Оптимизация и применение схемы литья под давлением алюминиевого корпуса дроссельной заслонки ETC на базе MAGMASOFT
В последние годы, с развитием мировой экономики, спрос на детали из автомобильных алюминиевых сплавов оказывает большое влияние на общие перспективы развития отрасли литья под давлением. Перед лицом все более жесткой отраслевой конкуренции и постоянного сокращения циклов разработки новых продуктов поставка качественных продуктов, отвечающих требованиям клиентов, за короткий период времени станет новым направлением развития предприятий по литью под давлением; В этой статье используется функция DOE MAGMASOFT для проведения анализа моделирования и сравнения различных схем литья и различных параметров процесса на ранней стадии отливки алюминиевого корпуса дроссельной заслонки ETC. И оптимизация, чтобы выбрать лучшее решение, тем самым сократив цикл разработки и обеспечив успех однократного испытания продукта и бесперебойное массовое производство и доставку.
Перед лицом усугубляющегося глобального климатического кризиса и все более жесткой тенденции к энергосбережению, сокращению выбросов и снижению загрязнения автомобильная промышленность также продолжит развитие в направлении энергосбережения, сокращения выбросов и интеллектуальных технологий; и электронная система дроссельной заслонки родилась в этой среде (Electronic Throttle Control System, сокращенно ETC), которая является незаменимой и важной частью нынешней автомобильной системы двигателя. Он определяет условия работы двигателя, управляя потоком всасываемого воздуха двигателя, чтобы обеспечить максимальную мощность и расход топлива автомобиля. Экономичный, чтобы дополнительно снизить требования к выбросам. Можно предвидеть, что электронный дроссель, как одна из ключевых технологий передовых систем управления и безопасности транспортных средств, несомненно, будет иметь хорошие перспективы применения, как и другие передовые технологии управления транспортными средствами.
Литой алюминиевый корпус дроссельной заслонки ETC, являющийся одним из наиболее важных компонентов в электронной системе дроссельной заслонки, определенно повлияет на надежность и стабильность системы; поэтому производство алюминиевых отливок дроссельной заслонки ETC, отвечающих требованиям, будет чрезвычайно важным. В этой статье, с помощью функции DOE компании MAGMASOFT, на ранней стадии отливки алюминиевого корпуса дроссельной заслонки ETC, различные схемы разливки и анализ моделирования различных параметров процесса проводятся сравнения и оптимизации, чтобы выбрать лучшую схему, тем самым сокращая разработку цикл и гарантия на этот продукт один раз. Успех пробной модели и бесперебойное массовое производство и поставка.
1 Анализ структуры продукта и технические требования
Марка материала для литья под давлением алюминиевого корпуса дроссельной заслонки ETC, изученного в этой статье, - AlSi12Cu1Fe, а его максимальный габаритный размер составляет 111 мм * 109 мм * 84 мм. Средняя толщина этой отливки составляет 4 мм, а толщина при максимальной толщине стенки составляет 13 мм. Общая структура продукта более сложная. , Имеется много изолированных высоких ребер, что не способствует упорядоченному заполнению расплавленным алюминием; толщина стенки в некоторых местах сильно различается, и тонкостенная область сначала затвердеет в твердое состояние, что эквивалентно разделению расплавленного сплава на множество. Небольшая замкнутая область образует изолированную область жидкой фазы на толстой стенке. Когда процесс затвердевания и усадки расплавленного металла в этих изолированных областях жидкой фазы невозможно дополнить, проблема усадочных полостей и пористости неизбежно возникнет внутри.
