Сборник общих дефектов и профилактических мероприятий при науглероживании и закалке
Науглероживание и закалка - фактически составной процесс, а именно науглероживание + закалка. Мы часто привыкли говорить об этих двух вместе, потому что два процесса, которые выполняются на одном и том же оборудовании, наиболее часто встречаются в производстве (но есть также науглероживание воздушного охлаждения, науглероживание медленного охлаждения, а затем процессы повторного нагрева и закалки и вторичные процессы). Закалка. Процесс) Тогда некоторые из нежелательных явлений, встречающихся при производстве, - это проблемы науглероживания, некоторые - проблемы закалки, а некоторые - результат комбинированного воздействия науглероживания и закалки.
Мы знаем, что все процессы термообработки неотделимы от трех основных проблем: нагрева, сохранения тепла и охлаждения. Подробно, включая температуру нагрева, скорость нагрева, время выдержки, скорость охлаждения и, конечно же, вопросы атмосферы. Поэтому, если что-то пойдет не так, мы обычно анализируем причину с учетом этих аспектов.
Для науглероживания и закалки мы часто проверяем следующие показатели: внешний вид поверхности продукта, твердость поверхности, твердость сердцевины, глубину науглероженного слоя, (эффективная глубина закаленного слоя, глубина полностью закаленного слоя) металлографическая структура и деформация. Поделимся своими взглядами на эти показатели соответственно.
1. Проблема с внешним видом
1. Оксидная накипь: в основном это происходит из-за утечки оборудования, загрязненного газа-носителя или содержания воды. Причину нужно искать в оборудовании и сырье.
2. Другой наиболее неприятной проблемой является проблема пятен, которая также является новым и сложным требованием для термической обработки в наше время. Причины сложны и очень глубоки.
два. Безусловная твердость
1. Высокая твердость (не обсуждается)
2. Низкая твердость. Возможны две ситуации, одна из которых - неквалифицированное науглероживание. Причина может заключаться в том, что науглероженный слой слишком мелкий, чтобы соответствовать требованиям чертежей (науглероженный слой не пропитан), или выбранный масштаб обнаружения превышает допустимый диапазон существующего науглероженного слоя, что приведет к разрушению науглероженного слоя.
Решение: Пополните фильтрацию и следуйте инструкциям по проверочной линейке. JBT 6050-2006 «Общие принципы контроля твердости при термообработке стальных деталей» Глубина науглероженного слоя фактически является функцией температуры, времени и углеродного потенциала. Исходя из вышеперечисленных факторов, мы можем рассмотреть способы повышения температуры нагрева, увеличения времени выдержки и увеличения потенциала науглероживания. (Конечно, настройка каждого параметра должна полностью сочетаться с требованиями вашего собственного оборудования и продуктов). Это также может быть связано с существованием на поверхности организаций, не связанных с лошадьми. Другая ситуация возникает, когда твердость низкая, то есть науглероживание допустимо, а закалка неквалифицированная. Вообще говоря, не закаливается. Как говорится, это самая сложная ситуация: термообработка предполагает нагрев три четверти, а охлаждение - семь четвертей. Это также отражает положение, которое процесс охлаждения занимает в процессе термообработки.
Ниже приводится сравнительный тест, который я разработал. Вы можете обсудить влияние охлаждения на твердость.
Возьмите 3 группы испытательных стержней из разных материалов, но с одинаковыми характеристиками и размерами, размер которых составляет Φ20 мм X 100 мм. (Мы называем испытательный стержень из стали № 20 № 1, испытательный стержень из 20Cr № 2 и испытательный стержень из 20CrMnTi № 3) Испытательные стержни науглероживаются при той же температуре с использованием того же процесса. Предполагая, что глубина науглероженного слоя трех испытательных стержней составляет 0.6-0.7 мм (ps: допущение установлено только в идеальном состоянии).
Пожалуйста, примите во внимание следующие условия:
а. Завершите закалку в тех же условиях.
б. Среда закалки: медленное масло, быстрое масло, чистая вода, соленая вода.
c. В одной и той же среде без перемешивания и интенсивного перемешивания и гашения каждую из трех испытательных полосок берут на две группы для тестирования.
