Плавление и обработка ADC12
1. Основные характеристики алюминиевого сплава.
Японский алюминиево-кремниевый сплав ADCI2 имеет хорошие характеристики литья, а отливка имеет высокую прочность, низкий коэффициент теплового расширения, высокую коррозионную стойкость и хорошую стойкость к скалыванию. Поэтому он широко используется в производстве автомобильных карбюраторов, блоков цилиндров, головок цилиндров и редукторов локомотивов.
Вибраторы, коробки передач двигателей, коробки передач сельхозтехники, корпуса камер, корпуса электроинструментов и другие детали. В последние годы, с быстрым развитием автомобильной и мотоциклетной промышленности, они все более широко используются в производстве корпусов тормозных насосов для небольших автомобилей, корпусов амортизаторов мотоциклов и других массовых деталей малых и средних размеров сложной формы. и высокая точность прочности.
Si | Fe | Cu | Mn | Mg | Ni | Zn | Sn | Pb |
9.6-12.0 | 1.8-3.5 |
В отливках из алюминиевого сплава ADC12 фаза a-Al является наиболее важной структурой. В литом состоянии фаза a-Al является дендритной и относительно грубой, а ее ориентация не имеет определенной регулярности и довольно беспорядочная, что делает ее характеристики не очень хорошими. ; Si в сплаве в основном используется для улучшения характеристик литья, износостойкости, коррозионной стойкости и механических свойств. Cu и Mg образуют фазы CuAl2 и Mg2Si для упрочнения сплава, но если их содержание будет слишком высоким, пластичность будет снижена, а Cu также может повысить высокотемпературные характеристики, но это снизит коррозионную стойкость; Mn в основном образует фазу AIFeMnS, снижает вредное воздействие примесей Fe и может улучшить термостойкость отливок. Fe обычно считается наиболее вредным примесным элементом в сплавах алюминия. Фаза Fe - это фаза a-Fe (AlgSiFez) и фаза B-Fe (AIsSiFe). Твердая и хрупкая игольчатая фаза β-Fe нарушит прочность соединения металлической матрицы и значительно снизит механические свойства сплава (такие как сопротивление при растяжении), Fe в сплаве Al как вредный элемент значительно снизит: механические свойства сплава, влияет на шероховатость разрушения и так далее.
2. процесс обработки сырья из алюминиевого сплава, подлежащего контролю
В настоящее время большинство предприятий литья под давлением закупают слитки алюминиевых сплавов на предприятиях по производству слитков алюминиевых сплавов. Приготовленные слитки алюминиевого сплава этого типа в основном представляют собой вторичный вторичный алюминий в качестве основного материала, а состав регулируется (добавляются слитки чистого алюминия и некоторые промежуточные продукты). Сплав). Следовательно, себестоимость и отпускная цена слитка из этого сплава алюминия ниже, чем у слитка чистого алюминия в качестве основного материала, но содержание примесей выше. В связи с этой ситуацией необходимо проверить химический состав купленных слитков алюминиевого сплава и внести соответствующие изменения при подписании технических требований с производителем алюминиевых слитков сплава в соответствии с GB / T8733, а затем продолжить работу в соответствии с требованиями. из литого под давлением алюминиевого сплава - ступенчатая регулировка. Из-за требований к содержанию газа и твердости в алюминиевом сплаве завод по производству алюминиевых слитков должен проводить рафинирование, дегазацию и шлакование, чтобы предотвратить унаследование высокого содержания газа и многих примесей в алюминиевом слитке при литье алюминиевая жидкость. Требуется алюминиевый слиток. Поверхность гладкая (после удаления накипи), излом мелкий и нет ярких кристаллических зерен кристаллического кремния. Пузырьки воздуха на поверхности алюминиевого слитка возникают из-за того, что краска на изложнице содержит большое количество воды и не была высушена. Поверхность не светлая, потому что накипь не соскреба. Излом алюминиевого слитка имеет яркие кристаллические зерна из-за слишком высокой температуры разливки и кристаллов кремния. При литье под давлением вторичный материал составляет от 30% до 60%. Если переработанный материал маслянистый, его необходимо сжечь, а затем вдавить в алюминиевую жидкость. Измельченный алюминиевый шлак необходимо просеять и очистить от пыли, а песок и гравий необходимо удалить перед возвратом в печь. Если используется переработанный материал. Количество расплавленного алюминия, рафинирующего агента и средства для удаления шлака должно быть увеличено соответствующим образом и, как правило, контролироваться в соответствии с верхним предельным соотношением. При плавке добавляемый алюминиевый слиток должен быть сухим.
