Контроль процесса производства вермикулярного железа
По сравнению с серым чугуном прочность на разрыв вермикулярного чугуна увеличена как минимум на 70%, модуль упругости увеличен на 35%, а усталостная прочность почти удвоена. По сравнению с алюминиевым сплавом прочность и жесткость вермикулярного чугуна в два раза выше, а усталостная прочность в два раза выше. Эти характеристики вермикулярного железа позволяют двигателю улучшить соотношение мощности и веса и повысить давление в цилиндре. Повышение давления в цилиндрах - ключ к оптимальной производительности дизельного двигателя следующего поколения с прямым впрыском. Чтобы удовлетворить повсеместное применение вермикулярного железа, литейная промышленность в настоящее время активно готовится, вкладывает значительные средства и перестраивает новые процессы, чтобы сделать производство вермикулярного железа стабильным и надежным.
Для двигателей из вермикулярного чугуна от прототипа до серийного производства решающим фактором является риск качества. Для высококачественного вермикулярного железа стабильная зона очень мала, всего лишь в пределах 0.008% содержания магния. Незначительное количество, например потеря 0.001% магния, приведет к образованию чешуек графита, что приведет к снижению механических свойств на 25-40%. В статье описывается система управления технологическим процессом, основанная на методах термического анализа. Система измеряет потери магния и регулирует состояние расплавленного чугуна в режиме онлайн, чтобы предотвратить образование чешуйчатого графита. Этот метод измерения и регулировки в режиме онлайн снижает нестабильность в процессе производства вермикулярного железа до минимума и принципиально устраняет риск качества, связанный с производством вермикулярного железа.
Спрос на высокую мощность, высокий крутящий момент, низкий уровень выбросов выхлопных газов и снижение расхода топлива продолжает расти. Это вынуждает конструкторов дизельных двигателей большой мощности увеличивать пиковое давление зажигания, что значительно увеличивает тепловую и механическую нагрузку двигателя. Тепловая нагрузка и механическая нагрузка увеличиваются одновременно, так что обычные двигатели из чугуна и легированного чугуна (CrMo), используемые в настоящее время, достигли или превысили верхний предел своего использования. Производителям двигателей нужны материалы с более высокой прочностью и лучшей термостойкостью.
Вермикулярное железо быстро стало предпочтительным материалом для людей. Это значительно повышает надежность блока цилиндров, головки блока цилиндров и гильзы цилиндров двигателей грузовых автомобилей нового поколения. Для достижения наилучшего сочетания различных свойств (таких как литейные свойства, свойства механической обработки, теплопроводность и механические свойства) эти детали должны изготавливаться со степенью сфероидизации от 0% до 20% (скорость ползучести от 80% до 100%. ) Изготовлен из вермикулярного железа. Если уровень сфероидизации превышает 20%, это вызовет ряд неблагоприятных факторов. Например, величина усадки слишком велика, а детали сложной формы, такие как головки цилиндров, особенно склонны к усадке. Другой пример - снижение срока службы инструмента из-за чрезмерного износа во время обработки. Также происходит значительное снижение теплопроводности, вызывая термическое напряжение и так далее. На другом конце вермикулярного чугуна появление чешуйчатого графита приведет к линейному ухудшению механических свойств, в результате чего двигатель не сможет соответствовать новым требованиям. Таким образом, чтобы удовлетворить потребности двигателей грузовых автомобилей нового поколения, степень сфероидизации высокопрочного вермикулярного железа должна составлять от 0% до 20% (то есть скорость ползучести составляет более 80% без хлопьев).
Использовать ли контроль производственного процесса или нет, зависит от годового выпуска продукта, сложности продукта и допустимого диапазона изменений металлографической структуры. Как показано на Рисунке 1, относительно простые детали небольшого объема, такие как изложницы, обычно можно изготавливать обычными методами литья. Управление процессом обычно не требуется, и это экономически неэффективно. Когда годовой объем выпуска таких компонентов, как выхлопные трубы, втулки кривошипа и кронштейны, увеличивается, имеет смысл ввести управление технологическим процессом. Хотя этот тип продукта имеет большой годовой объем производства, годовой тоннаж отливки невысок. Требования к металлографической структуре не очень строгие, что позволяет достичь степени сфероидизации до 50%. Кроме того, из-за небольшого объема обработки таких деталей увеличение количества титана, которое может быть добавлено при производстве, может позволить расширить контролируемый диапазон. Для этого типа продуктов обычные методы литья и строгая подготовка обычно подходят для производства вермикулярного чугуна. Но с точки зрения контроля качества контроль процесса должен быть более надежным. Аналогичным образом, управление технологическим процессом также обеспечивает гарантию производства крупных блоков судовых двигателей и головок цилиндров. Несмотря на то, что большие размеры и малое количество продукции способствуют производству продукции, экономических потерь, вызванных продуктами, превышающими стандарты, достаточно, чтобы добавить систему управления технологическим процессом.
