Процесс плавки закаленного высокопрочного чугуна
В традиционном процессе производства высокопрочного чугуна для изготовления ингредиентов обычно используется около 10% углеродного скрапа. В этой статье рассматриваются только некоторые вопросы, на которые следует обратить особое внимание в производственном процессе после увеличения доли углеродного скрапа, используемого при производстве высокопрочного чугуна в индукционной печи. Согласно производственной практике, автор выдвигает собственные взгляды на ознакомление коллег.
Выбор заряда
(1) Стальной лом
Лом, используемый при производстве высокопрочного чугуна, должен быть углеродным ломом. В нем не должно быть элементов, препятствующих графитизации, например хрома. Он не должен содержать антисфероидизирующих легирующих элементов. Куски стального лома должны составлять около 30% в виде толстых хлопьев, которые можно уложить в печи.
(2) Рекабюризатор
- ① Качественный кокс. Содержание серы должно быть низким, комковатость 60-80 мм, прочность должна быть высокой. После сжигания его нельзя раздавить.
- ② Блок отработанных электродов. Лучше всего иметь определенную длину, чтобы облегчить резку расплавленного чугуна.
(3) чугун
Он в основном используется для регулирования содержания углерода в расплавленном чугуне. Надеемся на использование высокоуглеродистого чугуна с низким содержанием серы с wC> 4%. Содержание кремния в чугуне соответственно выше, а производство чугуна с шаровидным графитом может быть меньше ферросилиция.
(4) сфероидизация
Сфероидизирующий агент и модификатор используются в соответствии с традиционными методами и определяются в соответствии с фактическими условиями каждого завода.
корюшка
Процесс плавки: коксовый блок + стальной лом → электродный блок → повышение температуры → вытащить коксовый блок и электродный блок → отобрать и проанализировать содержание углерода → чугун → возвратный материал → отобрать и проанализировать Si, Mn → повышение температуры → ферромарганец + ферросилиций → разряд → Посев + сфероидизация → заливка.
Меры предосторожности в процессе плавки следующие:
- Коксовый блок устанавливается на дне печи с целью увеличения времени выдержки коксового блока в жидком чугуне. Количество коксового блока составляет около 5% лома. Около 50% лома расплавляется, а кокс должен быть покрыт толстым хлопьевидным ломом. Также можно использовать блоки отработанных электродов 60-80 мм вместо кокса, который будет установлен на дне печи в качестве перекуглерожителя с более низким содержанием серы, что более выгодно для получения высококачественного высокопрочного чугуна.
- Доля используемого стального лома в основном определяется эффективностью увеличения содержания углерода. Для производителей, которые начинают использовать этот метод для производства высокопрочного чугуна, лучше около 30%. После повышения эффективности увеличения углерода постепенно увеличивайте долю стального лома. Чрезмерное использование стального лома, если эффективность увеличения углерода невысока, повлияет на углеродно-кремниевый эквивалент конечного продукта.
- После плавления стального лома вставьте электродный стержень, чтобы соответствующим образом повысить температуру в печи и повысить эффективность использования углерода. Однако температура печи слишком высока, что увеличивает потребление энергии, а также наносит ущерб футеровке печи.
- После того, как содержание углерода будет оценено как достаточно высокое, выньте коксовый блок и электродный стержень, возьмите образец и проанализируйте содержание углерода.
- По результатам анализа рассчитайте количество добавленного чугуна и количество переработанного высокопрочного чугуна.
- Определите, можно ли восполнить общее количество расплавленного железа с помощью восстановленного материала, основываясь на оценке содержания кремния.
- После расплавления материала для повторного нагрева возьмите образец и проанализируйте содержание Si, Mn и других легирующих элементов.
- Правильно увеличивайте температуру жидкого чугуна, добавляйте легирующие элементы в соответствии с результатами анализа и добавляйте ферросилиций до того, как печь достигнет температуры печи.
- Ферросилиций плавится до расплавленного состояния и сразу же выпускается из печи.
- Сфероидизация, посев и заливка производятся в обычном режиме.
Расчет корректировки состава
Как мы все знаем, механические свойства высокопрочного чугуна в основном зависят от химического состава, скорости охлаждения (литой высокопрочный чугун) и процесса термообработки. Химический состав - это внутренняя причина, корень и переменная, почти все печи разные. Следовательно, необходимо усилить обнаружение химических компонентов и произвести тщательную корректировку, и нецелесообразно применять «производство с фиксированным соотношением». В химическом составе углеродный эквивалент особенно важен. В частности, чугун с шаровидным графитом, производимый с использованием стального лома в качестве основной загрузки, поскольку эффективность увеличения содержания углерода трудно контролировать, а углеродный эквивалент сильно колеблется, поэтому особое внимание следует уделять корректировке углеродного эквивалента.
