Процесс термической обработки деталей пресс-формы
В качестве пластиковых форм используются разные типы стали, их химический состав и механические свойства различаются, поэтому технологические маршруты производства различаются; Точно так же для различных типов сталей для форм для пластика используются разные процессы термообработки. Этот раздел в основном знакомит с технологическим процессом производства и характеристиками процесса термообработки пластиковой формы.
1. Технологический маршрут изготовления пластиковых форм.
1. Формы для низкоуглеродистой стали и низкоуглеродистой легированной стали.
Например, технологический маршрут для сталей 20, 20Cr, 20CrMnTi и других сталей: вырубка → ковка штамповой заготовки → отжиг → механическая черновая обработка → формование методом холодного экструзии → рекристаллизационный отжиг → механическая чистовая обработка → науглероживание → закалка, отпуск → шлифование и полировка → сборка .
2. Форма из высоколегированной науглероженной стали.
Например, технологический маршрут стали 12CrNi3A и 12CrNi4A: вырубка → ковка штамповой заготовки → нормализация и высокотемпературный отпуск → механическая черновая обработка → высокотемпературный отпуск → чистовая обработка → науглероживание → закалка и отпуск → шлифовка и полировка → сборка.
3. Форма из закаленной и отпущенной стали.
Например, процесс производства сталей 45, 40Cr и других сталей: вырубка → ковка штамповых заготовок → отжиг → механическая черновая обработка → отпуск и отпуск → механическая чистовая обработка → правка, полировка → сборка.
4. Формы для углеродистой инструментальной стали и легированной инструментальной стали.
Например, технологический маршрут T7A, T10A, CrWMn, 9SiCr и других сталей: вырубка → штамповка в штамп → сфероидизирующий отжиг → механическая черновая обработка → отжиг для снятия напряжений → механическая получистовая обработка → механическая чистовая обработка → закалка, отпуск → шлифование. Полировка → сборка.
5. Предварительно закаленная стальная форма.
Например, 5NiSiCa, 3Cr2Mo (P20) и другие стали. Для тех, которые непосредственно обрабатываются прутковыми заготовками, они предварительно закалены в соответствии с состоянием поставки, и их можно напрямую обрабатывать и формовать, а затем полировать и собирать. Для тех, которые необходимо выковать в заготовки, а затем обработать для формирования, технологический маршрут следующий: вырубка → ковка → сфероидизирующий отжиг → строгание или фрезерование шести сторон → предварительная закалка (34 ~ 42HRC) → механическая черновая обработка → отжиг для снятия напряжения → Механическая обработка → полировка → сборка.
Характеристики термообработки пластиковых форм
(1) Характеристики термообработки науглероженной стальной пластмассовой формы
- Для пластиковых форм с высокой твердостью, высокой износостойкостью и высокими требованиями к вязкости следует использовать науглероженную сталь для изготовления, а науглероживание, закалка и низкотемпературный отпуск являются окончательной термообработкой.
- Требования к науглероженному слою, обычно толщина науглероженного слоя составляет 0.8 ~ 1.5 мм, при прессовании пластмасс, содержащих твердые наполнители, толщина науглероженного слоя формы должна составлять 1.3 ~ 1.5 мм, при прессовании мягких пластиков науглероженный слой Толщина 0.8 ~ 1.2 мм. Содержание углерода в науглероженном слое предпочтительно составляет от 0.7% до 1.0%. Если используется совместная инфильтрация углерода и азота, износостойкость, коррозионная стойкость, стойкость к окислению и антипригарные свойства будут лучше.
- Температура науглероживания обычно составляет 900 920 ℃, а небольшие формы со сложными полостями могут выдерживать среднетемпературное карбонитрирование 840 ~ 860 ℃. Время сохранения тепла науглероживания составляет 5-10 часов, которое следует выбирать в соответствии с требованиями к толщине науглероженного слоя. Процесс науглероживания подходит для применения иерархического процесса науглероживания, то есть высокотемпературная стадия (900 920 ℃) в основном предназначена для быстрого проникновения на поверхность детали; стадия средней температуры (820 ~ 840 ℃) в основном предназначена для увеличения толщины науглероженного слоя. В науглероженном слое устанавливается равномерное и разумное распределение градиента концентрации углерода, что удобно для прямой закалки.