В области управления технологическим процессом больше всего нуждаются блоки цилиндров автомобильных двигателей, головки цилиндров и тормозные диски с большим годовым объемом производства, высокой сложностью и строгими техническими требованиями. Годовой объем производства и годовой тоннаж этих продуктов очень высок. Они сложны по размеру, требуют металлографической структуры и имеют тенденцию к образованию усадочных полостей. Эти продукты не должны иметь рисков для качества, иначе потери будут очень серьезными.
Строгие требования к характеристикам блока цилиндров, головки блока цилиндров и седла цилиндра заложили основу для технических характеристик продукции. Чтобы получить наилучшие комплексные характеристики литья, обрабатываемости и механических свойств, степень сфероидизации должна находиться в диапазоне от 0% до 20% во всех ключевых частях детали. Что еще более важно, необходимо полностью избегать использования чешуйчатого графита, чтобы предотвратить повреждение деталей из-за местной слабости. Для достижения хорошей механической аддитивности количество свободных карбидов должно быть сведено к минимуму. Поэтому ни в коем случае нельзя добавлять титан. Наконец, с производственной точки зрения литейному производству необходим стабильный и надежный процесс, обеспечивающий минимальный процент брака, обусловленный металлографической структурой. Производители автомобильной промышленности требуют гарантии качества, и 100% отливок должны соответствовать металлографическим требованиям. Крупномасштабное и надежное производство блоков цилиндров, головок цилиндров и седел цилиндров требует точного анализа и корректировки жидкого чугуна в режиме онлайн для устранения колебаний в процессе перед разливкой.
Стабильность вермикулярного железа
Причина, по которой уплотненное железо не используется в больших количествах для производства сложных деталей (таких как блоки двигателя), заключается в том, что стабильная площадь уплотненного железа слишком мала, чтобы гарантировать отсутствие риска при производстве. Вообще говоря, эта стабильная зона охватывает только область с содержанием магния 0.008%, как показано на Рисунке 2. Размер и положение платформы в стабильной зоне меняются в зависимости от продукта. Фактически, доступный диапазон магния меньше этого. Потому что каждые 5 минут активный магний будет сжигать 0.001%. Начальная точка разливки расплавленного чугуна должна быть достаточно далеко от точки поворота прессованного чугуна до серого чугуна, чтобы гарантировать, что чешуйчатый графит не появится в окончательной отливке. При добавлении магния в расплавленный чугун чешуйчатый графит появится примерно через 15 минут.
Начальная точка не должна находиться слишком близко к правой стороне стабильной платформы (высокое содержание магния), в противном случае это приведет к образованию большого количества сфероидального графита в более тонкой части и в части с быстрым охлаждением.
Помимо небольшой доступной площади платформы, платформа всегда находится в движении. Если содержание активного кислорода и серы будет высоким, они будут потреблять больше активного магния, и вся платформа переместится вправо (высокое содержание магния). И наоборот, если содержание активного кислорода и серы низкое, платформа переместится влево (низкое содержание магния). Изменения в составе сырья, чистоте, степени окисления и влажности и т. Д. Лишают людей возможности контролировать вермикулярное железо с фиксированным диапазоном химического состава.
Хотя преобразование вермикулярного чугуна в серый чугун требует только снижения активного магния на 0.001%, сжигание магния не приводит к превращению всей детали в чешуйчатый графит. Когда активного магния недостаточно, графит сначала образует хлопья и расширяется наружу по мере затвердевания, а магний проседает и концентрируется на переднем конце границы раздела твердое тело-жидкость. Если исходное количество активного магния является подходящим, вермикулярный графит будет образовываться на границе эвтектики, как показано на рисунке 3. Чешуйчатый графит сначала проявляется в виде рассеянных чешуйчатых графитовых пятен. В отличие от всего обычного чешуйчатого графита, эти изолированные пятна чешуйчатого графита трудно обнаружить с помощью ультразвука. Вероятность их сканирования ультразвуком невелика.
