Технология выплавки высокопрочного серого чугуна
В этой статье рассказывается, как получить технологию плавки высокопрочного серого чугуна в условиях более высокого углеродного эквивалента и лучших требований к производительности механической обработки в процессе плавки в электропечи, а также как контролировать следовые элементы в материале.
Ключевые слова: серый чугун, углеродный эквивалент, механические свойства, свойства обработки, микроэлементы
Традиционным направлением управления плавкой серого чугуна является низкоуглеродистый высокопрочный чугун (C: 2.7 ~ 3.0, Si: 2.0 ~ 2.3, Mn: 0.9 ~ 1.3). Хотя такие материалы могут соответствовать требованиям к механическим свойствам материала, их характеристики литья и обработки низкие. С развитием и расширением рынка компании все больше и больше литейных изделий с высокой сложностью и высокими требованиями к техническому качеству включается в производственный цикл MINGHE, особенно когда MINGHE использует процесс плавки в электропечи промышленной частоты для замены процесса вагранки.
Получение высокопрочного чугуна с высокоуглеродистым эквивалентом в условиях плавки в электропечи для удовлетворения требований заказчиков было темой исследований в то время. В статье описана технология производства высокопрочного серого чугуна в условиях электропечи.
Факторы, влияющие на характеристики материала
1.1 Влияние углеродного эквивалента на свойства материала
Основными факторами, определяющими свойства серого чугуна, являются морфология графита и свойства металлической матрицы. Когда углеродный эквивалент (CE = C + 1 / 3Si) высокий, количество графита увеличивается, и форма графита ухудшается, когда условия инкубации плохие или присутствуют следы вредных элементов. Такой графит уменьшает эффективную площадь металлической матрицы, которая может выдерживать нагрузку, и вызывает концентрацию напряжений при несении нагрузки, так что прочность металлической матрицы не может использоваться нормально, тем самым снижая прочность чугуна. Среди материалов перлит имеет хорошую прочность и твердость, в то время как феррит имеет более мягкую основу и более низкую прочность. По мере увеличения количества C и Si количество перлита будет уменьшаться, а количество феррита увеличиваться. Следовательно, увеличение углеродного эквивалента повлияет на предел прочности отливок из чугуна и твердость отливки как в форме графита, так и в структуре матрицы. При управлении процессом плавки контроль углеродного эквивалента является очень важным фактором для определения характеристик материала.
1.2 Влияние легирующих элементов на свойства материала
Легирующие элементы в сером чугуне в основном относятся к Mn, Cr, Cu, Sn, Mo и другим элементам, которые способствуют образованию перлита. Содержание этих элементов напрямую влияет на содержание перлита. При этом за счет добавления легирующих элементов он в определенной степени очищается. Добавление графита уменьшает или даже исчезает количество феррита в матрице, в то время как перлит в определенной степени очищается, а феррит в нем упрочнен в твердом растворе за счет определенного количества легирующих элементов, так что чугун всегда имеет более высокие прочностные характеристики. При управлении процессом плавки контроль сплава также является важным средством.
1.3 Влияние коэффициента заряда на материалы
В прошлом мы всегда настаивали на том, что до тех пор, пока химический состав соответствует требованиям спецификации, мы должны иметь возможность получить представление, которое соответствует стандартным механическим свойствам материала, но на самом деле это представление рассматривает только обычные химические свойства. состав, и игнорирует некоторые легирующие элементы и вредные элементы в нем. Роль. Например, чугун является основным источником Ti, поэтому количество используемого чугуна напрямую влияет на содержание Ti в материале и оказывает большое влияние на механические свойства материала. Точно так же стальной лом является источником многих легирующих элементов, поэтому количество лома напрямую влияет на механические свойства чугуна. В первые дни, когда электрическая печь вводилась в эксплуатацию, мы всегда использовали коэффициент загрузки вагранки (чугун: 25 ~ 35%, стальной лом: 30 ~ 35%). В результате механические свойства (предел прочности) материала были очень низкими. Когда количество использованной стали влияет на характеристики чугуна, после корректировки количества лома во времени проблема быстро решается. Следовательно, стальной лом является очень важным параметром контроля в процессе регулирования плавления. Таким образом, соотношение заряда оказывает прямое влияние на механические свойства чугуна и находится в центре внимания при управлении плавкой.