- Рассчитайте количество добавленного чугуна. Рассчитайте количество добавленного чугуна на основе анализа содержания углерода. Фактически, необходимо отрегулировать углеродный эквивалент чугуна с шаровидным графитом таким образом, чтобы углеродный эквивалент расплава, образованного как передельным чугуном, так и стальным ломом, достигал углеродного эквивалента, необходимого для чугуна с шаровидным графитом. добавленный лом × (требуемое содержание углерода в чугуне с шаровидным графитом - анализ содержания углерода) / (содержание углерода в чугуне - требуемое содержание углерода в чугуне с шаровидным графитом)
- Расчет добавленного количества переработанного высокопрочного чугуна Углеродный эквивалент переработанного высокопрочного чугуна в основном нормальный, и добавленное количество невелико. Следовательно, после добавления повторно нагретого чугуна определяется содержание углерода в расплавленном чугуне во всей печи. Количество чугуна с шаровидным графитом, добавленного в печь = общее количество загрузки - количество стального лома - количество чушек железо добавлено
- Оценка содержания кремния Формула расчета выглядит следующим образом: Содержание кремния ≈ ((стальной лом + чугун + добавленное количество чугуна с шаровидным графитом) × содержание кремния / общая загрузка] × 100% ≤ допустимое содержание кремния в исходном чугуне При оценке кремния содержание слишком велико, добавьте небольшое количество переработанного высокопрочного чугуна и используйте такое же количество передельного чугуна и лома в соотношении 9: 1, чтобы восполнить общую загрузку.
- Расчет добавления ферросилиция Формула расчета выглядит следующим образом: Количество добавленного ферросилиция = [общее количество заряда × (требуемое содержание кремния в ковком чугуне - повышенное содержание кремния путем внесения прививки - повышенное содержание кремния посредством сфероидизационного анализа содержания кремния)] / содержание кремния в ферросилиция
- Количество добавленного марганца и других легирующих элементов рассчитывается следующим образом: Количество добавленного легированного железа = общее количество заряда × (требуемое содержание легированного пластичного чугуна по результатам анализа) / содержание легирующего элемента в легированном чугуне. включены в приведенные выше расчеты.
Это связано с тем, что чугун с шаровидным графитом плавится в индукционной печи, и элементы не сильно обгорают, а также до некоторой степени обжигается чугун. Если вы столкнулись с особыми обстоятельствами, стоит обратить внимание на пригорание.
Пример применения корректировки композиции:
- При использовании индукционной электропечи емкостью 1 т для производства ковкого перлитного чугуна QT800-2 вес отливки составляет 1000 кг.
- «Контрольный химический состав: wC = 3.5%, wSi = 2.5%, wMn = 0.5%, wP <0.07%, wS <0.02%, wMg = 0.03% 0.06%, wRE = 0.02% 0.04%.
- После повторного науглероживания содержание углерода в «жидком стальном ломе» в печи составляет 2.5%.
- Количество добавленного чугуна = 300 × (3.5% -2.5%) / (4% -3.5%) = 600 (кг)
- Количество чугуна с шаровидным графитом, используемого в печи = 1000-300-600 = 100 (кг)
- Расчетное содержание кремния = (300 × 0.3% + 600 × 1.8% + 100 × 2.5%) × 100% = 1.42%
- Если содержание кремния в нодулизаторе составляет 0.6%, а содержание кремния в модификаторе составляет 0.4%, содержание кремния в исходном расплавленном чугуне должно составлять 1.5%, что выше расчетного содержания кремния. Для этого можно использовать чугун Z18 для корректировки углеродного эквивалента, а ковкий чугун после повторного обжига можно использовать для восполнения общего количества заряда.
- Содержание кремния составляет 1.38%, а содержание марганца - 0.15% до того, как печь будет выпущена.
- Количество добавленного ферросилиция = [1000 (2.5% -0.6% -0.4% -1.38%)] / 75% = 1.6 кг.
- Количество добавленного ферромарганца = [1000 (0.5% -0.15%)] / 65% = 5.4 кг.
4. Заключительные замечания
При производстве индукционных электропечей мы используем стальной лом для производства QT800-2, прочность составляет 800 ~ 1000 МПа, а относительное удлинение составляет более 4%.
Сейчас на рынке много стального лома, чугун стоит дорого, а качественного чугуна еще меньше. Поэтому мы предлагаем производителям, которые занимаются производством чугуна с шаровидным графитом, использовать вышеупомянутое допущение и «заменить сталь на чугун» для производства чугуна с шаровидным графитом.
