Факторы, влияющие на свойства прутков из микролегированной высокопрочной стали марки ВН 500 МПа
Влияние содержания азота на механические свойства прутков из микролегированной высокопрочной стали марки ВН 500 МПа изучено в ходе производственных испытаний. Результаты показали, что содержание азота увеличилось с 81 до 269 частей в минуту, размер зерна стальных стержней существенно не изменился, а предел текучести стальных стержней увеличился с 526 МПа до 607 МПа. Предел текучести увеличился на 15.4%; предел прочности увеличился с 678 МПа до 738 МПа, а предел прочности увеличился на 8.8%; коэффициент прочности снизился с 1.29 до 1.22. Упрочняющее действие азота в стержнях из микролегированной высокопрочной стали ВН заключается в основном в дисперсионном упрочнении, и дисперсионное упрочнение является основной причиной снижения отношения прочности к пределу текучести стержней из стали ВН.
Введение
В январе 2012 года Министерство жилищного строительства и городского и сельского развития и Министерство промышленности и информационных технологий совместно выпустили документ, предлагающий руководство по ускорению применения высокопрочной стальной арматуры: к концу 2015 года производство высокопрочной стали На долю арматурного проката приходится 80% от общего выпуска арматуры. Для крупномасштабных высотных зданий и крупнопролетных общественных зданий предпочтительна арматура марки 500 МПа. С учетом потребностей экономического строительства моей страны потребность в высокопрочных стальных стержнях 500 МПа для строительных конструкций растет. Из-за высокой скорости производства стальных прутков и высокой температуры прокатки конечная температура прокатки обычно превышает 1000 ℃. Его технологические характеристики определяют, что легированная конструкция стальных стержней пригодна для использования технологии микролегирования ванадием [1]. Увеличение содержания азота идет на достижение ванадия. Основной метод упрочнения прутков из микролегированной стали способствует снижению количества ванадия и экономии ресурсов ванадия [2-4]. Технология микролегирования VN широко используется в качестве основной производственной технологии для разработки высокопрочных свариваемых стальных стержней в стране и за рубежом. Большое количество исследований показали [1-9], что технология микролегирования VN в основном основана на увеличении азота для ускорения осаждения ванадия в форме карбида ванадия, нитрида ванадия или карбонитрида ванадия, образуя мелкодисперсные частицы второй фазы для получения сильный эффект дисперсионного упрочнения. Для увеличения прочности стали. Однако чрезмерное увеличение содержания азота вызовет другие дефекты характеристик стальных стержней, особенно индекс сейсмостойкости стальных стержней. Влияние содержания азота на механические свойства прутков из микролегированной стали VN 500 МПа изучено в ходе производственных испытаний. Проанализирован механизм упрочнения азотом стержней из микролегированной стали ВН и влияние азота на прочность и коэффициент текучести стержней из микролегированной стали ВН, который является развитием стержней из микролегированной высокопрочной сейсмической стали.
Обеспечивают основу для производства.
Материалы и методы испытаний
Чтобы разработать высокопрочные стальные прутки марки 500 МПа со стабильными характеристиками, сталеплавильный завод компании группы последовательно выплавил три типа микролегированных сталей VN с разным содержанием азота и использовал один и тот же процесс производства арматуры (естественное охлаждение после прокатки) для тестирования производства. проката из стали марки 500МПа. Эти три стали имеют названия 1 #, 2 #, 3 #, а их основные химические компоненты показаны в таблице 1.
Рафинирование трех видов стали с различным содержанием азота и непрерывная разливка в заготовки со спецификациями 150 мм × 150 мм × 6000 мм, отправка их на завод группы компаний для прокатки в стальные стержни со спецификациями Φ25 мм и вытягивание образцов стальных стержней размером 1 # , 2 # и 3 #. В эксперименте были испытаны предел текучести и предел прочности на растяжение трех сталей соответственно, рассчитано отношение прочности к пределу текучести стальных стержней 1 #, 2 # и 3 #, а также металлографическая структура наблюдались три стали.
Согласно результатам испытаний на растяжение стальных стержней 1 #, 2 # и 3 # кривая показана на Рисунке 1. Кривая на Рисунке 1 показывает, что по мере увеличения содержания азота, предел текучести и предел прочности на растяжение стальных стержней. увеличивать последовательно. Предел текучести стального прутка 1 # составляет 526 МПа, а предел прочности при растяжении - 678 МПа; предел текучести стального прутка 2 # составляет 553 МПа, а предел прочности - 698 МПа; Предел текучести стального прутка 3 # составляет 607 МПа, а предел прочности - 738 МПа. Содержание азота увеличилось с 81PPM до 269PPM, предел текучести стальных стержней увеличился с 526MPa до 607MPa, увеличение на 81MPa, а предел текучести увеличился на 15.4%; в то же время предел прочности на разрыв увеличился с 678 МПа до 738 МПа, с увеличением на 60 МПа, а увеличение прочности на разрыв составило 8.8%.