Чувствительность магния к вермикулярному чугуну может быть показана на рисунке 4. В ковше для чугуна достаточно добавить 10 граммов магния, и пятна чешуйчатого графита, диспергированные в испытательном образце Φ25, могут полностью превратиться в вермикулярный графит. Предел прочности на разрыв испытательного стержня с пятнами чешуйчатого графита составляет всего 300 МПа, в то время как предел прочности такого же испытательного стержня с полной утечкой достигает 450 МПа.
Модификатор также очень чувствителен к стабильной платформе вермикулярного железа, как показано на рисунке 5: добавление 80 граммов модификатора к одной тонне расплавленного железа увеличит степень сфероидизации в испытательном стержне Φ25 с 3% до 21%. Количество прививки велико, а кристаллических зародышей много, что способствует образованию сферического графита. Это поднимает платформу вермикулярного железа в направлении высокой скорости сфероидизации. Низкая скорость инокуляции заставляет платформу опускаться. Многочисленные факторы, такие как температура перегрева расплавленного чугуна, время выдержки, химический состав сырья, тип модификатора и количество прививки, будут влиять на положение платформы вермикулярного железа.
Самым основным требованием к любой технологии управления технологическим процессом является точное измерение и анализ состояния расплавленного чугуна. Для вермикулярного чугуна надежный производственный контроль требует одновременного измерения критической точки активного магния при переходе от ползучести к золе, степени последующего выгорания магния и степени инокуляции.
Образец для термического анализа массой 200 грамм получают, вставляя зонд Xinte в расплавленный чугун после сфероидизации и инокуляции. Во время трехсекундного процесса введения стенка зонда и расплавленный чугун достигают состояния теплового равновесия. В отличие от обычной чашки для термического анализа, этот тонкостенный пробоотборник не только гарантирует каждый раз один и тот же объем образца, но также предотвращает окисление расплавленного чугуна, наливаемого в чашку для образца. Измерение перегрева является более точным, поскольку в обычном термическом анализе нет такого явления, как явление сильной конденсации.
Как показано на рис. 6а, зонд Xinte изготовлен из штампованной вытянутой листовой стали. По сути, это сферический контейнер. Тонкая стальная стенка, содержащая расплавленный чугун, имеет изоляционный слой, напоминающий вакуумную колбу. Толщина изоляционного слоя увеличена симметрично в соответствии с направлением высоты для обеспечения равномерного отвода тепла и охлаждения в окружающую среду, а содержание железа в нем и воды в нем близко к затвердеванию сферического тела. В защитной трубке зонда есть две термопары N-типа. Термопару можно вынимать после каждого измерения и использовать повторно более 100 раз. Одна из двух термопар расположена на дне емкости, а другая - в тепловом центре емкости. Поскольку контейнер имеет сферическую форму и свободно подвешен (это отличается от обычного стакана для образцов для термического анализа, опирающегося на теплопоглощающий кронштейн), расплавленное железо создает в контейнере равномерный тепловой поток, как показано на рисунке 6b. Этот тепловой поток вызывает постоянный обмен жидкого чугуна в контейнере, образуя перегородку для потока на дне зонда.
Чтобы имитировать естественную потерю расплавленного железа во время разливки, на стенке зонда имеется покрытие, которое вступает в реакцию с активным магнием. Расплавленное железо течет вдоль стены с покрытием под действием теплового потока. После реакции содержание магния в расплавленном чугуне уменьшается и накапливается в отсеке на дне емкости. Прямо говоря: термопара в центре зонда измеряет количество непрореагировавшего расплавленного железа, которое является начальным состоянием разливки; термопара внизу измеряет состояние после окончания заливки. Состав реактивного покрытия очень специфический. Необходимо точно гарантировать, что расплавленный чугун, накопленный в отсеке, на 0.003% менее активен, чем центральный расплавленный чугун. Следовательно, если начальное содержание магния слишком близко к точке поворота ползучего пепла, расплавленный чугун в отсеке будет образовывать серое чугун, что будет измеряться термопарой в этой зоне. Таким образом, в начале литья мастерская может добавить больше магния, чтобы компенсировать неизбежные потери магния при горении.
