Технология получения композиционного материала с металлической матрицей, армированного частицами методом литья
Композиты с металлической матрицей представляют собой многофазные материалы со специальной второй фазой, диспергированной в матрице металла или сплава. Вторая фаза с особыми физико-механическими свойствами значительно увеличивает прочность, твердость, износостойкость, термостойкость и другие свойства материала. Поэтому эту вторую фазу также называют фазой усиления. Фаза армирования обычно делится на фазу армирования частицами и фазу армирования волокнами (нитями). По таким причинам, как цена армирования и композитная технология, большинство композитных материалов, изготовленных методом литья, армированы частицами.
В последние годы метод получения армированных частицами композитных материалов постоянно совершенствовался в отношении физического метода добавления армирования, и был разработан реакционный синтез метода армирования на месте.
Независимо от того, какой метод литья композита используется, для успешного изготовления композитных изделий с отличными эксплуатационными характеристиками и стабильным качеством необходимо технически решить следующие проблемы:
- ①Выберите подходящую матрицу и арматуру в зависимости от различных требований к материалу,
- ②Улучшение смачиваемости матричного расплава армированием,
- ③ контролировать разумное распределение арматуры в матрице,
- ④ решить проблему процесса формовки отливок, вызванную влиянием армирующих частиц на вязкость матричного расплава.
В этой статье суммируются вышеупомянутые проблемы технологии изготовления отливки композитного материала с металлической матрицей, армированного частицами, с целью содействия производству композитного материала, армированного частицами.
- Выбор армирования: характеристики матрицы, армирования и хорошее сочетание армирования и матрицы определяют характеристики композитного материала, поэтому армирование следует выбирать разумно в соответствии с типом основы и требованиями к характеристикам композитного материала. . При выборе арматуры следует учитывать модуль упругости, предел прочности, твердость, термическую стабильность, плотность, температуру плавления, цену и другие факторы арматуры. В то же время коэффициент линейного расширения и химическая активность между арматурой и матрицей должны быть согласованы. Требовать. Матрица с алюминием в качестве основного компонента, обычно используемые армирующие элементы - это графит, Al2O3, SiC, TiC, Al3Ti, TiB, Al3Zr и т. Д. Исследования композиционных материалов со сталью в качестве матрицы не столь зрелы, как алюминий. матричные композиты и обычно используемые арматуры более зрелые. В меньшей степени, в основном WC, VC, TiC, TiN, Al2O3, SiC и т. Д. После выбора типа армирования размер армирования и его объемная доля в матрице также должны быть определены экспериментально.
- Методы улучшения смачиваемости арматуры / матрицы: улучшение смачиваемости арматуры расплавом матрицы, помощь в уменьшении агломерации арматуры, помощь в улучшении прочности сцепления на границе раздела матрица / арматура и улучшение композитного материала в целом. Словом, это также способствует равномерному распределению арматуры в матрице. Следующие меры обычно используются для улучшения смачиваемости матричного расплава армированием.
- Обработка покрытия армирующей поверхности: нанесение на армирующую поверхность определенного металла или компаунда с помощью таких методов, как химическое нанесение покрытия или осаждение из паровой фазы, может эффективно улучшить смачиваемость матричного расплава армирующим телом. Исследования показали, что медное покрытие на поверхности графита и осаждение из паровой фазы TiN на поверхность частиц Al2O3 эффективно улучшили смачиваемость матрицы по отношению к частицам армирования.
- Дополнительные поверхностно-активные вещества: согласно сообщениям, добавление магниевых блоков при добавлении порошка графита или диоксида кремния к расплаву алюминия может улучшить смачиваемость жидкого алюминия для армирования. Исследования последних лет также показали, что в дополнение к Mg, Ca, RE, элементы щелочных металлов и элементы группы VI и группы VIa все имеют эффект улучшения смачиваемости расплавленным алюминием на таких армирующих материалах, как Al2O3 и SiC.
- Термическая обработка арматуры: термическая обработка для удаления масла и воды с поверхности частиц арматуры может увеличить поверхностную энергию арматуры и повысить смачиваемость расплава по отношению к арматуре. Кто-то приготовил композиционные материалы графит / алюминий с использованием термообработанного графитового порошка без медного покрытия. Метод термической обработки: нагревание графитового порошка примерно до 600 ° C в течение 8 часов для активации поверхности, затем охлаждение и повторный нагрев до 200 ° C перед добавлением алюминиевой жидкости для удаления влаги. Некоторые люди также использовали метод нагрева арматуры для улучшения смачиваемости арматуры и матрицы для производства композитных материалов.