1.4 Влияние микроэлементов на свойства материала
В прошлом мы обращали внимание только на влияние обычных пяти основных элементов на качество чугуна в процессе плавки, в то время как влияние других микроэлементов было только качественным пониманием, но они редко анализировались и обсуждались количественно. В последние годы, в связи с развитием технологии литья «Прогресс», плавильное оборудование постоянно обновляется, а вагранки постепенно заменяются электрическими печами. Хотя электроплавка в вагранке имеет свои несравненные преимущества, плавка в электропечи также теряет некоторые преимущества вагранки, поэтому влияние некоторых микроэлементов на чугун также отражается. Поскольку металлургическая реакция в вагранке очень сильная, шихта находится в сильной окислительной атмосфере, большая ее часть окисляется и выгружается со шлаком, лишь небольшая часть остается в расплавленном чугуне, поэтому некоторые из них отрицательно влияют на литье В ходе металлургического процесса вагранки микроэлементы обычно не оказывают вредного воздействия на чугун. В процессе плавки в вагранке часть азота в коксе и азота (N2) в воздухе растворяется в расплавленном железе в форме атомов при высоких температурах, что делает содержание азота в расплавленном железе относительно высоким.
Согласно статистическим данным, с момента пуска электропечи в эксплуатацию количество отходов, вызванных высоким содержанием свинца, и списанный жидкий чугун из-за того, что содержание свинца было слишком высоким, чтобы его можно было регулировать, составили не менее 100 тонн, а количество неквалифицированной продукции должно было быть Недостаточное содержание азота также было довольно высоким, что нанесло компании большие экономические убытки.
Основываясь на нашем многолетнем опыте и теории плавки в электропечах, я считаю, что ключевыми микроэлементами в процессе плавки в электропечах являются в основном N, Pb и Ti. Воздействие этих элементов на серый чугун в основном следующее:
Вести
Когда содержание свинца в расплавленном чугуне высокое (> 20 частей на миллион), особенно при взаимодействии с более высоким содержанием водорода, легко образовывать графит Видманштеттена в отливках с толстыми сечениями. Это связано с тем, что смоляной песок имеет хорошие теплоизоляционные свойства, а охлаждение расплавленного чугуна в форме происходит медленнее (эта тенденция более очевидна для толстых участков), расплавленное железо остается в жидком состоянии в течение более длительного времени и затвердевает. расплавленное железо ближе к состоянию затвердевания в равновесном состоянии из-за действия свинца и водорода. Когда отливка этого типа затвердевает и продолжает охлаждаться, углерод в аустените выпадает в осадок и в твердом состоянии становится вторичным графитом. В нормальных условиях вторичный графит только увеличивает толщину чешуек эвтектического графита, что не оказывает большого влияния на механические свойства. Однако при высоком содержании азота и водорода поверхностная энергия графита на одной и той же фиксированной кристаллической плоскости аустенита будет уменьшена, и вторичный графит будет расти вдоль определенной кристаллической плоскости аустенита и распространяться в металлическую матрицу. Понаблюдайте под микроскопом. Многие мелкие заусенцы, похожие на чешуйки графита, растут на стороне чешуек графита, обычно известных как графитовые волоски, что является причиной образования графита Видмана. Алюминий в чугуне может способствовать поглощению жидким чугуном водорода и увеличению его содержания. Следовательно, алюминий также косвенно влияет на образование видманштеттенского графита.
Когда графит Видманштеттена появляется в чугуне, это сильно влияет на его механические свойства, особенно на прочность и твердость, которые в тяжелых случаях могут быть снижены примерно на 50%.
