Механизм деградации пресс-формы
В настоящее время штамповка является самой передовой технологией штамповки, которая в основном используется для массового производства ключевых компонентов пресс-форм. Самый большой недостаток - низкая долговечность формующих инструментов. По словам редактора diecastingcompany.com, стоимость инструментов составляет 8-15% от общей стоимости продукции. Фактически, если учесть время, необходимое для замены изношенных инструментов, и потери, вызванные случайным отказом, стоимость может достигать от 30% до 50%. Кроме того, износ инструмента приведет к значительному ухудшению качества поковки. Наиболее частыми дефектами, вызванными износом инструмента, являются ошибки заполнения полости, то есть складки, заусенцы, деформация, царапины, расслоение, а также микро- и макротрещины.
Эти дефекты в конечном итоге повлияют на характеристики кованых изделий. Из-за сильной конкуренции на рынке производители штамповочных изделий продолжают сокращать свои затраты, одновременно улучшая качество поковок. Несмотря на это, их по-прежнему очень интересует проблема плохой стойкости инструмента.
Долговечность инструмента обычно определяется несколькими способами. С точки зрения производства долговечность инструмента выражается количеством поковок, то есть количеством изделий ожидаемого качества, которые можно получить с помощью этого инструмента. Согласно этому определению, средний срок службы инструментов может составлять от 2,000 20,000 до XNUMX XNUMX штук. С точки зрения инструментов, долговечность связана с деградацией, поэтому она определяется как способность противостоять явлениям деградации. В этой статье в основном используется второе определение. Следует сказать, что во время использования ковочные инструменты подвержены воздействию множества факторов, ухудшающих качество, и взаимодействие этих факторов затрудняет анализ проблемы. В литературе по этой теме можно найти различные объяснения явлений деградации.
Согласно статистике многих ученых, основная причина вывода пресс-форм из эксплуатации связана с изменением размеров износа. Отход пресс-формы из-за износа составляет около 70%, пластическая деформация составляет около 25%, а усталостное растрескивание и другие причины составляют лишь около 5%. Многие явления часто происходят одновременно, и их взаимодействие зависит от конструкции пресс-формы, условий их ковки и изготовления, термической обработки материала пресс-формы и формы преформы и вставки.
Рабочие условия ковочных штампов: в процессе горячей штамповки инструменты в основном подвергаются деградации по трем причинам: интенсивный тепловой удар, периодические изменения механической нагрузки, а также высокая температура и высокое давление. Чтобы снизить предел текучести стальных изделий при горячей ковке, деформируемый металл нагревают до 10,000 2,000–800 900 градусов Цельсия. В момент деформации материала температура поверхности инструмента может достигать XNUMX градусов Цельсия с последующим интенсивным охлаждением, и поэтому инструмент будет подвергаться воздействию большого температурного градиента. В поперечном сечении формы температура поверхности формы и приповерхностная температура могут отличаться на несколько сотен градусов Цельсия. Температура горячей штамповки ниже, чем горячей штамповки, то есть температура деформации стали достигает около XNUMX градусов Цельсия. Это означает, что нагрузка, создаваемая циклическим нагревом и охлаждением поверхности инструмента, не такая большая, как при горячей штамповке. Тем не менее, срок службы инструментов, используемых в процессе полугорячей ковки, по-прежнему невелик. В основном это происходит из-за комбинированного воздействия циклической температуры и большей механической нагрузки. Механическая нагрузка в основном возникает из-за охлаждения и более твердых материалов.
Механизм вырождения кузнечного инструмента
Срок службы кузнечных инструментов в основном зависит от их конструкции, подготовки, термообработки инструментальных материалов, условий их ковки, формы преформ и стержневых блоков и т. Д. Мы можем найти много информации о деградации в литературе по этой теме. Эти механизмы делятся на разные категории. Результаты исследований показывают, что на поверхности кузнечного инструмента в основном возникают следующие механизмы износа: абразивный износ, термомеханическая усталость, пластическая деформация, усталостное растрескивание, адгезионный износ и окисление. Форма рабочего углубления инструмента определяет время контакта, давление, траекторию трения и изменения температуры, которые определяют скорость возникновения специального механизма деградации.
