Что такое литье под давлением? Что такое процесс литья под давлением?
Литье под высоким давлением - это своего рода специальный метод литья с меньшими затратами и без резания, который быстро развился в современной технологии обработки металлов. Это процесс, в котором расплавленный металл заливают в форму под высоким давлением и с высокой скоростью, а затем кристаллизуют и затвердевают под высоким давлением с образованием отливки. Высокое давление и высокая скорость - основные характеристики литья под высоким давлением. Обычно используемое давление составляет десятки мегапаскалей, скорость заполнения (скорость внутреннего затвора) составляет примерно 16-80 м / с, а время заполнения расплавленным металлом полости формы чрезвычайно короткое, примерно 0.01-0.2 секунды. Поскольку продукты, произведенные этим методом, имеют преимущества высокой эффективности производства, простых процедур, более высоких уровней допуска отливок, хорошей шероховатости поверхности и высокой механической прочности, он может сэкономить много процедур обработки и оборудования, сэкономить сырье и т. Д. , так что это стало литье важной частью отрасли.
Основные параметры процесса литья под давлением
1. Введение в процесс литья под давлением
- A: Процесс литья под давлением представляет собой процесс органического сочетания трех элементов машины для литья под давлением, формы для литья под давлением и сплава для литья под давлением.
- B: Процесс заполнения полости металлом во время литья под давлением - это процесс динамического уравновешивания факторов процесса, таких как давление, скорость, температура и время.
- C: Эти факторы процесса как ограничивают друг друга, так и дополняют друг друга. Только правильно подбирая и корректируя эти факторы, чтобы согласовать их, можно получить ожидаемые результаты. В процессе литья под давлением можно получить не только технологичность конструкции отливки, но и усовершенствованный характер формы. Производительность и конструкция машины для литья под давлением превосходны, адаптируемость к выбору сплава для литья под давлением и стандартизация процесса плавки. Больше внимания следует уделять важному влиянию давления, скорости и времени на качество отливок.
2. давление
Наличие давления - главная особенность, которая отличает процесс литья под давлением от других методов литья. Давление - фактор, благодаря которому отливки приобретают компактную структуру и четкие очертания; давление может быть выражено в силе впрыска и удельном давлении.
2.1 Сила впрыска
Сила впрыска - это сила, которая толкает движение впрыскивающего поршня в механизме впрыска литье под давлением машина. Сила впрыска является основным параметром, отражающим функцию машины для литья под давлением. Величина силы впрыска определяется площадью поперечного сечения цилиндра впрыска и давлением рабочей жидкости в камере впрыска. Формула силы впрыска имеет следующий вид: F давление = P жидкость XA цилиндр
2.2 Удельное давление
Давление расплавленного металла в барокамере на единицу площади называется удельным давлением. Удельное давление - это отношение силы впрыска к площади поперечного сечения напорной камеры. Формула расчета выглядит следующим образом: соотношение P = впрыск P / камера.
Удельное давление является методом выражения действительной силы расплавленного металла на каждой стадии процесса заполнения и отражает концепцию силы расплавленного металла на каждой стадии заполнения и когда металл течет через различные поперечные сечения. области. Удельное давление во время наполнения называется удельным давлением наполнения или удельным давлением впрыска. Удельное давление в фазе наддува называется удельным давлением наддува. Величины двух удельных давлений также определяются в соответствии с силой впрыска.
2.3 Роль и влияние давления
- A: Удельное давление заполнения предназначено для преодоления сопротивления потоку в системе затвора и полости, особенно сопротивления на внутреннем затворе, чтобы поток металлической жидкости мог достичь требуемой скорости внутреннего затвора.
- B: Давление наддува и удельное давление определяют давление на затвердевший металл и силу выпучивания, возникающую в это время. Влияние удельного давления на механические свойства отливки: повышенное удельное давление, мелкие кристаллы и увеличенные мелкозернистые слои. Более толстые, благодаря улучшенным характеристикам заполнения, улучшенному качеству поверхности, уменьшению поровых эффектов и повышенной прочности на разрыв.