В соответствии со значениями предела текучести и прочности на разрыв стальных стержней 1 #, 2 # и 3 #, соотношения прочности и текучести трех соответственно рассчитываются и наносятся на кривую, показанную на рисунке 2. Кривая на рисунке 2 показывает, что по мере увеличения содержания азота отношение прочности к пределу текучести стальных стержней последовательно уменьшается. Среди них отношения прочности к текучести стальных стержней 1, 2 и 3 # составляют 1.29, 1.26 и 1.22 в последовательности.
Влияние содержания азота на размер зерна стальных прутков
На рис. 3 показана металлографическая микроструктура стальных прутков 1, 2 и 3. Подробная информация о трех металлографических микроструктурах показана в таблице 2. В таблице 2 перечислены фазовый состав и размер зерна структуры стальных прутков 1 #, 2 #, 3 #. Три стальные конструкции представляют собой феррит + перлит, размер зерна феррита в стальном стержне 1 # составляет около 9-9.5, размер зерна феррита арматуры 2 # составляет около 9.5, размер зерна феррита 3 # составляет около 9-9.5. Данные в таблице 2 показывают, что с увеличением содержания азота размер зерен стального стержня существенно не изменяется или что увеличение содержания азота не оказывает значительного влияния на микроструктуру микролегированного стального стержня VN.
Анализ и обсуждение
Анализ механизма упрочнения азотом микролегированной стали ВН 500МПа
Результаты испытаний в этой статье показывают, что содержание азота в прутках из микролегированной стали марки VN 500 МПа увеличилось с 81 до 269 частей в минуту, а размер зерен стальных прутков составляет примерно 9-9.5. То есть увеличение содержания азота не оказывает очевидного влияния на структуру стержней из микролегированной стали ВН. В то же время предел текучести и предел прочности стальных стержней увеличились в разной степени, причем предел текучести увеличился на 81 МПа, а предел прочности на разрыв - на 60 МПа. В настоящее время основные теории упрочнения стальных материалов включают упрочнение твердого раствора, упрочнение мелкозернистой стали, упрочнение с фазовым переходом и упрочнение второй фазы. Очевидно, что результаты испытаний в этой статье явно исключают эффект мелкозернистого упрочнения, в то время как упрочнение твердого раствора и фазовый переход. Упрочняющие эффекты, такие как упрочнение, в основном одинаковы для трех сталей, испытанных в этой статье, за исключением упрочнения второй. фаза. Большое количество теоретических исследований и практики показали, что азот фиксируется ванадием в ванадийсодержащих микролегированных сталях с образованием нитрида ванадия или продуктов второй фазы, таких как карбонитрид ванадия, частицы второй фазы в стали значительно повышают прочность сталь через механизм взаимодействия со скользящей дислокацией, то есть эффект дисперсионного упрочнения.
Соответствующие исследования показали, что увеличение содержания азота способствует осаждению ванадия. То есть азот способствует осаждению ванадия и увеличивает объемную долю частиц второй фазы. Последовательные результаты исследований показывают, что прочность стали пропорциональна половинной объемной доле частиц второй фазы. Следовательно, когда содержание ванадия является достаточным, увеличение содержания азота в микролегированной стали VN фактически составляет. Объемная доля частиц второй фазы (нитрида ванадия, карбонитрида ванадия) в стали увеличивается, так что эффект дисперсионного упрочнения становится сильнее. Результаты испытаний, приведенные в этой статье, показывают, что с увеличением содержания азота последовательно увеличиваются предел текучести и предел прочности при растяжении прутков марки VN 500 МПа. Очевидно, что результаты испытаний в этой статье согласуются с результатами соответствующих теоретических исследований.
Анализ влияния азота на предел текучести стержней из микролегированной стали марки ВН 500 МПа
Результаты испытаний в этой статье показывают, что с увеличением содержания азота предел текучести и предел прочности на разрыв прутков из микролегированной стали VN не увеличиваются в той же пропорции. Увеличение предела текучести составляет 15.4%, а увеличение предела прочности на разрыв - 8.8%. Именно потому, что увеличение предела текучести больше, чем увеличение предела текучести, это явление снижает соотношение прочности и текучести стальных стержней.
