Контроль качества при закалке отходами тепла после ковки
Страны во всем мире решительно выступают за политику сокращения выбросов и потребления: многие отечественные ученые и компании приняли меры с разных сторон, и гашение отходящего тепла после ковки является одной из важных мер.
Закалка остаточным теплом после ковки - это высокотемпературная термомеханическая термообработка в термомеханической термообработке. Данные [1, 2, 3] имеют конкретные описания. До сих пор многие отечественные производители использовали закалку отходящим теплом после ковки, а некоторые производители запустили → демонтированные → повторно установленные или смонтированные → демонтированные → продолжающие демонтаж из-за плохих мер контроля качества.
По сравнению с обычной термообработкой, из-за высокотемпературного нагрева и деформации отливки, мартенситная малоугловая граница зерен стали увеличивается, плотность дислокаций увеличивается, исходный водород частично уходит, исходные трещины залечиваются и уменьшаются, а карбиды диспергируются и осаждаются. Твердость стальных деталей при закалке значительно улучшилась (обычно примерно на 10%). Во время отпуска стальные детали обладают высокой стойкостью к отпуску (температура отпуска улучшена по сравнению с обычными деталями, обычно 20 ℃ -30 ℃).
- 1. Когда мы по разным причинам пошли на установку для термообработки, многие инженеры и технический персонал предположили, что сырье и другие аспекты хороши, как предсказать явление разрушения при закалке, посмотрев друг на друга? Это сводка трех основных эффектов (эти три основных эффекта также имеют эталонное значение для водородного охрупчивания и коррозионного разрушения под напряжением в процессе обработки поверхности).
- 1.1 Влияние химического состава: Например: углеродистая сталь: тот же размер ф6, та же закалка в соленой воде: сталь 35, сталь 40, сталь 45, сталь 50, сталь 55, сталь 60, сталь 65, в результате получается, что сталь 45 ~ сталь 60 легко ломается. Поскольку чем выше содержание углерода в мартенсите, тем больше напряжение, а максимальное содержание углерода составляет около 0.6%. Когда содержание углерода в стали очень высокое, оно будет более 0.6%, и будет образовываться остаточный A, который замедляет избирательное снятие мартенситного напряжения и его нелегко сломать. Вообще говоря: легированная сталь наиболее уязвима к закалке и растрескиванию. Например: 42CrM. При большом размере ф100 закалочная вода не трескается. Это размерный эффект, описанный ниже.
- 1.2 Размерный эффект: Например: сталь 45: ф1, ф2, ф3 ...... Результаты закалки ф10 показали, что закалка ф6 является наиболее вероятной. Поскольку ниже ф6, его обычно можно закалить до мартенсита. Однако общее превращение ф6 в мартенсит имеет наибольшее напряжение, поэтому его легче всего сломать. Причина та же: максимальное общее напряжение легированной стали - это показатель прокаливаемости (прокаливаемость - половина мартенсита), который составляет около 2/3. . Поэтому сначала проверьте индекс прокаливаемости определенной легированной стали, а затем посмотрите на заготовку. Какой самый опасный размер?
- 1.3 Эффект формы: резкое изменение поперечного сечения, слишком маленький угол R, выступающие соседние острые углы, глубокие канавки на краях, пробивка и маркировка острых краев, глухие отверстия, нижние отверстия, портальные отверстия, неправильное расстояние между отверстиями и различные размеры отверстий Асимметрия площади поперечного сечения и т. Д.