- Процесс закалки после науглероживания различается в зависимости от типа стали. После науглероживания его можно использовать отдельно: повторный нагрев и закалка; прямая закалка после градуированной науглероживания (например, легированная науглероженная сталь); прямая закалка после среднетемпературного нитроцементации (например, в промышленных малых прецизионных формах, полученных путем холодной экструзии чистого железа или низкоуглеродистой стали); закалка на воздухе после науглероживания (например, в больших и средних формах из высоколегированной науглероженной стали).
(2) Термическая обработка закаленной стальной пластмассовой формы.
- Для форм более сложной формы термообработку следует проводить после черновой обработки, а затем - финишной обработки, чтобы обеспечить наименьшую деформацию во время термообработки. Для прецизионных форм деформация должна быть менее 0.05%.
- Требования к поверхности полости пластиковой формы очень строгие, поэтому во время процесса закалки и нагрева необходимо следить за тем, чтобы поверхность полости не окислялась, не обезуглероживалась, не корродировала, не перегревалась и т.д. в печи с защитной атмосферой или в печи с соляной баней после строгого раскисления. Если для нагрева используется обычная печь сопротивления коробчатого типа, на поверхность полости формы следует нанести защитное средство и контролировать скорость нагрева. Охлаждающая среда, контролируйте скорость охлаждения, чтобы избежать деформации, растрескивания и брака во время процесса закалки. Как правило, закалка в горячей ванне лучше, также можно использовать закалку с предварительным охлаждением.
- После закалки его следует вовремя отпустить, температура отпуска должна быть выше, чем рабочая температура формы, а время отпуска должно быть достаточным. Длина зависит от материала формы и размера секции, но не менее 40-60 минут.
(3) Термическая обработка предварительно закаленной стальной пластмассовой формы.
- Предварительно закаленная сталь поставляется в предварительно закаленном состоянии и, как правило, не требует термической обработки, но иногда требуется модифицированная ковка, а заготовка штампа после модифицированной ковки должна подвергаться термообработке.
- Для предварительной термообработки предварительно закаленной стали обычно используется сфероидизирующий отжиг, цель которого состоит в том, чтобы устранить напряжение ковки, получить однородную сферическую перлитную структуру, снизить твердость, повысить пластичность и улучшить характеристики резки или формовки заготовки методом холодной экструзии.
- Процесс предварительного упрочнения предварительно закаленной стали прост, в большинстве случаев применяется закалка и отпуск, а структура отпущенного сорбита получается после закалки и отпуска. Высокотемпературный отпуск имеет широкий диапазон температур, что позволяет удовлетворить различные требования к твердости пресс-формы. Благодаря хорошей закаливаемости такой стали во время закалки можно использовать охлаждение маслом, воздушное охлаждение или нитратно-солевую закалку. В таблице 3-27 для справки показан процесс предварительной закалки некоторых предварительно закаленных сталей.
Стальной номер | Температура нагрева / ℃ | метод охлаждения | Температура отпуска / ℃ | Предварительно закаленная твердость: HRC |
3Cr2Mo | 830 ~ 840 | Масляное охлаждение или классификация нитратов 160 ~ 180 ℃ | 580 ~ 650 | 28 ~ 36 |
5НиСКа | 880 ~ 930 | Масляный радиатор | 550 ~ 680 | 30 ~ 45 |
8Cr2MnWMoVS | 860 ~ 900 | Масляное или воздушное охлаждение | 550 ~ 620 | 42 ~ 48 |
P4410 | 830 ~ 860 | Масляное охлаждение или классификация нитратов | 550 ~ 650 | 35 ~ 41 |
SM1 | 830 ~ 850 | Масляный радиатор | 620 ~ 660 | 36 ~ 42 |
(4) Термическая обработка стальной пластиковой формы для старения.
- Процесс термообработки стали, упрочняющейся старением, делится на два основных этапа. Сначала проводится обработка на твердый раствор, то есть сталь нагревается до высокой температуры для растворения различных легирующих элементов в аустените, а после того, как аустенит завершен, мартенситная структура получается закалкой. Второй этап - это обработка старением, и старение используется для усиления механических свойств, которые соответствуют конечным требованиям.
