Меры по предотвращению крупнозернистости отливок
Крупные кристаллические зерна отливок относятся к дефектам, которые демонстрируют чрезмерно крупнозернистую структуру и не подходят для применения после машиностроения или проверки на излом. Эта крупнозернистая структура может быть распределена по всей отливке или может возникать в отливке.
По сути, крупнозернистый дефект - это дефект металлургии. Основываясь на многолетней производственной практике и ссылаясь на соответствующие материалы, автор рассказывает о причинах и мерах профилактики грубых дефектов литья.
1. Структура отливки и технологический процесс
- (1) Если разница в поперечном сечении отливки слишком велика, более толстое поперечное сечение будет медленно охлаждаться, и в нем появятся крупные зерна. Металлы, такие как серый чугун, которые очень чувствительны к изменениям поперечного сечения, более склонны к возникновению таких дефектов. Эффективный способ предотвращения таких дефектов - избежать чрезмерного несоответствия размеров поперечного сечения отливок, но такой подход иногда бывает вне досягаемости литейщиков. Следовательно, что касается самого литья, можно уменьшить возникновение таких проблем и серьезность таких дефектов, установив холодный чугун, контролируя температуру разливки или выбрав подходящую систему разливки. Использование холодного чугуна может ускорить охлаждение более толстой части отливки; слишком высокая температура заливки сделает проблему более серьезной, и ее следует избегать; За счет корректировки и изменения конструкции системы разливки нижняя температура расплавленного металла находится в нижней части отливки. Толстые детали и спроектируйте наиболее эффективный стояк на толстой части отливки, чтобы максимально уменьшить размер стояка.
- (2) Для отливок с отверстиями разработчики процессов иногда не используют стержни, которые помогают уменьшить эффективный размер поперечного сечения, и делают поперечные сечения без стержней слишком толстыми, чтобы вызвать этот дефект. Поэтому при проектировании процесса он должен быть как можно меньше. В толстом участке устанавливается песчаный керн.
- (3) В некоторых случаях секция отливки не слишком толстая, но поскольку узкая выемка или сердечник образует секцию теплоотвода в отливке, результат такой же, как и у толстой секции. Например, может потребоваться установить стержень на столбчатом пупке в более глубокой части отливки, и это вызовет медленное охлаждение. В случае, если конструкция не может быть изменена, кроме случаев, когда температура металла может быть снижена или затвор не может быть перемещен, лучшим решением является установка холодного чугуна на стержне или секции формы.
- (4) Припуск на обработку слишком велик в технологическом проекте, что не только увеличивает стоимость резки, но также срезает более плотную поверхность отливки и обнажает незакрепленную часть с более медленным охлаждением в центре. Такая конструкция нежелательна, поскольку нецелесообразна с точки зрения литья или механической обработки. Решение - изменить конструкцию отливки. Если конструкцию нельзя менять, правильным методом будет использование холодного утюга, контроль температуры разливки и регулировка системы разливки.
- (5) Несоответствующая конструкция сердечника в толстой секции, неправильная опора сердечника или другие технологии, вызывающие эксцентриситет, вызовут изменения в секции отливки и вызовут крупные зерна.
2. Система заливки и стояка
- (1) Неспособность достичь последовательного затвердевания. Неспособность системы разливки достичь хорошего последовательного затвердевания обычно является причиной крупных зерен. Для отливок с резкими изменениями поперечного сечения необходимо обращать внимание на количество и расположение заслонки. Чтобы обеспечить загрузку, удерживание горячего расплавленного металла в зоне действия питателя снизит скорость охлаждения толстой секции до такой степени, что будут производиться крупные зерна. Неправильная конструкция стояка, например, слишком длинная шейка стояка, неподходящий стояк конструкция прокладки или слишком большой размер стояка приведет к чрезмерному накоплению тепла в более толстой секции.
- (2) Распределение сливного стояка, которое может вызвать радиатор. Аналогичным образом, для подачи питания на толстые секции на определенных участках часто возникает чрезмерное накопление тепла. Например, поскольку боковой стояк может вызвать перегрев толстых секций и замедлить скорость охлаждения, иногда его неудобно использовать в реальной эксплуатации. При реальном производстве требуется разумная конструкция стояка, чтобы максимально уменьшить размер стояка.