После завершения науглероживания группа A закаливается при 800 градусах, а группа B закаливается при 860 градусах. Каков порядок их жесткости от высокой к низкой? Как упорядочить упрочненный слой (предел 550HV1.0) от глубокого к мелкому? Возьмите два испытательных прутка из одного материала и сравните и проверьте, какая группа может получить более высокую твердость при закалке и эффективную глубину закаленного слоя?
Можно ли сделать вывод из приведенных выше результатов испытаний, что глубина науглероженного слоя не равна глубине эффективного упрочненного слоя, а на фактическую глубину затвердевшего слоя влияют способность материала к упрочнению, температура закалки и охлаждение. показатель. Характеристики охлаждения и интенсивность закалки охлаждающей среды также влияют на закалочный эффект. Выше мнения людей, если есть какие-то неполноты, можете добавить. Конечно, размерный эффект деталей также влияет на эффект закалки.
Я думаю, что опытный инспектор может определить настоящую причину низкой твердости, организовав и комбинируя другие методы испытаний, а затем найти настоящую причину для ее устранения; как ремесленник, если вы знакомы с характеристиками обычного металлического сырья, охлаждающая способность его собственного оборудования и среды достигла определенного уровня признания, что очень помогает в разработке процессов науглероживания и закалки.
3. Неравномерная твердость: равномерная температура печи (влияющая на однородность науглероживания), конструкция оборудования, циркуляция атмосферы, загрузка печи (влияющая на однородность науглероживающего слоя и в то же время влияющая на однородность закалки).
4. Твердость сердечника не определена. Слишком высокая: температура закалки слишком высока, закаливаемость материала слишком хорошая, верхний предел состава углерода и сплава и средняя скорость охлаждения слишком высоки. Твердость сердцевины низкая: как раз наоборот.
Пример совместного использования: сталь 20 # 1.5 мм, требования: слой инфильтрации 0.2-0.4 мм сердцевина HV250, некоторые друзья в той же отрасли считают требования необоснованными (каждый должен знать, что самая высокая твердость мартенсита стальной плиты 20 # будет HV450- 470) Чтобы решить эту проблему, мы должны сначала понять характеристики этого материала: включая прокаливаемость и прокаливаемость.
Затем объедините вышеупомянутые факторы, влияющие на эффект закалки, и найдите способы нагрева и охлаждения. В этом случае материал фиксируется. Выход можно найти по температуре закалки и скорости охлаждения. Этот производитель использует масло для превышения скорости. Если снижение интенсивности закалки не соответствует требованиям, мы также можем снизить температуру закалки. Метод.
По-прежнему то же предложение, от 860-760 градусов (когда температура понижается до определенного уровня, определенное количество феррита будет выделено из переохлажденного аустенита в сердечнике, и твердость в это время снизится., Чем больше температура снижается, чем больше выделяется феррит, тем сильнее уменьшается твердость.
Напоминаем: необходимо полностью совмещать существующие условия оборудования и поднимать шум по поводу особого благоприятного показателя мелкой проницаемости.
3. Науглероженный слой или эффективный науглероженный слой глубже и мельче.
Как упоминалось ранее, глубина инфильтрационного слоя является комплексной функцией температуры, времени и концентрации углерода. Чтобы решить эту проблему, мы должны начать с температуры нагрева, скорости нагрева, времени выдержки, скорости охлаждения и контроля градиента концентрации углерода в углеродном слое. Чем выше температура, тем больше время и чем выше углеродный потенциал, тем глубже слой инфильтрации и наоборот.
Но на самом деле это гораздо больше, чем просто. Чтобы спроектировать процесс науглероживания, вы также должны учитывать оборудование, производительность печи, характеристики масла, металлографическую структуру, прокаливаемость материала, градиент концентрации углерода в науглероженном слое и скорость охлаждения. И многие другие факторы. Это можно проанализировать со ссылкой на предыдущую ситуацию с низкой твердостью и не будет подробно объяснять.
В-четвертых, металлографическая организация
Избыточный мартенсит: сырье имеет крупные зерна или не нормализовано, а температура науглероживания слишком высока. Решение: нормализация или многократная нормализация (рекомендуется, чтобы температура нормализации была на 20-30 градусов выше, чем температура науглероживания). Если возможно, рассмотрите науглероживание и медленное охлаждение, а затем повторный нагрев и закалку.