Если термопара внизу показывает кривую вермикулярного чугуна, это указывает на то, что начальное содержание магния достаточно высоко, чтобы чешуйчатый графит отсутствовал после окончания литья.
Рисунок 7 представляет собой диаграмму эрозии зонда Xinte в поперечном сечении после измерения образца. На рисунке вы можете ясно видеть зону перегородки, основную зону образца и защитную трубку термопары. Когда содержание активного магния уменьшается на 0.003%, в зоне разделения образуются D-образная графитовая и ферритная матрица. Размер области чешуйчатого графита внизу напрямую отражает исходное содержание магния в основной области образца. Размер этой зоны можно рассчитать по теплу, выделяемому внизу. Коэффициент регрессии дисперсии между тепловыделением и размером перегородки превышает 0.9, что доказывает, что связь между ними очень близка. Выделяемое тепло рассчитывается путем интегрирования кривой охлаждения по времени. Этот метод измерения состояния расплавленного чугуна при токе и в конце разливки одновременно обеспечивает точность определения содержания магния перед разливкой.
Поскольку вермикулярное железо очень чувствительно к сфероидизирующим агентам и модификаторам, для литейных предприятий невозможно использовать чрезмерные методы обработки, используемые при производстве серого чугуна и высокопрочного чугуна. Как показано на Рисунке 8, из-за своей чувствительности вермикулярное железо стабильно только в квадратном окне, а не только в области магниевой платформы. Надежный процесс производства вермикулярного железа должен контролировать сфероидизацию и инокуляцию от начала до конца, чтобы металлографическая структура соответствовала поставленной цели.
Независимо от того, сколько усилий прилагается, независимо от того, насколько строгое управление, колебания расплавленного чугуна всегда неизбежны. Не говоря уже о том, насколько точно люди знают об обработке расплавленным чугуном, одностадийные методы обработки, такие как сэндвич-метод, не могут гарантировать, что каждая обработка попадет в узкое окно с чугуном. Многочисленные производственные переменные, такие как соотношение компонентов, температура печи, время выдержки, степень предварительного нагрева ковша для жидкого чугуна, скорость выпуска, положение выпуска выпуска жидкого чугуна (внутреннее или внешнее измерение), вес выпуска расплавленного чугуна, состояние мешка из сплава, сфероидизирующий агент. фактическое содержание магния в (PeSiMg), расположение сплава каждого слоя в многослойном методе, а также степень покрытия опилками железного лома и т. д. - все это влияет на абсорбцию магния. В дополнение к этим факторам, содержание активного кислорода и активной серы также изменит размер и положение окна для червеобразного железа. Изменения времени пребывания расплавленного чугуна в ковше, времени транспортировки и времени разливки изменяют доступное время горения.
Однако наиболее непредсказуемыми факторами колебаний являются ошибки оператора или различия между операторами из-за разных привычек работы.
При крупномасштабном массовом производстве единственным безопасным способом является измерение характеристик затвердевания расплавленного чугуна после обработки. Таким образом, были всесторонне измерены, проанализированы и рассмотрены различные факторы, влияющие на размер, положение и поглощение сплава окном из вермикулярного железа. Затем можно добавить соответствующее количество магния и модификатора. Каждый ковш жидкого чугуна разливается после доведения до идеального состояния. Этот двухэтапный метод управления процессом измерения и регулировки сводит к минимуму изменчивость производства и полностью исключает риск образования чешуек графита в отливке.
Управление технологическим процессом производства вермикулярного чугуна с помощью ковша для горячего металла
Как показано на рисунке 9, управление процессом начинается с термического анализа расплавленного чугуна после начальной сфероидизации и обработки модифицированием. Согласно результатам анализа, устройство подачи проволоки автоматически отображает длину проволоки, в которую необходимо добавить магний и модификатор, и ожидает, пока оператор запустит ее. Когда линия подачи завершена, ковш немедленно отправляется на линию разливки. Весь процесс измерения и настройки занимает около трех минут. В течение этого периода цех может выполнять обычные операции перед заливкой, такие как удаление шлака. Это обеспечивает непрерывность линии разливки.
