Причины чрезмерного содержания углерода при производстве отливок из пенопласта
- Необоснованный выбор литейных материалов. При выборе материала белой формы для литья одним из них является высокое содержание углерода; во-вторых, плотность белой плесени слишком высока. В результате образец литья имеет высокое содержание углерода во время термического разложения во время процесса разливки, а жидкая фаза и свободное от тумана содержание углерода в отливке во время процесса заливки и заполнения высокое, что приводит к увеличению вероятности науглероживания стальное литье.
- Для изготовления отливок выбирайте пенопласт или предварительно расширенные шарики с низким содержанием углерода. В настоящее время отечественный пенополистирол EPS содержит 92% углерода; смола на основе сополимера стирола и метилметакрилата STMMAC имеет содержание углерода 69.6%; вспениваемый полиметилметакрилат ЭПММА имеет содержание углерода 60.0%; Использование материала EPS для изготовления литейной формы увеличит содержание углерода в жидкой стали на 0.1–0.3% в процессе литья. Когда для изготовления литейной формы используется EPMMA или STMMA, отливка происходит из-за материала формы во время процесса разливки. Увеличение содержания углерода составляет менее 0.05%.
- Выберите подходящую плотность пены, чтобы сделать рисунок отливки. При обеспечении технических требований к температуре изготовления модели и отсутствии других дефектов, вызванных качеством пены во время изготовления и заливки отливки, чем меньше плотность пены модели отливки и чем меньше пена, тем лучше уменьшить науглероживание отливки.
- Повышение качества изготовления моделей литья. Когда рисунок отливки может быть выполнен как единое целое, его не следует изготавливать в комбинации, а поверхность скрепления рисунка отливки должна быть сведена к минимуму. При выполнении склеивания рисунка необходимо обеспечить, чтобы склеиваемая поверхность рисунка была гладкой и плоской, минимизировать количество клея, используемого для склеивания, и уменьшить количество продуктов термического разложения клея, чтобы уменьшить содержание углерода в термическом склеивании. продукты разложения.
- Используйте клеи с низким содержанием углерода или без углерода. То есть, для склеивания с комбинацией рисунков следует использовать специальный клей для литья под отрицательным давлением и склеивания вместо некачественных обычных клеев с высоким содержанием углерода для склеивания. И когда узор объединяется и склеивается, при обеспечении температуры склеивания и прочности склеивания клея количество клея должно быть минимизировано, чтобы уменьшить продукты термического разложения клея.
- Выберите и определите разумную систему стробирования. Для проектирования процесса литья отливок необходимо, чтобы отливки обладали эффектом ускорения газификации пенопласта в процессе литья, а также минимизировали и смещали время контакта и реакции жидкой и твердой фаз в термической фазе. продукты разложения, что снижает или предотвращает науглероживание отливки.
- Выберите и определите подходящую температуру и скорость разливки отливки. Из-за различных форм одной и той же отливки, например, процесса литья, фактическая температура заполнения отливки полностью различается, когда жидкая сталь разливается при той же температуре. Если температура разливки увеличится, скорость разливки также увеличится, что приведет к более быстрому термическому разложению модели разливки и затруднению полной газификации, что приведет к увеличению количества продуктов термического разложения в жидкой фазе. В то же время, поскольку зазор между расплавленной сталью и рисунком небольшой, жидкая фаза после выдавливания из зазора часто сжимается между слоем покрытия узора и расплавленным металлом или холодом. углы или мертвые углы, по которым течет расплавленная сталь, вызывая увеличение контактной поверхности, концентрация углерода и степень науглероживания также увеличиваются. В то же время обратите особое внимание на тот факт, что, если процесс разливки нецелесообразен, температура разливки расплавленной стали слишком высока, а скорость разливки слишком высокая, это приведет к производственным авариям, таким как выделение газа и обратное распыление.