- Ультразвуковая обработка расплава с высокой энергией: кто-то подготовил композитный материал SiC / ZA27 с помощью ультразвуковой обработки расплава с высокой энергией. В исследовании полагают, что эффект кавитации, создаваемый ультразвуком высокой энергии при распространении в расплаве, очищает поверхность армированных частиц, увеличивает поверхностное натяжение частиц и в то же время снижает поверхностное натяжение расплава и значительно улучшает взаимосвязь между частицами SiC и расплавом ZA27. Смачиваемость.
- Реакционный синтез армирования на месте: применение технологии реакционного синтеза на месте для получения лигатуры, содержащей армирующие частицы, с последующим добавлением этой лигатуры в матричный расплав для получения композитных материалов Технология композитных материалов стала горячей точкой в исследованиях композитных материалов. в былые времена. Метод синтеза с реакцией на месте обычно добавляет в лигатуру некоторые чистые металлы, сплавы, соединения или солевые вещества, а усиление получается за счет химических реакций между добавками или между добавками и компонентами лигатуры. Поскольку армирование создается в результате реакции на месте, поверхность чистая и свободная от загрязнений, а термическая стабильность хорошая, что хорошо решает проблему смачиваемости арматуры расплавом матрицы, а арматура и матрица являются очень прочно сочетается с лучшим усиливающим эффектом. Некоторые ученые смешивали порошки Al, Ti и C в определенной пропорции, а затем прессовали их на мелкие кусочки. Небольшие детали были подвергнуты вакуумному спеканию в высокотемпературной диффузионной печи для получения лигатуры TiC / Al, и композит TiC / 2618 был приготовлен из лигатуры. материал. Другие также успешно получили композитные материалы с равномерным распределением армированных частиц и превосходными свойствами путем синтеза на месте реакции.
- Технология управления распределением арматуры: Контроль распределения арматуры в матрице и обеспечение полного доступа к эффективному усилению матрицы является фундаментальной гарантией изготовления композитных изделий, отвечающих определенным требованиям к характеристикам.
- Метод контроля неравномерного распределения арматуры: для износостойких / снижающих износ материалов рабочая поверхность должна иметь высокие противоизносные характеристики, в то время как остальные детали имеют лучшие комплексные механические свойства, чтобы гарантировать, что рабочая поверхность эффективно поддерживается.
Следовательно, для таких изделий, которые необходимо локально усилить, необходимо, чтобы армирование было распределено в определенном диапазоне вблизи рабочей поверхности изделия. Есть несколько часто используемых методов:
- Метод предварительного армирования: метод предварительного армирования является одним из основных методов получения поверхностно-упрочненных композиционных материалов аддитивным методом. Это применение технологии модификации поверхности методом литья-инфильтрации при получении композиционных материалов. В основном подходит для изготовления износостойких композитных изделий. Конкретный метод заключается в следующем: предварительно поместите арматуру в виде блока краски или пасты на ту часть, где необходимо укрепить изделие, а затем залейте его в жидкость из матричного сплава. Жидкость матричного сплава проникает в зазор армирующего тела за счет капиллярного сифонного эффекта и давления жидкого сплава и затвердевает. Затем образуется композитный продукт с упрочненной поверхностью, в котором армирующее тело и матрица плотно соединены. Ученые провели глубокие исследования этой технологии и считают, что ключом к технологии предварительно армированных поверхностных композитов является: ① соответствующий размер армирующих частиц и хорошая смачиваемость арматуры расплавом матрицы; ② подбор связующего и нанесение покрытия, подготовка пасты и нанесение кистью, ③ контроль температуры заливки и процесс заливки; Предустановленный метод армирования отличается простотой процесса, низкой стоимостью и отличным эффектом. Это технология поверхностных композитов, которая успешно применяется в настоящее время и имеет очень широкие перспективы применения.