- 2. Выбор температуры предварительного охлаждения: Всем известно, что зерна мартенситной структуры при прямой закалке без предварительного охлаждения после ковки меньше. Оно может соответствовать текущим внутренним требованиям общего металлографического стандарта, и его характеристики также хорошие, но для больших и сложных деталей закалочное масло не может соответствовать требованиям, закалка водой или водной закалочной средой легко вызовет растрескивание. Это закалочное масло, чтобы предотвратить загрязнение и сократить расходы, его следует по возможности заменить на закалочную среду на водной основе; 42CrM в сборке тяжелых грузовиков Steyr, производимой компанией в Чунцине. Стали; Поковки балки переднего моста и балансирного вала, определенный технический персонал компании в одностороннем порядке изменил предварительное охлаждение с ≈800 ℃ на ≥850 ℃ для прямой закалки, что вызвало около 80% крупных закалочных трещин. Конечно, причина разрушения была проанализирована, и содержание B в сырье достигло 0.0022% от отчета об инспекции Chongqing Construction Group, а группа Changan Юго-Западного центра физико-химической инспекции Министерства вооружений сообщила. 0.0042%. Примечание: (1). Национальный военный стандарт GJB2720-1996, стандарт содержания бора в борсодержащей стали составляет 0.0005 ~ 0.0035%; (2). Технические условия золотосодержащей конструкционной стали GB3077-88 Норма содержания бора борсодержащей стали составляет 0.0005 ~ 0.0035%. Сегрегация полос до уровня I ... также является одной из причин. Проблема сильной зональной сегрегации сырья, достигающей уровня I, является важным фактором для трещин (более сильная сегрегация вызывает неравномерный химический состав и распределение закалочных напряжений при термообработке, что легко вызвать закалочные трещины);
Использование рентгеновского анализа энергетического спектра: границы зерен и матрица в структуре подготовленного металлографического образца были проанализированы качественно и полуколичественно с помощью анализатора рентгеновского энергетического спектра Vantage. Результаты анализа показаны на Рисунке 1, Рисунке 2 и Таблице 1.
Однако другая печная сталь имеет высокое содержание бора и большую сегрегацию. Концентрация ПАГ регулируется снижением температуры предварительного охлаждения, поэтому трещин не возникает.
Выбор температуры предварительного охлаждения: Прежде всего, в соответствии с тремя упомянутыми выше эффектами, определите наиболее уязвимую часть. Параметры процесса следует соответствующим образом отрегулировать. Например:
- (1) «Над балкой переднего моста» 42CrM. Мы предварительно охлаждаем ≈800 ℃, чтобы погасить PAG, и легко контролировать HRC на уровне 48-52.
- (2) Крупный завод по производству коленчатых валов мотоциклов в Чунцине: применяет метод очереди и предварительного охлаждения после ковки для достижения предварительного охлаждения ≈770 ℃ для закалки PAG, а также использует подъемный механизм с сетчатым ремнем, чтобы оставить поверхность жидкости без холода и холода. слегка самозакаливающийся. После вырубки температура предварительного охлаждения для стали 45 и 40Cr аналогична, но концентрация PAG отличается.
- (3) Завод по производству коленчатых валов в Чунцине: использует устройство, которое входит в печь с постоянной температурой после ковки, чтобы поддерживать его предварительное охлаждение до ≈770 ℃ и закаливать в раствор на водной основе ...
Выбор закалочной среды: основан на последних мировых исследованиях, так называемый эффект твердой оболочки. Требования: Первая скорость вращения перлита должна быть быстрой, чтобы образовался эффект твердой оболочки с сжимающим напряжением. Мартенсит вращается медленно, поэтому возникновение трещин затруднено, и ряд результатов исследований, таких как использование программного управления струйным охлаждением для управления скоростью, заслуживают популяризации и применения.
Разработанные нами закалочные жидкости PAG-A и PAG-ⅢB основаны на острой необходимости в новом типе скорости перлитного превращения, подобной соленой и щелочной воде, и скорости мартенситного превращения, подобной маслу, которая действительно заменяет закалку в воде и масло. охлаждение. Закалочная жидкость и антикоррозионная способность сохраняется более 5 дней. Чтобы перлит изменился подобно соленой и щелочной воде, пузырьковая пленка, образующаяся, когда закалка входит в жидкость, должна быть быстро разорвана, чтобы скорость охлаждения увеличилась. Например, при концентрации 3% первая скорость охлаждения не так хороша, как рассол и щелочная вода, то есть для удовлетворения вышеуказанных требований необходимо добавить одну или несколько смешанных добавок. Фактически, концентрация PAG-A достигает первой скорости быстрее, чем вода и поливиниловый спирт, а вторая скорость медленнее, чем у других производителей при той же концентрации PAG ....... При науглероживании и закалке сетки ленточные печи: PAG-A был разработан и применяется во многих сферах ... В настоящее время в стране используется более 20 ленточных печей с сеткой; цементация в печи с сетчатым ремнем решает проблему мягких участков, недостаточной твердости, большой деформации ...…. Антикоррозионная способность составляет более 5 дней, а расход ПАГ снижается на 20%.
