Применение технологии пропитки в производстве двигателей
Обработка пропиткой деталей из легких материалов, таких как алюминиевые цилиндры, может эффективно снизить процент брака деталей и значительно улучшить их качество. Обеспечивая качество продукции, они могут эффективно снизить производственные затраты и повысить эффективность производства.
Предложение облегчения двигателя и пропитки.
Легкость стала тенденцией в современной автомобильной промышленности, которая в основном определяется всемирным вниманием к охране окружающей среды и энергосбережению. Данные показывают, что если собственный вес автомобиля уменьшится на 10%, его топливная эффективность может быть увеличена на 15%. Повышение топливной эффективности означает снижение расхода топлива и выбросов. Следовательно, уменьшение веса автомобиля - наиболее эффективный способ улучшить энергосбережение и защиту окружающей среды автомобиля. Двигатель - это наиболее важный крупный узел автомобиля, и снижение его веса имеет решающее значение для уменьшения веса автомобиля.
С технической точки зрения существует множество способов достижения легкости, например оптимизация всей конструкции машины, дополнительных модулей и легкости, но использование легких материалов, таких как пластмассы, алюминиевые сплавы и сплавы магния, для замены традиционных материалов, таких как как чугун - это текущее сокращение. Основной способ веса двигателя. Фактически, алюминиевый сплав широко используется в головках цилиндров двигателей, впускных коллекторах и более мелких деталях, таких как корпуса водяных насосов и корпуса масляных насосов, в течение многих лет, и все больше и больше компаний применяют блоки цилиндров из алюминиевого сплава в последнее десятилетие. Однако, по сравнению с чугуном, алюминиевые отливки более подвержены внутренней рыхлости, усадке и образованию пор в процессе литья из-за образования кристаллов, усадки и поглощения газа. Эти дефектные отливки после обработки имеют плотный поверхностный слой. Площадь удаляется, обнажая внутренние организационные недостатки. Для тех алюминиевых отливок, которые требуют герметичности двигателя, при прохождении процесса обнаружения утечек на производственной линии наличие дефектных микропор приведет к чрезмерной утечке и образованию отходов, иногда даже партиями. Поскольку эти условия могут быть обнаружены только после многократной обработки, это также приведет к серьезным потерям человеко-часов, сырья и энергии. Видно, что для решения проблемы высокого уровня брака алюминиевых отливок необходимо проводить определенные меры обработки на производстве. В настоящее время наиболее распространенной технологией является пропитка, то есть устранение течи. Так называемая «пропитка» заключается в том, чтобы пропитать инфильтрант в микропоры алюминиевой отливки при определенных условиях, и после затвердевания наполнитель, пропитанный в поры, и внутренняя стенка поры отливки соединяются как единое целое с блокировать микропоры, чтобы детали могли соответствовать технологическому процессу A, необходимому для создания давления, предотвращения просачивания и предотвращения утечки.
Процесс пропитки под вакуумом
В настоящее время при производстве алюминиевых отливок в стране и за рубежом обычно применяется метод вакуумной инфильтрации под давлением. Этот процесс в основном выполняется в вакуумном резервуаре под давлением. В зависимости от технологического процесса его можно разделить на три этапа: предварительная обработка, пропитка и последующая обработка. Его различные этапы в основном включают: предварительную обработку, также называемую предварительной микропористой обработкой, которая в основном состоит из обезжиривания, очистки и сушки отливок для подготовки к следующему процессу; первый шаг пропитки - поместить заготовку в корзину. Затем поместить корзину в емкость для пропитки; пропылесосить емкость для пропитки, чтобы удалить газ в порах деталей; переместите герметик из резервуара для хранения в резервуар для пропитки и погрузите детали, которые все еще находятся под вакуумом; Снова пропылесосьте емкость для пропитки, чтобы удалить газ из герметика; сбросить вакуум и нагнетать давление в резервуаре для пропитки сжатым воздухом, что способствует проталкиванию герметика в поры; сбросить давление и вернуть герметик в емкость для хранения; Последующая обработка заключается в основном в удалении деталей, сушке отжимом, полоскании и завершении операций отверждения.