- (3) Соединение между внутренним затвором или стояком и отливкой вызывает локальное горячее соединение. Внутренний затвор или шейка подступенка короткие, что удобно для кормления, но из-за этого побег или подступенок будут слишком близко к отливке. Уменьшите скорость охлаждения этой детали. Увеличение горловины стояка вызовет проблемы с кормлением. Следовательно, лучшая мера - принять эффективную конструкцию стояка, максимально уменьшить размер стояка, не располагать желоб и стояк слишком близко к ключевой секции, которая легко образует крупнозернистый продукт, и установить бегунок и стояк соответственно. Чтобы добиться кормления.
- (4) Недостаточное количество внутренних ворот. Слишком мало внутренних ворот не только легко вызовет мытье песка, но и вызовет локальные горячие точки и грубую структуру. Это явление характерно для всех литых металлов, даже для алюминиевых сплавов с более низкими температурами литья. В некоторых случаях из-за того, что количество ворот слишком мало, это вызовет дефекты усадки. Этот дефект усадки может скрывать дефекты крупного зерна, вызванные той же причиной. Фактически, когда дефект крупного зерна серьезно ухудшается, он становится дефектом усадки. Таким образом, меры по предотвращению и устранению этих двух дефектов часто одинаковы.
3. Формовочный песок.
Только тогда, когда смещение формовочной стенки, вызванное формовочным песком, достаточно для увеличения размера поперечного сечения критического участка (участка, который легко формируется с крупными зернами), жало формы является фактором, вызывающим дефекты крупного зерна. . Поскольку смещение стенки на толстом участке может быть самым большим, этот вид дефекта все еще возможен, а образовавшийся в это время крупнозернистый дефект связан с расширением песка.
4. Изготовление стержней
При производстве следует избегать использования необожженных или закаленных на воздухе стержней из нефтеносного песка, поскольку такие стержни могут вызывать экзотермическую реакцию и вызывать чрезмерный сбор тепла. Это происходит либо в больших отливках, либо в толстых и больших стержнях с использованием клея с экзотермическими свойствами. В некотором смысле этот сердечник действует как высокоэффективный изолятор и снижает скорость охлаждения расплавленного металла до опасного уровня.
5. Моделирование
- (1) Отсутствие вентиляционных отверстий, которые могут увеличить скорость охлаждения. Для более толстых отливок скорость охлаждения отливки зависит от скорости рассеивания тепла через формовочный песок. Соответствующая вытяжка поможет быстро удалить водяной пар, создавая охлаждающий эффект.
- (2) Отсутствие холодных ногтей или холодного железа обычно вызвано небрежностью.
6. Химический состав
По сути, крупные кристаллические зерна и химический состав металла связаны со скоростью охлаждения, поэтому очень важно выбрать эту комбинацию. Если скорость охлаждения трудно регулировать, то крупнозернистая структура должна быть из-за неправильного химического состава металла. Ввиду важности металлических компонентов каждый металл кратко описывается следующим образом.
- (1) Углеродный эквивалент серого чугуна и ковкого чугуна слишком высок. Математический расчет эффектов углерода и кремния обычно сводится к следующему: CE = C + 1 / 3Si. Крупные зерна могут быть вызваны чрезмерным содержанием углерода или кремния или чрезмерным содержанием углерода и кремния. К. По сравнению с кремнием влияние углерода в три раза выше, чем у кремния, поэтому изменение количества углерода намного опаснее, чем изменение того же количества кремния. Этот эффект углерода и кремния влияет как на ковкий чугун, так и на серый чугун. В ковком чугуне крупные зерна не выглядят черными и не появляются в виде ямок, указывающих на первичный графит. Вместо этого они появляются в виде общих крупных зерен. Это связано с высоким содержанием углерода или кремния, либо оба они слишком высоки. Фосфор также влияет на крупность кристаллических зерен. При wp = 0.1% дефект усадочной полости будет усугубляться, особенно на участке, где охлаждение медленнее, будет увеличиваться степень крупных дефектов зерна.
- (2) Стальное литье: при плавлении и раскислении стального литья добавляются некоторые элементы, замедляющие рост зерен. Следовательно, по сравнению с кованой сталью вероятность образования крупных зерен в литой стали ниже. Стальные отливки с крупными зернами, обусловленными составом, могут быть улучшены отжигом или нормализацией.
- (3) Примеси алюминиевого сплава и железа делают алюминиевые отливки более крупнозернистыми и увеличивают хрупкость. Большинство этих дефектов вызвано неправильными операциями плавки. В алюминиевые сплавы, особенно те, которые требуют перегрева, необходимо добавлять соответствующее количество рафинированных легирующих элементов.