3. Плавление алюминиевого сплава.
Компания использует плавильную печь АТМ-1500. Компания требует, чтобы плавильная печь обжигалась каждый раз при открытии смены, чтобы удалить влагу из печи, а печь после обжига должна соответствовать указанным технологическим требованиям. В процессе плавки требуется температура плавки: (680 ~ 750) С; температура рафинировочной печи: (730 + 10) С. В течение всего процесса плавки алюминиевого сплава шихта при нагревании начинает плавиться, осуществляя переход из твердого состояния в жидкое. Во время этого процесса преобразования металл будет окисляться, сгорать и выделять газ. Окисление и горение металла не только повлияют на химический состав сплава, но и включение шлака, вызванное окислением, является одним из наиболее вредных дефектов слитков алюминиевого сплава. Вдыхание металла сделает слиток слишком поздно или невозможным во время процесса затвердевания. Он улетучивается и существует в слитке в виде рыхлых пор. Следовательно, правильность процесса плавления алюминиевого сплава напрямую зависит от качества расплава. Это не только влияет на его химический состав, но также влияет на качество слитка и даже на конечный результат. Качество обрабатываемых продуктов тесно связано. Алюминий очень активен, кроме инертных газов, он реагирует практически со всеми газами:
Более того, эти реакции необратимы. После реакции металл не может быть восстановлен, что приводит к его потере. Более того, продукты (оксиды, карбиды и т. Д.), Попадающие в расплав, будут загрязнять металл и вызывать дефекты внутренней структуры слитка. Поэтому в процессе плавления сплавов алюминиевого сплава существует строгий выбор технологического оборудования (такого как тип печи, метод нагрева и т. Д.), А также строгий выбор и меры для технологического процесса, такие как сокращение времени плавления и контроль соответствующая скорость плавления. Используйте флюс для покрытия и так далее.
- Из-за активности алюминия при температуре плавления он будет химически реагировать с влагой в атмосфере и влагой, маслом, углеводородами и т. Д. В ряде процессов. С одной стороны, содержание газа в расплаве увеличивается, вызывая рыхлость и поры, а с другой стороны, продукт может окрашивать металл. Поэтому необходимо принять все меры для минимизации влажности во время процесса плавления, а технологическое оборудование, инструменты и сырье должны быть строго сухими и иметь масляные пятна.
- Компания использует метод непрерывной плавки, этот метод обеспечивает непрерывную подачу и периодическую разгрузку. При выплавке алюминиевого сплава из-за конструкции печи время пребывания расплава должно быть как можно короче. Поскольку время пребывания расплава увеличивается, особенно при более высоких температурах плавления, большое количество неспонтанных зародышей кристаллов дезактивируется, вызывая крупные кристаллические зерна слитка, что приводит к отходам отливки слитков и увеличению всасывания металла, что делает расплав неукрепленным металлические включения и содержание газа увеличивается.
- Газ, содержащийся в атмосфере печи для плавки металла, является одним из важнейших источников газа. В зависимости от типа и конструкции используемой плавильной печи, а также от метода сжигания или нагрева используемого топлива, атмосфера печи часто содержит различные пропорции водорода (H2), кислорода (O2), водяного пара (H2O), диоксида углерода ( CO2) и оксид углерода. (CO), азот (N2), диоксид серы (SO2) в дополнение к различным углеводородам. Эти результаты, конечно, неполные, а диапазон составов очень широк. Это связано с тем, что продукты сгорания в топочно-топочном газе сильно изменяются и очень нестабильны. Здесь мы в основном представляем процесс поглощения водорода (H) жидкостью из алюминиевого сплава, который в основном включает три процесса: адсорбцию, диффузию и растворение.
Поскольку водород представляет собой единичный газ с относительно простой структурой, его атомы или молекулы очень малы, его легче растворять в металлах и легко быстро диффундировать при высоких температурах. Следовательно, водород - это газ, который легко растворяется в металлах.
Процесс растворения водорода в расплавленном алюминии: физическая адсорбция- + химическая адсорбция →> диффузия
Водород химически не реагирует с алюминием, но существует в промежутках кристаллической решетки в ионном состоянии, образуя твердый раствор внедрения. При отсутствии оксидной пленки на поверхности жидкого металла скорость диффузии газа в металл обратно пропорциональна толщине металла, пропорциональна корню квадратному из давления газа, и увеличивается с увеличением температуры.