Основная цель предварительной обработки - удалить масляные пятна, металлическую стружку и пыль с поверхности деталей, улучшить качество пропитки, а также предотвратить попадание масла и механических примесей в пропиточную жидкость, что повлияет на проникновение и адгезия. Обычно используемые методы обезжиривания включают обезжиривание растворителем, обезжиривание щелочью и электрохимическое обезжиривание. Отливки вынимаются после вышеупомянутого обезжиривания и очистки, промываются горячей водой и сушатся при 80-90 ℃. Чтобы улучшить эффект замачивания и предотвратить попадание большого количества воды в вакуумный насос, очень важна сушка после очистки.
Обработка пропиткой заключается в помещении предварительно обработанных деталей в резервуар для пропитки для герметизации и вакуумирования, полного удаления воздуха и мелкой пыли из резервуара и пор отливки, а также создания динамических условий перепада давления для заполнения и инфильтрации. пропитки. Затем инфильтрант всасывается за счет разрежения в резервуаре, и снова создается вакуум. Целью второго вакуумирования является удаление газа из пропиточной жидкости в резервуаре для предотвращения проникновения пропиточной жидкости, содержащей газ, в микропористые дефекты отливки, чтобы избежать образования пор во время затвердевания, влияющих на герметичность. представление. Наконец, подайте давление, чтобы инфильтрант, который был заполнен и просочился в поры отливки, проник в самую глубокую часть каждой части дефекта. Пропитка - это жидкое вещество, приготовленное из неорганических или органических веществ. В настоящее время наиболее широко используемый герметик на основе метакрилата PC504 / 66 отверждается при нагревании и обеспечивает заметное заполнение микропор с его низкой усадкой во время полимеризации. Способность, в то же время его низкая вязкость, способствует быстрому и глубокому проникновению герметика в микропоры. Затвердевший герметик может нормально функционировать в диапазоне от -50 до 200 ℃.
Последующая обработка заключается в том, чтобы капнуть на заготовку, очистить ее и поместить в сушильный шкаф для застывания, чтобы инфильтрант, попадающий в поры отливки, превратился из жидкого в твердое с образованием твердой застывшей пленки. Температура отверждения обычно устанавливается на 80 ~ 90 ℃ или помещается при комнатной температуре (выше 25 ℃) на 24 часа. Если отливка используется при температуре выше 300 ℃, ее следует отверждать при 80 ℃ в течение 2 часов, а затем при 110 ℃ в течение 1 часа.
Что касается того, какая часть производственного процесса пропитывается, разные производственные предприятия и разные типы заготовок сильно различаются. Небольшое количество компаний разработают единые правила для всех деталей трансмиссии, требующих высокой точности изготовления и герметичности: такие детали должны быть пропитаны перед обработкой, то есть, когда они еще находятся в состоянии литья, чтобы добиться улучшения. Цель литья - продление срока службы инструмента при обработке и обеспечение качества продукции. Однако большинство заводов по-прежнему применяют разные методы в зависимости от типа деталей. Вообще говоря, для некоторых ключевых деталей, таких как алюминиевый блок цилиндров в двигателе, обычно требуется пропитать все детали, когда они находятся в состоянии литья, а затем отправить их. OEM. Что касается пропитки некоторых деталей в соответствии с определенными критериями после определенного процесса на производственной линии OEM, это зависит от производственного процесса OEM.
Большинство деталей, как правило, не требует пропитки, когда они находятся в состоянии отливки. Вместо этого процесс пропитки осуществляется после определенного процесса в производственном процессе в соответствии с реальной ситуацией. То есть, когда детали после нескольких процессов обработки подтверждают, что значение обнаружения утечки некоторых деталей находится в пределах указанного интервала, пропитывается только эта часть отбракованной детали. В большинстве случаев доля бракованных деталей очень мала (примерно от 1% до 2%), но когда эта доля превышает определенный предел (в зависимости от конкретной ситуации), изготовитель оборудования потребует, чтобы завод-изготовитель заготовок выполнял пропитку всех отливок. .
Некоторые детали, требующие пропитки, не входят в производственный процесс изготовителя оригинального оборудования по конструктивным причинам. Детали, результаты обнаружения утечек которых выходят за пределы допуска, независимо от того, насколько велико фактическое измеренное значение, они будут сразу утилизированы. Однако, если величина утечки в определенной степени превышает долю детали, завод по производству главного двигателя также выдвигает требование пропитки для всех литых заготовок.