Графит Видмана имеет следующие металлографические характеристики:
- 1) На 100-кратной микрофотографии видно множество мелких шиповидных чешуек графита, прикрепленных к крупной чешуйке графита, которая представляет собой графит Видманштеттена.
- 2) отношения общего кристаллического графита связаны друг с другом.
- 3) Когда графитовая сетка Видманштеттена проникает в матрицу при комнатной температуре, она становится хрупкой поверхностью матрицы, что значительно снижает механические свойства серого чугуна. Но с точки зрения поперечного сечения трещины излома по-прежнему проходят вдоль графита, похожего на стружку.
Азот
Достаточное количество азота может способствовать зарождению графита, стабилизировать перлит, улучшить структуру серого чугуна и улучшить характеристики серого чугуна.
Азот оказывает на серый чугун два основных влияния. Первое - это влияние на форму графита, а второе - на структуру матрицы. Влияние азота на морфологию графита - очень сложный процесс. В основном проявляется в: влиянии адсорбционного слоя на поверхность графита и влиянии размера эвтектической группы. Поскольку азот почти нерастворим в графите, азот непрерывно адсорбируется на фронте роста графита и на обеих сторонах графита во время процесса эвтектического затвердевания, что приводит к увеличению окружающей концентрации графита во время процесса осаждения, особенно когда графит распространяется в расплавленное железо. На вершине это влияет на рост графита на границе раздела жидкость-твердое тело. В процессе эвтектического роста наблюдается значительная разница в распределении концентрации азота на вершине и обеих сторонах графитового листа. Адсорбционный слой атомов азота на поверхности графита может препятствовать диффузии атомов углерода к поверхности графита. Когда концентрация азота на фронте графита выше, чем на двух сторонах, скорость роста графита в продольном направлении снижается. Напротив, боковой рост становится легче, и в результате графит становится короче и толще. В то же время, поскольку в процессе роста графита всегда есть дефекты, часть атомов азота адсорбируется в месте дефекта и не может диффундировать, а граница зерен будет асимметрично наклонена на фронте роста графита, и остальное все равно будет расти в исходном направлении. Графит дает ответвления, и увеличение количества ответвлений графита - еще одна причина, по которой графит становится короче. Таким образом, за счет улучшения структуры графита, эффект расщепления на матричную структуру снижается, что способствует улучшению характеристик чугуна.
Влияние азота на структуру матрицы заключается в том, что он является элементом, стабилизирующим перлит. Увеличение содержания азота снижает температуру эвтектоидного превращения чугуна. Следовательно, когда в сером чугуне содержится определенное количество азота, степень переохлаждения эвтектоидного превращения может быть увеличена, тем самым улучшая перлит. С другой стороны, поскольку атомный радиус азота меньше, чем у углерода и железа, его можно использовать в качестве межузельных атомов для растворения в феррите и цементите, вызывая искажение его кристаллической решетки. По двум указанным выше причинам азот может оказывать упрочняющее действие на матрицу.
Хотя азот может улучшить характеристики серого чугуна, когда он превышает определенное количество, образуются азотные поры и микротрещины, как показано на рисунке 2, поэтому контроль азота следует контролировать в определенном диапазоне. Обычно 70–120 ppm, когда оно превышает 180 ppm, характеристики чугуна резко падают.
Ti - вредный элемент в чугуне. Причина в том, что титан имеет сильное сродство с азотом. Когда содержание титана в сером чугуне высокое, это не способствует укрепляющему эффекту азота. Во-первых, он образует соединение TiN с азотом, которое восстанавливается. Фактически, именно потому, что этот свободный азот оказывает упрочняющее действие твердого раствора на серый чугун. Следовательно, уровень содержания титана косвенно влияет на характеристики серого чугуна.