С эксплуатационной точки зрения сырой расплавленный чугун не содержит магния, и его инкубационная способность также очень ограничена. После сфероидизации и инокуляции магний и модификаторы сначала поглощают активный кислород и серу в расплавленном чугуне, а затем «перескакивают» расплавленное железо в определенное положение на доске. В примере на Рисунке 10 магниевый индекс и индекс модифицирования расплавленного чугуна составляют 65 и 45 соответственно. Поскольку основные параметры изменения теневого производства отображаются в жидком чугуне после измерения и обработки, результаты термического анализа напрямую отражают текущее состояние жидкого чугуна. Все, что осталось, - это добавить соответствующее количество магния и модификатора, чтобы поднять расплавленный чугун из его текущего положения в требуемую начальную точку. В примере на Рисунке 10 сначала добавляются семь единиц магниевых кабелей, а затем 23 единиц модифицирующих кабелей. Соответствующее соотношение между единицей индекса и длиной кабеля калибруется в зависимости от продукта и мастерской и составляется в программе. Исходя из прошлого опыта производства почти 100,000 5 отливок из вермикулярного чугуна, среднее количество добавляемого магниевого кабеля составляет 12 метров на тонну. Он содержит 50 граммов магния на метр, и при расчете на степень абсорбции 30% количество магния, добавленного на тонну расплавленного железа, составляет всего XNUMX граммов. Поскольку добавляемое количество очень мало, и основные изменения уже произошли при первоначальном лечении, корректировка очень эффективна и надежна. После настройки нет необходимости проводить термический анализ.
При начальной обработке состояние после обработки должно быть ниже, чем начальное положение заливки, так что даже если все факторы, которые благоприятствуют абсорбции магния и модификатора, достигают оптимального значения, расплавленный чугун достигнет только начального состояния заливки. . За исключением случаев чрезмерной обработки, расплавленный чугун после обработки не находится в состоянии серого чугуна и белого чугуна. Чтобы сделать процесс разливки более эффективным, на блок-схеме процесса отображается индекс магния и индекс модифицирования каждого ковша с расплавленным чугуном. В соответствии с изменяющейся тенденцией блок-схемы оператор может регулировать количество жидкого чугуна, добавляемого в следующий ковш. Значение углеродного эквивалента также отображается на экране. Эти данные были отредактированы и сохранены в производственном журнале, чтобы их можно было отслеживать и исчерпывающе, а также они соответствовали требованиям обеспечения качества.
Хотя термический анализ и последующие регулировки могут обеспечить производство вермикулярного чугуна, рекомендуется брать пробы из литниковой чашки окончательной отливки для анализа. По сравнению с обычным контролем качества, этот результат термического анализа позволяет проводить онлайн-анализ и при необходимости классифицировать отливки. Моделирование потерь магния в зонде делает этот метод «неразрушающего» контроля более эффективным, чем металлографические и ультразвуковые методы. Поскольку этот метод измеряет больший размер образца, он также определяет, как расплавленное железо затвердеет в следующие 10-15 минут.
Подводить итоги
Выбор системы управления технологическим процессом зависит от продукта и процесса литья. При литье сложных изделий, таких как крышка двигателя и цилиндр из вермикулярного чугуна, система должна одновременно контролировать содержание магния и модификатора так, чтобы оно находилось в очень узком окне от начала до конца разливки. Степень сфероидизации должна составлять от 0% до 20% (скорость ползучести от 80% до 100%) для обеспечения наилучших литейных свойств, механической аддитивности и других комплексных характеристик и наилучшего использования. Пятна чешуйчатого графита должны быть полностью устранены во избежание локальных дефектов и слабых мест.
Отправной точкой любой системы управления технологическим процессом является точное и эффективное измерение состояния жидкого чугуна. Надежное крупномасштабное производство вермикулярного чугуна должно иметь эффективные методы контроля, исключающие изменения процесса и ошибки оператора. Самый эффективный способ избежать изменений в процессе - это провести термический анализ расплавленного чугуна после сфероидизации и модифицирования. Согласно результатам термического анализа, перед заливкой добавляется точное количество магния и модификатора. Этот метод измерения и регулировки в реальном времени обеспечивает стабильность производственной линии отливки и устраняет различные риски, связанные с крупномасштабным производством чугуна.
Сохраните источник и адрес этой статьи для перепечатки.: Контроль процесса производства вермикулярного железа
Минхэ Компания по литью под давлением специализируются на производстве и предоставлении качественных и высокопроизводительных литых деталей (ассортимент металлических деталей для литья под давлением в основном включает Тонкостенное литье под давлением,Литье под давлением,Литье под давлением в холодной камере), Round Service (Служба литья под давлением,Обработка с ЧПУ,Изготовление пресс-форм, Обработка поверхности) .Любое индивидуальное литье под давлением из алюминия, магния или замака / цинка, а также другие требования к отливкам, пожалуйста, свяжитесь с нами.