Итак, где же собственно операция пропитки? Обычной практикой в стране и за рубежом занимаются независимые и профессиональные предприятия. Это не только эффективно и легко обеспечить качество, но и относительно невысокие затраты для сборочного предприятия. Однако есть также несколько заводов по производству двигателей с большими партиями, высокими темпами производства и высокими требованиями к качеству продукции. Они откроют закрытое пространство в цехе, чтобы вышеупомянутые профессиональные предприятия, занимающиеся пропиткой, могли построить относительно единую, эффективную, а производственная линия пропитки с более высокой степенью механизации эквивалентна секции цеха. Конечно, скорость работы этого «участка работы» ниже, чем у общей производственной линии.
Выполнение нескольких определений пропитанных деталей
Как мы все знаем, блок цилиндров, являясь основным корпусом двигателя, является самой большой и тяжелой частью среди них. При выборе алюминиевого сплава снижение веса примерно вдвое имеет наибольшее значение для облегчения двигателя. Однако ввиду сложной конструкции блока цилиндров и количества процессов механической обработки по сравнению с другими алюминиевыми отливками в двигателе вероятность внутренних дефектов в алюминиевом блоке цилиндров во время процесса литья и формовки также выше. Поэтому, как стандартизировать и эффективно внедрить процесс иммерсионного проникновения для обеспечения его качества, также больше всего волнует предприятия. Далее на примере алюминиевого цилиндра проблема определения и утверждения деталей, которые необходимо пропитывать, дополнительно поясняется на типичном случае. Недавно построенная производственная линия для обработки алюминиевых цилиндров на современном заводе автомобильных двигателей завершила все процессы грубой обработки перед тем, как заготовка поступит на станцию промежуточной очистки. Перед следующей установкой крышки коренного подшипника и последующими финишными операциями была создана станция испытания герметичности. В дополнение к обнаружению утечек из масляного канала низкого давления, водяного канала и масляного канала высокого давления алюминиевого блока цилиндров, эта станция также эквивалентна установке заслонки. По измеренному значению утечки необходимо определить, пропитан ли этот алюминиевый баллон.
Для заготовки устанавливаются два предела экранирования: первый - это скорость утечки проверяемой детали, на примере масляного канала низкого давления предел скорости утечки составляет 30 куб. См / мин; второй предел экранирования: Эта проверяемая часть является объектом, чтобы определить, есть ли утечка в алюминиевом цилиндре, но возможно ли и необходимо ли устранить ее с помощью пропитки. Если взять в качестве примера масляный канал низкого давления, в таблице указано, что оно составляет 500 куб. См / мин. Ввиду этого, когда алюминиевый корпус цилиндра после процесса промежуточной очистки поступает на станцию испытания герметичности вдоль конвейерной дорожки, если какое-либо из измеренных значений утечки детали ниже, чем соответствующий предел экранирования, указанный в таблице, то То есть, скорость утечки будет оценена как квалифицированная, и затем она перейдет в следующий процесс. Но до тех пор, пока любое из фактических измеренных значений утечки превышает его скорость утечки, но меньше предела брака, возьмите в качестве примера масляный канал низкого давления в таблице, диапазон составляет от 30 до 500 куб. См / мин. Алюминиевый блок цилиндров рассматривается как заготовка, которую необходимо вынуть для пропитки, направить по дорожке качения в обратном направлении, а затем вручную снять и отправить. Что касается очень небольшого количества деталей, измеренное значение утечки которых достигло или даже превысило предел брака, указанный в таблице, они будут вытекать через дорожку качения конвейера. Вышеупомянутый процесс обнаружения, проверки и переключения выполняется роботом на станции проверки герметичности.
Таким образом, после пропитки алюминиевых цилиндров и других деталей не только снижается количество брака и значительно улучшается качество, но также снижаются производственные затраты при условии обеспечения качества и эффективно повышается производительность. Таким образом, в процессе того, как промышленность современных автомобильных двигателей становится все более легкой, научное и разумное использование технологии инфильтрации является лучшим решением для полного решения неотъемлемых проблем отливок из алюминиевых сплавов и других легких материалов (таких как дефекты, такие как микропоры).
Сохраните источник и адрес этой статьи для перепечатки.:Применение технологии пропитки в производстве двигателей
Минхэ Компания по литью под давлением специализируются на производстве и предоставлении качественных и высокопроизводительных литых деталей (ассортимент металлических деталей для литья под давлением в основном включает Тонкостенное литье под давлением,Литье под давлением,Литье под давлением в холодной камере), Round Service (Служба литья под давлением,Обработка с ЧПУ,Изготовление пресс-форм, Обработка поверхности) .Любое индивидуальное литье под давлением из алюминия, магния или замака / цинка, а также другие требования к отливкам, пожалуйста, свяжитесь с нами.