- Центробежный метод управления: основанный на разнице в удельном весе арматуры и матричного расплава, метод создания армирования с градиентным распределением сегрегации в радиальном направлении с помощью центробежной силы называется центробежным методом управления. Важное направление развития градиентных композиционных материалов. Кто-то использовал метод центробежного контроля для получения композитного материала графит / алюминий с градиентным распределением графита. Учеными центробежного литья сплава Al-Fe была получена самогенерирующаяся градиентная композитная литая труба, в которой первичная фаза Fe распределена по радиальному градиенту. Металлический центробежный литейный материал с песчаным покрытием из сплава Al-Fe с самогенерированным градиентом композитного материала отметил: ①По мере увеличения количества арматуры градиент распределения арматуры в радиальном направлении постепенно уменьшается, а диапазон распределения в радиальном направлении постепенно расширяется. ; В диапазоне от 0 до 2000 об / мин с увеличением скорости вращения градиент распределения арматуры в радиальном направлении постепенно увеличивается, а диапазон распределения в радиальном направлении постепенно уменьшается.
- Метод управления электромагнитным перемешиванием: ученые применили сильное электромагнитное перемешивание переменного тока к расплаву сплава (Mg2Si) 20Al80 во время процесса затвердевания, чтобы приготовить градиентный композитный материал, обогащенный Mg2Si, на внешней поверхности. Согласно анализу, когда выполняется электромагнитное перемешивание, расплавленный металл будет подвергаться воздействию электромагнитной силы, направленной к оси в переменном магнитном поле. Из-за низкой проводимости арматуры (возникающего Mg2Si) на нее в основном не влияет электромагнитная сила, направленная к оси, в то время как электромагнитная сила, действующая на расплав, относительно велика, что приводит к несбалансированному силовому полю вокруг арматуры, и усиление подвергается действию Сжимающая сила, оказываемая расплавом металла вдали от центра вала, перемещается наружу в радиальном направлении, тем самым получая градиентный композитный материал с внешней поверхностью, обогащенной и усиленной. Исследование показало, что чем больше напряжение трехфазного переменного тока, подаваемого электромагнитной мешалкой, тем больше сила сдвига между границей раздела жидкость / твердое тело и расплавом, и тем легче проталкивать первичные частицы Mg2Si. к внешней поверхности образца, а сегрегационный слой толще.
- Метод контроля равномерного распределения арматуры: для всего армированного композитного материала очень важно равномерное распределение арматуры в матрице. Усиление перемешивания расплава является основным средством достижения цели гомогенизации арматуры. Вот несколько эффективных методов смешивания:
- Механическое перемешивание: Механическое перемешивание - самый традиционный метод перемешивания расплава. Из-за ограничений материала лопастей мешалки существует несколько примеров метода механического перемешивания, используемого в стальных сплавах. Обратите внимание на механическое перемешивание расплава: ① Разумно выберите материал и форму лопасти мешалки: лопасть мешалки находится в непосредственном контакте с расплавом, что может легко вызвать загрязнение сплава. Для цветных сплавов следует использовать лезвия из цветных металлов или стальные лезвия должны быть покрыты внешним покрытием (например, слоем белой глины). И направление вращения лопасти следует выбирать в соответствии с плотностью частиц арматуры. ②Хорошее перемешивание: следует соответствующим образом контролировать глубину погружения лопастей мешалки для создания стабильного вихря. Встряхивание стержня для перемешивания или неправильных лопастей мешалки увеличивает вероятность отталкивания арматуры расплавом, тем самым ухудшая распределение арматуры в матрице. ③ Время перемешивания: после добавления арматуры время перемешивания должно быть как можно большим, а время ожидания для заливки после перемешивания должно быть как можно более коротким. Существует патент США на «устройство для смешивания твердых частиц с жидкостью», в котором говорится, что композитный материал, производимый с помощью этого устройства, «преодолевает общие дефекты армированных частицами композитных материалов и имеет короткое время смешивания, высокую производительность и бюджетный."
- Перемешивание газа: перемешивание расплава с большим количеством газа, образующегося за счет внешнего газового потока или реакции расплава, также может достичь цели равномерного распределения арматуры в расплаве. Ученые использовали большое количество газа, образующегося в результате реакции на месте, для перемешивания расплава и приготовили композиты Al3Zr (p) .Al2O3 (p) / A356 и (TiB2 + TiAl3) / AlSi6Cu4 с равномерно распределенным армированием.