- C: Влияние на условия заполнения: расплав сплава заполняет полость под высоким удельным давлением, температура сплава повышается и улучшается текучесть, что способствует улучшению качества отливок.
3. скорость
Во время процесса литья под давлением на скорость впрыска напрямую влияет давление, и вместе с давлением оно играет важную роль для внутреннего качества, требований к поверхности и четкости контура отливки. Давление - это основная скорость. Представление скорости делится на два типа: скорость удара и скорость затвора.
3.1 Взаимосвязь между скоростью удара и скоростью полового акта
Согласно принципу непрерывности, при этом объем потока металла, протекающего через жидкость сплава с площадью поперечного сечения напорной камеры F1 со скоростью V1, должен быть равен объему жидкости сплава протекающий через внутренний затвор с площадью поперечного сечения F2 со скоростью V2 F1 камера V1 выстрел = Внутри F2 и внутри V2. Следовательно, чем выше скорость впрыска отбойного молотка, тем выше металл проходит через затвор.
3.2 Скорость впрыска
- О: Скорость впрыска делится на два уровня. Скорость впрыска первого уровня также называется медленной скоростью впрыска. Этот уровень скорости относится к скорости движения пуансона от начального движения до тех пор, пока пуансон не отправит расплавленный металл из комнаты во внутренние ворота. На этом этапе требуется заполнить камеру давления расплавленным металлом в камере давления, следуя принципу не слишком сильно снижать температуру жидкости сплава, но также помогая удалить газ в камере давления.
- B: Скорость вторичного впрыска также называется скоростью быстрого впрыска. Эта скорость определяется характеристиками машины для литья под давлением. Максимальная скорость впрыска, обеспечиваемая машиной для литья под давлением, обычно находится в диапазоне 4-5 м / с.
3.3 Роль и влияние высокой скорости впрыска
Влияние и влияние высокой скорости впрыска на механические свойства сплавов, увеличение скорости впрыска, преобразование кинетической энергии в тепловую, улучшение текучести расплава сплава, помощь в устранении дефектов, таких как следы текучести, барьеры от холода, и улучшение механических свойств и качество поверхности. Но когда скорость слишком высока, расплав сплава будет туманным и смешанным с газом, что приведет к серьезному захвату и ухудшению механических свойств.
3.4 Скорость внутренних ворот
Линейная скорость, когда расплавленный металл входит во внутренний затвор и вводится в полость, называется скоростью внутреннего затвора; обычный диапазон скорости внутренних ворот 15-70 м / с. Скорость внутреннего затвора имеет большое влияние на механические свойства отливки. Если скорость внутренних ворот слишком мала, прочность отливки снижается; увеличивается скорость, увеличивается сила; скорость слишком высока, и сила падает.
4. Температуры
В процессе литья под давлением температура играет важную роль в тепловом состоянии процесса заполнения и эффективности операции. Температура, относящаяся к литью под давлением, относится к температуре заливки, температуре и температуре формы. Контроль температуры - важный производственный фактор для получения хороших отливок. Температура разливки расплавленного металла относится к средней температуре, когда он входит в полость из напорной камеры. Поскольку измерять температуру расплавленного металла в наполняющей камере неудобно, ее обычно выражают как температуру раздаточной печи.
4.1 Роль и влияние температуры заливки
Влияние температуры сплава на механические свойства отливок. По мере повышения температуры сплава. Механические характеристики улучшились, но после определенного предела производительность ухудшается, основными причинами являются:
- A: Растворимость газа в сплаве увеличивается с повышением температуры. Хотя газ растворен в сплаве, его трудно осаждать в процессе литья под давлением, что влияет на механические свойства.
- B: содержание железа увеличивается с повышением температуры сплава, что снижает текучесть, крупные кристаллы и ухудшает характеристики.