- Нагревание при обработке раствора обычно осуществляется в печи с соляной ванной или коробчатой печи. Время нагрева может составлять соответственно: 1 мин / мм, 2 ~ 2.5 мин / мм, при закалке используется масляное охлаждение, а сталь с хорошей закаливаемой способностью также может охлаждаться воздухом. Если при ковке заготовки штампа можно точно контролировать конечную температуру ковки, закалку в растворе можно проводить непосредственно после ковки.
- Обработку старением лучше всего проводить в вакуумной печи. Если это осуществляется в коробчатой печи, то для предотвращения окисления поверхности полости кристаллизатора в печь должна быть пропущена защитная атмосфера, либо в печи следует использовать порошок оксида алюминия, порошок графита, отходы чугуна. коробка. Старение в защитных условиях. Нагрев защиты упаковки должен соответствующим образом продлить время сохранения тепла, в противном случае будет трудно добиться эффекта старения. Спецификации термической обработки частично твердеющей пластмассовой стали для литейных форм можно найти в Таблице 3-28.
Стальной номер | Процесс обработки раствора | Процесс лечения старения | Жесткость при старенииHRC |
06Ni6CrMoVTiAl | 800 ~ 850 ℃ Масляный радиатор | 510 ~ 530 ℃ × (6 ~ 8) ч | 43 ~ 48 |
PMS | 800 ~ 850 ℃ Воздушное охлаждение | 510 ~ 530 ℃ × (3 ~ 5) ч | 41 ~ 43 |
25CrNi3MoAl | 880 ℃ Закалка в воде или охлаждение на воздухе | 520 ~ 540 ℃ × (6 ~ 8) ч | 39 ~ 42 |
SM2 | 900 ℃ × 2 часа Маслоохладитель + 700 ℃ × 2 часа | 510 ℃ × 10 ч | 39 ~ 40 |
ПЦР | 1050 ℃ Воздушное охлаждение твердого раствора | 460 ~ 480 ℃ × 4 ч | 42 ~ 44 |
Обработка поверхности пластиковых форм
Чтобы улучшить износостойкость и коррозионную стойкость поверхности пластмассовой формы, ее часто подвергают соответствующей обработке.
- Хромирование пластиковых форм - один из самых распространенных методов обработки поверхности. Слой хромирования обладает сильной пассивирующей способностью в атмосфере, может сохранять металлический блеск в течение длительного времени и не вступает в химические реакции в различных кислых средах. Твердость покрытия достигает 1000HV, поэтому оно обладает отличной износостойкостью. Хромированный слой также обладает высокой термостойкостью, а его внешний вид и твердость остаются неизменными при нагревании до 500 ° C на воздухе.
- Азотирование имеет преимущества низкой температуры обработки (обычно 550 570 ℃), небольшой деформации формы и высокой твердости пропитанного слоя (до 1000 1200HV), поэтому он также очень подходит для обработки поверхности пластиковых форм. Марки стали, содержащие легирующие элементы, такие как хром, молибден, алюминий, ванадий и титан, обладают лучшими характеристиками азотирования, чем углеродистая сталь. Обработка азотом при использовании в качестве пластмассовой формы может значительно улучшить износостойкость.
Методы обработки поверхности, подходящие для пластиковых форм, включают: нитроцементацию, химическое никелирование, ионное покрытие нитридом титана, карбид титана или карбонитрид титана, PVD, осаждение методом CVD твердой пленки или сверхтвердой пленки и т. Д.
Сохраните источник и адрес этой статьи для перепечатки.:Процесс термической обработки деталей пресс-формы
Минхэ Компания по литью под давлением специализируются на производстве и предоставлении качественных и высокопроизводительных литых деталей (ассортимент металлических деталей для литья под давлением в основном включает Тонкостенное литье под давлением,Литье под давлением,Литье под давлением в холодной камере), Round Service (Служба литья под давлением,Обработка с ЧПУ,Изготовление пресс-форм, Обработка поверхности) .Любое индивидуальное литье под давлением из алюминия, магния или замака / цинка, а также другие требования к отливкам, пожалуйста, свяжитесь с нами.
