7 часто задаваемых вопросов в области производства пресс-форм
Что является основным фактором, влияющим на обрабатываемость материала?
Химический состав стали очень важен. Чем выше легирующий состав стали, тем труднее ее обрабатывать. Когда содержание углерода увеличивается, производительность резки металла снижается.
Структура стали также очень важна для производительности резки металла. Различные конструкции включают: кованые, литые, экструдированные, катаные и обработанные. Поковки и отливки имеют очень трудную для обработки поверхность.
Твердость - важный фактор, влияющий на производительность резки металла. Общее правило заключается в том, что чем тверже сталь, тем труднее ее обрабатывать. Из быстрорежущей стали (HSS) можно обрабатывать материалы с твердостью до 330-400HB; быстрорежущая сталь + покрытие TiN позволяет обрабатывать материалы с твердостью до 45HRC; а для материалов с твердостью 65-70HRC необходимо использовать твердый сплав, керамику, металлокерамику и кубический нитрид бора (CBN).
Неметаллические включения обычно отрицательно сказываются на стойкости инструмента. Например, Al2O3 (оксид алюминия), представляющий собой чистую керамику, очень абразивен.
Последний - это остаточное напряжение, которое может вызвать проблемы с производительностью резки металла. Часто рекомендуется выполнять процесс снятия напряжения после черновой обработки.
Каковы режущие характеристики чугуна?
Вообще говоря, это:
Чем выше твердость и прочность чугуна, тем ниже производительность резки металла и тем ниже ожидаемый срок службы лезвий и фрез. Большинство типов чугуна, используемых при резке металлов, обычно имеют хорошие характеристики резки. Производительность резки металла зависит от структуры, и более твердый перлитный чугун также труднее обрабатывать. Чугун с чешуйчатым графитом и ковкий чугун обладают отличными режущими свойствами, а ковкий чугун - довольно плохими.
Основные виды износа при обработке чугуна: абразивный, адгезионный и диффузионный. Истирание в основном вызывается карбидами, частицами песка и твердой литой коркой. Износ связки с наростом на кромке происходит при низкой температуре резания и низкой скорости резания. Ферритную часть чугуна легче всего приварить к лезвию, но этого можно избежать, увеличив скорость резания и температуру.
С другой стороны, диффузионный износ зависит от температуры и возникает при высоких скоростях резания, особенно при использовании высокопрочных марок чугуна. Эти марки обладают высокой устойчивостью к деформации, что приводит к высоким температурам. Этот износ связан с взаимодействием между чугуном и режущим инструментом, из-за чего некоторые чугуны необходимо обрабатывать керамическими режущими инструментами или режущими инструментами из кубического нитрида бора (CBN) на высоких скоростях для получения хорошего срока службы и качества поверхности.
Обычно для обработки чугуна требуются следующие типичные свойства инструмента: высокая термическая твердость и химическая стабильность, но это также зависит от процесса, обрабатываемой детали и условий резания; режущая кромка должна обладать ударной вязкостью, термостойкостью и прочностью кромки. Степень удовлетворенности резкой чугуна зависит от того, как развивается износ режущей кромки: быстрое затупление означает, что горячие трещины и зазубрины приводят к преждевременному разрушению режущей кромки, повреждению заготовки, низкому качеству поверхности, чрезмерной волнистости и т. Д. Нормальный износ по задней поверхности , баланс и острые режущие кромки - вот что обычно требует усилий.
Каковы основные и распространенные технологические процессы при производстве пресс-форм?
Процесс резки следует разделить как минимум на 3 типа:
Черновая обработка, получистовая обработка и чистовая обработка, а иногда даже суперпроизводство (в основном, высокоскоростная обработка). Остаточное фрезерование, конечно, подготавливается для чистовой обработки после процесса получистовой обработки. В каждом процессе необходимо стараться оставлять равномерно распределенную маржу для следующего процесса, что очень важно. Если направление и рабочая нагрузка траектории инструмента редко меняются быстро, срок службы инструмента может быть увеличен и более предсказуем. По возможности, чистовую обработку следует проводить на специальном станке. Это повысит геометрическую точность и качество пресс-формы за счет сокращения времени наладки и сборки.
Какие инструменты следует использовать в этих различных процессах?
Процесс черновой обработки: фреза с круглым лезвием, фреза со сферическим концом и фреза с большим радиусом дуги при вершине.
Полуфабрикат: фреза с круглым лезвием (фреза с круглым лезвием с диапазоном диаметров 10-25 мм), фреза со сферическим концом.
Процесс отделки: фреза с круглым лезвием, фреза со сферическим концом.
Остаточный процесс фрезерования: фреза с круглым лезвием, фреза со сферическим концом, фреза вертикальная.
