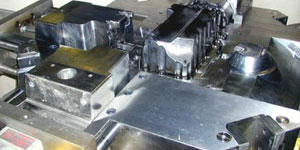
Производитель литья под давлением из магния, сертифицированный по стандарту ISO 9001: 2015. Возможности включают литье под давлением магния под высоким давлением с горячей камерой до 200 тонн и холодной камерой на 3000 тонн, проектирование инструментов, полировку, формование, механическую обработку, порошковую и жидкостную окраску, полный контроль качества с возможностями CMM , сборка, упаковка и доставка.
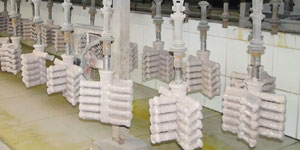
Сертифицирован ITAF16949. Дополнительные услуги трансляции включают инвестиционное литье,литье в песчаные формы,Гравитационное литье, Литье по выплавляемым моделям,Центробежное литье,Вакуумное литье,Постоянное литье формыВозможности включают EDI, техническую поддержку, твердотельное моделирование и вторичную обработку.
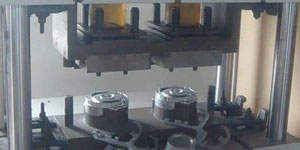
Литейная промышленность Примеры использования запчастей для: автомобилей, велосипедов, самолетов, музыкальных инструментов, судов, оптических устройств, датчиков, моделей, электронных устройств, корпусов, часов, машинного оборудования, двигателей, мебели, ювелирных изделий, приспособлений, телекоммуникаций, освещения, медицинских устройств, фотографических устройств, Роботы, скульптуры, звуковое оборудование, спортивное оборудование, инструменты, игрушки и многое другое.
Что мы можем вам сделать дальше?
∇ Перейти на главную страницу для Литье под давлением Китай
→Литье деталей-Узнай, что мы сделали.
→ Общие советы о Услуги литья под давлением
By Производитель литья под давлением Minghe | Категории: Полезные статьи |Материалы Теги: Литье алюминия, Цинковое литье, Литье магния, Титановое литье, Литье из нержавеющей стали, Латунное литье,Бронзовое литье,Кастинг видео,История компании,Литье алюминия под давлением | Комментарии отключены