- Антипирен добавляется к рисунку, чтобы предотвратить растрескивание и возгорание рисунка при высокой температуре, чтобы он не производил или не производил менее углеродсодержащих твердых продуктов. Например, добавление антипирена от 0.5% до 3% хлорированного парафина, трифосфата, пентабромдифенилового эфира, триоксида сурьмы и т.д. газа, тем самым снижая условия науглероживания и условия в процессе литья.
- В процессе нанесения кистью на слой узорчатого покрытия могут быть добавлены материалы, препятствующие науглероживанию. Некоторые катализаторы против науглероживания, такие как соль щелочного металла и порошок известняка, добавляются в процессе подготовки покрытия рисунка, так что рисунок может разлагать достаточно газа CO и CO2 для поглощения углерода в слое покрытия после заливки, тем самым предотвращая литье из проникающего углерода; или добавление окислителя к покрытию, чтобы способствовать превращению газов C и H2 после термического разложения модели в нейтральный газ, так что C и H после термического разложения могут уменьшить проникновение в отливку, вызывая увеличение углерода или водородное охрупчивание .
После анализа и обобщения различных возможных причин чрезмерного содержания углерода при производстве отливок из низкоуглеродистой стали с потерянной пеной была изменена и скорректирована конструкция производственного процесса и технические параметры производства отливок из низкоуглеродистой стали с потерянной пеной. Разумные и надежные технологические условия литья низкоуглеродистой стали задают производственный режим работы системы, чтобы обеспечить технические требования для производства качественных литейных изделий из низкоуглеродистой стали с использованием потерянной пены.
При корректировке уставок технических параметров технологического процесса управления производством отливок из низкоуглеродистой стали в производстве пенополистирола следует обратить особое внимание на следующие моменты:
- При использовании плавки с промежуточной частотой необходимо строго контролировать расчет дозирования и фактические операции дозирования, выбора материала и подачи при выплавке углеродистой стали. Потому что расчет ингредиентов является ключом к тому, чтобы расплавленная сталь с квалифицированным составом и наименьшим количеством газов и включений плавилась для производства высококачественных стальных отливок. Точность ингредиентов, их подбора и подачи - основная гарантия качества отливок. Следовательно, для вторичного лома должна проводиться строгая система дополнительных проверок. В частности, необходимо удалить обрезки и обрезки легированной стали с непрозрачными материалами, чтобы состав плавильных ингредиентов соответствовал требованиям технических параметров процесса литья, что является первоочередной задачей при эксплуатации и контроле производства низкотемпературных материалов. отливки из углеродистой стали в потерянной пене.
- Для изготовления отливок выбирайте пенопласт или предварительно расширенные шарики с низким содержанием углерода. В настоящее время отечественный пенополистирол EPS содержит 92% углерода; смола на основе сополимера стирола и метилметакрилата STMMAC имеет содержание углерода 69.6%; вспениваемый полиметилметакрилат ЭПММА имеет содержание углерода 60.0%; Использование материала EPS для изготовления литейной формы увеличит содержание углерода в жидкой стали на 0.1–0.3% в процессе литья. Когда для изготовления литейной формы используется материал EPMMA или STMMA, отливка происходит из-за материала формы во время процесса разливки. Увеличение содержания углерода составляет менее 0.05%.
- Выберите подходящую плотность пены, чтобы сделать рисунок отливки. При обеспечении технических требований к температуре изготовления модели и отсутствии других дефектов, вызванных качеством пены во время изготовления и заливки отливки, чем меньше плотность пены модели отливки и чем меньше пена, тем лучше уменьшить науглероживание отливки.
- Повышение качества изготовления моделей литья. Когда рисунок отливки может быть выполнен как единое целое, его не следует изготавливать в комбинации, а поверхность скрепления рисунка отливки должна быть сведена к минимуму. При выполнении склеивания рисунка необходимо обеспечить, чтобы склеиваемая поверхность рисунка была гладкой и плоской, минимизировать количество клея, используемого для склеивания, и уменьшить количество продуктов термического разложения клея, чтобы уменьшить содержание углерода в термическом склеивании. продукты разложения.