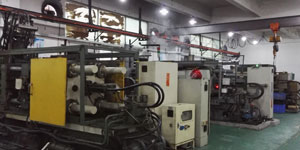
Под контролем ISO9001 и TS 16949, все процессы выполняются на сотнях передовых машин для литья под давлением, 5-осевых станках и других объектах, от струйных до стиральных машин Ultra Sonic. Minghe не только имеет современное оборудование, но и имеет профессиональное оборудование. команда опытных инженеров, операторов и инспекторов для воплощения в жизнь проекта заказчика.
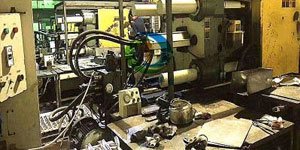
Контрактный производитель отливок под давлением. Возможности включают в себя детали для литья под давлением алюминия с холодной камерой весом от 0.15 фунта. до 6 фунтов, быстрая установка и обработка. Дополнительные услуги включают полировку, вибрацию, удаление заусенцев, дробеструйную очистку, окраску, гальванику, нанесение покрытий, сборку и оснастку. Обрабатываемые материалы включают такие сплавы, как 360, 380, 383 и 413.
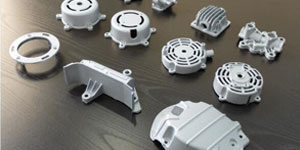
Помощь в проектировании литья цинка под давлением / сопутствующие инженерные услуги. Изготовление на заказ прецизионных отливок из цинка под давлением. Могут изготавливаться миниатюрные отливки, отливки под высоким давлением, отливки в формы с несколькими суппортами, отливки в обычные формы, единичные отливки под давлением и независимые отливки под давлением, а также отливки с герметизацией полости. Отливки могут изготавливаться длиной и шириной до 24 дюймов с допуском +/- 0.0005 дюйма.
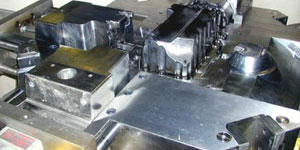
Производитель литья под давлением из магния, сертифицированный по стандарту ISO 9001: 2015. Возможности включают литье под давлением магния под высоким давлением с горячей камерой до 200 тонн и холодной камерой на 3000 тонн, проектирование инструментов, полировку, формование, механическую обработку, порошковую и жидкостную окраску, полный контроль качества с возможностями CMM , сборка, упаковка и доставка.
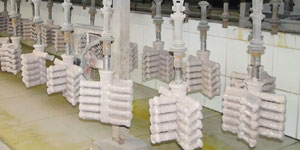
Сертифицирован ITAF16949. Дополнительные услуги трансляции включают инвестиционное литье,литье в песчаные формы,Гравитационное литье, Литье по выплавляемым моделям,Центробежное литье,Вакуумное литье,Постоянное литье формыВозможности включают EDI, техническую поддержку, твердотельное моделирование и вторичную обработку.
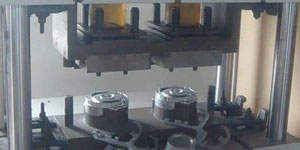
Литейная промышленность Примеры использования запчастей для: автомобилей, велосипедов, самолетов, музыкальных инструментов, судов, оптических устройств, датчиков, моделей, электронных устройств, корпусов, часов, машинного оборудования, двигателей, мебели, ювелирных изделий, приспособлений, телекоммуникаций, освещения, медицинских устройств, фотографических устройств, Роботы, скульптуры, звуковое оборудование, спортивное оборудование, инструменты, игрушки и многое другое.
Что мы можем вам сделать дальше?
∇ Перейти на главную страницу для Литье под давлением Китай
→Литье деталей-Узнай, что мы сделали.
→ Общие советы о Услуги литья под давлением
By Производитель литья под давлением Minghe | Категории: Полезные статьи |Материалы Теги: Литье алюминия, Цинковое литье, Литье магния, Титановое литье, Литье из нержавеющей стали, Латунное литье,Бронзовое литье,Кастинг видео,История компании,Литье алюминия под давлением | Комментарии отключены