Из-за сложной рабочей среды отливок алюминиевого корпуса дроссельной заслонки ETC требуется дробеструйная обработка для улучшения качества поверхности отливок и повышения их коррозионной стойкости; подходящее место установки продукта требует более высоких геометрических и размерных допусков; Убедитесь, что объем утечки при испытательном давлении 3 бар меньше или равен 3 см0.7 / мин, а диаметр усадочного отверстия в локальной области изделия не должен превышать 5 мм, общее количество не должно превышать 10 мм. не более 10, шаг не менее XNUMX мм и не более XNUMX% от общей площади. ; Следовательно, для этого литья под давлением требуются очень высокие требования к проектированию процесса литья, чтобы гарантировать, что внутреннее качество отливки может соответствовать стандартам приемки потребителя;
2 Схема литья под давлением продукта и расчет параметров процесса
2.1 Разработка схемы литья под давлением
Чрезвычайно важное звено проектирования ворот для литья под давлением в технологии производства литья под давлением определяет качество деталей для литья под давлением, эффективность производства литья под давлением, срок службы формы, обрезку и очистку деталей для литья под давлением, скорость переплава сплавов для литья под давлением, и энергоэффективность машин для литья под давлением. Это имеет далеко идущие последствия; таким образом, правильное расположение ворот, их толщина и размер, а также количество ворот являются ключевыми факторами для обеспечения качественного литья под давлением; на основе анализа характеристик структуры продукта и опыта проектирования процессов, алюминиевый корпус дроссельной заслонки ETC. Есть три места для отливок, которые подходят для конструкции входного отверстия; Таким образом, в этой статье будут разработаны три различные схемы литья под давлением. Исходя из теоретического пути заполнения и расстояния потока, разные схемы разливки будут давать разные эффекты заполнения, поэтому они должны быть основаны на результатах моделирования программного обеспечения MAGMA, которые сравниваются и анализируются для проверки;
2.1.1 План заливки одной конструкции
Как показано на рисунке, количество затворов в первой схеме разливки спроектировано в виде двойных нитей, которые соответственно спроектированы в области боковой стенки места установки двигателя и положения установки пластины клапана. Выбран пуансон для впрыска диаметром 60 мм, а соотношение скоростей впрыска 1:14; Преимущество этой схемы разливки состоит в том, что поток расплавленного металла относительно короткий, что мало влияет на величину снижения температуры во время процесса заполнения; конструкция из трех проточных каналов способствует передаче давления и подаче расплавленного металла, что помогает сократить последующий производственный процесс. Риск появления усадочных дефектов имеет определенный положительный эффект; его недостаток состоит в том, что из-за классификации продукта и структурных соображений бегунок должен иметь определенные ступеньки и тонкостенные участки. Эти места склонны к попаданию газа в оболочку во время более позднего процесса заполнения. Кроме того, положение установки двигателя этого продукта не обрабатывается, и здесь присутствует конструкция ворот, которая позволяет легко промывать внутреннюю сердцевину стены и температуру в положении ворот. Более того, легко вызвать дефекты штампа и эрозию в месте установки двигателя; и положение ворот не обрабатывается, что оказывает определенное негативное влияние на обрезку и очистку последующих отливок под давлением;
2.1.2 Расчет второй схемы заливки
Как показано на рисунке, количество затворов во второй схеме разливки рассчитано на единицу, а положение спроектировано в области бокового круглого отверстия в месте установки пластины клапана. Выбран пуансон для впрыска диаметром 60 мм, а соотношение скоростей впрыска составляет 1:30; такая заливка.Преимущество решения состоит в том, что желоб может быть спроектирован с относительно плавным переходом, что способствует наполнению расплавленным металлом и уменьшает явление газовой оболочки во время процесса наполнения, а также уменьшает дефекты, вызванные газом принесенный бегуном; ворота рассчитаны на положение обрабатываемой поверхности. Снизить объем работ по обрезке и очистке отливок под давлением, а также снизить производственные затраты; однопроволочный затвор может предотвратить попадание нескольких нитей расплавленного металла в полость и вызвать завихрение, унос и окисление. Недостаток в том, что он находится в дальнем конце ворот. Эффект питания от положения горячей точки в основном отсутствует, поэтому необходимо учитывать другие схемы вспомогательного питания; и поток расплавленного металла относительно длинный, что оказывает определенное негативное влияние на температуру расплавленного металла во время процесса заполнения, и дефекты холодного материала могут возникать в определенных местах. ;
2.1.3 Расчет третьей схемы заливки
Как показано на рисунке, количество трех затворов в схеме заливки рассчитано на единицу, а положение задается в области бокового круглого отверстия в месте установки пластины клапана. Выбран пуансон для впрыска диаметром 60 мм, а соотношение скоростей впрыска составляет 1:30; Преимущество ворот заключается в том, что ворота спроектированы в положении обрабатываемой поверхности, что может снизить рабочую нагрузку по обрезке и очистке машины для литья под давлением и снизить производственные затраты. Затвор спроектирован с линейным стилем заполнения, что может уменьшить ход заполнения расплавленным алюминием и потерю температуры расплавленного алюминия. Сумма уменьшена; расстояние между пуансоном и затвором небольшое, что может обеспечить эффективную передачу давления пуансона; недостатком является то, что гибкость более поздних параметров регулировки производства мала, и качество продукта не может быть улучшено путем регулировки параметров литья под давлением.