Предел текучести стальных материалов и микроскопический механизм контроля прочности на разрыв, очевидно, различаются. Податливость в основном контролируется крупномасштабным скольжением дислокаций в материале, в то время как разрушение в основном контролируется зарождением и распространением микротрещин в материале. . Таким образом, исследование текучести материала в основном рассматривает поведение дислокаций в материале, в то время как исследование разрушения материала в основном рассматривает поведение микротрещин в материале. Предел текучести стальных материалов относится к прочности, когда источник дислокаций в материале активирован и большое количество подвижных дислокаций скользит, что приводит к тому, что материал поддается или вызывает определенную степень пластической деформации. Механизм дисперсионного упрочнения частиц второй фазы - это механизм взаимодействия между частицами второй фазы и скользящей дислокацией. Этот механизм взаимодействия подразделяется на механизм прорезания и механизм Орована, будь то механизм прорезания или механизм Орована, второй. Выделение фазовых частиц будет препятствовать скольжению дислокаций, тем самым значительно улучшая предел текучести стали. Что касается прочности на разрыв стальных материалов, то она в основном связана с образованием и распространением микротрещин в стали. Образование микротрещин включает в себя препятствие движению микродислокаций, что неизбежно препятствует образованию и распространению микротрещин. Расширение, тем самым в определенной степени улучшая прочность стали на растяжение. Следовательно, хотя предел текучести стали улучшается, ее предел прочности также в определенной степени улучшается.
Отмечено, что, когда размер второй фазы очень мал, эффект дисперсионного упрочнения при увеличении предела текучести стали больше, чем эффект увеличения предела прочности стали на растяжение. Результаты испытаний в этой статье показывают, что вклад дисперсионного упрочнения в предел текучести составляет 81 МПа, значение вклада прочности на разрыв составляет 60 МПа. Результаты этой работы доказывают, что вклад дисперсионного упрочнения в предел текучести больше, чем вклад прочности на растяжение. Кроме того, даже если предел текучести и предел прочности стали увеличиваются в той же степени, коэффициент текучести стали будет уменьшаться. В целом эффект дисперсионного упрочнения частиц второй фазы в конечном итоге приведет к снижению коэффициента текучести стали. Следовательно, с увеличением содержания азота, чем сильнее эффект дисперсионного упрочнения стального стержня VN, тем ниже отношение прочности к пределу текучести стального стержня.
Освещение результатов исследований по разработке сейсмической арматуры 500 МПа.
В результатах испытаний этой статьи содержание азота в прутках из микролегированной стали марки VN 500 МПа составляет 81PPM, 136PPM, 269PPM, а соответствующие показатели прочности и текучести стального прутка составляют 1.29, 1.26, 1.22, то есть соотношение прочности и текучести Прутки из микролегированной стали VN варьируются в зависимости от того, как содержание азота увеличивается и уменьшается, подробный анализ причин уже был проведен. В настоящее время основной показатель сейсмостойкости высокопрочных антисейсмических стальных стержней должен быть не менее 1.25. Таким образом, по результатам исследований в этой статье, для разработки микролегированных высокопрочных антисейсмических стальных стержней класса VN 500 МПа, чтобы обеспечить высокий основной индекс сейсмических характеристик. Если коэффициент текучести квалифицирован, азот содержание должно строго контролироваться с точки зрения химического состава. Более целесообразно контролировать содержание азота в пределах 130 частей на миллион.
Заключение
- 1) При увеличении содержания азота размер зерен прутка из микролегированной высокопрочной стали существенно не изменяется.
- 2) Предел текучести и предел прочности на разрыв прутков из микролегированной высокопрочной стали повышаются с увеличением содержания азота, но коэффициент текучести уменьшается с увеличением содержания азота.
- 3) Упрочняющее действие азота в стержнях из микролегированной высокопрочной стали ВН заключается в основном в дисперсионном упрочнении, и дисперсионное упрочнение является основной причиной снижения отношения прочности к пределу текучести стержней из стали ВН.
- 4) При разработке прутков из микролегированной высокопрочной сейсмической стали марки ВН 500 МПа содержание азота в стали должно контролироваться в пределах 130 л / мин.