- Используйте клеи с низким содержанием углерода или без углерода. То есть для склейки узоров следует использовать специальный клей для литья под отрицательным давлением и склеивания вместо некачественного обычного клея с высоким содержанием углерода для склеивания. И когда узор объединяется и склеивается, при обеспечении температуры склеивания и прочности склеивания клея количество клея должно быть минимизировано, чтобы уменьшить продукты термического разложения клея.
- Выберите и определите разумную систему стробирования. Для проектирования процесса литья отливок необходимо, чтобы отливки обладали эффектом ускорения газификации пенопласта в процессе литья, а также минимизировали и смещали время контакта и реакции жидкой и твердой фаз в термической фазе. продукты разложения, что снижает или предотвращает науглероживание отливки.
- Выберите и определите подходящую температуру и скорость разливки отливки. Из-за различных форм одной и той же отливки, например, процесса литья, фактическая температура заполнения отливки полностью различается, когда жидкая сталь разливается при той же температуре. Если температура разливки увеличится, скорость разливки также увеличится, что приведет к более быстрому термическому разложению модели разливки и затруднению полной газификации, что приведет к увеличению количества продуктов термического разложения в жидкой фазе. В то же время, поскольку зазор между расплавленной сталью и рисунком небольшой, жидкость После выдавливания из зазора продукты термического разложения часто сжимаются между слоем покрытия узора и расплавленным металлом, или холодными углами, или мертвые углы, по которым течет расплавленная сталь, вызывая увеличение контактной поверхности, концентрация углерода и степень науглероживания также увеличиваются. В то же время обратите особое внимание на тот факт, что, если процесс разливки нецелесообразен, температура разливки расплавленной стали слишком высока, а скорость разливки слишком высокая, это приведет к производственным авариям, таким как выделение газа и обратное распыление.
- Антипирен добавляется к рисунку, чтобы предотвратить растрескивание и возгорание рисунка при высокой температуре, чтобы он не производил или не производил менее углеродсодержащих твердых продуктов. Например, добавление антипирена от 0.5% до 3% хлорированного парафина, трифосфата, пентабромдифенилового эфира, триоксида сурьмы и т.д. газа, тем самым снижая условия науглероживания и условия в процессе литья.
- В процессе нанесения кистью на слой узорчатого покрытия могут быть добавлены материалы, препятствующие науглероживанию. Некоторые катализаторы против науглероживания, такие как соль щелочного металла и порошок известняка, добавляются в процессе подготовки покрытия рисунка, так что рисунок может разлагать достаточно газа CO и CO2 для поглощения углерода в слое покрытия после заливки, тем самым предотвращая литье из проникающего углерода; или добавление окислителя к покрытию, чтобы способствовать превращению газов C и H2 после термического разложения модели в нейтральный газ, так что C и H после термического разложения могут уменьшить проникновение в отливку, вызывая увеличение углерода или водородное охрупчивание .
После анализа и обобщения различных возможных причин чрезмерного содержания углерода при производстве отливок из низкоуглеродистой стали с потерянной пеной была изменена и скорректирована конструкция производственного процесса и технические параметры производства отливок из низкоуглеродистой стали с потерянной пеной. Разумные и надежные технологические условия литья низкоуглеродистой стали задают производственный режим работы системы, чтобы обеспечить технические требования для производства качественных литейных изделий из низкоуглеродистой стали с использованием потерянной пены. При корректировке уставок технических параметров технологического процесса управления производством отливок из низкоуглеродистой стали в производстве пенополистирола следует обратить особое внимание на следующие моменты:
- При использовании плавки с промежуточной частотой необходимо строго контролировать расчет дозирования и фактические операции дозирования, выбора материала и подачи при выплавке углеродистой стали. Потому что расчет ингредиентов является ключом к тому, чтобы расплавленная сталь с квалифицированным составом и наименьшим количеством газов и включений плавилась для производства высококачественных стальных отливок. Точность ингредиентов, их подбора и подачи - основная гарантия качества отливок. Следовательно, для вторичного лома должна проводиться строгая система дополнительных проверок. В частности, необходимо удалить обрезки и обрезки легированной стали с непрозрачными материалами, чтобы состав плавильных ингредиентов соответствовал требованиям технических параметров процесса литья, что является первоочередной задачей при эксплуатации и контроле производства низкотемпературных материалов. отливки из углеродистой стали в потерянной пене.