- Ультразвуковая обработка высокой энергии: ученые добавляют частицы SiC к поверхности расплава сплава ZA27 при 600 ° C и обрабатывают расплав ультразвуком высокой энергии в течение 60-90 секунд, чтобы получить суспензию частиц расплава и общее распределение частиц (как -каст) получается. Однородный композитный материал SiCp / ZA27. Авторы исследования полагают, что затухание с конечной амплитудой ультразвука высокой энергии в расплаве вызывает определенный градиент звукового давления в расплаве с образованием струи жидкости, которая непосредственно покидает торцевую поверхность ультразвукового рупора и образуется во всем расплаве. Циркуляция (т. Е. Эффект акустического тока), скорость акустического тока может в 10-103 раз превышать скорость конвекции расплава. Звуковой поток удаляет загрязнения с поверхности армирующих частиц, а также направляет частицы в глубокую часть расплава и обеспечивает их равномерное диспергирование.
- Рабочие характеристики композитного расплава и ключевые моменты процесса формования: Самая большая разница между композитным расплавом и обычным расплавом заключается во введении твердых частиц армирования. Из-за введения твердых частиц вязкость композитного расплава внезапно и значительно возрастет с появлением следов TiC и TiB2, вызывая резкое изменение вязкости алюминиевого расплава. Ученые указали на теорию формирования отливок. Вязкость жидкого металла оказывает значительное влияние на характеристики потока металла в кристаллизаторе, заполнение формы, плавание газа в жидком металле и подачу металла.
Чтобы получить качественный продукт, процесс формирования композитного расплава с внезапным увеличением вязкости должен иметь дело со следующими двумя проблемами:
- ①Повышение текучести расплава и повышение его наполняемости;
- ② Предотвратить вдыхание газа в расплав и усилить удаление газа из расплава.
Manchang Gui и другие разработали процесс разливки при перепаде давления в вакууме, состоящий из сетчатого фильтра и литника. Композитный расплав заливается непосредственно в форму после прохождения через фильтр. После заполнения расплавленным металлом литник всегда оказывает давление и, наконец, затвердевает, чтобы его можно было подавать в отливку. Особенности этого процесса литья особенно проявляются в:
- ①Основное устранение источника газа и устранение дефектов пор, возникающих в процессе разливки;
- ② Упростите систему заливки, вес системы заливки и вес отливки уменьшены по сравнению с заливкой без вакуума (5-10): 1 (0.5 1.5): 1;
- ③Победя недостаток плохой текучести композитного расплава, он может отливать сложные тонкостенные композитные отливки.
Outlook
Метод литья - один из наиболее перспективных методов получения композиционных материалов. Дальнейшие исследования должны быть сосредоточены на следующих аспектах:
- ① Для матрицы из черного металла выберите арматуру в зависимости от требований к характеристикам композитных материалов;
- ② Разработать методы подготовки, которые легче реализовать и применить в промышленном производстве;
- ③ Значительно снизить затраты на материалы и изготовление композитных изделий;
- ④ Исследование возможности восстановления композитных материалов Технология повторного использования.
Поэтому считается, что метод литья очень поможет в производстве износостойких и жаропрочных композитных изделий.
Композиционный материал с металлической матрицей представляет собой многофазный материал со специальной второй фазой, диспергированной в матрице металла или сплава. Вторая фаза с особыми физико-механическими свойствами значительно увеличивает прочность, твердость, износостойкость, термостойкость и другие свойства материала. Поэтому эту вторую фазу также называют фазой усиления. Фаза армирования обычно делится на фазу армирования частицами и фазу армирования волокнами (нитями). По таким причинам, как цена армирования и композитная технология, большинство композитных материалов, изготовленных методом литья, армированы частицами.
Сохраните источник и адрес этой статьи для перепечатки.: Технология получения композиционного материала с металлической матрицей, армированного частицами методом литья
Минхэ Компания по литью под давлением специализируются на производстве и предоставлении качественных и высокопроизводительных литых деталей (ассортимент металлических деталей для литья под давлением в основном включает Тонкостенное литье под давлением,Литье под давлением,Литье под давлением в холодной камере), Round Service (Служба литья под давлением,Обработка с ЧПУ,Изготовление пресс-форм, Обработка поверхности) .Любое индивидуальное литье под давлением из алюминия, магния или замака / цинка, а также другие требования к отливкам, пожалуйста, свяжитесь с нами.