В Чунцине действует 6 приложений PAG-ⅢA. Поскольку некоторые производители используют эту модель, некоторые специальные продукты решают проблемы, которые трудно решить с помощью других носителей, и производительность увеличивается. В целях конфиденциальности мы не будем вводить их по порядку. Он широко используется в высоких частотах; среднечастотная закалка автомобильного полуоси.
Концентрация, температура и перемешивание закалочной жидкости
Единицы, которые мы обслуживаем: концентрация ПАГ в закалочной жидкости в зависимости от марки стали, размера деталей и внешних размеров в соответствии с теорией и опытом для регулировки ее концентрации ....
Температура жидкости регулируется на уровне 30-50 ℃, а большой циркуляционный бассейн за пределами завода используется для циркуляционного теплообмена. Перемешивание и циркуляция составляют единое целое.
Контроль твердости после закалки
Твердость после закалки является очень важным показателем для предотвращения растрескивания: особенно при использовании закалочной жидкости на водной основе, чем выше твердость, тем легче возникают трещины и увеличение деформации. Возьмите 42CrMo. Например, балку передней оси нужно регулировать на HRC48 52.
Закалка должна производиться сразу после закалки.
Интервал закалки и отпуска: ≤30 минут (для продукции военного и гражданского назначения Chongqing Construction Group требуется, чтобы время закалки жидкостью на водной основе до интервала возврата воды превышало 30 минут, затем она будет списана) Производство мелких деталей можно использовать в непрерывном отпуске производственные линии.
Металлографическая структура и свойства после ковки и закалки
Ковка с термической закалкой, если требуется предварительное охлаждение, зерна обычно крупнее. Данные [1, 2, 3], полученные в результате проверки дипломной работы студентов в этом году, обычно используемые небольшие образцы не предварительно охлаждаются и не подвергаются непосредственной закалке, что дает очень важную теоретическую основу.
Благодаря инновациям и развитию людей: текущая производственная технология в настоящее время использует предварительное охлаждение и закалку, а размер зерна обычно составляет 2-3, но производительность отличная. Возьмем в качестве примера вышеупомянутую балку передней оси: зернистость небольшая, и стандартные данные о цикле усталости говорят о том, что он может сломаться после 900,000 раз, а цикл усталости предварительного охлаждения и закалки после ковки принят равным 1.3. миллион раз без поломки.
Почему ковка, предварительное охлаждение и закалка крупного зерна и хорошие результаты испытаний? Основная причина заключается в том, что увеличиваются малоугловые границы зерен и увеличивается плотность дислокаций, которые невидимы под обычным металлургическим микроскопом. Поэтому многие кузнечные и закалочные агрегаты вынуждены «учить проблемы» с предыдущим контрольным агрегатом. По этой причине для инженерно-технического персонала, который в настоящее время занимается металлографическими стандартами, срочно необходимо быстро сформулировать стандарты металлографической штамповки и закалки ...
Заключение
- Применение метода предварительного охлаждения для закалки отходящим теплом после ковки. Выбор температуры предварительного охлаждения основан на требуемой структуре и характеристиках, если она соответствует требованиям, чем ниже, тем лучше.
- После ковки закалочную среду для закалки остаточным теплом выбирают, насколько это возможно, чтобы использовать первую скорость охлаждения (скорость перлитного превращения) для образования эффекта твердой оболочки. Вторая закалочная жидкость с низкой скоростью охлаждения (низкая скорость мартенситного превращения).
- Если сырье и другие аспекты хороши, при предварительном планировании следует учитывать три основных эффекта.
- Химический состав и сегрегация сырья особенно склонны к образованию трещин. При изменении номера печи рекомендуется выполнить небольшую пробную партию и 100% контроль намагниченности. Воспользуйтесь преимуществами, чтобы найти меры по предотвращению появления большого количества записок.
Сохраните источник и адрес этой статьи для перепечатки.: Контроль качества при закалке отходами тепла после ковки
Минхэ Компания по литью под давлением специализируются на производстве и предоставлении качественных и высокопроизводительных литых деталей (ассортимент металлических деталей для литья под давлением в основном включает Тонкостенное литье под давлением,Литье под давлением,Литье под давлением в холодной камере), Round Service (Служба литья под давлением,Обработка с ЧПУ,Изготовление пресс-форм, Обработка поверхности) .Любое индивидуальное литье под давлением из алюминия, магния или замака / цинка, а также другие требования к отливкам, пожалуйста, свяжитесь с нами.