Очень важно оптимизировать процесс резания путем выбора комбинации специальных размеров, геометрии и сплавов инструментов, а также параметров резания и подходящих стратегий фрезерования.
Информацию о высокопроизводительных инструментах, которые можно использовать, см. В каталоге C-1102: 1 для изготовления пресс-форм.
Есть ли один из самых важных факторов в процессе резки?
Одна из наиболее важных целей в процессе резания - создать равномерно распределенный припуск на обработку для каждого инструмента в каждом процессе. Это означает, что необходимо использовать инструменты разного диаметра (от большого до малого), особенно при черновой и получистовой обработке. Главный критерий в любой момент должен быть как можно ближе к окончательной форме формы в каждом процессе.
Равномерно распределенные припуски на обработку для каждого инструмента обеспечивают постоянную и высокую производительность и безопасный процесс резания. Когда ap / ae (осевая глубина резания / радиальная глубина резания) не изменяется, скорость резания и скорость подачи также могут постоянно поддерживаться на высоком уровне. Таким образом, механическое воздействие и изменения рабочей нагрузки на режущей кромке незначительны, поэтому генерируемые тепло и усталость также меньше, что увеличивает срок службы инструмента. Если последующие процессы представляют собой некоторые процессы получистовой обработки, особенно все процессы отделки, обработка без участия человека или частичная обработка без участия человека может выполняться. Постоянный припуск на обработку материала также является основным стандартом для высокоскоростной резки.
Еще одним положительным эффектом постоянного припуска на обработку является небольшое отрицательное воздействие на направляющие рельсы станка, шариковые винтовые пары и подшипники шпинделя.
Почему фрезы с круглым лезвием являются наиболее распространенным выбором для инструментов для черновой обработки пресс-форм?
Если для чернового фрезерования полости используется фреза с квадратным уступом, при получистовой обработке будет удален большой припуск на ступенчатую резку. Это изменит силу резания и приведет к изгибу инструмента. В результате остается неровный припуск на обработку для чистовой обработки, что влияет на геометрическую точность формы. Если вы используете фрезу с квадратным уступом (с треугольной пластиной) с более слабым концом, это приведет к непредсказуемым эффектам резания. Треугольные или алмазные пластины также создают большие радиальные силы резания, а поскольку количество режущих кромок пластин невелико, они являются менее экономичными инструментами для черновой обработки.
С другой стороны, круглую пластину можно фрезеровать в различных материалах и во всех направлениях. Если он используется, переход между соседними траекториями инструмента будет более плавным, и он также может оставить меньшую и более равномерную обработку для получистовой обработки. поле. Одной из характеристик круглых лезвий является то, что толщина стружки, которую они производят, варьируется. Это позволяет им использовать более высокие скорости подачи, чем у большинства других пластин.
Угол въезда круглой пластины изменяется от почти нуля (очень неглубокое резание) до 90 градусов, и режущее действие очень плавное. На максимальной глубине резания угол в плане составляет 45 градусов. При резке по прямой стене по внешнему кругу входной угол составляет 90 градусов. Это также объясняет, почему у инструмента с круглым лезвием большая сила - режущая нагрузка постепенно увеличивается. Для черновой и получистовой обработки всегда следует использовать фрезы с круглым лезвием, такие как CoroMill200 (см. Каталог изготовления пресс-форм C-1102: 1) в качестве первого выбора. Для 5-осевой резки очень подходят круглые пластины, тем более, что она не имеет ограничений.
Благодаря правильному программированию фрезы с круглыми пластинами могут в значительной степени заменить шаровые концевые фрезы. Круглый нож с малым биением сочетается с мелко заточенным, положительным передним углом и легкой геометрией резания, а также может использоваться для получистовой обработки и некоторых чистовых процессов.
Какова эффективная скорость резания (ve) и почему она всегда очень важна для базового расчета эффективной скорости резания на эффективном диаметре высокой производительности.
Поскольку подача стола зависит от скорости вращения при определенной скорости резания, если эффективная скорость не вычисляется, подача стола будет рассчитана неправильно.
Если при расчете скорости резания используется номинальный диаметр инструмента (Dc), то при небольшой глубине резания эффективная или фактическая скорость резания намного ниже расчетной скорости. Такие как инструменты CoroMill200 с круглыми пластинами (особенно в диапазоне малых диаметров), сферические концевые фрезы, концевые фрезы с большим радиусом дуги и концевые фрезы CoroMill390 и другие инструменты (для этих инструментов см. Образец Sandvik Coromant для изготовления пресс-форм C-1102: 1 ). В результате расчетная скорость подачи также намного ниже, что серьезно снижает производительность. Что еще более важно, условия резания инструмента ниже, чем его возможности и рекомендуемый диапазон применения.