Технология контроля плавления
2.1 Выбор химического состава материала
Благодаря вышеупомянутому анализу, контроль химического состава очень важен в технологии плавки, и он является основой контроля плавки. Следовательно, разумный химический состав является основой для обеспечения рабочих характеристик материала. Обычно контроль состава высокопрочного чугуна (предел прочности ≥300 Н / мм2) в основном включает в себя др. C, Si, Mn, P, S, Cu, Cr, Pb, N
2.3 Технология контроля микроэлементов
При фактическом управлении технологическим процессом, основанном на анализе шихты, подтверждается, что источником свинца является в основном стальной лом. Следовательно, контроль содержания свинца в сырье в основном направлен на контроль включений Pb в стальном ломе, а содержание свинца обычно регулируется ниже 15 частей на миллион. Если содержание свинца в неочищенном расплавленном чугуне> 20 частей на миллион, во время инкубационной обработки необходимо провести специальную обработку для разрушения.
Поскольку Ti в основном получают из чушкового чугуна, контроль Ti в основном направлен на контроль передельного чугуна. С одной стороны, необходимо предъявлять жесткие требования к содержанию Ti в чугуне при покупке. Обычно требуется, чтобы содержание титана в передельном чугуне составляло: Ti <0.8%, и другой аспект заключается в корректировке количества использования во времени в соответствии с содержанием титана в передельном чугуне.
В основном поступает из материалов повторного науглероживания и стального лома, поэтому контроль N в основном осуществляется для контроля материалов повторного науглероживания и стального лома. Однако, как упоминалось выше, слишком низкие и слишком высокие значения имеют отрицательную сторону для характеристик серого чугуна, поэтому содержание N Диапазон регулирования обычно составляет: 70 ~ 120 ppm, но содержание N должно разумно совпадать с содержание Ti. Обычно соотношение между N и Ti составляет: N: Ti = 1: 3.42, то есть 0.01% Ti может поглощать 30 частей на миллион азота. Общее рекомендуемое количество азота во время производства: N = 0.006 ~ 0.01 + Ti / 3.42.
2.4 Технология управления процессом плавки
1) Технология посева
Целью инокуляции является стимулирование графитизации, уменьшение склонности к побелению и снижение чувствительности торцевой поверхности; контролировать морфологию графита и исключить переохлаждение графита; соответствующим образом увеличить количество эвтектических кластеров и способствовать образованию чешуйчатого перлита, чтобы улучшить прочностные характеристики чугуна и других рабочих целей.
Влияние температуры жидкого чугуна на модифицирование и регулирование температуры жидкого чугуна оказывают значительное влияние на модифицирование. Повышение температуры перегрева расплавленного чугуна в определенном диапазоне и поддержание ее в течение определенного периода времени может привести к тому, что нерастворенные частицы графита останутся в расплавленном чугуне, который может полностью раствориться в расплавленном чугуне, чтобы исключить генетическое влияние чугуна и чугуна. дать полную игру эффекту прививки модификатора, улучшить способность к плодородию расплавленного железа. При управлении процессом температура перегрева увеличивается до 1500 ~ 1520 ℃, а температура инокуляции регулируется на уровне 1420 ~ 1450 ℃.
Размер частиц модификатора является важным показателем состояния модификатора и имеет большое влияние на эффект модификатора. Если размер частиц слишком мелкий, они легко диспергируются или окисляются в расплавленный шлак и теряют свой эффект. Если размер частиц слишком большой, модификатор не расплавится или не растворится полностью. Он не только не может полностью проявить свой эффект прививки, но и вызовет сегрегацию, твердые пятна, переохлажденный графит и другие дефекты. Следовательно, размер частиц модификатора следует контролировать в пределах 2 ~ 5 мм, насколько это возможно. Обеспечьте инкубационный эффект.