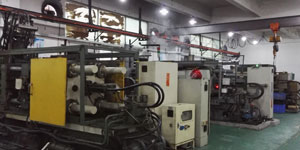
Под контролем ISO9001 и TS 16949, все процессы выполняются на сотнях передовых машин для литья под давлением, 5-осевых станках и других объектах, от струйных до стиральных машин Ultra Sonic. Minghe не только имеет современное оборудование, но и имеет профессиональное оборудование. команда опытных инженеров, операторов и инспекторов для воплощения в жизнь проекта заказчика.
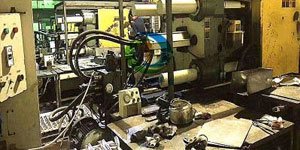
Контрактный производитель отливок под давлением. Возможности включают в себя детали для литья под давлением алюминия с холодной камерой весом от 0.15 фунта. до 6 фунтов, быстрая установка и обработка. Дополнительные услуги включают полировку, вибрацию, удаление заусенцев, дробеструйную очистку, окраску, гальванику, нанесение покрытий, сборку и оснастку. Обрабатываемые материалы включают такие сплавы, как 360, 380, 383 и 413.
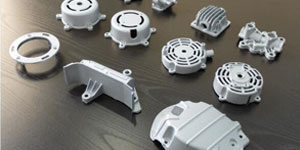
Помощь в проектировании литья цинка под давлением / сопутствующие инженерные услуги. Изготовление на заказ прецизионных отливок из цинка под давлением. Могут изготавливаться миниатюрные отливки, отливки под высоким давлением, отливки в формы с несколькими суппортами, отливки в обычные формы, единичные отливки под давлением и независимые отливки под давлением, а также отливки с герметизацией полости. Отливки могут изготавливаться длиной и шириной до 24 дюймов с допуском +/- 0.0005 дюйма.
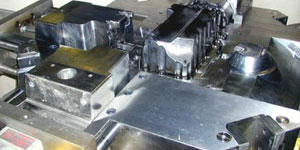
Производитель литья под давлением из магния, сертифицированный по стандарту ISO 9001: 2015. Возможности включают литье под давлением магния под высоким давлением с горячей камерой до 200 тонн и холодной камерой на 3000 тонн, проектирование инструментов, полировку, формование, механическую обработку, порошковую и жидкостную окраску, полный контроль качества с возможностями CMM , сборка, упаковка и доставка.
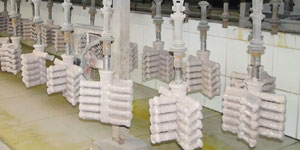
Сертифицирован ITAF16949. Дополнительные услуги трансляции включают инвестиционное литье,литье в песчаные формы,Гравитационное литье, Литье по выплавляемым моделям,Центробежное литье,Вакуумное литье,Постоянное литье формыВозможности включают EDI, техническую поддержку, твердотельное моделирование и вторичную обработку.
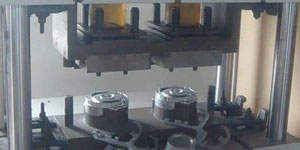
Литейная промышленность Примеры использования запчастей для: автомобилей, велосипедов, самолетов, музыкальных инструментов, судов, оптических устройств, датчиков, моделей, электронных устройств, корпусов, часов, машинного оборудования, двигателей, мебели, ювелирных изделий, приспособлений, телекоммуникаций, освещения, медицинских устройств, фотографических устройств, Роботы, скульптуры, звуковое оборудование, спортивное оборудование, инструменты, игрушки и многое другое.
Что мы можем вам сделать дальше?
∇ Перейти на главную страницу для Литье под давлением Китай
→Литье деталей-Узнай, что мы сделали.
→ Общие советы о Услуги литья под давлением
By Производитель литья под давлением Minghe | Категории: Полезные статьи |Материалы Теги: Литье алюминия, Цинковое литье, Литье магния, Титановое литье, Литье из нержавеющей стали, Латунное литье,Бронзовое литье,Кастинг видео,История компании,Литье алюминия под давлением | Комментарии отключены