Сохраните источник и адрес этой статьи для перепечатки.:Процесс плавки закаленного высокопрочного чугуна
Минхэ Компания по литью под давлением специализируются на производстве и предоставлении качественных и высокопроизводительных литых деталей (ассортимент металлических деталей для литья под давлением в основном включает Тонкостенное литье под давлением,Литье под давлением,Литье под давлением в холодной камере), Round Service (Служба литья под давлением,Обработка с ЧПУ,Изготовление пресс-форм, Обработка поверхности) .Любое индивидуальное литье под давлением из алюминия, магния или замака / цинка, а также другие требования к отливкам, пожалуйста, свяжитесь с нами.
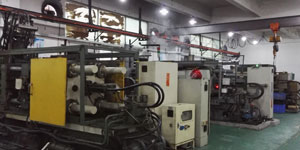
Под контролем ISO9001 и TS 16949, все процессы выполняются на сотнях передовых машин для литья под давлением, 5-осевых станках и других объектах, от струйных до стиральных машин Ultra Sonic. Minghe не только имеет современное оборудование, но и имеет профессиональное оборудование. команда опытных инженеров, операторов и инспекторов для воплощения в жизнь проекта заказчика.
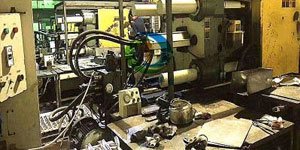
Контрактный производитель отливок под давлением. Возможности включают в себя детали для литья под давлением алюминия с холодной камерой весом от 0.15 фунта. до 6 фунтов, быстрая установка и обработка. Дополнительные услуги включают полировку, вибрацию, удаление заусенцев, дробеструйную очистку, окраску, гальванику, нанесение покрытий, сборку и оснастку. Обрабатываемые материалы включают такие сплавы, как 360, 380, 383 и 413.
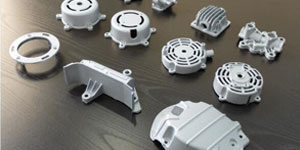
Помощь в проектировании литья цинка под давлением / сопутствующие инженерные услуги. Изготовление на заказ прецизионных отливок из цинка под давлением. Могут изготавливаться миниатюрные отливки, отливки под высоким давлением, отливки в формы с несколькими суппортами, отливки в обычные формы, единичные отливки под давлением и независимые отливки под давлением, а также отливки с герметизацией полости. Отливки могут изготавливаться длиной и шириной до 24 дюймов с допуском +/- 0.0005 дюйма.
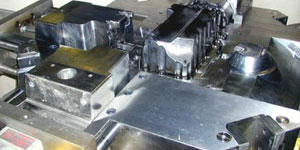
Производитель литья под давлением из магния, сертифицированный по стандарту ISO 9001: 2015. Возможности включают литье под давлением магния под высоким давлением с горячей камерой до 200 тонн и холодной камерой на 3000 тонн, проектирование инструментов, полировку, формование, механическую обработку, порошковую и жидкостную окраску, полный контроль качества с возможностями CMM , сборка, упаковка и доставка.
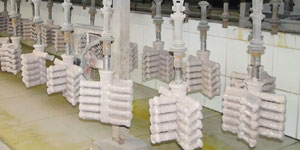
Сертифицирован ITAF16949. Дополнительные услуги трансляции включают инвестиционное литье,литье в песчаные формы,Гравитационное литье, Литье по выплавляемым моделям,Центробежное литье,Вакуумное литье,Постоянное литье формыВозможности включают EDI, техническую поддержку, твердотельное моделирование и вторичную обработку.
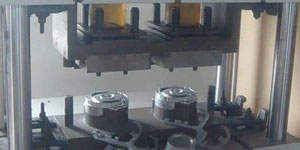
Литейная промышленность Примеры использования запчастей для: автомобилей, велосипедов, самолетов, музыкальных инструментов, судов, оптических устройств, датчиков, моделей, электронных устройств, корпусов, часов, машинного оборудования, двигателей, мебели, ювелирных изделий, приспособлений, телекоммуникаций, освещения, медицинских устройств, фотографических устройств, Роботы, скульптуры, звуковое оборудование, спортивное оборудование, инструменты, игрушки и многое другое.
Что мы можем вам сделать дальше?
∇ Перейти на главную страницу для Литье под давлением Китай
→Литье деталей-Узнай, что мы сделали.
→ Общие советы о Услуги литья под давлением
By Производитель литья под давлением Minghe | Категории: Полезные статьи |Материалы Теги: Литье алюминия, Цинковое литье, Литье магния, Титановое литье, Литье из нержавеющей стали, Латунное литье,Бронзовое литье,Кастинг видео,История компании,Литье алюминия под давлением | Комментарии отключены