- Для изготовления отливок выбирайте пенопласт или предварительно расширенные шарики с низким содержанием углерода. В настоящее время отечественный пенополистирол EPS содержит 92% углерода; смола на основе сополимера стирола и метилметакрилата STMMAC имеет содержание углерода 69.6%; вспениваемый полиметилметакрилат ЭПММА имеет содержание углерода 60.0%; Использование материала EPS для изготовления литейной формы увеличит содержание углерода в жидкой стали на 0.1–0.3% в процессе литья. Когда для изготовления литейной формы используется материал EPMMA или STMMA, отливка происходит из-за материала формы во время процесса разливки. Увеличение содержания углерода составляет менее 0.05%.
- Выберите подходящую плотность пены, чтобы сделать рисунок отливки. При обеспечении технических требований к температуре изготовления модели и отсутствии других дефектов, вызванных качеством пены во время изготовления и заливки отливки, чем меньше плотность пены модели отливки и чем меньше пена, тем лучше уменьшить науглероживание отливки.
- Повышение качества изготовления моделей литья. Когда рисунок отливки может быть выполнен как единое целое, его не следует изготавливать в комбинации, а поверхность скрепления рисунка отливки должна быть сведена к минимуму. При выполнении склеивания рисунка необходимо обеспечить, чтобы склеиваемая поверхность рисунка была гладкой и плоской, минимизировать количество клея, используемого для склеивания, и уменьшить количество продуктов термического разложения клея, чтобы уменьшить содержание углерода в термическом склеивании. продукты разложения.
- Используйте клеи с низким содержанием углерода или без углерода. То есть, для склеивания с комбинацией рисунков следует использовать специальный клей для литья под отрицательным давлением и склеивания вместо некачественных обычных клеев с высоким содержанием углерода для склеивания. И когда узор объединяется и склеивается, при обеспечении температуры склеивания и прочности склеивания клея количество клея должно быть минимизировано, чтобы уменьшить продукты термического разложения клея.
- Выберите и определите разумную систему стробирования. Для проектирования процесса литья отливок необходимо, чтобы отливки обладали эффектом ускорения газификации пенопласта в процессе литья, а также минимизировали и смещали время контакта и реакции жидкой и твердой фаз в термической фазе. продукты разложения, что снижает или предотвращает науглероживание отливки.
- Выберите и определите подходящую температуру и скорость разливки отливки. Из-за различных форм одной и той же отливки, например, процесса литья, фактическая температура заполнения отливки полностью различается, когда жидкая сталь разливается при той же температуре. Если температура разливки увеличится, скорость разливки также увеличится, что приведет к более быстрому термическому разложению модели разливки и затруднению полной газификации, что приведет к увеличению количества продуктов термического разложения в жидкой фазе. В то же время, поскольку зазор между расплавленной сталью и рисунком небольшой, жидкость После выдавливания из зазора продукты термического разложения часто сжимаются между слоем покрытия узора и расплавленным металлом, или холодными углами, или мертвые углы, по которым течет расплавленная сталь, вызывая увеличение контактной поверхности, концентрация углерода и степень науглероживания также увеличиваются. В то же время обратите особое внимание на тот факт, что, если процесс разливки нецелесообразен, температура разливки расплавленной стали слишком высока, а скорость разливки слишком высокая, это приведет к производственным авариям, таким как выделение газа и обратное распыление.