2.2 Разработка параметров технологического процесса продукта
Согласно структурному анализу и требованиям к качеству отливок алюминиевого корпуса дроссельной заслонки ETC, в этом продукте используется машина для литья под давлением 350T, конструкция с одной формой и одной полостью, а давление отливки установлено на 100 МПа для обеспечения достаточной эффективности подачи и уменьшения появления дефектов усадки. в более поздний период. ; Температура разливки рассчитана на 660-680 ℃, а подвижные и неподвижные стержни формы предварительно нагреваются до 180-200 ℃; во время заполнения низкая скорость установлена на 0.25 м / с, высокая скорость установлена на 3 м / с, а точки переключения высокой скорости проверяются на 340 мм и 350 мм соответственно. Положение используется для определения наиболее стабильного состояния заполнения расплавленным металлом и наименьшего вихревого тока и явления уноса; при этом используется система контроля температуры линейного и точечного охлаждения для обеспечения хорошего теплового баланса формы;
3. Численное моделирование и сравнительный анализ импорта в один клик.
Контроль процесса заполнения и затвердевания отливки имеет решающее влияние на качество литья под давлением, но поскольку эти два процесса завершаются в закрытой и невидимой полости во время производственного процесса, невозможно наблюдать и анализировать прямо или косвенно, поэтому предыдущее значение Simulation особенно важно; с помощью функции DOE кода MAG, импорта трех вышеуказанных схем впрыска и двух тестовых высокоскоростных положений переключения одним щелчком мыши, однократного расчета нескольких схем, самого быстрого прогнозирования местоположения дефекта и поиска лучшего плана для улучшения внутреннее качество продукции, сокращение циклов разработки и снижение производственных затрат.
3.1 Моделирование и анализ процесса розлива
Как показано на рисунке 3, результатом моделирования первой строки изображения является время заполнения. Положение высокоскоростного переключения первых трех схем составляет 340 мм, а время заполнения короткое. Положение высокоскоростного переключения последних трех схем составляет 350 мм, а время заполнения большое. Позиция яркого цвета - это последняя позиция заполнения трех схем впрыска;
Результатом второй строки рисунка является результат максимального давления воздуха. Яркий цвет результата моделирования - это положение высокого давления воздуха и высокий риск образования устьиц. Путем сравнения было обнаружено, что значение давления воздуха по схеме 2 и схеме 5 относительно низкое, а риск стомы относительно невелик;
Результат третьей строки рисунка - результат заполнения объема. Результат моделирования имеет высокое содержание воздуха в ярком месте и высокий риск утечки. Путем сравнения установлено, что стоимость второго и пятого томов схемы относительно невысока, а риск утечки относительно невелик;
Всесторонний анализ результатов моделирования процесса наполнения показывает, что давление воздуха и унос второго и пятого вариантов относительно низки, второе высокоскоростное положение переключения - вперед, а время наполнения короткое, поэтому общая формуемость хорошо.
3.2 Моделирование и анализ процесса затвердевания
Как показано на рисунке 4, результатом первой строки рисунка является поле температуры замерзания. Результаты моделирования показывают, что время затвердевания внутреннего затвора схемы 3 и схемы 6 является наибольшим, а время подачи давления - наибольшим; схема 1 и схема 4 - вторые, время напорной подачи - среднее; время застывания внутреннего затвора по схеме 2 и схеме 5 Наименьшее и кратчайшее время подачи давления;
Результатом второй строки является эффективное время подачи горячего стыка, а яркий цвет результата моделирования - это положение горячего стыка продукта, то есть положение, в котором структура продукта относительно толстая и окончательно затвердевает. Расположение программ 1, 2, 4 и 5 в основном одинаковое. Схема 3 и Схема 6 имеют относительно толстые внутренние ворота, поэтому, если две горячие точки на внутренних воротах соединены вместе, горячие точки увеличатся;
Результатом третьего ряда является результат усадки. Из-за подачи под давлением состояние усадки схем 3 и 6 является наименьшим, а усадка четырех других схем в основном такая же. Для сравнения, схема 2 и схема 5 относительно небольшие.
По результатам анализа результатов моделирования процесса затвердевания усадочная полость схемы 3 и схемы 6 наименьшая, но горячий стык у внутреннего затвора наибольший, а результаты термосварки и усадки схемы 2 и схема 5 относительно лучше.
4. Проверка производства
Комплексный симуляционный анализ, для производства используется второй метод литья. На рис. 5 показано производственное изображение отливок алюминиевого корпуса дроссельной заслонки ETC; при осмотре продукции и рентгеновском контроле отливки не выявили пор и усадочных дефектов, превышающих требования заказчика к качеству; Также прошли требования к боковой утечке, утечки не произошло; поверхность отливки была блестящей, явных дефектов холодного материала и недостаточной заливки не наблюдалось, общий эффект полностью соответствовал требованиям заказчика по контролю качества, серийное производство плавное.