- (4) Медные сплавы. Крупнозернистые дефекты в медных сплавах часто покрываются точечными отверстиями, порами или усадками. Медные сплавы вызывают более крупные зерна из-за изменений в составе, но обычно сначала появляются точечные отверстия, поры или усадочная пористость.
7. плавление
Небольшая плавка повлияет на остальную структуру зерна. Для различных литых металлов необходимо применять процесс плавления Сяотун.
- (1) Купол плавит серый чугун. Несбалансированный объем дутья и кокса вызовут чрезмерное увеличение углерода. Например, высота нижнего кокса слишком высока, и уменьшение объема дутья приведет к чрезмерному увеличению содержания углерода. Когда футеровка печи эродирована, увеличение углерода будет более серьезным. Поскольку диаметр вагранки становится больше, для поддержания того же содержания углерода необходимо увеличить объем взрыва. Плавление при чрезмерно высокой температуре увеличивает количество углерода, что имеет место при плавке горячим воздухом. Согласно опыту, каждое повышение температуры дутья на 55 ° C увеличивает содержание углерода (массовую долю) на 0.10%. Если для повышения температуры используется кислород, это не обязательно вызывает ту же проблему. Слишком большой интервал между выпуском жидкости или слишком долгое пребывание жидкого чугуна в топке, что также приведет к увеличению содержания углерода. При производстве низкоуглеродистого чугуна обычно используется более мелкий под и сокращается интервал между выпусками жидкого чугуна, а также делается попытка добиться непрерывного выпуска жидкого чугуна в максимально возможной степени. Прерывистая плавка вызовет чрезмерное науглероживание, что приведет к крупнозернистой структуре . Кроме того, плавление прерывается почти без исключения из-за прекращения ветра, вызывающего колебания содержания углерода и кремния. После остановки ветра обычно требуется 15 минут, чтобы восстановить исходный химический состав.
- (2) Ковкий чугун. Отклонения при взвешивании или дозировании шихты приведут к изменению химического состава; количество дутья в печи не гарантируется, что повлияет на контроль химического состава; перегрев плавки или попадание дыма в пламя приведет к увеличению углерода.
- (3) Использование грязных тиглей для латуни и бронзы, а также оставшиеся конденсированные оболочки или тонкие металлические слои от последней плавки на дне и боковых стенках тигля вызовут загрязнение до следующей плавки, поэтому производство В процессе этого процесса мы должны избегать использования отходов неизвестного происхождения и не допускать попадания в шихту металлической печи газообразующего сырья, такого как влажные, загрязненные нефтью или другие грязные материалы.
- (4) Алюминий Перегрев расплавленного алюминия из-за неправильного контроля температуры плавления является частой причиной крупных зерен алюминиевого сплава. Следовательно, перегретый расплавленный алюминий следует медленно охлаждать во время производства, чтобы снизить его температуру разливки. Кроме того, небрежность или загрязнение шихты во время процесса дозирования также может стать причиной крупных дефектов зерна.
8. Заливка
Для всех металлов слишком высокая температура разливки может легко вызвать крупнозернистые дефекты.
9. Другой
- (1) Чрезмерная скорость охлаждения связана не только с конструкцией, системой разливки и составом металла, но и с другими факторами, такими как низкая плотность формовочного песка, когда необходимо использовать холодное железо, и временной интервал между разливкой и падением. Слишком длинный песок и укладка горячих отливок после падения песка и т. д.
- (2) Неправильная термообработка »также является одной из основных причин крупных частиц некоторых металлов.
- (3) Неправильная обработка «Неправильная обработка может привести к тому, что действительно плотные отливки будут выглядеть так, как будто они имеют крупнозернистые дефекты. Так называемая неправильная обработка означает неправильное шлифование инструмента, тупого инструмента, неправильную скорость резания или управление подачей, а также неправильный метод черновой обработки и т. д., который приведет к появлению пористости с определенными повреждениями. Считается, что отливка имеет дефект в виде крупных зерен.