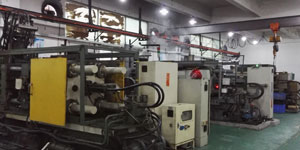
Под контролем ISO9001 и TS 16949, все процессы выполняются на сотнях передовых машин для литья под давлением, 5-осевых станках и других объектах, от струйных до стиральных машин Ultra Sonic. Minghe не только имеет современное оборудование, но и имеет профессиональное оборудование. команда опытных инженеров, операторов и инспекторов для воплощения в жизнь проекта заказчика.
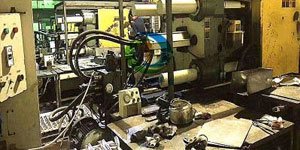
Контрактный производитель отливок под давлением. Возможности включают в себя детали для литья под давлением алюминия с холодной камерой весом от 0.15 фунта. до 6 фунтов, быстрая установка и обработка. Дополнительные услуги включают полировку, вибрацию, удаление заусенцев, дробеструйную очистку, окраску, гальванику, нанесение покрытий, сборку и оснастку. Обрабатываемые материалы включают такие сплавы, как 360, 380, 383 и 413.
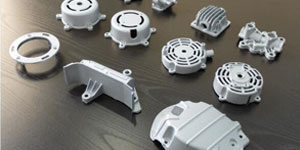
Помощь в проектировании литья цинка под давлением / сопутствующие инженерные услуги. Изготовление на заказ прецизионных отливок из цинка под давлением. Могут изготавливаться миниатюрные отливки, отливки под высоким давлением, отливки в формы с несколькими суппортами, отливки в обычные формы, единичные отливки под давлением и независимые отливки под давлением, а также отливки с герметизацией полости. Отливки могут изготавливаться длиной и шириной до 24 дюймов с допуском +/- 0.0005 дюйма.
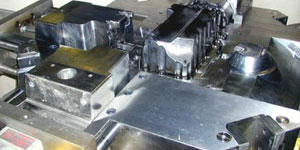
Производитель литья под давлением из магния, сертифицированный по стандарту ISO 9001: 2015. Возможности включают литье под давлением магния под высоким давлением с горячей камерой до 200 тонн и холодной камерой на 3000 тонн, проектирование инструментов, полировку, формование, механическую обработку, порошковую и жидкостную окраску, полный контроль качества с возможностями CMM , сборка, упаковка и доставка.
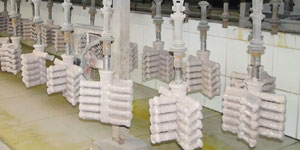
Сертифицирован ITAF16949. Дополнительные услуги трансляции включают инвестиционное литье,литье в песчаные формы,Гравитационное литье, Литье по выплавляемым моделям,Центробежное литье,Вакуумное литье,Постоянное литье формыВозможности включают EDI, техническую поддержку, твердотельное моделирование и вторичную обработку.
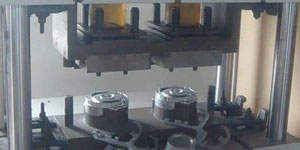
Литейная промышленность Примеры использования запчастей для: автомобилей, велосипедов, самолетов, музыкальных инструментов, судов, оптических устройств, датчиков, моделей, электронных устройств, корпусов, часов, машинного оборудования, двигателей, мебели, ювелирных изделий, приспособлений, телекоммуникаций, освещения, медицинских устройств, фотографических устройств, Роботы, скульптуры, звуковое оборудование, спортивное оборудование, инструменты, игрушки и многое другое.
Что мы можем вам сделать дальше?
∇ Перейти на главную страницу для Литье под давлением Китай
→Литье деталей-Узнай, что мы сделали.
→ Общие советы о Услуги литья под давлением
By Производитель литья под давлением Minghe | Категории: Полезные статьи |Материалы Теги: Литье алюминия, Цинковое литье, Литье магния, Титановое литье, Литье из нержавеющей стали, Латунное литье,Бронзовое литье,Кастинг видео,История компании,Литье алюминия под давлением | Комментарии отключены