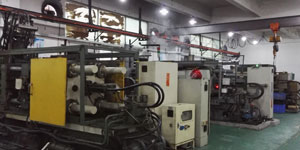
Под контролем ISO9001 и TS 16949, все процессы выполняются на сотнях передовых машин для литья под давлением, 5-осевых станках и других объектах, от струйных до стиральных машин Ultra Sonic. Minghe не только имеет современное оборудование, но и имеет профессиональное оборудование. команда опытных инженеров, операторов и инспекторов для воплощения в жизнь проекта заказчика.
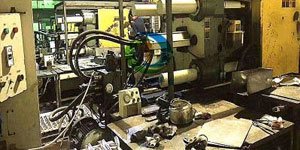
Контрактный производитель отливок под давлением. Возможности включают в себя детали для литья под давлением алюминия с холодной камерой весом от 0.15 фунта. до 6 фунтов, быстрая установка и обработка. Дополнительные услуги включают полировку, вибрацию, удаление заусенцев, дробеструйную очистку, окраску, гальванику, нанесение покрытий, сборку и оснастку. Обрабатываемые материалы включают такие сплавы, как 360, 380, 383 и 413.
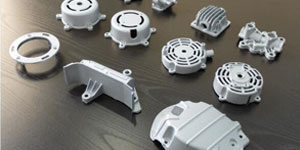
Помощь в проектировании литья цинка под давлением / сопутствующие инженерные услуги. Изготовление на заказ прецизионных отливок из цинка под давлением. Могут изготавливаться миниатюрные отливки, отливки под высоким давлением, отливки в формы с несколькими суппортами, отливки в обычные формы, единичные отливки под давлением и независимые отливки под давлением, а также отливки с герметизацией полости. Отливки могут изготавливаться длиной и шириной до 24 дюймов с допуском +/- 0.0005 дюйма.
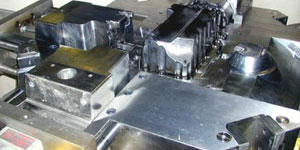
Производитель литья под давлением из магния, сертифицированный по стандарту ISO 9001: 2015. Возможности включают литье под давлением магния под высоким давлением с горячей камерой до 200 тонн и холодной камерой на 3000 тонн, проектирование инструментов, полировку, формование, механическую обработку, порошковую и жидкостную окраску, полный контроль качества с возможностями CMM , сборка, упаковка и доставка.
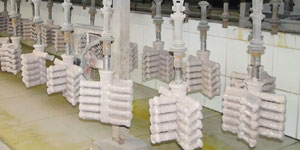
Сертифицирован ITAF16949. Дополнительные услуги трансляции включают инвестиционное литье,литье в песчаные формы,Гравитационное литье, Литье по выплавляемым моделям,Центробежное литье,Вакуумное литье,Постоянное литье формыВозможности включают EDI, техническую поддержку, твердотельное моделирование и вторичную обработку.
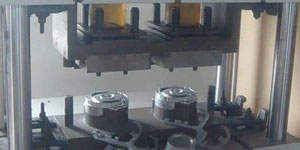
Литейная промышленность Примеры использования запчастей для: автомобилей, велосипедов, самолетов, музыкальных инструментов, судов, оптических устройств, датчиков, моделей, электронных устройств, корпусов, часов, машинного оборудования, двигателей, мебели, ювелирных изделий, приспособлений, телекоммуникаций, освещения, медицинских устройств, фотографических устройств, Роботы, скульптуры, звуковое оборудование, спортивное оборудование, инструменты, игрушки и многое другое.
Что мы можем вам сделать дальше?
∇ Перейти на главную страницу для Литье под давлением Китай
→Литье деталей-Узнай, что мы сделали.
→ Общие советы о Услуги литья под давлением
By Производитель литья под давлением Minghe | Категории: Полезные статьи |Материалы Теги: Литье алюминия, Цинковое литье, Литье магния, Титановое литье, Литье из нержавеющей стали, Латунное литье,Бронзовое литье,Кастинг видео,История компании,Литье алюминия под давлением | Комментарии отключены