- C: Алюминиевые и магниевые сплавы становятся более окисленными с повышением температуры, окисляя включения и ухудшая свойства сплава.
4.2 Роль и влияние температуры пресс-формы
В процессе литья под давлением форма требует определенной температуры. Температура формы - еще один важный фактор в процессе литья под давлением, который играет важную роль в повышении эффективности производства и получении высококачественных отливок.
Во время процесса наполнения температура формы имеет большое влияние на температуру металлической жидкости, вязкость, текучесть, время наполнения, состояние потока при прямом наполнении и т. Д. Когда температура формы слишком низкая, поверхностный слой конденсируется и высокоскоростной поток жидкости снова прерывается, что приводит к появлению дефектов поверхностного слоя, даже если температура формования слишком высока, хотя полезно получить гладкую поверхность отливки, она легко дает усадку и вмятину
Температура формы оказывает значительное влияние на скорость охлаждения, кристаллическое состояние и усадочное напряжение расплава сплава.
Если температура формы слишком низкая, усадочное напряжение увеличится, и отливка склонна к образованию трещин.
Температура формы имеет большое влияние на срок ее службы. Сильные перепады температуры формируют сложное напряженное состояние, а частые изменения напряжения вызывают ранние трещины.
Температура формы влияет на размерный допуск отливки. Если температура формы стабильна, размерная усадка отливки также остается стабильной, и уровень допусков на размер также улучшается.
5. Время
«Время» в процессе литья под давлением - это время заполнения, время создания давления, время выдержки под давлением и время удерживания формы. Все эти «времена» - это три фактора: давление, скорость и температура, а также физические свойства расплавленного металла. , Структура отливки (особенно толщина стенок), структура формы (особенно система заливки и система перелива) и другие подробные результаты.
5.1 Время наполнения
Время, необходимое для того, чтобы расплавленный металл попал в полость под давлением до ее заполнения, называется временем заполнения. Время заполнения оцинкованных деталей составляет 0.02 с, а время заполнения деталей для впрыска топлива составляет 0.04 с.
5.2 Время наполнения
Время повышения давления наддува относится к фазе наддува расплавленного металла в процессе заполнения, начиная с момента заполнения полости до тех пор, пока давление наддува не достигнет заданного значения, то есть от повышения удельного давления впрыска до увеличение Время, необходимое для повышения давления
5.3 Время выдержки
После того, как расплавленный металл заполняет полость, период времени, в течение которого расплавленный металл затвердевает под действием давления наддува, называется временем выдержки. Функция времени выдержки состоит в том, чтобы заставить инжекционный пуансон передавать давление через не затвердевший оставшийся материал и не затвердевший металл в части затвора в полость, чтобы затвердевший металл кристаллизовался под давлением с получением плотной отливки.
3. Дизайн литья под давлением
Для того чтобы принципиально предотвратить появление дефектных изделий и массового производства деталей для литья под давлением с низкими затратами, конструкция деталей для литья под давлением должна подходить для производства литья под давлением. Хорошая конструкция для литья под давлением может гарантировать срок службы, производство и надежность изготовления пресс-формы. При хорошем уровне текучести нижеследующее поясняет принципы проектирования и требования к конструкции и процессу литья под давлением.
1. Избегайте внутренней вогнутости и минимизируйте количество боковых вытягиваний сердечника при проектировании
2. Расчет толщины стенок отливок под давлением.
Толщина стенок отливок под давлением обычно составляет 2-5 мм. Обычно считается, что толщина стенки 7 мм или более не является хорошей, поскольку ее прочность снижается с увеличением толщины стенки. Кроме того, при расчете толщины стенки следует придерживаться принципа равной толщины стенки, насколько это возможно, в основном для предотвращения большой разницы между усадочным напряжением, создаваемым локальными горячими соединениями, и разной толщиной, вызывающей внутренние поры, деформацию, трещины и другие дефекты. .