Где: v скорость диффузии n-константа d-толщина металла E-энергия активации p-парциальное давление газа R-постоянная газа T-температура K Следовательно, до достижения насыщения растворимости газа, чем выше температура расплава, тем выше диссоциация водорода. Молекулы Чем выше скорость, тем выше скорость диффузии, поэтому тем выше содержание газа в расплаве.
В производственных условиях, независимо от того, в какой плавильной печи производят алюминиевый сплав, расплав находится в непосредственном контакте с воздухом, то есть с воздухом.
Кислород в газе контактирует с азотом. Алюминий - относительно активный металл. После того, как он вступит в контакт с кислородом, он неизбежно вызовет сильное окисление с образованием оксида алюминия.
Как только алюминий окисляется, он становится окисленным шлаком и становится необратимой потерей. Глинозем - очень стабильное твердое вещество, при смешивании с расплавом он превращается в окисленный шлак. Из-за высокого сродства алюминия и кислорода реакция между кислородом и алюминием очень интенсивна. Однако поверхностный алюминий реагирует с кислородом с образованием Al2O3, и молекулярный объем Al2O больше, чем у алюминия, поэтому поверхностный слой алюминия окисляется с образованием A12O; пленка плотная, что может предотвратить диффузию атомов кислорода внутрь через оксидную пленку. В то же время она может также предотвратить диффузию ионов алюминия наружу, предотвращая тем самым дальнейшее окисление алюминия.
4. обработка алюминиевого сплава
Обработка алюминиевого сплава в основном включает удаление и рафинирование шлака.
- (1) В процессе шлаковой плавки алюминиевого сплава из-за неэффективного удаления и очистки шлака небольшое количество шлака растворяется в расплаве, что приводит к образованию снежных пятен на поверхности алюминиевого сплава, что серьезно влияет на качество алюминиевого сплава. Если удаление шлака не является чистым, это приведет к образованию шлаковых включений и других ловушек, и отливка будет утилизирована. Алюминий - это активный металл. В процессе плавки легко производить оксиды алюминия. Некоторые неметаллические включения также легко попадают в расплав. Включения очень вредны для алюминиевых изделий. Удаление включений стало основной задачей очистки расплава алюминия. В производственной практике распространенными включениями в расплавах алюминиевых сплавов являются Al203O2, SiOXNUMX, MgO и др. Это вызовет примесь расплавленного металла, включения повлияют на текучесть расплава, полимеризация приведет к образованию пузырьков в процессе затвердевания, что повлияет на степень усадки. Поскольку плотность мелких оксидных частиц аналогична плотности алюминия, они обычно взвешены в расплавленном алюминии, и их трудно удалить, стоя на месте. Удаленный оксид обычно содержит много алюминия. Хотя флюс имеет много других применений, уменьшение окисления алюминия и удаление окисленных включений являются основными причинами использования флюса. Принцип шлакования в плавильной печи: разбрызгивайте шлакообразующий агент (или средство для удаления шлака) на поверхность расплавленного алюминия, чтобы отделить шлак и воду, и вытащить отделенный шлак из печи, потому что шлакообразующий агент содержит NajAIF. (Или KzSiFg), эта соль обладает способностью сильно адсорбировать Al2O3, а также Na2SiF. Первая реакция может поглощать часть Al2O3, а третья реакция отделяет шлак от воды и вытягивает шлак из печи для достижения цель удаления шлака. В то же время он также генерирует NaAlF%, который имеет эффект сильной адсорбции r-Al2O3, в результате чего шлак и алюминий отделяются. Целью процесса удаления шлака из алюминиевого сплава является удаление примесей и оксидного шлака, которые попадают в расплавленный алюминий. Часто во время удаления шлака шлак содержит расплавленный алюминий. Следовательно, есть надежда, что расплавленного алюминия, содержащегося в шлаке, должно быть как можно меньше, и шлак следует снова перемешать. Цель жарки золы - выдавить расплавленный алюминий из шлака и осесть на дно вока, чтобы шлак мягко разрушился и распределился по верхней части, так что шлак и расплавленный алюминий отделятся. Для этого необходимо выбрать хороший флюс для удаления шлака. . Метод удаления шлака основан на количестве расплавленного алюминия в плавильной печи, которое равномерно помещается в шлакоуловитель в соответствии с требуемой пропорцией и перемешивается с постоянной скоростью, а затем вынимается фильтрующий шлак после простоя в течение 8- 10 минут. Шлакование требует, чтобы температура расплавленного алюминия составляла 720-740 ° C.
