Обсуждение процесса термообработки литейной формы из алюминиево-магниевого сплава
Использование упрочняющей обработки и процесса поверхностного упрочнения является важным производственным способом повышения производительности и срока службы пресс-формы. В данной статье анализируются характеристики пресс-формы в соответствии с условиями работы и требованиями к характеристикам пресс-форм для литья под давлением из алюминиево-магниевого сплава. термообработка и общие процессы в деталях, и указывает, что разумная формулировка спецификаций процесса термообработки может обеспечить твердость поверхности формы, износостойкость, прочность и ударную вязкость сердечника, а также предотвратить коррозию металла жидкостью. Приклеивание к форме может эффективно снизить процент брака и значительно увеличить срок службы формы.
Алюминиево-магниевые сплавы находят все более широкое применение из-за их низкой плотности и высокой прочности. Среди них технология литья под давлением из алюминиево-магниевого сплава, как усовершенствованный процесс резки, отличается высокой производительностью, экономией сырья, снижением производственных затрат, хорошими эксплуатационными характеристиками и высокой точностью. , В основном используемые в электронике, автомобилях, двигателях, бытовой технике и других отраслях промышленности, некоторые высокопроизводительные, высокоточные, высокопрочные высококачественные изделия из алюминиево-магниевого сплава также применялись в крупных самолетах, кораблях и других отраслях промышленности с относительно высокие технические требования.
Условия работы и эксплуатационные требования форм для литья под давлением из алюминиево-магниевого сплава
Форма для литья под давлением из алюминиево-магниевого сплава - это пресс-форма, используемая для литья под давлением отливок из алюминиево-магниевого сплава на машине для литья под давлением. Температура плавления алюминиевого сплава составляет 600 750 ℃, а температура плавления магниевого сплава составляет 600 700 ℃. Температура рабочей поверхности обычно может достигать 500 600 ℃. Поверхности полости, оправки и сопла подвергаются сильным колебаниям температуры, а поверхность формы склонна к трещинам от термической усталости. Кроме того, алюминиево-магниевый сплав легко прилипает к поверхности формы во время процесса литья под давлением, что влияет на непрерывную работу процесса литья под давлением. Жидкий алюминиево-магниевый сплав оказывает сильное эрозионное воздействие на поверхность формы. Следовательно, для изготовления форм для литья под давлением из алюминиево-магниевого сплава требуется, чтобы материал формы имел высокую стабильность при отпуске и устойчивость к холоду и тепловой усталости при температуре около 600 ° C, а также имел хорошую устойчивость к высоким температурам, высокому давлению, высокой скорости вращения и т. Д. и высокая эрозионная стойкость жидких алюминиево-магниевых сплавов. Прочность и ударная вязкость формы и в то же время правильная термообработка необходимы для раскрытия потенциала материала формы и увеличения срока ее службы. В настоящее время обычно используемые штамповые стали для литья под давлением из алюминиево-магниевого сплава при производстве пресс-форм включают: сталь 3Cr2W8V, сталь 4Cr5MoSiV1, сталь 4Cr3Mo3SiV, сталь 4Cr5MoSiV и сталь новых типов 4Cr5Mo2MnSiV1 и сталь 3Cr3Mo3VNb.
Технологический маршрут изготовления литейной формы из алюминиево-магниевого сплава
Процесс изготовления формы для литья под давлением из алюминиево-магниевого сплава: вырубка → ковка → сфероидизирующий отжиг → механическая обработка → закалка, отпуск → ремонт, шлифовка, полировка → азотирование (нитроцементация) → сборка и использование.
Процесс упрочнения и закалки литейной формы из алюминиево-магниевого сплава
Закалочная обработка формы для литья под давлением из алюминиево-магниевого сплава заключается в изменении структуры стали для получения требуемой структуры и характеристик формы. Термическая обработка должна основываться на материале пресс-формы, форме, размере и сложности пресс-формы для определения технических характеристик процесса термообработки.
3.1 Предварительная термообработка
Предварительная термообработка формы для литья под давлением может включать три процесса: непрерывный отжиг, изотермический отжиг, а также закалка и термообработка с отпуском. Цель состоит в том, чтобы получить однородную структуру и диспергированный карбид перед окончательной термообработкой для повышения прочности и ударной вязкости стали. Процесс непрерывного отжига относительно прост, и также может быть получена лучшая гранулированная перлитная структура. Для литейных форм сложной формы и высоких требований можно использовать изотермический отжиг для получения более идеальной гранулированной перлитной структуры.