На плоской поверхности время контакта между инструментом и термическим материалом является наибольшим, и это также место, где возникает максимальное давление. Термомеханическая усталость - главный механизм деградации.
На внутренний радиус закругления влияет циклическая растягивающая нагрузка, которая вызвана увеличением внешней нагрузки, которая в основном возникает, когда деформация имеет тенденцию концентрироваться в процессе ковки. В результате усталостные микротрещины в процессе эксплуатации инструмента перерастают в большие трещины и появляются в этих местах. Наружный радиус вмятины пресс-формы и место, где отпечаток пресс-формы входит в опорную перемычку из-за ослабления материала в условиях высоких температур, тем ниже предел текучести материала, что приводит к пластической деформации. Плотный поток деформированных материалов вызывает абразивный износ в этих областях, который дополнительно усугубляется твердыми оксидами, которые образуются на поверхности ковочного материала инструмента в процессе высокотемпературного окисления.
Адгезионный износ механизма деградации ковочных штампов
Адгезионный износ возникает в области пластической деформации поверхностного слоя, особенно там, где поверхность неровная. Обычно это происходит в условиях высокого давления и относительно низкой скорости, в основном из-за сходных взаимодействий материалов или материалов, проявляющих химическое сродство (типичные условия обработки при ковке). В условиях более высокого давления формованный материал скользит по поверхности инструмента, удаляя оксидное покрытие, оставляя незащищенной свежую поверхность инструмента. В основном это происходит в неровной области проекции поверхности (пиковая часть шероховатой поверхности).
Когда материалы в этих местах помещаются близко друг к другу, так что начинают действовать межатомные силы, образуются локальные связи металлов. Затем по мере дальнейшего смещения поверхностей друг к другу металлическая связь разрушалась. При этом формируется пластическая деформация поверхностного слоя. Разрыв металлической связи приводит к отслаиванию металлических частиц, которые имеют тенденцию прилипать к поверхности.
Абразивный износ механизма деградации ковочных штампов
Потери материала обычно связаны с абразивным износом. Размер отслоившихся частиц в основном зависит от коэффициента ковки и свойств поверхностного слоя инструмента. Примером адгезионного износа является операция второго этапа ковки картера карданного вала, как показано на рисунке. Температура, при которой материал деформируется в этом процессе, составляет около 900 ° C, то есть она обычно намного ниже, чем при традиционном процессе горячей штамповки, который имеет тенденцию к такому типу износа. Адгезионный износ будет прилипать к самому материалу или к инструменту, где площадь поперечного сечения уменьшается.
Абразивный износ является результатом потери материала и в основном достигается за счет отделения материала от поверхности. Абразивный износ будет возникать при наличии незакрепленных или закрепленных абразивных частиц или при наличии неровных участков выступов на взаимодействующей поверхности. У кузнечного инструмента его твердость намного выше, чем у деформируемого материала. В этом случае при появлении абразивных частиц в части контакта кузнечного инструмента и деформируемого материала произойдет абразивный износ. Абразивный износ усугубляется появлением твердых оксидных частиц, которые образуются на поверхности мелких частиц, отделенных от поковки, формы и поверхности формы в условиях высоких температур. Благодаря этому механизму создаются канавки по направлению, в котором изменяется деформация материала.
Их форма и глубина во многом зависят от условий ковки. Выступающая часть особенно подвержена износу и будет быстро удаляться с поверхности инструмента во время его дальнейшей эксплуатации, что приводит к потере материала и изменению геометрии материала. Особенно легко формируется абразивный износ, а также особенно чувствительно к абразивному износу - это место, где происходит наибольшее скольжение во время деформации материала. Наиболее распространенным является внешний радиус полости формы, где форма входит в мостик оплавления.
Сохраните источник и адрес этой статьи для перепечатки.: Механизм деградации пресс-формы
Минхэ Компания по литью под давлением специализируются на производстве и предоставлении качественных и высокопроизводительных литых деталей (ассортимент металлических деталей для литья под давлением в основном включает Тонкостенное литье под давлением,Литье под давлением,Литье под давлением в холодной камере), Round Service (Служба литья под давлением,Обработка с ЧПУ,Изготовление пресс-форм, Обработка поверхности) .Любое индивидуальное литье под давлением из алюминия, магния или замака / цинка, а также другие требования к отливкам, пожалуйста, свяжитесь с нами.