Сохраните источник и адрес этой статьи для перепечатки.:7 часто задаваемых вопросов в области производства пресс-форм
Минхэ Компания по литью под давлением специализируются на производстве и предоставлении качественных и высокопроизводительных литых деталей (ассортимент металлических деталей для литья под давлением в основном включает Тонкостенное литье под давлением,Литье под давлением,Литье под давлением в холодной камере), Round Service (Служба литья под давлением,Обработка с ЧПУ,Изготовление пресс-форм, Обработка поверхности) .Любое индивидуальное литье под давлением из алюминия, магния или замака / цинка, а также другие требования к отливкам, пожалуйста, свяжитесь с нами.
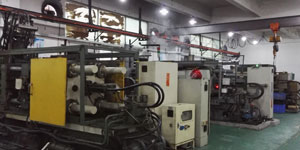
Под контролем ISO9001 и TS 16949, все процессы выполняются на сотнях передовых машин для литья под давлением, 5-осевых станках и других объектах, от струйных до стиральных машин Ultra Sonic. Minghe не только имеет современное оборудование, но и имеет профессиональное оборудование. команда опытных инженеров, операторов и инспекторов для воплощения в жизнь проекта заказчика.
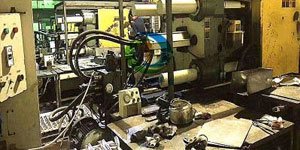
Контрактный производитель отливок под давлением. Возможности включают в себя детали для литья под давлением алюминия с холодной камерой весом от 0.15 фунта. до 6 фунтов, быстрая установка и обработка. Дополнительные услуги включают полировку, вибрацию, удаление заусенцев, дробеструйную очистку, окраску, гальванику, нанесение покрытий, сборку и оснастку. Обрабатываемые материалы включают такие сплавы, как 360, 380, 383 и 413.
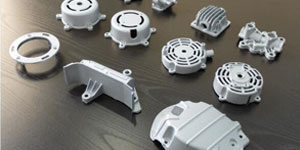
Помощь в проектировании литья цинка под давлением / сопутствующие инженерные услуги. Изготовление на заказ прецизионных отливок из цинка под давлением. Могут изготавливаться миниатюрные отливки, отливки под высоким давлением, отливки в формы с несколькими суппортами, отливки в обычные формы, единичные отливки под давлением и независимые отливки под давлением, а также отливки с герметизацией полости. Отливки могут изготавливаться длиной и шириной до 24 дюймов с допуском +/- 0.0005 дюйма.
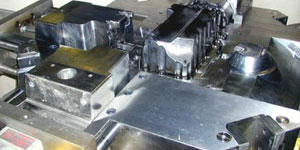
Производитель литья под давлением из магния, сертифицированный по стандарту ISO 9001: 2015. Возможности включают литье под давлением магния под высоким давлением с горячей камерой до 200 тонн и холодной камерой на 3000 тонн, проектирование инструментов, полировку, формование, механическую обработку, порошковую и жидкостную окраску, полный контроль качества с возможностями CMM , сборка, упаковка и доставка.
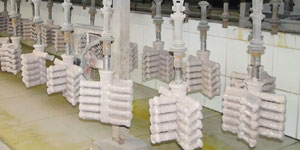
Сертифицирован ITAF16949. Дополнительные услуги трансляции включают инвестиционное литье,литье в песчаные формы,Гравитационное литье, Литье по выплавляемым моделям,Центробежное литье,Вакуумное литье,Постоянное литье формыВозможности включают EDI, техническую поддержку, твердотельное моделирование и вторичную обработку.
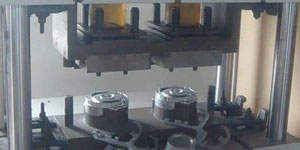
Литейная промышленность Примеры использования запчастей для: автомобилей, велосипедов, самолетов, музыкальных инструментов, судов, оптических устройств, датчиков, моделей, электронных устройств, корпусов, часов, машинного оборудования, двигателей, мебели, ювелирных изделий, приспособлений, телекоммуникаций, освещения, медицинских устройств, фотографических устройств, Роботы, скульптуры, звуковое оборудование, спортивное оборудование, инструменты, игрушки и многое другое.
Что мы можем вам сделать дальше?
∇ Перейти на главную страницу для Литье под давлением Китай
→Литье деталей-Узнай, что мы сделали.
→ Общие советы о Услуги литья под давлением
By Производитель литья под давлением Minghe | Категории: Полезные статьи |Материалы Теги: Литье алюминия, Цинковое литье, Литье магния, Титановое литье, Литье из нержавеющей стали, Латунное литье,Бронзовое литье,Кастинг видео,История компании,Литье алюминия под давлением | Комментарии отключены