3.2 Закалка и предварительный нагрев
Сталь для литья под давлением - это в основном высоколегированная сталь с плохой теплопроводностью. Во время закалки и нагрева часто предпринимаются меры по предварительному нагреву. Количество предварительных нагревов и температура зависят от состава штамповой стали и требований к деформации пресс-формы. Для форм с низкой температурой закалки, простой формой и низкими требованиями к деформации требуется предварительный нагрев (800 ~ 850 ℃) во время закалки и нагрева без образования трещин. Для пресс-форм с закалкой при более высоких температурах, сложных форм и высоких требований к деформации необходим вторичный предварительный нагрев (600-650 ° C, 800-850 ° C). Цель состоит в том, чтобы уменьшить напряжение, возникающее в процессе нагрева, и в то же время сделать общую структуру формы однородной.
3.3 Закалочный нагрев
Температуру нагрева при закалке кристаллизатора для литья под давлением можно установить в соответствии со спецификацией нагрева при закалке для каждой марки стали. Например, температура закалки стали 3Cr2W8V составляет 1050 ~ 1150 ℃, а температура закалки стали H13 составляет 1020 ~ 1100 ℃. Повышение температуры закалки двух сталей может повысить жаропрочность и сопротивление термической усталости формы для литья под давлением, но это увеличит деформацию формы. При нагревании в печи с соляной ванной, чтобы избежать окислительного обезуглероживания на поверхности формы, следует использовать солевую ванну с хлоридом бария с хорошим раскислением, и раскисление следует проводить часто. При нагреве в печи сопротивления коробчатого типа следует соблюдать защитную атмосферу; или нагрев в обычной печи сопротивления коробчатого типа после упаковки. Для обеспечения полного растворения карбидов, получения однородного аустенита и получения хороших высокотемпературных характеристик время выдержки при закалке и нагреве форм для литья под давлением должно быть соответствующим образом увеличено. Обычно коэффициент выдержки тепла в печи с соляной ванной составляет 0.8-1.0 мин / мм.
3.4 Закалочное охлаждение
Скорость закалки в масле высокая, и могут быть получены хорошие характеристики, но тенденция к деформации и растрескиванию велика. Как правило, используются формы для литья под давлением с масляным охлаждением простой формы и с низкими требованиями к деформации; Для литейных форм сложной формы и высоких требований к деформации следует использовать иерархическую закалку, чтобы предотвратить деформацию формы и растрескивание. Закалочное охлаждение должно быть как можно более медленным, чтобы уменьшить закалочную деформацию, нагрев и закалку в вакуумной печи сопротивления, охлаждение может быть принято газовой закалкой. При охлаждении можно применять нагрев и закалку в соляной ванне, а также постепенную закалку. Когда форма закаливается и охлаждается, ее обычно охлаждают до 150–200 ℃, а затем сразу после замачивания закаляют. Не допускается охлаждение до комнатной температуры.
3.5 Темперирование
Твердость формы для литья под давлением достигается за счет отпуска, а твердость полости формы для литья под давлением напрямую влияет на усталостную долговечность формы при горячих и низких температурах. Разные материалы, разная температура закалки и температура отпуска также различаются. Например, твердость формы для литья под давлением из стали 3Cr2W8V из алюминиево-магниевого сплава обычно составляет 42 ~ 48HRC, а ее температура отпуска обычно выбирается между 560 ~ 620 ℃, но если используется высокотемпературная закалка, температура отпуска достигает 670 ℃. Твердость после закалки при 1150 ° C и отпуска при 650 ° C составляет 45HRC; в то время как твердость после закалки при 1050 ° C и отпуска при 650 ° C составляет 35HRC. Твердость формы для литья под давлением из алюминиево-магниевого сплава из стали H13 должна составлять 44 ~ 50HRC. Пик вторичного упрочнения стали H13 появляется при отпуске при 500 ℃, но размер пика зависит от температуры закалки. Температура отпуска обычно составляет 560 ~ 620 ℃. Закаливание следует проводить 2–3 раза. Температура первого отпуска может быть ниже. После первого отпуска измерьте твердость. Если требования к твердости достигнуты, температуру отпуска следует снизить на 20 30 ℃, чтобы избежать снижения твердости. Если твердость слишком высока, отрегулируйте температуру отпуска соответствующим образом, чтобы удовлетворить требованиям твердости в соответствии с высокой твердостью. Третий отпуск предназначен для повышения прочности, температура отпуска должна быть выше, чем во втором.