При контроле процесса процесс инокуляции в основном инокулируется в инкубационный резервуар, так что заливка упаковки отливок может быть в основном завершена до того, как инкубация снизится. Но для относительно больших деталей и деталей, отлитых с помощью двойного ковша, он не может соответствовать требованиям. Поэтому принят метод поздней модифицирования: то есть плавающая модификация кремния выполняется в ковше перед разливкой отливки (количество модифицирования составляет 0.1%), что снижает или вовсе не снижает снижение прививки и улучшает эффект модифицирования.
2) Обработка легированием
При легировании в обычный чугун добавляется небольшое количество легирующих элементов для улучшения механических свойств серого чугуна. При управлении процессом плавки сплавы добавляются в основном для деталей, которые заказчики требуют закалки, и для деталей с относительно толстыми направляющими рельсами, добавляются основные легирующие элементы и количество добавок.
Это в определенной степени обеспечивает снижение характеристик из-за увеличения значения CE, а для закаленных деталей улучшается способность к закалке во время закалки. Обеспечьте глубину закалки.
Во время процесса подачи и плавки порядок подачи основного элемента управления на этом этапе состоит в том, чтобы подавать стальной лом, механическое железо и чушковый чугун в порядке приоритета. Чтобы уменьшить потери при горении легирующих элементов, в конце следует добавлять ферросплав. Когда холодный материал полностью очищен, температура повышается до 1450 ℃. Это точка А. Если она ниже 1450 ° C, существует риск неполного растворения науглероживающего агента или ферросплава.
В пунктах AB следует провести следующие процедуры:
- Измерение температуры;
- Отвод шлака;
- Отбор проб и анализ химического состава;
- Анализировать обычные элементы и микроэлементы с помощью термоспектрометра;
- Возьмите образец треугольника, чтобы измерить значение CW;
- После корректировки расплавленного чугуна в соответствии с различными результатами испытаний, продолжайте подачу питания в течение 10 минут, а затем повторно пробы и проанализируйте. Убедившись, что все данные в норме, продолжайте повышать температуру примерно до 1500 ° C, то есть до точки C. В секции CD дайте расплавленному чугуну постоять в течение 5-10 минут, а затем возьмите образец треугольника, чтобы проверить Значение CW. После измерения температуры подготовьте утюг к постукиванию.
Контрольный образец треугольной формы
Для разных марок определите контрольный диапазон белого горла (CW) для различных треугольных испытательных блоков и определите качество расплавленного чугуна в сочетании с анализом состава перед печью.
Заключение
Вышеупомянутая технология выплавки серого чугуна успешно применялась в CSMF в течение 8 лет с 1996 по 2003 год. CE отливок контролируется в соответствии с предпосылкой 3.6 ~ 3.9, будь то индекс прочности на разрыв или индекс физической твердости ( В частности, часть твердости направляющего рельса деталей станков соответствует требованиям, что значительно улучшает режущие характеристики отливки.Показано, что эта технология является завершенной технологией, и ее контрольные точки следующие:
- 3.1 Контроль химического состава материалов
- 3.2 Определение коэффициента заряда
- 3.3 Технология контроля микроэлементов
- 3.4 Контроль процесса посевной обработки
- 3.5 Обработка легированием
- 3.6 Контроль температуры в процессе плавки
- 3.7 Контроль треугольного испытательного образца
Сохраните источник и адрес этой статьи для перепечатки.: Технология выплавки высокопрочного серого чугуна
Минхэ Компания по литью под давлением специализируются на производстве и предоставлении качественных и высокопроизводительных литых деталей (ассортимент металлических деталей для литья под давлением в основном включает Тонкостенное литье под давлением,Литье под давлением,Литье под давлением в холодной камере), Round Service (Служба литья под давлением,Обработка с ЧПУ,Изготовление пресс-форм, Обработка поверхности) .Любое индивидуальное литье под давлением из алюминия, магния или замака / цинка, а также другие требования к отливкам, пожалуйста, свяжитесь с нами.