3. Круглый угловой дизайн литья под давлением
За исключением особых требований к согласованию, все части отливки должны иметь закругленные углы. Функция закругленных углов заключается в том, чтобы избежать концентрации напряжений и растрескивания, и в то же время продлить срок службы формы. Кроме того, если детали требуют обработки поверхности, можно равномерно покрыть закругленные углы. Пол.
4. Расчет угла тяги литья под давлением.
Роль угла уклона состоит в том, чтобы обеспечить плавное извлечение изделия из формы, уменьшить усилие затяжки деталей и избежать деформации деталей. Минимальный наклон отлитых под давлением деталей указан в следующей таблице, и следует выбирать наибольший наклон, если он разрешен. , Общий диапазон составляет 1-3 градуса с одной стороны.
5. Конструкция позиции выброса в процессе литья под давлением.
После открытия формы в процессе литья под давлением продукт наматывается на подвижную форму и должен выталкиваться выталкивающим штифтом формы. Следовательно, в изделии должно быть достаточно места для размещения выталкивающего стержня. Диаметр выталкивающего штифта отлитого под давлением изделия обычно составляет более 5 мм и менее 5 мм. Он часто ломается во время производства, поэтому не рекомендуется. При проектировании изделий из литья под давлением учитывайте, достаточно ли места и места для выброса. Старайтесь избегать использования наперстка особой формы и используйте круглый наперсток. При этом обратите внимание на положение наперстка и стенки. Достаточное расстояние, обычно более 3 мм.
6. Уменьшить дизайн последующей обработки отливок под давлением.
Детали, отлитые под давлением, позволяют достичь высокой точности размеров, поэтому большинство поверхностей и деталей не требуют механической обработки и могут быть непосредственно собраны и использованы. При этом механическая обработка не поддерживается по двум причинам. Во-первых, поверхность отливки твердая и износостойкая, и после обработки она теряется. Это охлажденный слой, второй заключается в том, что внутри литья под давлением обычно есть поры. Мелкие дисперсные поры не влияют на использование. После обработки поры подвергаются воздействию, что влияет на внешний вид и функцию использования. Даже если есть особые требования, требующие механической обработки, ее следует использовать. Разумно контролируйте припуск на обработку, сокращайте время обработки и вероятность просачивания отверстий для воздуха. Обычно припуск на обработку не превышает 0.8. Чтобы свести к минимуму механическую обработку, требуется обоснованно сформулировать допуск чертежа, чтобы обеспечить установку деталей. Несоответствующий диапазон допуска приведет к увеличению последующей обработки. Во-вторых, разумная конструкция снижает усадку и деформацию деталей. В-третьих, угловые монтажные отверстия можно рассматривать как отверстия в форме стыка.
7. Встроенный дизайн в литье под давлением.
Металлические или неметаллические вставки можно отливать в детали, отлитые под давлением, в основном для улучшения местной прочности и износостойкости или для образования трудноформируемых внутренних полостей. Деталь, в которой вставка заделана в металл, должна быть спроектирована таким образом, чтобы предотвратить вращение и осевое перемещение. Учитывайте удобство вставки вставки в форму и устойчивость к ударам расплавленного металла.
5. Кейсы решения проблем качества литья под давлением.
Проблема не видения света при обработке 100 граней из ракушки
1.1 Обзор статуса
1.2 Причина, по которой обработка не видит свет
1.2.1 При обработке оболочки сначала используйте торцевые поверхности B1, B2 и B3 в качестве эталонной поверхности для обработки движущейся поверхности фильеры, а затем используйте обработанную движущуюся поверхность фильеры в качестве эталонной поверхности для обработки статической поверхности фильеры. После измерения невидимой части было обнаружено, что подвижная поверхность формы после обработки имеет фаску (как показано на рисунке ниже). По сравнению с обычной обрабатываемой деталью, подвижная поверхность формы невидимой детали локально обрабатывается на 1 мм больше. Это вызвано неправильным зажимом базовой плоскости B2 или деформацией базовой плоскости во время обработки.