Температура вторичного отпуска на 30 ~ 50 ℃ ниже. Время отпуска и выдержки должно быть достаточным для устранения напряжения, возникающего во время закалки, и уменьшения образования трещин в форме. Время выдержки для каждого отпуска составляет 2 часа, и время выдержки для больших форм соответственно увеличивается. Из-за высокого термического напряжения и микроструктурного напряжения штампа для литья под давлением после закалки штамп обычно отпускают сразу после охлаждения до 150-200 ° C.
Процесс упрочнения поверхности формы для литья под давлением из алюминиево-магниевого сплава
После закалки и отпуска твердость поверхности штампа для литья под давлением из алюминиево-магниевого сплава не очень высока. Для получения высокой твердости и износостойкости на поверхности формы, в то время как основная часть по-прежнему сохраняет достаточную прочность и ударную вязкость, а также для улучшения характеристик предотвращения прилипания формы для литья под давлением из алюминиево-магниевого сплава, азотирование поверхности или азотирование можно выполнить на пресс-форме. Науглероживание.
4.1 Азотирование
Азотирование - это процесс термической обработки азотирования поверхности стали для увеличения концентрации азота в поверхностном слое. Целью азотирования является уменьшение деформации деталей пресс-формы, повышение твердости поверхности, износостойкости, усталостной прочности и сопротивления заеданию литейных форм из алюминиево-магниевого сплава, повышение коррозионной стойкости пресс-формы по отношению к атмосфере и перегретому пару, и улучшить устойчивость к отпуску и размягчению. Notch чувствительность. Твердое азотирование, жидкое азотирование и газовое азотирование являются распространенными методами азотирования. Новые технологии, такие как ионное азотирование, вакуумное азотирование, электролитическое азотирование и высокочастотное азотирование, позволяют значительно сократить цикл азотирования, получить качественный слой азотирования и повысить экономическую эффективность предприятий, поэтому они широко используются в производстве.
4.2 Нитроцементация
Нитроцементация - это аммиак плюс спиртовые жидкости (метанол, этанол) и совместно проникающие среды, такие как мочевина, формиловый клей и триэтанольный клей. Реакция термического разложения происходит при определенной температуре с образованием активных атомов азота и углерода, которые отливаются под давлением из алюминиево-магниевых сплавов. После впитывания поверхности формы она диффундирует и проникает в поверхностный слой формы для получения нитроцементационного слоя на основе азота, благодаря чему форма приобретает более высокую твердость поверхности, сопротивление усталости, износостойкость и коррозионную стойкость. Методы нитроцементации включают жидкие и газовые методы, и большинство методов, используемых в производстве, представляют собой газовую нитроцементацию. Форма для литья под давлением из алюминиевого сплава стали H13 нагревается в две стадии предварительной термообработки при 550 ℃ × 40 мин и 850 ℃ × 40 мин в высокотемпературной печи с соляной ванной, закалена при 1030 ℃, отпущена при 600 ℃, а затем подвергнута обработке. на газовую нитроцементацию при 580 ℃. Твердость выше 900HV, твердость матрицы 46 ~ 48HRC, износостойкость, сопротивление усталости и коррозионная стойкость пресс-формы значительно улучшены, а также отсутствует адгезия, отслаивание, царапины и коррозия, что эффективно увеличивает срок службы пресс-формы. плесень.
Заключение
В качестве важного технологического оборудования формы для литья под давлением из алюминиево-магниевого сплава напрямую влияют на качество продукции и экономические выгоды компании. Исследования и статистика показывают, что отказы пресс-формы из-за неправильного процесса термообработки составляют около 50% от общего числа отказов. Таким образом, разумный выбор процессов упрочнения и упрочнения и поверхностного упрочнения, а также строгий контроль технических характеристик процесса термообработки являются важными способами улучшения характеристик и срока службы пресс-форм. При производстве пресс-форм для литья под давлением из алюминиево-магниевого сплава необходимо анализировать и изучать причины отказов в соответствии с условиями работы пресс-формы и разумно формулировать процессы термообработки, чтобы обеспечить твердость поверхности пресс-формы, износостойкость, прочность и ударную вязкость сердечника, предотвратить появление металла. жидкая коррозия и прилипание формы, а также эффективно снижают процент брака, значительно увеличивают срок службы формы.