Сохраните источник и адрес этой статьи для перепечатки.:Меры по предотвращению крупнозернистости отливок
Минхэ Компания по литью под давлением специализируются на производстве и предоставлении качественных и высокопроизводительных литых деталей (ассортимент металлических деталей для литья под давлением в основном включает Тонкостенное литье под давлением,Литье под давлением,Литье под давлением в холодной камере), Round Service (Служба литья под давлением,Обработка с ЧПУ,Изготовление пресс-форм, Обработка поверхности) .Любое индивидуальное литье под давлением из алюминия, магния или замака / цинка, а также другие требования к отливкам, пожалуйста, свяжитесь с нами.
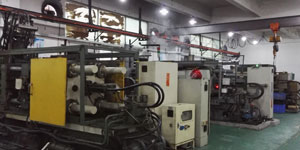
Под контролем ISO9001 и TS 16949, все процессы выполняются на сотнях передовых машин для литья под давлением, 5-осевых станках и других объектах, от струйных до стиральных машин Ultra Sonic. Minghe не только имеет современное оборудование, но и имеет профессиональное оборудование. команда опытных инженеров, операторов и инспекторов для воплощения в жизнь проекта заказчика.
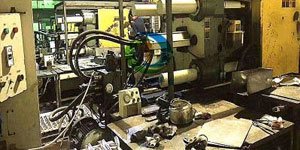
Контрактный производитель отливок под давлением. Возможности включают в себя детали для литья под давлением алюминия с холодной камерой весом от 0.15 фунта. до 6 фунтов, быстрая установка и обработка. Дополнительные услуги включают полировку, вибрацию, удаление заусенцев, дробеструйную очистку, окраску, гальванику, нанесение покрытий, сборку и оснастку. Обрабатываемые материалы включают такие сплавы, как 360, 380, 383 и 413.
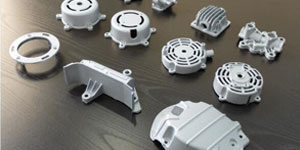
Помощь в проектировании литья цинка под давлением / сопутствующие инженерные услуги. Изготовление на заказ прецизионных отливок из цинка под давлением. Могут изготавливаться миниатюрные отливки, отливки под высоким давлением, отливки в формы с несколькими суппортами, отливки в обычные формы, единичные отливки под давлением и независимые отливки под давлением, а также отливки с герметизацией полости. Отливки могут изготавливаться длиной и шириной до 24 дюймов с допуском +/- 0.0005 дюйма.
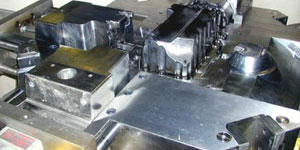
Производитель литья под давлением из магния, сертифицированный по стандарту ISO 9001: 2015. Возможности включают литье под давлением магния под высоким давлением с горячей камерой до 200 тонн и холодной камерой на 3000 тонн, проектирование инструментов, полировку, формование, механическую обработку, порошковую и жидкостную окраску, полный контроль качества с возможностями CMM , сборка, упаковка и доставка.
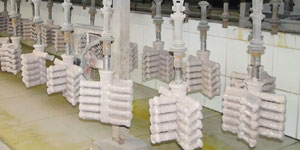
Сертифицирован ITAF16949. Дополнительные услуги трансляции включают инвестиционное литье,литье в песчаные формы,Гравитационное литье, Литье по выплавляемым моделям,Центробежное литье,Вакуумное литье,Постоянное литье формыВозможности включают EDI, техническую поддержку, твердотельное моделирование и вторичную обработку.
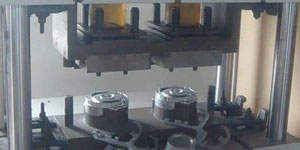
Литейная промышленность Примеры использования запчастей для: автомобилей, велосипедов, самолетов, музыкальных инструментов, судов, оптических устройств, датчиков, моделей, электронных устройств, корпусов, часов, машинного оборудования, двигателей, мебели, ювелирных изделий, приспособлений, телекоммуникаций, освещения, медицинских устройств, фотографических устройств, Роботы, скульптуры, звуковое оборудование, спортивное оборудование, инструменты, игрушки и многое другое.
Что мы можем вам сделать дальше?
∇ Перейти на главную страницу для Литье под давлением Китай
→Литье деталей-Узнай, что мы сделали.
→ Общие советы о Услуги литья под давлением
By Производитель литья под давлением Minghe | Категории: Полезные статьи |Материалы Теги: Литье алюминия, Цинковое литье, Литье магния, Титановое литье, Литье из нержавеющей стали, Латунное литье,Бронзовое литье,Кастинг видео,История компании,Литье алюминия под давлением | Комментарии отключены