- Антипирен добавляется к рисунку, чтобы предотвратить растрескивание и возгорание рисунка при высокой температуре, чтобы он не производил или не производил менее углеродсодержащих твердых продуктов. Например, добавление антипирена от 0.5% до 3% хлорированного парафина, трифосфата, пентабромдифенилового эфира, триоксида сурьмы и т.д. газа, тем самым снижая условия науглероживания и условия в процессе литья.
- В процессе нанесения кистью на слой узорчатого покрытия могут быть добавлены материалы, препятствующие науглероживанию. Добавьте некоторые катализаторы против науглероживания, такие как соль щелочного металла и известняковый порошок, во время процесса подготовки краски для рисунка, чтобы рисунок мог разложить достаточно газа CO и CO2 для поглощения углерода в слое краски после заливки, тем самым предотвращая литье. от проникновения. Углерод; или добавление окислителя к покрытию, чтобы способствовать превращению газов C и H2 после термического разложения модели в нейтральный газ, так что C и H после термического разложения могут уменьшить проникновение в отливку, вызывая увеличение углерода или водородное охрупчивание .
- Строго контролировать качество переработки песка. Убедитесь, что производство и использование формовочной смеси соответствует требованиям технических параметров процесса, особенно необходимо строго контролировать содержание пыли в формовочной смеси, чтобы предотвратить снижение воздухопроницаемости литейного песка из-за пыли, вызывающей продукты термического разложения модели отливки не могут вовремя выходить из литейной полости и увеличивают скорость повторного науглероживания отливок.
- При производстве и разливке отливок из низкоуглеродистой стали необходимо увеличить вакуум в литейной опоке. Ящик для формовки с песком должен иметь структуру вакуумирования стенок ящика. При разливке вакуумная очистка стенок коробки может ускорить выход продуктов термического разложения за пределы полости формы, тем самым уменьшая концентрацию и время контакта продуктов термического разложения модели, а также уменьшая или предотвращая науглероживание литой стали и углеродистые отложения деталей. . Когда размер формовочного песка составляет от 20 до 40 меш, 0.03 МПа ± 0.06 МПа подходит для литья стальных отливок. Если отрицательное давление слишком велико, это вызовет налипание песка и другие дефекты отливки.
- Для разливки отливок из низкоуглеродистой стали следует максимально использовать метод нижней разливки, чтобы поток заполнения расплавленной стали был гладким, а продукты термического разложения модели могли плавно попадать в полость для сбора шлака или стояк, тем самым уменьшение и уменьшение термического разложения рисунка Время реакции контакта жидкой фазы и твердой фазы в продукте сокращается и исключает вероятность увеличения содержания углерода. Использование дождевой системы для разливки отливок из низкоуглеродистой стали приведет к увеличению рабочих условий и условий науглероживания, науглероживания и отложения углерода в отливках, а также вызовет серьезные дефекты отливок и непригодность для использования.
Сохраните источник и адрес этой статьи для перепечатки.: Причины чрезмерного содержания углерода при производстве отливок из пенопласта
Минхэ Компания по литью под давлением специализируются на производстве и предоставлении качественных и высокопроизводительных литых деталей (ассортимент металлических деталей для литья под давлением в основном включает Тонкостенное литье под давлением,Литье под давлением,Литье под давлением в холодной камере), Round Service (Служба литья под давлением,Обработка с ЧПУ,Изготовление пресс-форм, Обработка поверхности) .Любое индивидуальное литье под давлением из алюминия, магния или замака / цинка, а также другие требования к отливкам, пожалуйста, свяжитесь с нами.