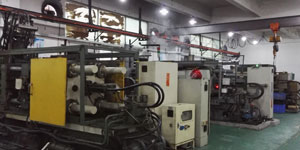
Под контролем ISO9001 и TS 16949, все процессы выполняются на сотнях передовых машин для литья под давлением, 5-осевых станках и других объектах, от струйных до стиральных машин Ultra Sonic. Minghe не только имеет современное оборудование, но и имеет профессиональное оборудование. команда опытных инженеров, операторов и инспекторов для воплощения в жизнь проекта заказчика.
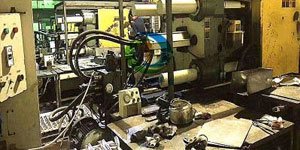
Контрактный производитель отливок под давлением. Возможности включают в себя детали для литья под давлением алюминия с холодной камерой весом от 0.15 фунта. до 6 фунтов, быстрая установка и обработка. Дополнительные услуги включают полировку, вибрацию, удаление заусенцев, дробеструйную очистку, окраску, гальванику, нанесение покрытий, сборку и оснастку. Обрабатываемые материалы включают такие сплавы, как 360, 380, 383 и 413.
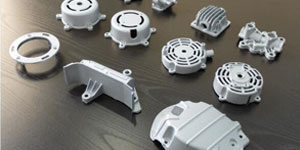
Помощь в проектировании литья цинка под давлением / сопутствующие инженерные услуги. Изготовление на заказ прецизионных отливок из цинка под давлением. Могут изготавливаться миниатюрные отливки, отливки под высоким давлением, отливки в формы с несколькими суппортами, отливки в обычные формы, единичные отливки под давлением и независимые отливки под давлением, а также отливки с герметизацией полости. Отливки могут изготавливаться длиной и шириной до 24 дюймов с допуском +/- 0.0005 дюйма.
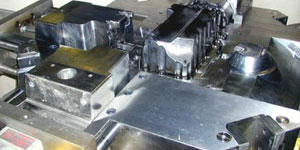
Производитель литья под давлением из магния, сертифицированный по стандарту ISO 9001: 2015. Возможности включают литье под давлением магния под высоким давлением с горячей камерой до 200 тонн и холодной камерой на 3000 тонн, проектирование инструментов, полировку, формование, механическую обработку, порошковую и жидкостную окраску, полный контроль качества с возможностями CMM , сборка, упаковка и доставка.
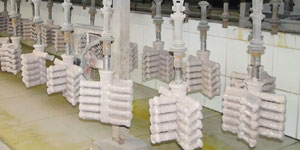
Сертифицирован ITAF16949. Дополнительные услуги трансляции включают инвестиционное литье,литье в песчаные формы,Гравитационное литье, Литье по выплавляемым моделям,Центробежное литье,Вакуумное литье,Постоянное литье формыВозможности включают EDI, техническую поддержку, твердотельное моделирование и вторичную обработку.
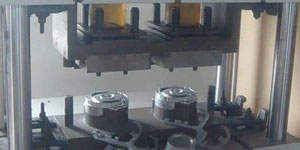
Литейная промышленность Примеры использования запчастей для: автомобилей, велосипедов, самолетов, музыкальных инструментов, судов, оптических устройств, датчиков, моделей, электронных устройств, корпусов, часов, машинного оборудования, двигателей, мебели, ювелирных изделий, приспособлений, телекоммуникаций, освещения, медицинских устройств, фотографических устройств, Роботы, скульптуры, звуковое оборудование, спортивное оборудование, инструменты, игрушки и многое другое.
Что мы можем вам сделать дальше?
∇ Перейти на главную страницу для Литье под давлением Китай
→Литье деталей-Узнай, что мы сделали.
→ Общие советы о Услуги литья под давлением
By Производитель литья под давлением Minghe | Категории: Полезные статьи |Материалы Теги: Литье алюминия, Цинковое литье, Литье магния, Титановое литье, Литье из нержавеющей стали, Латунное литье,Бронзовое литье,Кастинг видео,История компании,Литье алюминия под давлением | Комментарии отключены