Чрезмерно паралимпийский: температура закалки слишком высока, содержание углерода в аустените слишком высокое (углеродный потенциал слишком высок). Решение: полная диффузия и позволяющие условия могут снизить температуру закалки, высокотемпературный отпуск, повторный нагрев и закалку или криогенную обработку.
Избыточный карбид: слишком высокое содержание углерода в аустените (слишком высокий углеродный потенциал), слишком медленный процесс охлаждения, выделение карбида
Решение: полностью рассеять, контролировать скорость охлаждения, уменьшить разницу температур между науглероживанием и закалкой, насколько это возможно, и как можно меньше использовать низкотемпературную или субтемпературную закалку. Если необходимо использовать этот процесс, необходимо контролировать загрузку печи. Представим: это же оборудование науглероживается при 920 ° C и закаливается при 820 ° C. Емкость печи составляет 1000 кг и 600 кг, а скорость охлаждения такая же? Какой займет больше времени? Какая марка карбида выше?
Пятерки. Ненародное и внутреннее окисление
Внутреннее окисление: это реакция между легирующими элементами, такими как хром, марганец и молибден в стали, и окислительной атмосферой в атмосфере (в основном кислородом, водой, диоксидом углерода), которая истощает легирующие элементы в матрице, что приводит к снижению в закаливаемости материала. Черную сетчатую структуру можно увидеть под микроскопом, ее суть - структура троостита, полученная за счет истощения легирующих элементов в матрице и снижения прокаливаемости.
Решение состоит в том, чтобы найти способы увеличить скорость охлаждения среды, увеличить интенсивность закалки и уменьшить окислительную атмосферу в печи (обеспечить чистоту науглероживающего сырья и вспомогательных материалов, минимизировать количество сбалансированного воздуха, контролировать сбалансированный содержание влаги в воздухе и убедитесь, что оборудование не протекает. Достаточная вытяжка) Обычное оборудование трудно устранить. Говорят, что можно полностью отказаться от оборудования для вакуумной науглероживания при низком давлении. Кроме того, мощная дробеструйная обработка также может снизить уровень внутреннего окисления.
Я читал мнения некоторых экспертов, и некоторые считают, что чрезмерное количество аммиака в процессе нитроцементации также может вызывать серьезные проблемы с отсутствием лошадиных сил. У меня лично на этот счет другое мнение: может быть, это связано с чрезмерным содержанием воды в аммиаке? Поскольку я подвергался воздействию многих процессов нитроцементации, при осмотре продукта не было обнаружено никаких явных тканей, отличных от лошади. (Но я не думаю, что эта точка зрения ошибочна). Некоторые зарубежные машиностроительные отрасли придают большое значение внутреннему окислению, особенно в зубчатой промышленности. Внутри страны обычно требуется, чтобы глубина не превышала 0.02 мм.
Немартенситный: немартенситная структура появляется на поверхности науглероженного слоя из-за проблем науглероживания или закалки после закалки, таких как феррит, бейнит и, конечно же, троостит типа внутреннего окисления. Механизм генерации аналогичен внутреннему окислению, и решение аналогично.
Шесть. Проблема деформации
Это системная проблема, а также самая большая проблема для наших сотрудников, занимающихся термообработкой. Это гарантируется несколькими аспектами охлаждающей среды процесса сырья. Приведенный выше контент - это только личный опыт. Если есть какие-то несоответствия, пожалуйста, поправьте меня, спасибо.
Сохраните источник и адрес этой статьи для перепечатки.:Сборник общих дефектов и профилактических мероприятий при науглероживании и закалке
Минхэ Компания по литью под давлением специализируются на производстве и предоставлении качественных и высокопроизводительных литых деталей (ассортимент металлических деталей для литья под давлением в основном включает Тонкостенное литье под давлением,Литье под давлением,Литье под давлением в холодной камере), Round Service (Служба литья под давлением,Обработка с ЧПУ,Изготовление пресс-форм, Обработка поверхности) .Любое индивидуальное литье под давлением из алюминия, магния или замака / цинка, а также другие требования к отливкам, пожалуйста, свяжитесь с нами.