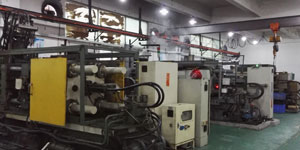
Под контролем ISO9001 и TS 16949, все процессы выполняются на сотнях передовых машин для литья под давлением, 5-осевых станках и других объектах, от струйных до стиральных машин Ultra Sonic. Minghe не только имеет современное оборудование, но и имеет профессиональное оборудование. команда опытных инженеров, операторов и инспекторов для воплощения в жизнь проекта заказчика.
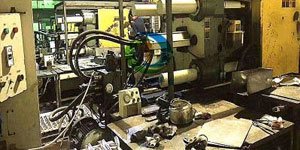
Контрактный производитель отливок под давлением. Возможности включают в себя детали для литья под давлением алюминия с холодной камерой весом от 0.15 фунта. до 6 фунтов, быстрая установка и обработка. Дополнительные услуги включают полировку, вибрацию, удаление заусенцев, дробеструйную очистку, окраску, гальванику, нанесение покрытий, сборку и оснастку. Обрабатываемые материалы включают такие сплавы, как 360, 380, 383 и 413.
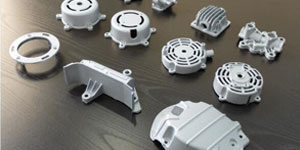
Помощь в проектировании литья цинка под давлением / сопутствующие инженерные услуги. Изготовление на заказ прецизионных отливок из цинка под давлением. Могут изготавливаться миниатюрные отливки, отливки под высоким давлением, отливки в формы с несколькими суппортами, отливки в обычные формы, единичные отливки под давлением и независимые отливки под давлением, а также отливки с герметизацией полости. Отливки могут изготавливаться длиной и шириной до 24 дюймов с допуском +/- 0.0005 дюйма.
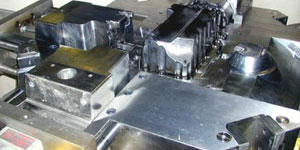
Производитель литья под давлением из магния, сертифицированный по стандарту ISO 9001: 2015. Возможности включают литье под давлением магния под высоким давлением с горячей камерой до 200 тонн и холодной камерой на 3000 тонн, проектирование инструментов, полировку, формование, механическую обработку, порошковую и жидкостную окраску, полный контроль качества с возможностями CMM , сборка, упаковка и доставка.
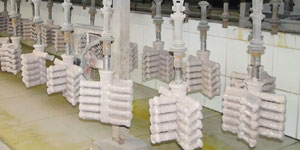
Сертифицирован ITAF16949. Дополнительные услуги трансляции включают инвестиционное литье,литье в песчаные формы,Гравитационное литье, Литье по выплавляемым моделям,Центробежное литье,Вакуумное литье,Постоянное литье формыВозможности включают EDI, техническую поддержку, твердотельное моделирование и вторичную обработку.
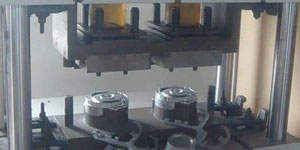
Литейная промышленность Примеры использования запчастей для: автомобилей, велосипедов, самолетов, музыкальных инструментов, судов, оптических устройств, датчиков, моделей, электронных устройств, корпусов, часов, машинного оборудования, двигателей, мебели, ювелирных изделий, приспособлений, телекоммуникаций, освещения, медицинских устройств, фотографических устройств, Роботы, скульптуры, звуковое оборудование, спортивное оборудование, инструменты, игрушки и многое другое.
Что мы можем вам сделать дальше?
∇ Перейти на главную страницу для Литье под давлением Китай
→Литье деталей-Узнай, что мы сделали.
→ Общие советы о Услуги литья под давлением
By Производитель литья под давлением Minghe | Категории: Полезные статьи |Материалы Теги: Литье алюминия, Цинковое литье, Литье магния, Титановое литье, Литье из нержавеющей стали, Латунное литье,Бронзовое литье,Кастинг видео,История компании,Литье алюминия под давлением | Комментарии отключены