Сохраните источник и адрес этой статьи для перепечатки.:Оптимизация и применение схемы литья под давлением алюминиевого корпуса дроссельной заслонки ETC на базе MAGMASOFT
Минхэ Компания по литью под давлением специализируются на производстве и предоставлении качественных и высокопроизводительных литых деталей (ассортимент металлических деталей для литья под давлением в основном включает Тонкостенное литье под давлением,Литье под давлением,Литье под давлением в холодной камере), Round Service (Служба литья под давлением,Обработка с ЧПУ,Изготовление пресс-форм, Обработка поверхности) .Любое индивидуальное литье под давлением из алюминия, магния или замака / цинка, а также другие требования к отливкам, пожалуйста, свяжитесь с нами.
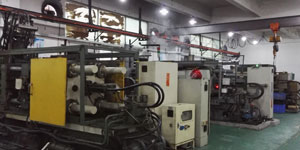
Под контролем ISO9001 и TS 16949, все процессы выполняются на сотнях передовых машин для литья под давлением, 5-осевых станках и других объектах, от струйных до стиральных машин Ultra Sonic. Minghe не только имеет современное оборудование, но и имеет профессиональное оборудование. команда опытных инженеров, операторов и инспекторов для воплощения в жизнь проекта заказчика.
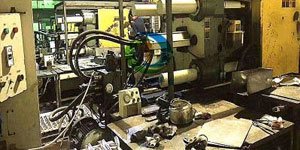
Контрактный производитель отливок под давлением. Возможности включают в себя детали для литья под давлением алюминия с холодной камерой весом от 0.15 фунта. до 6 фунтов, быстрая установка и обработка. Дополнительные услуги включают полировку, вибрацию, удаление заусенцев, дробеструйную очистку, окраску, гальванику, нанесение покрытий, сборку и оснастку. Обрабатываемые материалы включают такие сплавы, как 360, 380, 383 и 413.
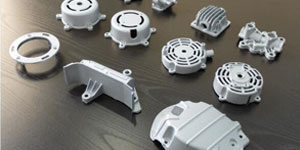
Помощь в проектировании литья цинка под давлением / сопутствующие инженерные услуги. Изготовление на заказ прецизионных отливок из цинка под давлением. Могут изготавливаться миниатюрные отливки, отливки под высоким давлением, отливки в формы с несколькими суппортами, отливки в обычные формы, единичные отливки под давлением и независимые отливки под давлением, а также отливки с герметизацией полости. Отливки могут изготавливаться длиной и шириной до 24 дюймов с допуском +/- 0.0005 дюйма.
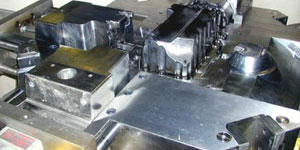
Производитель литья под давлением из магния, сертифицированный по стандарту ISO 9001: 2015. Возможности включают литье под давлением магния под высоким давлением с горячей камерой до 200 тонн и холодной камерой на 3000 тонн, проектирование инструментов, полировку, формование, механическую обработку, порошковую и жидкостную окраску, полный контроль качества с возможностями CMM , сборка, упаковка и доставка.
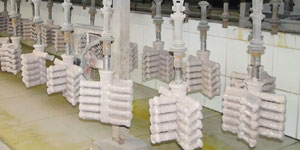
Сертифицирован ITAF16949. Дополнительные услуги трансляции включают инвестиционное литье,литье в песчаные формы,Гравитационное литье, Литье по выплавляемым моделям,Центробежное литье,Вакуумное литье,Постоянное литье формыВозможности включают EDI, техническую поддержку, твердотельное моделирование и вторичную обработку.
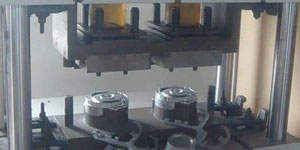
Литейная промышленность Примеры использования запчастей для: автомобилей, велосипедов, самолетов, музыкальных инструментов, судов, оптических устройств, датчиков, моделей, электронных устройств, корпусов, часов, машинного оборудования, двигателей, мебели, ювелирных изделий, приспособлений, телекоммуникаций, освещения, медицинских устройств, фотографических устройств, Роботы, скульптуры, звуковое оборудование, спортивное оборудование, инструменты, игрушки и многое другое.
Что мы можем вам сделать дальше?
∇ Перейти на главную страницу для Литье под давлением Китай
→Литье деталей-Узнай, что мы сделали.
→ Общие советы о Услуги литья под давлением
By Производитель литья под давлением Minghe | Категории: Полезные статьи |Материалы Теги: Литье алюминия, Цинковое литье, Литье магния, Титановое литье, Литье из нержавеющей стали, Латунное литье,Бронзовое литье,Кастинг видео,История компании,Литье алюминия под давлением | Комментарии отключены