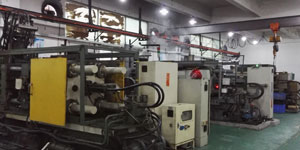
Под контролем ISO9001 и TS 16949, все процессы выполняются на сотнях передовых машин для литья под давлением, 5-осевых станках и других объектах, от струйных до стиральных машин Ultra Sonic. Minghe не только имеет современное оборудование, но и имеет профессиональное оборудование. команда опытных инженеров, операторов и инспекторов для воплощения в жизнь проекта заказчика.
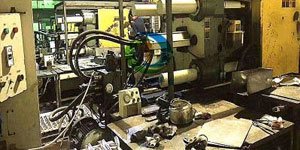
Контрактный производитель отливок под давлением. Возможности включают в себя детали для литья под давлением алюминия с холодной камерой весом от 0.15 фунта. до 6 фунтов, быстрая установка и обработка. Дополнительные услуги включают полировку, вибрацию, удаление заусенцев, дробеструйную очистку, окраску, гальванику, нанесение покрытий, сборку и оснастку. Обрабатываемые материалы включают такие сплавы, как 360, 380, 383 и 413.
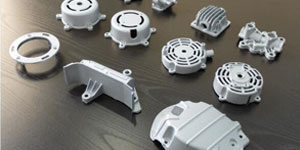
Помощь в проектировании литья цинка под давлением / сопутствующие инженерные услуги. Изготовление на заказ прецизионных отливок из цинка под давлением. Могут изготавливаться миниатюрные отливки, отливки под высоким давлением, отливки в формы с несколькими суппортами, отливки в обычные формы, единичные отливки под давлением и независимые отливки под давлением, а также отливки с герметизацией полости. Отливки могут изготавливаться длиной и шириной до 24 дюймов с допуском +/- 0.0005 дюйма.
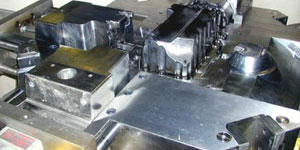
Производитель литья под давлением из магния, сертифицированный по стандарту ISO 9001: 2015. Возможности включают литье под давлением магния под высоким давлением с горячей камерой до 200 тонн и холодной камерой на 3000 тонн, проектирование инструментов, полировку, формование, механическую обработку, порошковую и жидкостную окраску, полный контроль качества с возможностями CMM , сборка, упаковка и доставка.
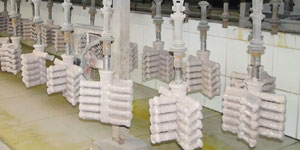
Сертифицирован ITAF16949. Дополнительные услуги трансляции включают инвестиционное литье,литье в песчаные формы,Гравитационное литье, Литье по выплавляемым моделям,Центробежное литье,Вакуумное литье,Постоянное литье формыВозможности включают EDI, техническую поддержку, твердотельное моделирование и вторичную обработку.
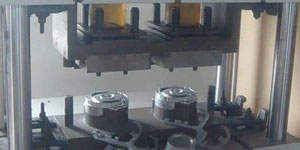
Литейная промышленность Примеры использования запчастей для: автомобилей, велосипедов, самолетов, музыкальных инструментов, судов, оптических устройств, датчиков, моделей, электронных устройств, корпусов, часов, машинного оборудования, двигателей, мебели, ювелирных изделий, приспособлений, телекоммуникаций, освещения, медицинских устройств, фотографических устройств, Роботы, скульптуры, звуковое оборудование, спортивное оборудование, инструменты, игрушки и многое другое.
Что мы можем вам сделать дальше?
∇ Перейти на главную страницу для Литье под давлением Китай
→Литье деталей-Узнай, что мы сделали.
→ Общие советы о Услуги литья под давлением
By Производитель литья под давлением Minghe | Категории: Полезные статьи |Материалы Теги: Литье алюминия, Цинковое литье, Литье магния, Титановое литье, Литье из нержавеющей стали, Латунное литье,Бронзовое литье,Кастинг видео,История компании,Литье алюминия под давлением | Комментарии отключены