- (2) Рафинирование: химические свойства алюминия в 17 раз активнее. Следовательно, даже если содержание водорода в жидком сплаве очень низкое, большое количество водорода будет выделяться во время затвердевания, образуя поры и включения в отливках, что серьезно повлияет на механические свойства алюминиевого сплава. Повышение качества расплава алюминиевого сплава и очистка жидкого сплава является одной из ключевых задач при плавке алюминиевого сплава, а также эффективным способом и средством повышения качества продукции и конкурентоспособности алюминиевых отливок на рынке. Нецелесообразный процесс рафинирования, дегазация сплава не чистая, отливки склонны к образованию пор. Чтобы усилить эффект дегазации, необходимо увеличить количество добавляемого рафинирующего агента. Однако, если количество слишком велико, легко вызвать окислительное горение Mg. Al, Ti и другие элементы, а также образование шлаков окисления. Для этого важен ключевой процесс рафинирования алюминиевого сплава. Исследования показали, что чем короче расстояние, необходимое водороду для достижения пузыря, тем выше скорость дегазации. Наша компания выбрала деаэратор с вращающимся ротором, разработанный FOSECO, для деаэрации жидкости из алюминиевого сплава. Его принцип работы: вращающийся ротор разбивает большие пузырьки обычного инертного газа на маленькие и диспергирует их в расплавленном металле. За счет уменьшения диаметра пузырьков площадь поверхности пузырьков резко увеличивается, и появляется большая инертность. Поверхность пузырька контактирует с водородом и примесями в расплавленном металле, тем самым повышая эффективность дегазации. Дегазация вращающегося ротора признана одним из лучших процессов дегазации. Структурная схема машины для дегазации с вращающимся ротором: двигатель приводит во вращение вращающийся стержень и графитовый ротор, а инертный газ входит во вращающийся стержень через вращающуюся муфту. Вращающийся стержень и графитовый ротор имеют центральное отверстие, которое позволяет инертному газу проходить и распыляться в металлическую жидкость. Вращающийся графитовый ротор разбивает пузырьки инертного газа на очень мелкие пузырьки, которые рассеиваются по расплавленному металлу. Регулируя и контролируя скорость потока инертного газа и скорость графитового ротора, можно контролировать размер пузырьков и улучшать эффект очистки. В то же время рафинирующий агент, помещенный в установку для дегазации, добавляется к обработанной алюминиевой жидкости в определенной пропорции, чтобы обеспечить дальнейшее удаление оксидной пены во время дегазации. Требования к процессу рафинирования: перенос алюминиевой воды из плавильной печи во роторный деаэратор с переносным водяным мешком: давление азота необходимо контролировать на уровне 0.1-0.3 МПа, чтобы предотвратить разбрызгивание и повреждение алюминия; время очистки и дегазации Контролируется в пределах 5мин. Удаление шлака и рафинирование литого под давлением алюминиевого сплава - это временной процесс, который не может быть завершен быстро. Это неправильная операция по сокращению времени рафинирования. И адсорбция газа в расплавленном алюминии, и всплытие примесей требуют фиксированного времени, это только гарантия. Время адсорбции и время всплытия примесей достаточны для достижения цели рафинирования. Во время рафинирования убедитесь, что жидкий алюминий полностью контактирует с пузырьками. Необходимо постоянное волнение. Газ из алюминиевой жидкости удаляется, а загрязнения удаляются, чтобы гарантировать поры продукта.
5.Conclusion
Выбор разумного процесса плавки в процессе производства литья под давлением алюминиевого сплава является первым шагом к достижению превосходного качества продукции для литья под давлением. Строгий контроль сырья - ключевой шаг в плавке. В то же время перед плавкой необходимо иметь простое представление о влиянии различных элементов на сплав. Удаление и рафинирование шлака - очень важные процессы в процессе плавки алюминиевых сплавов. Благодаря теоретическим исследованиям по удалению и дегазации шлака был получен подходящий процесс плавки для нашей компании.