Сохраните источник и адрес этой статьи для перепечатки.: Обсуждение процесса термообработки литейной формы из алюминиево-магниевого сплава
Минхэ Компания по литью под давлением специализируются на производстве и предоставлении качественных и высокопроизводительных литых деталей (ассортимент металлических деталей для литья под давлением в основном включает Тонкостенное литье под давлением,Литье под давлением,Литье под давлением в холодной камере), Round Service (Служба литья под давлением,Обработка с ЧПУ,Изготовление пресс-форм, Обработка поверхности) .Любое индивидуальное литье под давлением из алюминия, магния или замака / цинка, а также другие требования к отливкам, пожалуйста, свяжитесь с нами.
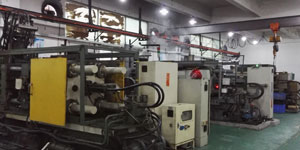
Под контролем ISO9001 и TS 16949, все процессы выполняются на сотнях передовых машин для литья под давлением, 5-осевых станках и других объектах, от струйных до стиральных машин Ultra Sonic. Minghe не только имеет современное оборудование, но и имеет профессиональное оборудование. команда опытных инженеров, операторов и инспекторов для воплощения в жизнь проекта заказчика.
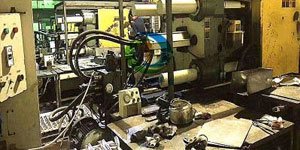
Контрактный производитель отливок под давлением. Возможности включают в себя детали для литья под давлением алюминия с холодной камерой весом от 0.15 фунта. до 6 фунтов, быстрая установка и обработка. Дополнительные услуги включают полировку, вибрацию, удаление заусенцев, дробеструйную очистку, окраску, гальванику, нанесение покрытий, сборку и оснастку. Обрабатываемые материалы включают такие сплавы, как 360, 380, 383 и 413.
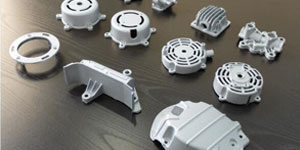
Помощь в проектировании литья цинка под давлением / сопутствующие инженерные услуги. Изготовление на заказ прецизионных отливок из цинка под давлением. Могут изготавливаться миниатюрные отливки, отливки под высоким давлением, отливки в формы с несколькими суппортами, отливки в обычные формы, единичные отливки под давлением и независимые отливки под давлением, а также отливки с герметизацией полости. Отливки могут изготавливаться длиной и шириной до 24 дюймов с допуском +/- 0.0005 дюйма.
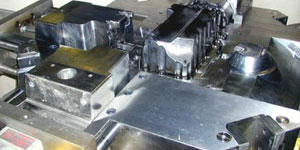
Производитель литья под давлением из магния, сертифицированный по стандарту ISO 9001: 2015. Возможности включают литье под давлением магния под высоким давлением с горячей камерой до 200 тонн и холодной камерой на 3000 тонн, проектирование инструментов, полировку, формование, механическую обработку, порошковую и жидкостную окраску, полный контроль качества с возможностями CMM , сборка, упаковка и доставка.
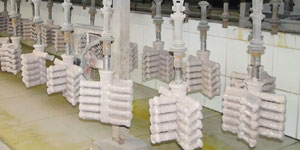
Сертифицирован ITAF16949. Дополнительные услуги трансляции включают инвестиционное литье,литье в песчаные формы,Гравитационное литье, Литье по выплавляемым моделям,Центробежное литье,Вакуумное литье,Постоянное литье формыВозможности включают EDI, техническую поддержку, твердотельное моделирование и вторичную обработку.
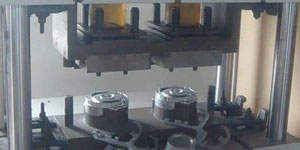
Литейная промышленность Примеры использования запчастей для: автомобилей, велосипедов, самолетов, музыкальных инструментов, судов, оптических устройств, датчиков, моделей, электронных устройств, корпусов, часов, машинного оборудования, двигателей, мебели, ювелирных изделий, приспособлений, телекоммуникаций, освещения, медицинских устройств, фотографических устройств, Роботы, скульптуры, звуковое оборудование, спортивное оборудование, инструменты, игрушки и многое другое.
Что мы можем вам сделать дальше?
∇ Перейти на главную страницу для Литье под давлением Китай
→Литье деталей-Узнай, что мы сделали.
→ Общие советы о Услуги литья под давлением
By Производитель литья под давлением Minghe | Категории: Полезные статьи |Материалы Теги: Литье алюминия, Цинковое литье, Литье магния, Титановое литье, Литье из нержавеющей стали, Латунное литье,Бронзовое литье,Кастинг видео,История компании,Литье алюминия под давлением | Комментарии отключены