Сохраните источник и адрес этой статьи для перепечатки.: Факторы, влияющие на свойства прутков из микролегированной высокопрочной стали марки ВН 500 МПа
Минхэ Компания по литью под давлением специализируются на производстве и предоставлении качественных и высокопроизводительных литых деталей (ассортимент металлических деталей для литья под давлением в основном включает Тонкостенное литье под давлением,Литье под давлением,Литье под давлением в холодной камере), Round Service (Служба литья под давлением,Обработка с ЧПУ,Изготовление пресс-форм, Обработка поверхности) .Любое индивидуальное литье под давлением из алюминия, магния или замака / цинка, а также другие требования к отливкам, пожалуйста, свяжитесь с нами.
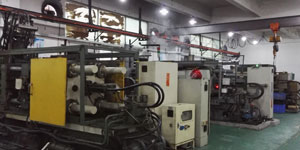
Под контролем ISO9001 и TS 16949, все процессы выполняются на сотнях передовых машин для литья под давлением, 5-осевых станках и других объектах, от струйных до стиральных машин Ultra Sonic. Minghe не только имеет современное оборудование, но и имеет профессиональное оборудование. команда опытных инженеров, операторов и инспекторов для воплощения в жизнь проекта заказчика.
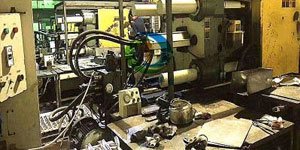
Контрактный производитель отливок под давлением. Возможности включают в себя детали для литья под давлением алюминия с холодной камерой весом от 0.15 фунта. до 6 фунтов, быстрая установка и обработка. Дополнительные услуги включают полировку, вибрацию, удаление заусенцев, дробеструйную очистку, окраску, гальванику, нанесение покрытий, сборку и оснастку. Обрабатываемые материалы включают такие сплавы, как 360, 380, 383 и 413.
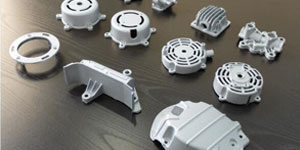
Помощь в проектировании литья цинка под давлением / сопутствующие инженерные услуги. Изготовление на заказ прецизионных отливок из цинка под давлением. Могут изготавливаться миниатюрные отливки, отливки под высоким давлением, отливки в формы с несколькими суппортами, отливки в обычные формы, единичные отливки под давлением и независимые отливки под давлением, а также отливки с герметизацией полости. Отливки могут изготавливаться длиной и шириной до 24 дюймов с допуском +/- 0.0005 дюйма.
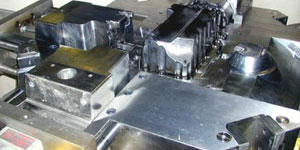
Производитель литья под давлением из магния, сертифицированный по стандарту ISO 9001: 2015. Возможности включают литье под давлением магния под высоким давлением с горячей камерой до 200 тонн и холодной камерой на 3000 тонн, проектирование инструментов, полировку, формование, механическую обработку, порошковую и жидкостную окраску, полный контроль качества с возможностями CMM , сборка, упаковка и доставка.
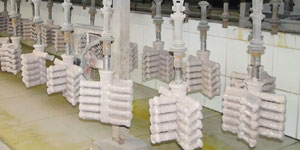
Сертифицирован ITAF16949. Дополнительные услуги трансляции включают инвестиционное литье,литье в песчаные формы,Гравитационное литье, Литье по выплавляемым моделям,Центробежное литье,Вакуумное литье,Постоянное литье формыВозможности включают EDI, техническую поддержку, твердотельное моделирование и вторичную обработку.
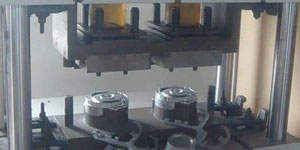
Литейная промышленность Примеры использования запчастей для: автомобилей, велосипедов, самолетов, музыкальных инструментов, судов, оптических устройств, датчиков, моделей, электронных устройств, корпусов, часов, машинного оборудования, двигателей, мебели, ювелирных изделий, приспособлений, телекоммуникаций, освещения, медицинских устройств, фотографических устройств, Роботы, скульптуры, звуковое оборудование, спортивное оборудование, инструменты, игрушки и многое другое.
Что мы можем вам сделать дальше?
∇ Перейти на главную страницу для Литье под давлением Китай
→Литье деталей-Узнай, что мы сделали.
→ Общие советы о Услуги литья под давлением
By Производитель литья под давлением Minghe | Категории: Полезные статьи |Материалы Теги: Литье алюминия, Цинковое литье, Литье магния, Титановое литье, Литье из нержавеющей стали, Латунное литье,Бронзовое литье,Кастинг видео,История компании,Литье алюминия под давлением | Комментарии отключены