1.3. Причины деформации базового отверстия B2
1.3.1 Толщина фрезы частичного типа приводит к увеличению торца эталонного отверстия B2. Толщина стенки невидимой части B2 составляет 8 мм, а две толщины стенок нормальной обрабатываемой части B одинаковы. Толщина стены меняется мало. Толщина заусенца не является причиной увеличения торцевой поверхности контрольного отверстия B2.
1.3.2 Сердечники отверстий B1, B2 и B3 на кристаллизаторе зафиксированы, отступа стержня не обнаружено. Проблема отступления ядра может быть устранена.
1..3 Удар в отверстии B2 вызывает его деформацию. Обратите внимание на возвращенную неисправную деталь. У лунки B2 серьезные неровности, и неровность не нова. Удар является основной причиной деформации отверстия B2.
Заключение 1.4
Вывод: из-за столкновения отверстие B2 деформируется в сторону статической формы, что делает B2 выше при обработке подвижной поверхности формы. Подвижная поверхность формы обрабатывается до фаски, а локальная обработка составляет еще 1 мм; при обработке статической поверхности пресс-формы подвижная поверхность пресс-формы используется в качестве опорной плоскости. Статическая часть пресс-формы, соответствующая многопроцессорному положению подвижной пресс-формы, не имеет объема обработки, что делает обработку статической стороны пресс-формы невидимой.
1.5 Меры по улучшению
1.5.1 При размещении деталей в цехе литья под давлением и цехе очистки аккуратно размещайте их и аккуратно, чтобы избежать ударов по отливкам, и строго соблюдайте процесс. Между каждым слоем отливок кладем по два слоя картона. Отдел хранения и транспортировки. Во время оборота предохраняйте погрузчик от ударов по деталям и не допускайте ударов деталей из-за несоответствующих методов транспортировки вилочным погрузчиком и чрезмерной скорости транспортировки.
1.5.2 Своевременно очищайте отрезные заусенцы, чтобы избежать слишком толстых отрезных заусенцев.
2.2 Анализ причин
2.2.1 Диаметр отверстия в детали, где поры появляются в отверстии 701 # Lishell, равен q26, диаметр отверстия после обработки равен p27.9, припуск на обработку составляет 0.95 мм, припуск на обработку большой, поры легкие. появляться.
Заключение 2.3
Вывод: внутренняя температура 701 # слишком высока, она находится в глубокой полости, и выхлоп плохой, а припуск на обработку слишком велик, что приводит к тому, что отверстие 701 # становится склонным к образованию пор после обработки.
2.4 Меры по улучшению
2.4.1 Технический отдел, предназначенный для добавления воды в скважину № 701 для снижения температуры ядра; изменить чертеж пресс-формы, добавить переливающую канавку в отверстии 701 # для усиления вытяжного эффекта; изменить чертеж сердечника и изменить припуск на обработку отверстий 701 # Уменьшен с 0.9 мм до 0.7 мм.
Сохраните источник и адрес этой статьи для перепечатки.: Что такое литье под давлением? Что такое процесс литья под давлением?
Минхэ Компания по литью под давлением специализируются на производстве и предоставлении качественных и высокопроизводительных литых деталей (ассортимент металлических деталей для литья под давлением в основном включает Тонкостенное литье под давлением,Литье под давлением,Литье под давлением в холодной камере), Round Service (Служба литья под давлением,Обработка с ЧПУ,Изготовление пресс-форм, Обработка поверхности) .Любое индивидуальное литье под давлением из алюминия, магния или замака / цинка, а также другие требования к отливкам, пожалуйста, свяжитесь с нами.