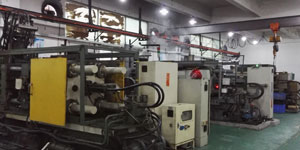
Под контролем ISO9001 и TS 16949, все процессы выполняются на сотнях передовых машин для литья под давлением, 5-осевых станках и других объектах, от струйных до стиральных машин Ultra Sonic. Minghe не только имеет современное оборудование, но и имеет профессиональное оборудование. команда опытных инженеров, операторов и инспекторов для воплощения в жизнь проекта заказчика.
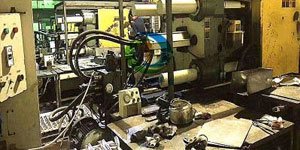
Контрактный производитель отливок под давлением. Возможности включают в себя детали для литья под давлением алюминия с холодной камерой весом от 0.15 фунта. до 6 фунтов, быстрая установка и обработка. Дополнительные услуги включают полировку, вибрацию, удаление заусенцев, дробеструйную очистку, окраску, гальванику, нанесение покрытий, сборку и оснастку. Обрабатываемые материалы включают такие сплавы, как 360, 380, 383 и 413.
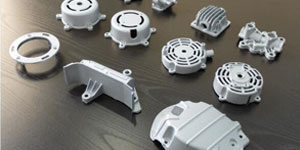
Помощь в проектировании литья цинка под давлением / сопутствующие инженерные услуги. Изготовление на заказ прецизионных отливок из цинка под давлением. Могут изготавливаться миниатюрные отливки, отливки под высоким давлением, отливки в формы с несколькими суппортами, отливки в обычные формы, единичные отливки под давлением и независимые отливки под давлением, а также отливки с герметизацией полости. Отливки могут изготавливаться длиной и шириной до 24 дюймов с допуском +/- 0.0005 дюйма.
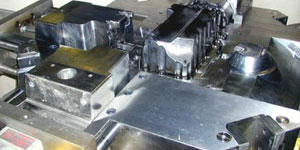
Производитель литья под давлением из магния, сертифицированный по стандарту ISO 9001: 2015. Возможности включают литье под давлением магния под высоким давлением с горячей камерой до 200 тонн и холодной камерой на 3000 тонн, проектирование инструментов, полировку, формование, механическую обработку, порошковую и жидкостную окраску, полный контроль качества с возможностями CMM , сборка, упаковка и доставка.
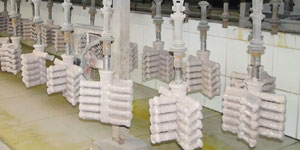
Сертифицирован ITAF16949. Дополнительные услуги трансляции включают инвестиционное литье,литье в песчаные формы,Гравитационное литье, Литье по выплавляемым моделям,Центробежное литье,Вакуумное литье,Постоянное литье формыВозможности включают EDI, техническую поддержку, твердотельное моделирование и вторичную обработку.
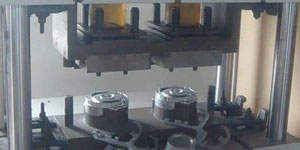
Литейная промышленность Примеры использования запчастей для: автомобилей, велосипедов, самолетов, музыкальных инструментов, судов, оптических устройств, датчиков, моделей, электронных устройств, корпусов, часов, машинного оборудования, двигателей, мебели, ювелирных изделий, приспособлений, телекоммуникаций, освещения, медицинских устройств, фотографических устройств, Роботы, скульптуры, звуковое оборудование, спортивное оборудование, инструменты, игрушки и многое другое.
Что мы можем вам сделать дальше?
∇ Перейти на главную страницу для Литье под давлением Китай
→Литье деталей-Узнай, что мы сделали.
→ Общие советы о Услуги литья под давлением
By Производитель литья под давлением Minghe | Категории: Полезные статьи |Материалы Теги: Литье алюминия, Цинковое литье, Литье магния, Титановое литье, Литье из нержавеющей стали, Латунное литье,Бронзовое литье,Кастинг видео,История компании,Литье алюминия под давлением | Комментарии отключены