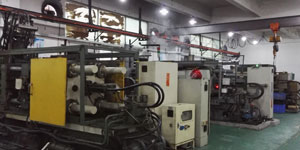
Под контролем ISO9001 и TS 16949, все процессы выполняются на сотнях передовых машин для литья под давлением, 5-осевых станках и других объектах, от струйных до стиральных машин Ultra Sonic. Minghe не только имеет современное оборудование, но и имеет профессиональное оборудование. команда опытных инженеров, операторов и инспекторов для воплощения в жизнь проекта заказчика.
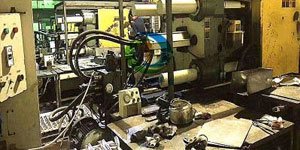
Контрактный производитель отливок под давлением. Возможности включают в себя детали для литья под давлением алюминия с холодной камерой весом от 0.15 фунта. до 6 фунтов, быстрая установка и обработка. Дополнительные услуги включают полировку, вибрацию, удаление заусенцев, дробеструйную очистку, окраску, гальванику, нанесение покрытий, сборку и оснастку. Обрабатываемые материалы включают такие сплавы, как 360, 380, 383 и 413.
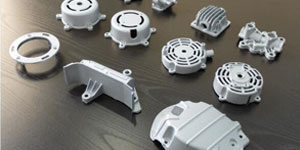
Помощь в проектировании литья цинка под давлением / сопутствующие инженерные услуги. Изготовление на заказ прецизионных отливок из цинка под давлением. Могут изготавливаться миниатюрные отливки, отливки под высоким давлением, отливки в формы с несколькими суппортами, отливки в обычные формы, единичные отливки под давлением и независимые отливки под давлением, а также отливки с герметизацией полости. Отливки могут изготавливаться длиной и шириной до 24 дюймов с допуском +/- 0.0005 дюйма.
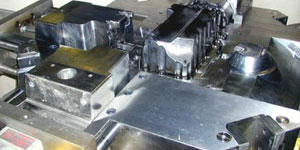
Производитель литья под давлением из магния, сертифицированный по стандарту ISO 9001: 2015. Возможности включают литье под давлением магния под высоким давлением с горячей камерой до 200 тонн и холодной камерой на 3000 тонн, проектирование инструментов, полировку, формование, механическую обработку, порошковую и жидкостную окраску, полный контроль качества с возможностями CMM , сборка, упаковка и доставка.
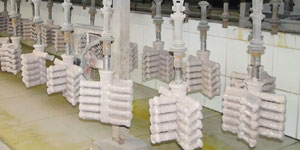
Сертифицирован ITAF16949. Дополнительные услуги трансляции включают инвестиционное литье,литье в песчаные формы,Гравитационное литье, Литье по выплавляемым моделям,Центробежное литье,Вакуумное литье,Постоянное литье формыВозможности включают EDI, техническую поддержку, твердотельное моделирование и вторичную обработку.
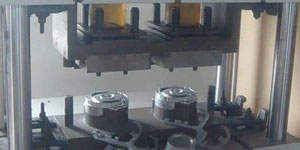
Литейная промышленность Примеры использования запчастей для: автомобилей, велосипедов, самолетов, музыкальных инструментов, судов, оптических устройств, датчиков, моделей, электронных устройств, корпусов, часов, машинного оборудования, двигателей, мебели, ювелирных изделий, приспособлений, телекоммуникаций, освещения, медицинских устройств, фотографических устройств, Роботы, скульптуры, звуковое оборудование, спортивное оборудование, инструменты, игрушки и многое другое.
Что мы можем вам сделать дальше?
∇ Перейти на главную страницу для Литье под давлением Китай
→Литье деталей-Узнай, что мы сделали.
→ Общие советы о Услуги литья под давлением
By Производитель литья под давлением Minghe | Категории: Полезные статьи |Материалы Теги: Литье алюминия, Цинковое литье, Литье магния, Титановое литье, Литье из нержавеющей стали, Латунное литье,Бронзовое литье,Кастинг видео,История компании,Литье алюминия под давлением | Комментарии отключены