Сохраните источник и адрес этой статьи для перепечатки.:Плавление и обработка ADC12
Минхэ Компания по литью под давлением специализируются на производстве и предоставлении качественных и высокопроизводительных литых деталей (ассортимент металлических деталей для литья под давлением в основном включает Тонкостенное литье под давлением,Литье под давлением,Литье под давлением в холодной камере), Round Service (Служба литья под давлением,Обработка с ЧПУ,Изготовление пресс-форм, Обработка поверхности) .Любое индивидуальное литье под давлением из алюминия, магния или замака / цинка, а также другие требования к отливкам, пожалуйста, свяжитесь с нами.
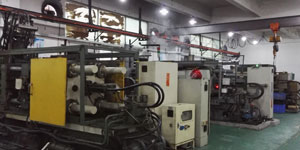
Под контролем ISO9001 и TS 16949, все процессы выполняются на сотнях передовых машин для литья под давлением, 5-осевых станках и других объектах, от струйных до стиральных машин Ultra Sonic. Minghe не только имеет современное оборудование, но и имеет профессиональное оборудование. команда опытных инженеров, операторов и инспекторов для воплощения в жизнь проекта заказчика.
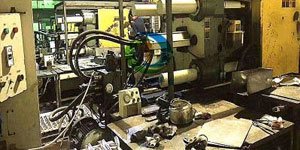
Контрактный производитель отливок под давлением. Возможности включают в себя детали для литья под давлением алюминия с холодной камерой весом от 0.15 фунта. до 6 фунтов, быстрая установка и обработка. Дополнительные услуги включают полировку, вибрацию, удаление заусенцев, дробеструйную очистку, окраску, гальванику, нанесение покрытий, сборку и оснастку. Обрабатываемые материалы включают такие сплавы, как 360, 380, 383 и 413.
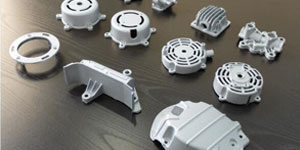
Помощь в проектировании литья цинка под давлением / сопутствующие инженерные услуги. Изготовление на заказ прецизионных отливок из цинка под давлением. Могут изготавливаться миниатюрные отливки, отливки под высоким давлением, отливки в формы с несколькими суппортами, отливки в обычные формы, единичные отливки под давлением и независимые отливки под давлением, а также отливки с герметизацией полости. Отливки могут изготавливаться длиной и шириной до 24 дюймов с допуском +/- 0.0005 дюйма.
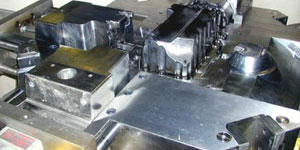
Производитель литья под давлением из магния, сертифицированный по стандарту ISO 9001: 2015. Возможности включают литье под давлением магния под высоким давлением с горячей камерой до 200 тонн и холодной камерой на 3000 тонн, проектирование инструментов, полировку, формование, механическую обработку, порошковую и жидкостную окраску, полный контроль качества с возможностями CMM , сборка, упаковка и доставка.
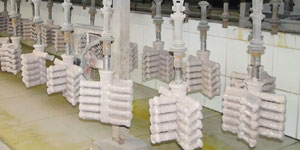
Сертифицирован ITAF16949. Дополнительные услуги трансляции включают инвестиционное литье,литье в песчаные формы,Гравитационное литье, Литье по выплавляемым моделям,Центробежное литье,Вакуумное литье,Постоянное литье формыВозможности включают EDI, техническую поддержку, твердотельное моделирование и вторичную обработку.
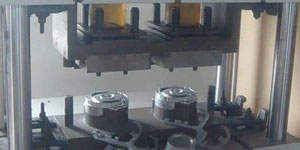
Литейная промышленность Примеры использования запчастей для: автомобилей, велосипедов, самолетов, музыкальных инструментов, судов, оптических устройств, датчиков, моделей, электронных устройств, корпусов, часов, машинного оборудования, двигателей, мебели, ювелирных изделий, приспособлений, телекоммуникаций, освещения, медицинских устройств, фотографических устройств, Роботы, скульптуры, звуковое оборудование, спортивное оборудование, инструменты, игрушки и многое другое.
Что мы можем вам сделать дальше?
∇ Перейти на главную страницу для Литье под давлением Китай
→Литье деталей-Узнай, что мы сделали.
→ Общие советы о Услуги литья под давлением
By Производитель литья под давлением Minghe | Категории: Полезные статьи |Материалы Теги: Литье алюминия, Цинковое литье, Литье магния, Титановое литье, Литье из нержавеющей стали, Латунное литье,Бронзовое литье,Кастинг видео,История компании,Литье алюминия под давлением | Комментарии отключены