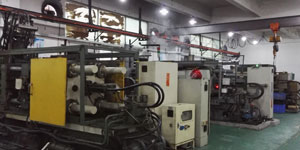
Под контролем ISO9001 и TS 16949, все процессы выполняются на сотнях передовых машин для литья под давлением, 5-осевых станках и других объектах, от струйных до стиральных машин Ultra Sonic. Minghe не только имеет современное оборудование, но и имеет профессиональное оборудование. команда опытных инженеров, операторов и инспекторов для воплощения в жизнь проекта заказчика.
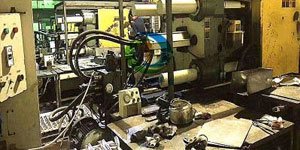
Контрактный производитель отливок под давлением. Возможности включают в себя детали для литья под давлением алюминия с холодной камерой весом от 0.15 фунта. до 6 фунтов, быстрая установка и обработка. Дополнительные услуги включают полировку, вибрацию, удаление заусенцев, дробеструйную очистку, окраску, гальванику, нанесение покрытий, сборку и оснастку. Обрабатываемые материалы включают такие сплавы, как 360, 380, 383 и 413.
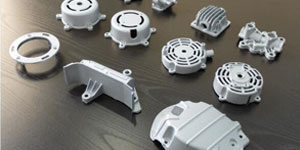
Помощь в проектировании литья цинка под давлением / сопутствующие инженерные услуги. Изготовление на заказ прецизионных отливок из цинка под давлением. Могут изготавливаться миниатюрные отливки, отливки под высоким давлением, отливки в формы с несколькими суппортами, отливки в обычные формы, единичные отливки под давлением и независимые отливки под давлением, а также отливки с герметизацией полости. Отливки могут изготавливаться длиной и шириной до 24 дюймов с допуском +/- 0.0005 дюйма.
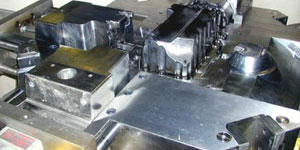
Производитель литья под давлением из магния, сертифицированный по стандарту ISO 9001: 2015. Возможности включают литье под давлением магния под высоким давлением с горячей камерой до 200 тонн и холодной камерой на 3000 тонн, проектирование инструментов, полировку, формование, механическую обработку, порошковую и жидкостную окраску, полный контроль качества с возможностями CMM , сборка, упаковка и доставка.
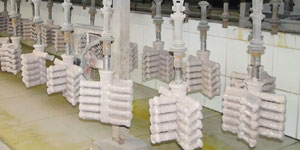
Сертифицирован ITAF16949. Дополнительные услуги трансляции включают инвестиционное литье,литье в песчаные формы,Гравитационное литье, Литье по выплавляемым моделям,Центробежное литье,Вакуумное литье,Постоянное литье формыВозможности включают EDI, техническую поддержку, твердотельное моделирование и вторичную обработку.
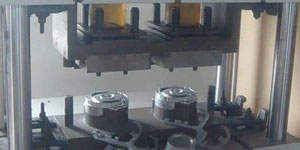
Литейная промышленность Примеры использования запчастей для: автомобилей, велосипедов, самолетов, музыкальных инструментов, судов, оптических устройств, датчиков, моделей, электронных устройств, корпусов, часов, машинного оборудования, двигателей, мебели, ювелирных изделий, приспособлений, телекоммуникаций, освещения, медицинских устройств, фотографических устройств, Роботы, скульптуры, звуковое оборудование, спортивное оборудование, инструменты, игрушки и многое другое.
Что мы можем вам сделать дальше?
∇ Перейти на главную страницу для Литье под давлением Китай
→Литье деталей-Узнай, что мы сделали.
→ Общие советы о Услуги литья под давлением
By Производитель литья под давлением Minghe | Категории: Полезные статьи |Материалы Теги: Литье алюминия, Цинковое литье, Литье магния, Титановое литье, Литье из нержавеющей стали, Латунное литье,Бронзовое литье,Кастинг видео,История компании,Литье алюминия под давлением | Комментарии отключены